- お役立ち記事
- Best Approaches for Achieving Complex Shapes with Spinning
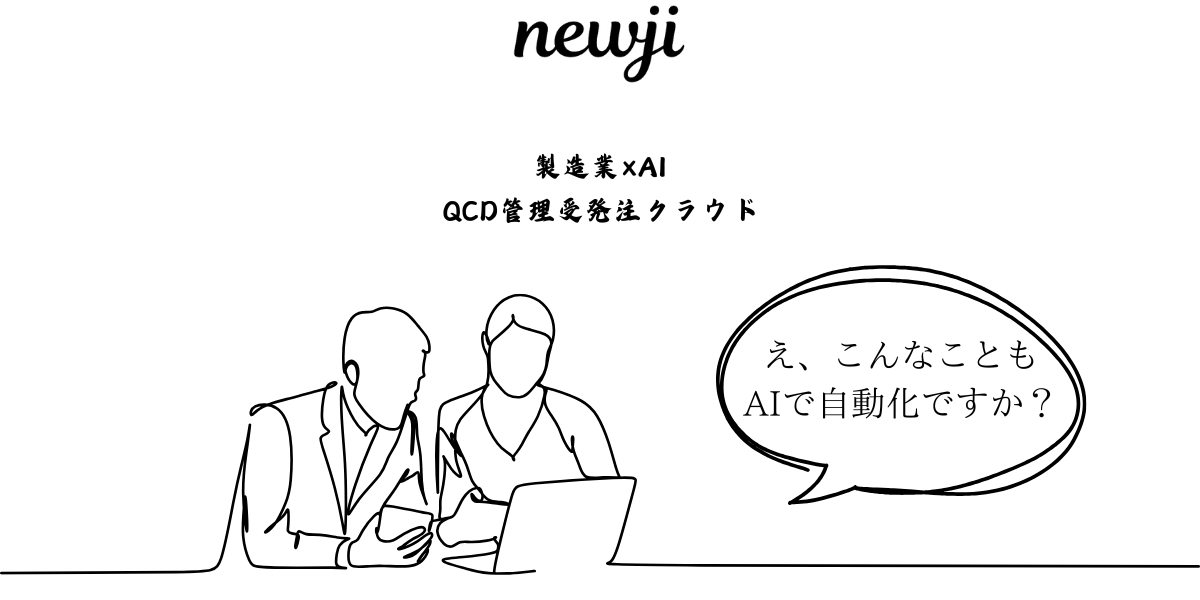
Best Approaches for Achieving Complex Shapes with Spinning
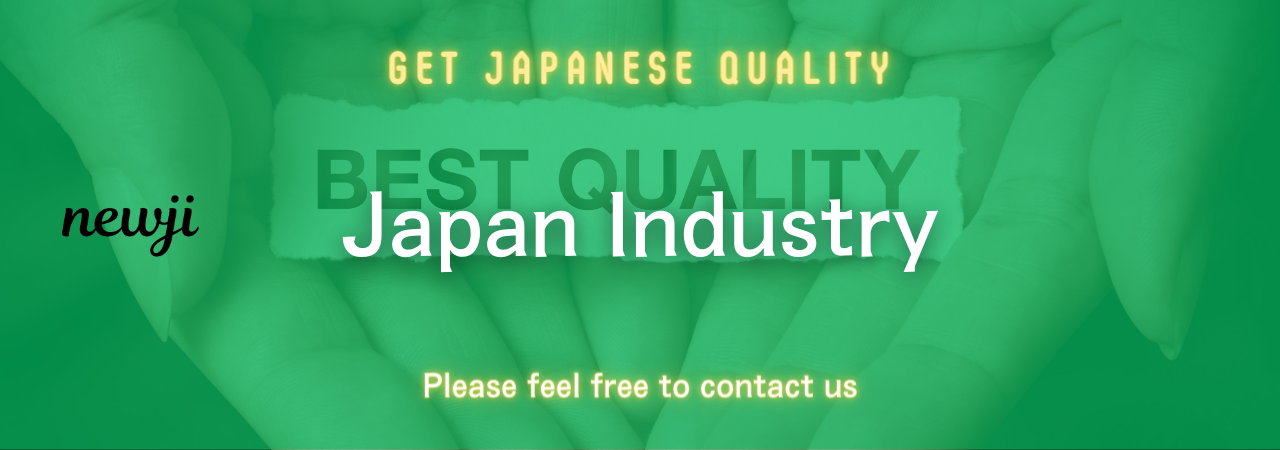
Spinning is a well-established manufacturing technique used to create complex shapes with precision and efficiency. This process involves rotating a disk or tube of material and applying force to shape it into a symmetrical object. Let’s explore some of the best approaches for achieving intricate shapes using spinning.
目次
Understanding the Spinning Process
Spinning, also known as metal spinning or spin forming, is one of the most versatile methods for shaping metals. The material is rotated at high speeds while tools press against it to contour the desired shape. This technique can create cylindrical, conical, and other axisymmetric forms.
Types of Spinning
There are several types of spinning processes, each suited to different applications and complexity levels:
Conventional Spinning
In conventional spinning, a flat metal blank is clamped against a mandrel and rotated. Rollers or spinning tools press against the blank, forming it closely around the mandrel’s shape. This method is excellent for producing simple symmetrical parts like cones or hemispheres.
Shear Spinning
Shear spinning involves thinning the material as it is formed. The workpiece is pressed against the mandrel while reducing its thickness. This technique is useful for making parts that require both shape and structural integrity.
