- お役立ち記事
- Benefits and practices of process approach in manufacturing
Benefits and practices of process approach in manufacturing
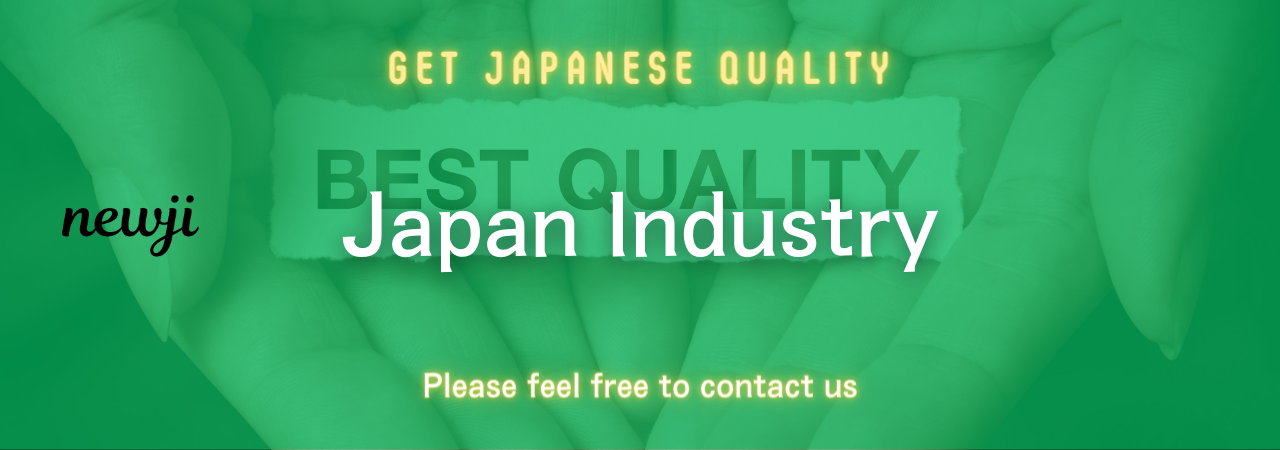
The process approach in manufacturing is a systematic method that focuses on understanding and managing the various processes that make up an operation.
By concentrating on processes rather than tasks, businesses can achieve greater efficiency, consistency, and quality in their products.
Let’s delve into the benefits and practices of implementing a process approach in manufacturing.
目次
Understanding the Process Approach
The process approach is essentially about mapping out, understanding, and managing the various processes involved in manufacturing.
This methodology views each element of production as part of a connected system, rather than as individual, isolated tasks.
It aims to optimize the flow of activities and ensure resources are used effectively.
Elements of the Process Approach
A successful process approach involves several key elements:
1. **Identifying Processes:** Recognize and define all the processes that comprise the production system.
2. **Mapping Relationships:** Understand the interrelationships between these processes.
3. **Managing Resources:** Ensure that resources such as materials, workforce, and machinery are aligned to support these processes.
4. **Monitoring Performance:** Continuously measure and monitor the performance of each process.
5. **Continuous Improvement:** Implement practices to continually improve process efficiency and output quality.
Benefits of the Process Approach
Adopting a process approach in manufacturing offers multiple advantages.
Enhanced Efficiency
By mapping out and understanding each process, manufacturers can identify and eliminate inefficiencies.
This leads to streamlined operations, reduced waste, and optimal use of resources.
Ultimately, manufacturers are able to produce goods faster and at a lower cost.
Consistency and Quality
A process approach ensures that every part of the manufacturing workflow adheres to set standards, leading to greater consistency in the final product.
Quality control becomes simpler, as well-defined processes allow for quicker identification and rectification of any deviations from the standard.
Improved Customer Satisfaction
Consistent quality and timely delivery play a major role in customer satisfaction.
By adhering to a structured process, manufacturers can foster reliability and trust among their customers.
Better Risk Management
Understanding the interdependencies between processes allows manufacturers to better anticipate and mitigate risks.
This preemptive approach helps in safeguarding against disruptions and ensures a more resilient production system.
Best Practices for Implementing a Process Approach
Successfully integrating a process approach in manufacturing requires thoughtful planning and execution.
Develop a Process Map
Begin by mapping out all the processes involved in your manufacturing operation.
