- お役立ち記事
- Best Practices for 5S (Sort, Set in Order, Shine, Standardize, Sustain) in Manufacturing
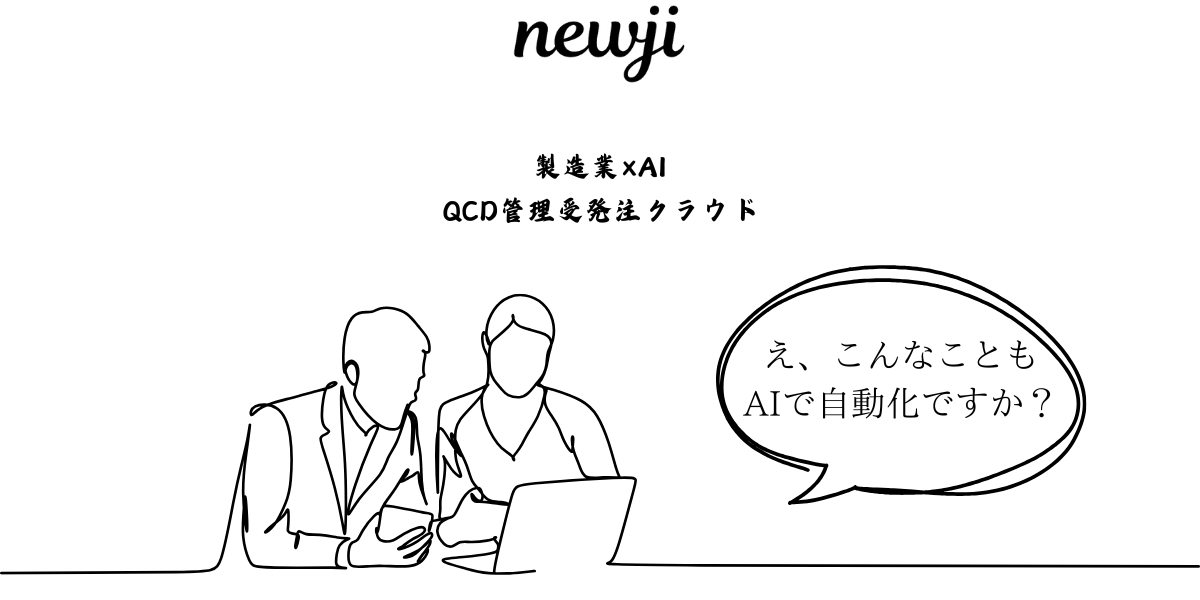
Best Practices for 5S (Sort, Set in Order, Shine, Standardize, Sustain) in Manufacturing
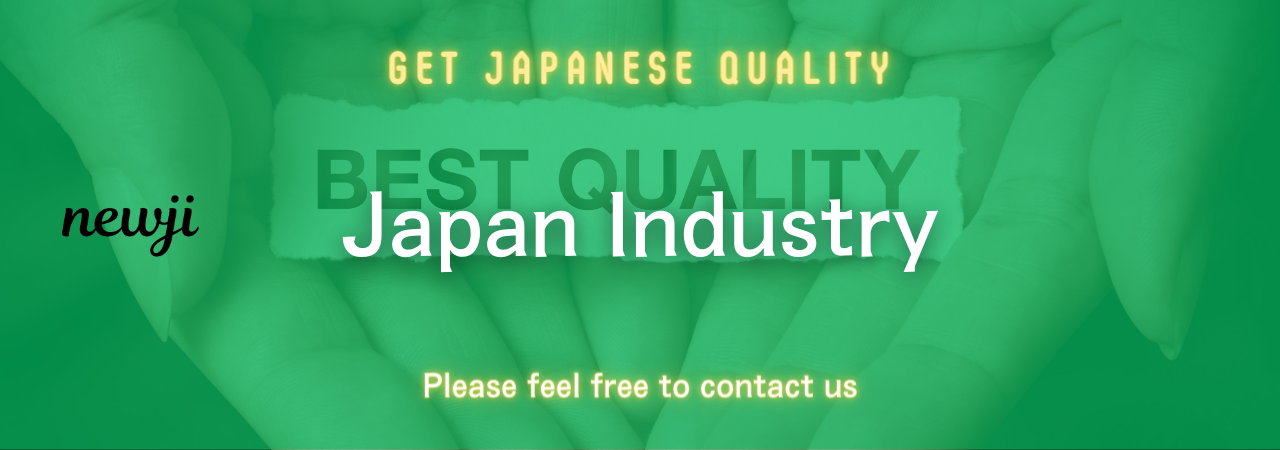
The 5S methodology is a system for organizing spaces so work can be performed efficiently, effectively, and safely.
This system focuses on five principles that can be translated into English as Sort, Set in Order, Shine, Standardize, and Sustain.
In manufacturing, applying the 5S principles helps to improve productivity and reduce waste.
目次
Understanding 5S
The concept of 5S originated in Japan and is part of the larger Lean Manufacturing philosophy.
Each of the five components is designed to foster efficiency and streamline operations.
Sort
The first ‘S’ stands for Sort.
