- お役立ち記事
- Best practices for designing human resource development programs that produce results in the manufacturing industry
月間76,176名の
製造業ご担当者様が閲覧しています*
*2025年3月31日現在のGoogle Analyticsのデータより
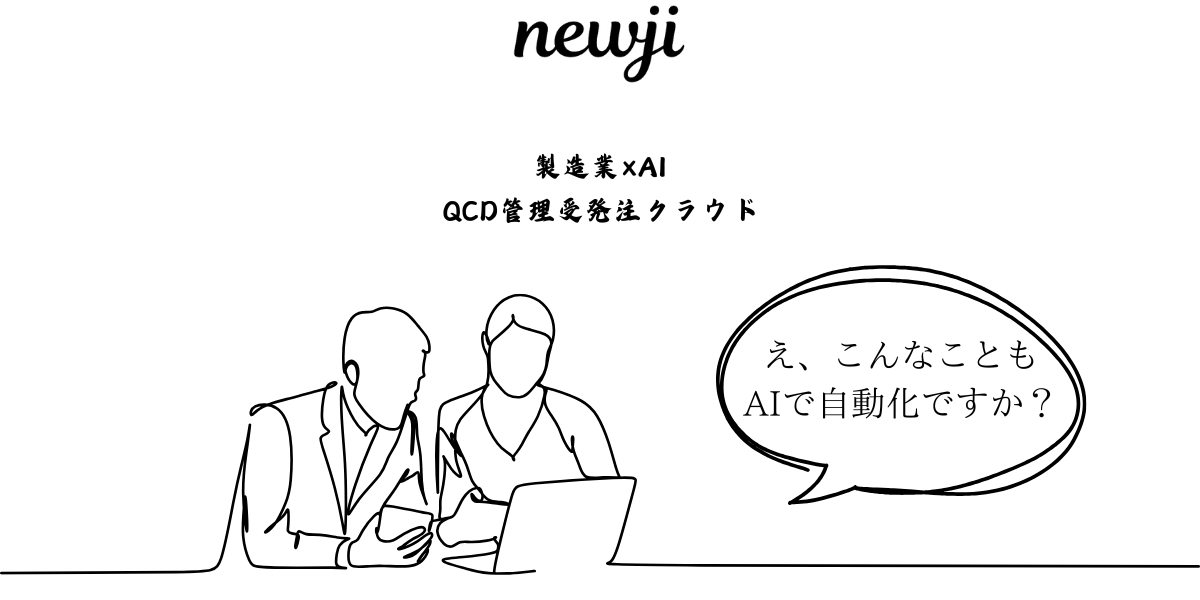
Best practices for designing human resource development programs that produce results in the manufacturing industry
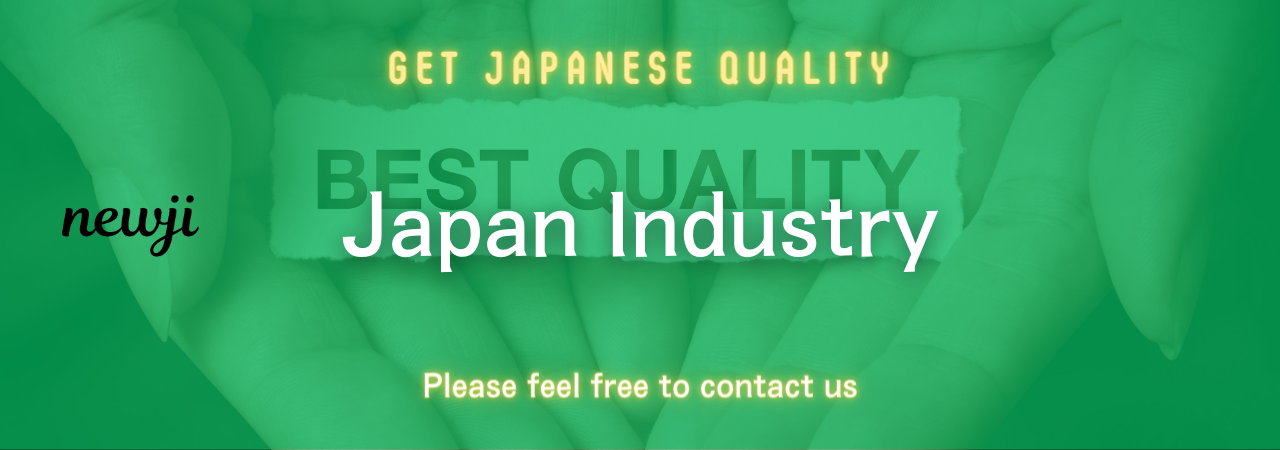
目次
Understanding Human Resource Development in Manufacturing
The manufacturing industry is a dynamic sector that plays a critical role in any economy.
To maintain competitiveness and drive productivity, it’s essential for manufacturing companies to focus on developing their human resources effectively.
Human resource development (HRD) programs are crucial in cultivating a skilled and competent workforce that meets the industry’s evolving demands.
Manufacturing is unique due to its reliance on both human labor and technology.
