- お役立ち記事
- Benefits and challenges of introducing digital twins in the manufacturing industry
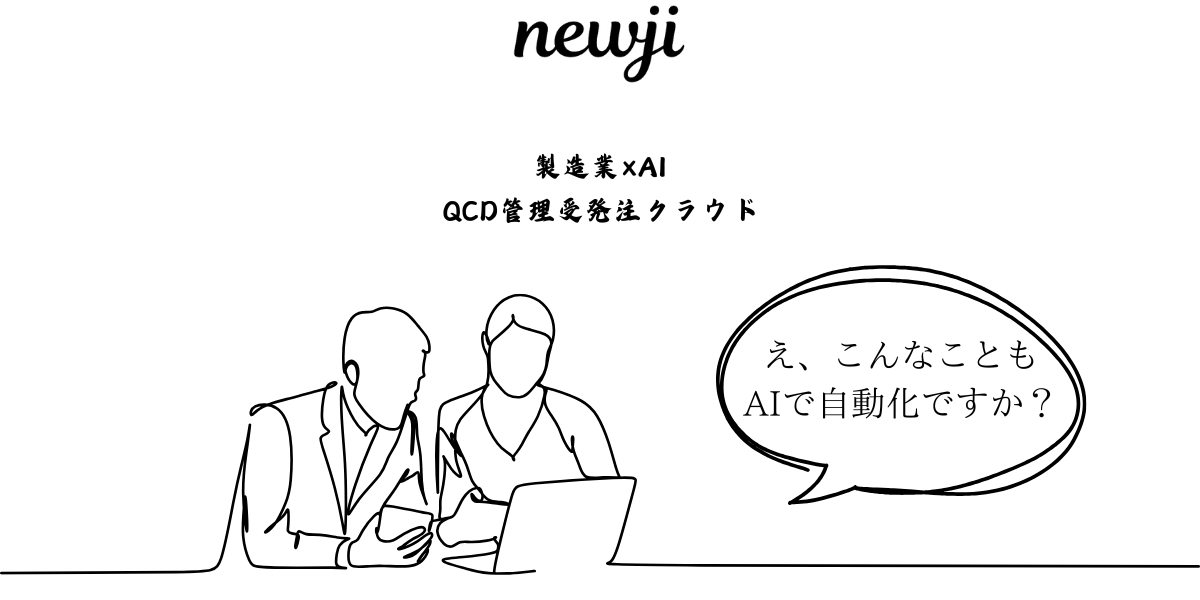
Benefits and challenges of introducing digital twins in the manufacturing industry
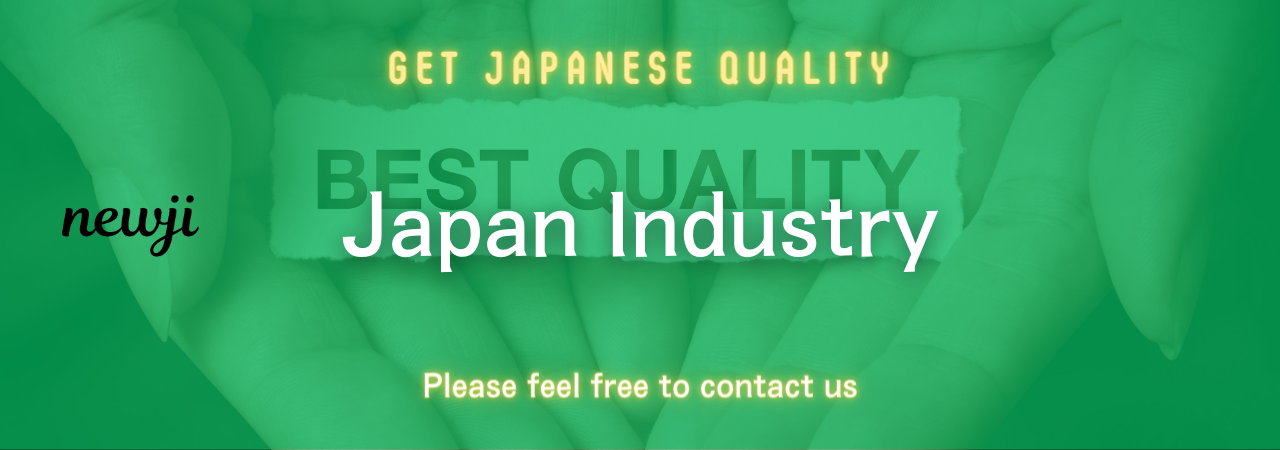
目次
Understanding Digital Twins
Digital twins are virtual replicas of physical systems or devices, using real-time data and advanced algorithms to represent the object as closely as possible.
This concept has been steadily gaining traction, especially in the manufacturing industry, where precision, efficiency, and predictive capabilities are crucial.