This step involves going through all the tools, materials, and resources available in the manufacturing area and eliminating anything unnecessary.
The goal is to keep only what is needed.
Unnecessary items are either disposed of or placed in storage locations farther from the workplace.
Set in Order
Once sorting is complete, the next step is Set in Order.
This means organizing the necessary items so that they are easy to access and return to their designated places.
Tools should be arranged in a way that reflects the sequence in which tasks are performed.
For example, commonly used tools should be within easy reach, while less frequently used items can be placed in more remote locations.
Shine
Shine involves cleaning the workplace and maintaining its appearance and equipment.
Regular cleaning eliminates dirt, dust, and clutter, making it easier to spot potential problems like leaks or worn parts.
A clean work environment boosts morale and efficiency and ensures that machinery runs smoothly.
Standardize
Standardizing means establishing common processes and practices for carrying out tasks and organizing space.
This step ensures everyone in the organization knows their responsibilities and follows the same protocols.
Checklists, signage, color-coding, and other visual cues can be used to help maintain consistency.
Sustain
The final step, Sustain, ensures the ongoing application of the 5S methodology.
The organization must commit to regular audits and reviews to maintain 5S principles.
This can involve training for new employees, routine checks, and continuous improvement meetings to ensure adherence to the standards set.
Benefits of Implementing 5S in Manufacturing
Improved Efficiency
By sorting and organizing tools and materials, workers spend less time searching for what they need.
This directly boosts productivity and reduces downtime.
Enhanced Safety
A well-organized and clean workspace minimizes the risk of accidents.
Clear labeling and orderly storage mean fewer tripping hazards and better awareness of surroundings.
Reduced Waste
When materials and tools are kept in order, it reduces the likelihood of overstocking or losing items.
This translates to less waste and more efficient use of resources.
Better Maintenance
Regular cleaning under the Shine principle means that machinery and tools are better maintained.
This reduces mechanical failures and extends the life of equipment.
Higher Morale
Employees are likely to feel more satisfied and motivated when working in a well-organized and clean environment.
A standardized system means that everyone knows their role and how to achieve expected standards.
Best Practices for Implementing 5S
Start Small
Instead of trying to implement 5S across the entire facility, start with a single area or department.
This allows for a focused approach and quicker adjustments based on initial outcomes.
Success in one area can then serve as a model for other areas.
Get Everyone Involved
5S is a team effort.
Encourage involvement from all levels of the organization, from management to floor workers.
Inclusive efforts can lead to creative solutions and better buy-in from all employees.
Provide Training
Proper training ensures that everyone understands the principles and objectives of 5S.
Workshops, manuals, and continuous learning opportunities can help embed the 5S principles into the company culture.
Use Visual Aids
Visual aids such as labels, signs, and floor markings can enhance organization and understanding.
Photos of how a perfectly organized workspace looks can offer employees clear examples to follow.
Perform Regular Audits
Routine checks and audits ensure that the standards are maintained.
An audit schedule can include daily, weekly, and monthly evaluations to catch any deviations early.
Challenges and Solutions
Resistance to Change
Change can be difficult, and some employees may resist adopting the new practices.
Effective communication about the benefits and involving employees in the process can mitigate resistance.
Maintaining Consistency
Sustaining the 5S principles can be challenging over time.
Regular training, audits, and encouraging a culture of continuous improvement can help maintain consistency.
Lack of Resources
Sometimes, lack of time or financial resources can hinder the implementation of 5S.
Prioritizing budget allocation and time management for 5S activities can address this issue.
Starting small and scaling gradually can also help manage resource constraints effectively.
Applying the 5S methodology in manufacturing is not just about cleaning and organizing.
It’s about creating a culture that values efficiency, safety, and continuous improvement.
By focusing on Sort, Set in Order, Shine, Standardize, and Sustain, manufacturers can see significant improvements in productivity, morale, and overall operational effectiveness.
資料ダウンロード
QCD調達購買管理クラウド「newji」は、調達購買部門で必要なQCD管理全てを備えた、現場特化型兼クラウド型の今世紀最高の購買管理システムとなります。
ユーザー登録
調達購買業務の効率化だけでなく、システムを導入することで、コスト削減や製品・資材のステータス可視化のほか、属人化していた購買情報の共有化による内部不正防止や統制にも役立ちます。
NEWJI DX
製造業に特化したデジタルトランスフォーメーション(DX)の実現を目指す請負開発型のコンサルティングサービスです。AI、iPaaS、および先端の技術を駆使して、製造プロセスの効率化、業務効率化、チームワーク強化、コスト削減、品質向上を実現します。このサービスは、製造業の課題を深く理解し、それに対する最適なデジタルソリューションを提供することで、企業が持続的な成長とイノベーションを達成できるようサポートします。
オンライン講座
製造業、主に購買・調達部門にお勤めの方々に向けた情報を配信しております。
新任の方やベテランの方、管理職を対象とした幅広いコンテンツをご用意しております。
お問い合わせ
コストダウンが利益に直結する術だと理解していても、なかなか前に進めることができない状況。そんな時は、newjiのコストダウン自動化機能で大きく利益貢献しよう!
(Β版非公開)