- お役立ち記事
- Benefits and challenges of improving productivity brought about by IoT in factories
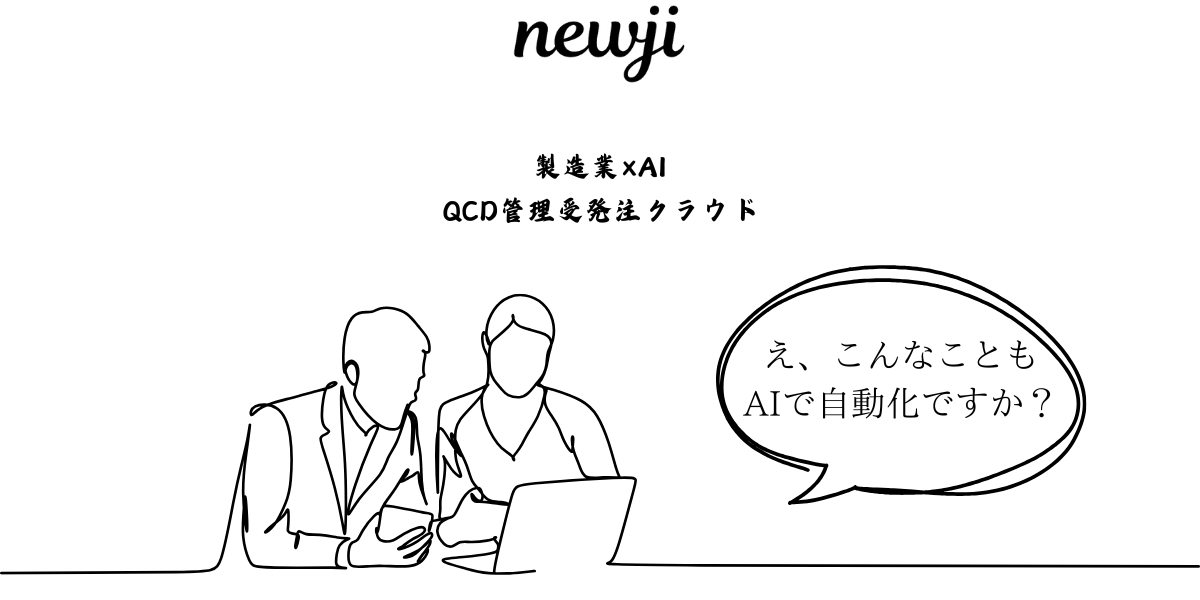
Benefits and challenges of improving productivity brought about by IoT in factories
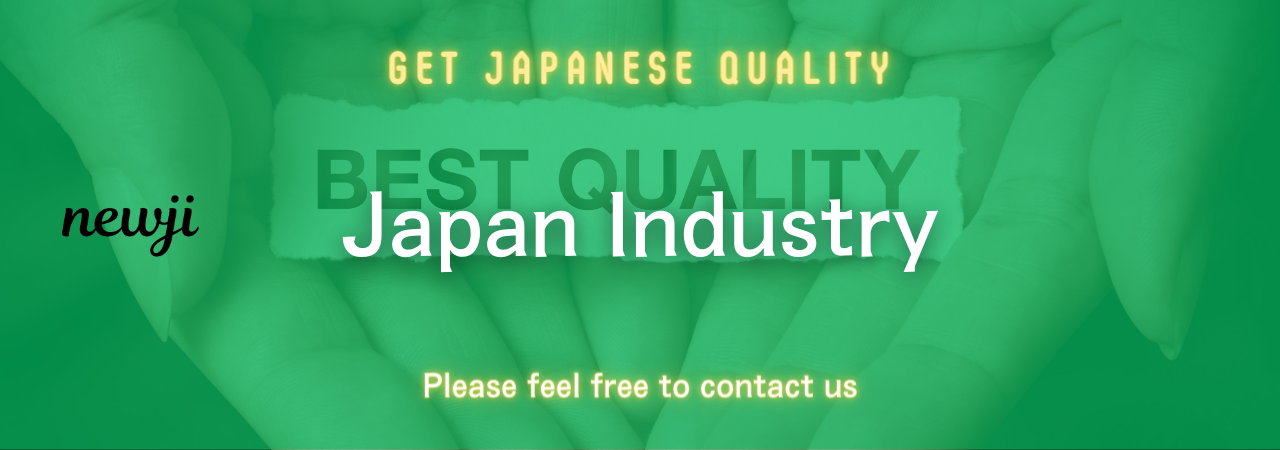
目次
Understanding IoT in Factories
The Internet of Things, commonly known as IoT, is revolutionizing industries across the globe.
In the context of factories, IoT refers to the interconnection of devices and systems through the internet to collect and exchange data.
This connectivity allows for smarter operations, enhancing efficiency and productivity.
As factories evolve with technology, understanding the benefits and challenges of IoT becomes increasingly important.
Benefits of IoT in Enhancing Productivity
1. Real-time Monitoring and Maintenance
One of the significant advantages IoT brings to factories is the ability for real-time monitoring.