Tube Spinning
Tube spinning focuses on shaping hollow cylindrical objects. The tube is clamped and rotated while external and internal rollers adjust its dimensions. This method is especially effective for creating long, seamless tubes with complex cross-sections.
Factors Influencing the Spinning Process
Several factors play a crucial role in determining the success of spinning operations. Understanding these factors can help achieve the desired complex shapes efficiently.
Material Selection
The type of material used significantly affects the spinning process. Metals like aluminum, steel, copper, and titanium are commonly used due to their ductility and strength. Each material’s properties must be considered to select the right tooling and parameters for the job.
Tooling and Equipment
The selection of tools and equipment is paramount. Precision-machined mandrels and robust spinning tools are essential to achieve high-quality results. Modern CNC spinning machines offer enhanced control and accuracy, making them ideal for complex shapes.
Speed and Feed Rates
The rotational speed of the workpiece and the feed rate of the spinning tool are critical parameters. Proper adjustment of these rates ensures the material flows smoothly into the desired shape without defects. Experimentation and experience often determine the optimal settings.
Best Practices for Achieving Complex Shapes
Successfully achieving complex shapes with spinning requires meticulous planning and execution. Here are some best practices to follow:
Design Considerations
Start with a clear design concept that considers the limitations and advantages of spinning. Utilize CAD software to model the part and simulate the spinning process. This helps identify potential issues and refine the design for manufacturability.
Prototype and Testing
Create prototypes to test the feasibility of the design. Prototyping allows for adjustments based on real-world performance, ensuring the final product meets specifications. Testing different materials and tooling setups during this phase can lead to better outcomes.
Tool Path Optimization
Optimize the path that the tool will take during the spinning process. A well-planned tool path minimizes stress on the material and reduces the likelihood of defects. Modern CNC machines can generate precise tool paths that ensure consistent quality.
Quality Control
Quality control is essential throughout the spinning process. Regularly inspect the workpiece for defects such as wrinkles, cracks, or thinning. Employ non-destructive testing methods to ensure structural integrity without damaging the part.
Collaboration and Expertise
Work closely with experts who have experience in spinning. Their knowledge can help navigate challenges and implement proven strategies. Collaboration with materials scientists, engineers, and machinists can provide valuable insights and improve the overall process.
Applications of Spinning for Complex Shapes
The ability to create intricate shapes through spinning opens up numerous applications across various industries. Some notable applications include:
Aerospace
The aerospace industry relies on spinning to produce high-precision components like turbine blades, rocket nose cones, and aircraft fuselage sections. The method ensures lightweight yet strong parts crucial for performance and safety.
Automotive
In the automotive sector, spinning is used to manufacture components like wheel rims, exhaust system parts, and suspension components. These parts require complex shapes that guarantee durability and aesthetics.
Medical Devices
Medical device manufacturers use spinning to create intricate shapes required for implants, surgical instruments, and diagnostic equipment. The precision and quality achievable with spinning meet the stringent standards of the healthcare industry.
Consumer Goods
Spinning finds applications in producing everyday items such as cookware, lighting fixtures, musical instruments, and sports equipment. The method allows for innovative designs and functional features.
Future Trends in Spinning Technology
The spinning process continues to evolve, with advancements aiming to enhance precision and efficiency. Some future trends to watch include:
Automation and AI Integration
The integration of automation and artificial intelligence promises to revolutionize spinning. AI can optimize tool paths, predict defects, and adjust parameters in real-time, resulting in improved quality and reduced production times.
Advanced Materials
The development of new materials with superior properties will expand the capabilities of spinning. High-strength alloys, composites, and lightweight metals will enable the production of parts with complex geometries and enhanced performance.
Environmental Sustainability
Sustainability is becoming a priority across industries. Advances in spinning technology will focus on reducing waste, energy consumption, and environmental impact. Eco-friendly materials and efficient processes will drive the future of spinning.
The spinning process is a powerful technique for achieving complex shapes with precision and efficiency. By understanding the fundamentals, following best practices, and leveraging advancements, manufacturers can produce high-quality parts for a wide range of applications.
資料ダウンロード
QCD調達購買管理クラウド「newji」は、調達購買部門で必要なQCD管理全てを備えた、現場特化型兼クラウド型の今世紀最高の購買管理システムとなります。
ユーザー登録
調達購買業務の効率化だけでなく、システムを導入することで、コスト削減や製品・資材のステータス可視化のほか、属人化していた購買情報の共有化による内部不正防止や統制にも役立ちます。
NEWJI DX
製造業に特化したデジタルトランスフォーメーション(DX)の実現を目指す請負開発型のコンサルティングサービスです。AI、iPaaS、および先端の技術を駆使して、製造プロセスの効率化、業務効率化、チームワーク強化、コスト削減、品質向上を実現します。このサービスは、製造業の課題を深く理解し、それに対する最適なデジタルソリューションを提供することで、企業が持続的な成長とイノベーションを達成できるようサポートします。
オンライン講座
製造業、主に購買・調達部門にお勤めの方々に向けた情報を配信しております。
新任の方やベテランの方、管理職を対象とした幅広いコンテンツをご用意しております。
お問い合わせ
コストダウンが利益に直結する術だと理解していても、なかなか前に進めることができない状況。そんな時は、newjiのコストダウン自動化機能で大きく利益貢献しよう!
(Β版非公開)