This visual representation helps in understanding the sequence and interaction of processes.
Engage and Train Employees
Ensure that employees at all levels are aware of the processes and their importance.
Provide training and resources so that they can effectively participate in the process improvement activities.
Set Clear Objectives
Establish clear goals for each process.
This could be in terms of output quantity, quality, resource utilization, or time.
Having specific objectives helps in focused monitoring and improvement efforts.
Use Technology
Invest in technology to monitor and manage processes effectively.
Manufacturing Execution Systems (MES) and Enterprise Resource Planning (ERP) systems can provide real-time data and analytics for better decision-making.
Monitor and Review
Regularly monitor the performance of processes against set benchmarks.
Conduct periodic reviews and make necessary adjustments to maintain efficiency and quality.
Implement Continuous Improvement
Adopt methodologies like Lean, Six Sigma, or Kaizen to foster a culture of continuous improvement.
Encourage feedback and suggestions from employees for ongoing process enhancements.
Challenges in Adopting a Process Approach
While the benefits are significant, implementing a process approach in manufacturing can come with its own set of challenges.
Change Management
Shifting from a task-based to a process-based approach requires a change in mindset across the organization.
Managing this transition and getting buy-in from all levels can be challenging.
Resource Allocation
Mapping out and optimizing processes may initially necessitate additional resources and time.
Balancing short-term investments with long-term gains is a critical consideration.
Maintaining Consistency
Once processes are defined, maintaining consistency in execution is crucial.
Any deviation can lead to inefficiencies and quality issues.
Technology Integration
Effective implementation often requires the integration of technology for monitoring and managing processes.
Choosing the right solutions and ensuring smooth implementation can be complex.
Case Study: Successful Implementation
To offer a concrete example, let’s look at a case study of a company that successfully implemented a process approach.
Company Background
ABC Manufacturing, a mid-sized firm specializing in automotive parts, faced issues with inconsistent product quality and high production costs.
Leadership decided to adopt a process approach to address these challenges.
Implementation Steps
1. **Process Mapping:** The company mapped all its production processes, identifying key areas of inefficiency.
2. **Employee Training:** Comprehensive training programs were rolled out to familiarize employees with the new processes.
3. **Technology Adoption:** ABC invested in an MES to monitor real-time production data.
4. **Continuous Improvement:** Regular feedback loops and performance reviews were established to foster a culture of continuous improvement.
Results
Within a year, ABC Manufacturing saw a 20% reduction in production costs and a 30% increase in product quality.
Customer satisfaction scores also improved significantly due to timely deliveries and consistent quality.
The process approach in manufacturing is not just a theoretical concept but a practical strategy that can lead to significant improvements in efficiency, quality, and customer satisfaction.
By understanding and managing the myriad of interconnected processes, manufacturers can create a more efficient, reliable, and competitive operation.
Whether you are a small-scale manufacturer or a large enterprise, adopting a process approach can pave the way for lasting success and growth.
資料ダウンロード
QCD調達購買管理クラウド「newji」は、調達購買部門で必要なQCD管理全てを備えた、現場特化型兼クラウド型の今世紀最高の購買管理システムとなります。
ユーザー登録
調達購買業務の効率化だけでなく、システムを導入することで、コスト削減や製品・資材のステータス可視化のほか、属人化していた購買情報の共有化による内部不正防止や統制にも役立ちます。
NEWJI DX
製造業に特化したデジタルトランスフォーメーション(DX)の実現を目指す請負開発型のコンサルティングサービスです。AI、iPaaS、および先端の技術を駆使して、製造プロセスの効率化、業務効率化、チームワーク強化、コスト削減、品質向上を実現します。このサービスは、製造業の課題を深く理解し、それに対する最適なデジタルソリューションを提供することで、企業が持続的な成長とイノベーションを達成できるようサポートします。
オンライン講座
製造業、主に購買・調達部門にお勤めの方々に向けた情報を配信しております。
新任の方やベテランの方、管理職を対象とした幅広いコンテンツをご用意しております。
お問い合わせ
コストダウンが利益に直結する術だと理解していても、なかなか前に進めることができない状況。そんな時は、newjiのコストダウン自動化機能で大きく利益貢献しよう!
(Β版非公開)