By creating a digital twin, manufacturers can simulate, analyze, and predict the performance of their products and processes with enhanced accuracy.
Benefits of Digital Twins in Manufacturing
Improved Product Design and Innovation
One of the primary benefits of digital twins is the ability to improve product design and foster innovation.
By simulating product designs and their various iterations, manufacturers can test different scenarios without physically fabricating parts.
This reduces the time and cost involved in prototyping while also enabling more innovative solutions to be identified and implemented faster.
Enhanced Operational Efficiency
Digital twins allow for significant improvements in operational efficiency.
They provide real-time data analytics that helps in monitoring the operations and predicting potential failures before they occur.
This predictive maintenance capability not only saves time but also reduces downtime, as solutions can be implemented before any disruption happens.
Personalized Customer Experience
Manufacturers can leverage digital twins to offer more customized products to their customers.
By understanding the exact needs and usage patterns through collected data, manufacturers can tailor their offerings to meet specific customer requirements, thereby enhancing the customer experience and satisfaction.
Streamlined Supply Chain Management
A digital twin provides insights into every aspect of the manufacturing process, including the entire supply chain.
By simulating and assessing different supply chain scenarios, manufacturers can identify bottlenecks and optimize logistics for more efficient and cost-effective operations.
It enables them to respond to changes in demand and supply dynamically, ensuring a smoother operation throughout.
Environmentally Friendly Manufacturing
With increased pressure on industries to reduce their environmental footprint, digital twins can play a pivotal role.
By optimizing processes and reducing material waste, digital twins contribute to more sustainable manufacturing practices.
They enable manufacturers to test the environmental impact of their processes and materials and choose more eco-friendly options, leading to greener operations.
Challenges of Implementing Digital Twins
High Initial Investment
One of the main challenges facing manufacturers is the high initial investment required to set up digital twin technologies.
This includes the cost of acquiring and integrating advanced software, hardware, and training personnel.
The return on investment might not be immediate, making it a financial challenge for some companies, especially small to medium-sized enterprises.
Data Security Concerns
Digital twins rely heavily on data exchange and connectivity for accurate simulations and analyses.
This dependency poses significant security risks as sensitive data can be intercepted during transmission.
Manufacturers must invest in robust cybersecurity measures to protect their data and systems from potential breaches, adding to the overall cost and complexity.
Integration with Existing Systems
Integrating digital twins with legacy systems can be a daunting task.
Manufacturers often face compatibility issues during integration, which can prolong the deployment process and increase costs.
It requires extensive IT expertise to ensure seamless operation and connectivity across all platforms involved.
Data Accuracy and Management
For digital twins to be effective, they must rely on accurate and up-to-date data.
Ensuring the accuracy of data can be a significant challenge, particularly for manufacturers operating complex systems or environments.
Moreover, managing vast amounts of data and extracting valuable insights from them requires sophisticated data management strategies and tools.
Skill Gap and Workforce Training
The implementation of digital twins necessitates a workforce that is skilled in new technologies and digital tools.
This often means companies need to invest considerable resources in training their employees or hiring new talent with the necessary competencies.
Bridging this skill gap can be time-consuming and costly but is vital for the successful adoption of digital twin technology.
Conclusion
The integration of digital twins in the manufacturing industry presents numerous benefits that can drive efficiency, innovation, and sustainability.
However, it comes with a set of challenges that manufacturers must carefully consider and plan for.
Balancing the initial investment and the long-term benefits is key to successfully implementing this transformative technology.
As the industry continues to evolve, digital twins will likely play an increasingly central role, helping manufacturers stay competitive in a rapidly changing landscape.
資料ダウンロード
QCD調達購買管理クラウド「newji」は、調達購買部門で必要なQCD管理全てを備えた、現場特化型兼クラウド型の今世紀最高の購買管理システムとなります。
ユーザー登録
調達購買業務の効率化だけでなく、システムを導入することで、コスト削減や製品・資材のステータス可視化のほか、属人化していた購買情報の共有化による内部不正防止や統制にも役立ちます。
NEWJI DX
製造業に特化したデジタルトランスフォーメーション(DX)の実現を目指す請負開発型のコンサルティングサービスです。AI、iPaaS、および先端の技術を駆使して、製造プロセスの効率化、業務効率化、チームワーク強化、コスト削減、品質向上を実現します。このサービスは、製造業の課題を深く理解し、それに対する最適なデジタルソリューションを提供することで、企業が持続的な成長とイノベーションを達成できるようサポートします。
オンライン講座
製造業、主に購買・調達部門にお勤めの方々に向けた情報を配信しております。
新任の方やベテランの方、管理職を対象とした幅広いコンテンツをご用意しております。
お問い合わせ
コストダウンが利益に直結する術だと理解していても、なかなか前に進めることができない状況。そんな時は、newjiのコストダウン自動化機能で大きく利益貢献しよう!
(Β版非公開)