- お役立ち記事
- Benefits and Applications of PVD Coatings: Process Technology for Surface Protection and Product Durability
Benefits and Applications of PVD Coatings: Process Technology for Surface Protection and Product Durability
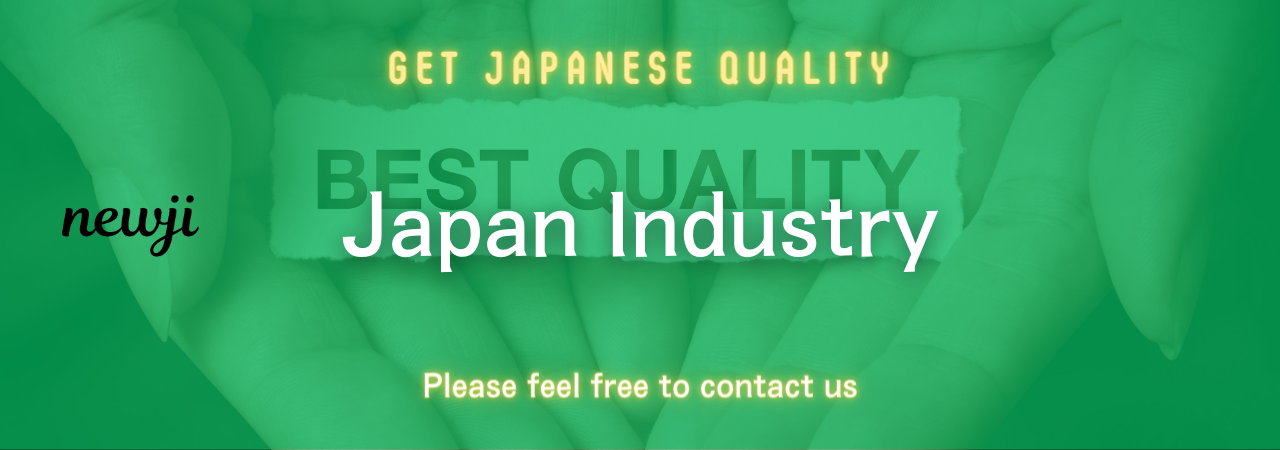
Physical Vapor Deposition (PVD) coatings are increasingly becoming a crucial component in various industries.
This advanced technology provides solutions for enhancing surface protection and product durability.
In this article, we will delve into the benefits and applications of PVD coatings, shedding light on why they are so valuable.
目次
What is PVD Coating?
PVD coating is a vacuum deposition method used to produce thin films and coatings.
It involves the transition of material from a condensed phase to a vapor phase and then back to a thin film condensed phase.
The materials used in PVD coatings are often metals such as titanium, chromium, and aluminum.
These metals are vaporized in a vacuum chamber and then deposited onto the substrate, forming a thin layer of coating.
Benefits of PVD Coatings
Enhanced Durability
One of the primary benefits of PVD coatings is the significant enhancement in durability they provide.
The thin film layer of coating is highly resistant to wear and tear.
This increased durability leads to a longer lifespan for coated products, which is particularly beneficial in high-stress environments.
Superior Hardness
PVD coatings are known for their superior hardness.
This quality is essential for tools and machinery that encounter frequent and intense usage.
The hardness provides a protective barrier that prevents scratches and dings, maintaining the product’s integrity over time.
Corrosion Resistance
Corrosion can dramatically affect the performance and lifespan of metal products.
PVD coatings offer excellent corrosion resistance, protecting the underlying material from rust and other forms of deterioration.
This makes PVD coatings ideal for products exposed to harsh environments or chemicals.
Improved Aesthetics
Aside from the functional benefits, PVD coatings also improve the aesthetics of products.
The coatings can be applied in a variety of colors and finishes, from gleaming metallic to matte.
This versatility allows manufacturers to enhance the visual appeal of their products, catering to both functional and aesthetic demands.
Applications of PVD Coatings
Aerospace Industry
In the aerospace industry, product reliability and safety are paramount.
PVD coatings are used to enhance the performance of aerospace components such as turbine blades and engine parts.