IoT devices collect data continuously, enabling factory managers to oversee operations and identify issues as they occur.
This real-time observation facilitates proactive maintenance, reducing downtime and increasing overall productivity.
By ensuring machines are functioning optimally, factories can avoid costly delays.
2. Improved Efficiency Through Automation
Automation is at the heart of IoT’s impact on productivity.
With IoT, factories can automate routine tasks such as monitoring equipment performance or managing inventory levels.
This automation allows employees to focus on more critical tasks that require human intervention.
As a result, processes become more streamlined, leading to faster production cycles and reduced operational costs.
3. Enhanced Supply Chain Management
IoT provides precise data collection and analytics that improve supply chain management.
By tracking goods from production to delivery, factories can optimize inventory levels and reduce wastage.
Real-time data allows for better demand forecasting, ensuring that resources are allocated efficiently.
This level of insight enhances the overall supply chain, resulting in faster response times and improved customer satisfaction.
4. Energy Efficiency and Sustainability
IoT devices can monitor energy usage throughout a factory, identifying areas where consumption can be reduced.
By optimizing energy usage, factories not only save on costs but also contribute to environmental sustainability.
This approach aligns with the growing emphasis on eco-friendly practices in manufacturing, appealing to consumers and stakeholders alike.
5. Predictive Analytics and Decision Making
One of the most transformative aspects of IoT in factories is its ability to use predictive analytics.
By analyzing data from various sources, IoT systems can predict potential equipment failures or production bottlenecks.
This foresight allows for timely interventions, minimizing disruptions and maintaining smooth operations.
Such predictive capabilities empower managers and decision-makers to make informed choices that enhance productivity.
Challenges in Implementing IoT in Factories
While IoT offers numerous advantages, it also presents challenges that factories must navigate.
1. High Initial Investment
Implementing IoT technology requires a substantial initial investment.
Factories need to upgrade their infrastructure, purchase IoT devices, and invest in software solutions that integrate these systems.
While the long-term benefits often justify the expenditure, the upfront costs can be a barrier for smaller facilities.
2. Data Security Concerns
With the increased connectivity that IoT brings, data security becomes a critical concern.
Factories are at risk of cyber-attacks that can lead to the theft or loss of sensitive data.
Ensuring robust cybersecurity measures are in place is essential to protect against vulnerabilities.
Balancing connectivity with security is an ongoing challenge in the implementation of IoT in factories.
3. Integration with Existing Systems
Another challenge is integrating IoT technology with existing factory systems.
Legacy equipment may not be compatible with IoT devices, requiring additional modifications or replacements.
The success of IoT implementation often depends on the seamless integration of new and old technologies, which can be both time-consuming and complex.
4. Workforce Training and Adaptation
Adopting IoT in factories necessitates a shift in workforce skills and culture.
Employees must be trained to work with new technologies and embrace IoT-driven processes.
This transition can encounter resistance or uncertainty as the workforce adapts to new ways of operating.
Ongoing training and support are crucial to facilitate this change smoothly.
5. Managing Data Overload
While IoT provides valuable data, managing the sheer volume of information can be overwhelming.
Factories need efficient data management systems to filter, analyze, and interpret the data generated.
Without proper systems in place, there is a risk of data overload, making it difficult to glean actionable insights.
Conclusion
IoT presents a transformative opportunity for factories seeking to enhance productivity.
By enabling real-time monitoring, automation, and predictive analytics, IoT can drive efficiency and competitiveness.
However, challenges such as initial investment, data security, and workforce adaptation must be addressed to fully realize its potential.
As technology progresses, factories that embrace and effectively implement IoT will likely lead the way in the manufacturing industry, reaping substantial benefits in productivity and innovation.
資料ダウンロード
QCD調達購買管理クラウド「newji」は、調達購買部門で必要なQCD管理全てを備えた、現場特化型兼クラウド型の今世紀最高の購買管理システムとなります。
ユーザー登録
調達購買業務の効率化だけでなく、システムを導入することで、コスト削減や製品・資材のステータス可視化のほか、属人化していた購買情報の共有化による内部不正防止や統制にも役立ちます。
NEWJI DX
製造業に特化したデジタルトランスフォーメーション(DX)の実現を目指す請負開発型のコンサルティングサービスです。AI、iPaaS、および先端の技術を駆使して、製造プロセスの効率化、業務効率化、チームワーク強化、コスト削減、品質向上を実現します。このサービスは、製造業の課題を深く理解し、それに対する最適なデジタルソリューションを提供することで、企業が持続的な成長とイノベーションを達成できるようサポートします。
オンライン講座
製造業、主に購買・調達部門にお勤めの方々に向けた情報を配信しております。
新任の方やベテランの方、管理職を対象とした幅広いコンテンツをご用意しております。
お問い合わせ
コストダウンが利益に直結する術だと理解していても、なかなか前に進めることができない状況。そんな時は、newjiのコストダウン自動化機能で大きく利益貢献しよう!
(Β版非公開)