The coatings help reduce friction and wear, thereby extending the service life of these critical components.
Automotive Sector
The automotive sector also benefits immensely from PVD coatings.
Car parts such as gears, pistons, and engine valves are often coated to improve performance and durability.
The superior hardness and corrosion resistance of PVD coatings ensure that automotive components perform efficiently even under extreme conditions.
Medical Devices
Medical devices require high levels of precision and reliability.
PVD coatings are used on surgical instruments, implants, and medical tools to enhance their durability and performance.
The coatings also ensure that devices remain sterile and free from contamination, which is essential for patient safety.
Cutting Tools
Cutting tools such as drills, saw blades, and milling cutters are subjected to intense use and wear.
PVD coatings increase the hardness and wear resistance of these tools, resulting in longer tool life and consistent performance.
This is particularly beneficial in industries where precision cutting and machining are crucial.
Electronics
In the electronics industry, PVD coatings are used to protect components like semiconductors and circuit boards.
The coatings provide a protective barrier against moisture, dust, and other environmental factors.
This ensures the longevity and reliability of electronic devices.
PVD Coating Process
Material Preparation
Before the PVD coating process can begin, the material to be coated must be properly prepared.
This involves cleaning the substrate to remove any contaminants that might interfere with adhesion.
Vaporization
In this stage, the coating material is vaporized.
This typically involves heating the material in a vacuum chamber until it transitions into a vapor state.
The use of a vacuum ensures that the coating material does not react with air or other gases.
Deposition
Once vaporized, the material is transported to the substrate where it condenses to form a thin film of coating.
This deposition occurs at atomic levels, ensuring a uniform and durable coating layer.
The process continues until the desired coating thickness is achieved.
Future Trends and Innovations in PVD Coatings
Smart Coatings
The future of PVD coatings lies in smart coatings that can adapt to environmental conditions.
These coatings could change properties in response to temperature, moisture, or stress.
Such innovations could offer even greater durability and functional benefits.
Environmentally Friendly Processes
As industries push towards greener manufacturing practices, the PVD coating process is also evolving.
Developments are being made to make the process more energy-efficient and environmentally friendly.
This includes reducing the use of hazardous materials and finding ways to recycle coating materials.
Advanced Materials
Researchers are continually exploring new materials that can be used in PVD coatings.
These materials could offer unique properties such as increased thermal resistance or enhanced electrical conductivity.
Advanced materials could open up new applications and improve the effectiveness of PVD coatings.
In conclusion, PVD coatings offer numerous benefits, including improved durability, hardness, corrosion resistance, and aesthetics.
Their applications span across various industries, from aerospace to electronics, demonstrating their versatility and value.
With ongoing advancements and innovations, the future of PVD coatings looks promising, paving the way for more efficient and sustainable practices.
資料ダウンロード
QCD調達購買管理クラウド「newji」は、調達購買部門で必要なQCD管理全てを備えた、現場特化型兼クラウド型の今世紀最高の購買管理システムとなります。
ユーザー登録
調達購買業務の効率化だけでなく、システムを導入することで、コスト削減や製品・資材のステータス可視化のほか、属人化していた購買情報の共有化による内部不正防止や統制にも役立ちます。
NEWJI DX
製造業に特化したデジタルトランスフォーメーション(DX)の実現を目指す請負開発型のコンサルティングサービスです。AI、iPaaS、および先端の技術を駆使して、製造プロセスの効率化、業務効率化、チームワーク強化、コスト削減、品質向上を実現します。このサービスは、製造業の課題を深く理解し、それに対する最適なデジタルソリューションを提供することで、企業が持続的な成長とイノベーションを達成できるようサポートします。
オンライン講座
製造業、主に購買・調達部門にお勤めの方々に向けた情報を配信しております。
新任の方やベテランの方、管理職を対象とした幅広いコンテンツをご用意しております。
お問い合わせ
コストダウンが利益に直結する術だと理解していても、なかなか前に進めることができない状況。そんな時は、newjiのコストダウン自動化機能で大きく利益貢献しよう!
(Β版非公開)