This necessitates HRD programs that not only improve traditional skills but also adapt to technological advancements.
To design HRD programs that yield tangible results, manufacturers must consider various best practices that align with the industry’s specific needs.
Identifying Skills Gaps
Before crafting an HRD program, it’s vital to conduct a comprehensive analysis to identify existing skills gaps within the workforce.
This involves evaluating the current skills of employees and comparing them with the skills required to meet organizational goals.
In the manufacturing industry, skills gaps can emerge due to rapid technological changes or the introduction of new production processes.
For instance, the integration of automation and robotics has altered the skill sets required on the factory floor.
By pinpointing these gaps, companies can tailor their training programs to address immediate needs and prepare employees for future challenges.
Aligning Programs with Business Goals
Effective HRD programs are aligned with the strategic goals of the organization.
This requires a close collaboration between HR managers and business leaders to ensure that the training initiatives support the company’s overall objectives.
For manufacturing companies, this might mean focusing on improving productivity, enhancing product quality, or reducing waste.
When training programs are directly linked to business outcomes, they not only promote workforce development but also contribute to the company’s success.
Aligning programs with business goals ensures that resources are utilized efficiently and that employees see the relevance of their training in real-world applications.
Incorporating Technology in Training
The incorporation of technology in HRD programs is essential for the manufacturing industry.
Training methods should leverage the latest technological tools and platforms to enhance learning and engagement.
For example, virtual reality (VR) and augmented reality (AR) can be used to simulate manufacturing environments, allowing employees to gain hands-on experience without the associated risks.
Moreover, e-learning platforms can offer flexible, on-demand training modules that accommodate diverse learning paces and styles.
The strategic use of technology not only optimizes the learning process but also fosters a culture of continuous development within the organization.
Emphasizing Continuous Learning
In the fast-paced world of manufacturing, continuous learning is vital.
HRD programs should promote a culture where learning is ongoing and employees are encouraged to expand their knowledge and skills regularly.
Companies can achieve this by providing access to resources such as online courses, workshops, and seminars.
Encouraging employees to pursue further education and certifications can keep them motivated and engaged.
Additionally, establishing mentorship programs where experienced workers guide newer colleagues can enhance knowledge transfer and foster a collaborative learning environment.
Evaluating Program Effectiveness
To ensure HRD programs deliver the desired results, it’s crucial to establish metrics for evaluation.
This involves setting clear objectives and measuring the outcomes against these benchmarks.
For instance, a manufacturing company might track improvements in production efficiency, error rates, or employee retention as indicators of program success.
Regularly evaluating the effectiveness of training initiatives helps identify areas for improvement and demonstrates a commitment to quality development processes.
Feedback from participants is also valuable in refining programs to better meet their needs.
Fostering a Supportive Learning Environment
A supportive learning environment is critical for the success of any HRD program.
Manufacturers should create a workplace culture that encourages curiosity and values employee development.
Leadership plays a key role in this aspect by championing learning initiatives and providing the necessary resources and encouragement.
Creating spaces where employees can collaborate and share knowledge fosters an open, communicative atmosphere that inspires innovation and growth.
Adapting to Industry Trends
The manufacturing industry is constantly evolving, with new trends and technologies reshaping the landscape.
HRD programs should be dynamic and adaptable to reflect these changes.
Keeping abreast of industry trends allows companies to anticipate the skills and competencies that will be required in the future.
This foresight enables organizations to proactively update their training programs, ensuring their workforce remains competitive and capable of managing change.
Building Partnerships with Educational Institutions
Collaborations with educational institutions can be beneficial for developing effective HRD programs in manufacturing.
These partnerships provide access to cutting-edge research, expert knowledge, and specialized training resources.
By working with universities and technical schools, manufacturing companies can gain insights into the latest industry advancements and incorporate them into their training curricula.
Internship and apprenticeship programs can also be developed in partnership with these institutions, offering students real-world experience while providing companies with potential talent.
Conclusion
Designing HRD programs that produce results in the manufacturing industry requires a thorough understanding of both the sector’s unique challenges and the evolving landscape of skills and technology.
By identifying skills gaps, aligning programs with business objectives, and leveraging technology, companies can create effective training initiatives that promote continuous learning and employee growth.
Evaluating program effectiveness and fostering a supportive learning environment are also crucial components of successful HRD strategy.
As manufacturing evolves, staying responsive to industry trends and building educational partnerships will ensure that HRD programs remain relevant and impactful.
Through these best practices, manufacturing companies can cultivate a skilled workforce that drives innovation and enhances competitiveness.
資料ダウンロード
QCD管理受発注クラウド「newji」は、受発注部門で必要なQCD管理全てを備えた、現場特化型兼クラウド型の今世紀最高の受発注管理システムとなります。
ユーザー登録
受発注業務の効率化だけでなく、システムを導入することで、コスト削減や製品・資材のステータス可視化のほか、属人化していた受発注情報の共有化による内部不正防止や統制にも役立ちます。
NEWJI DX
製造業に特化したデジタルトランスフォーメーション(DX)の実現を目指す請負開発型のコンサルティングサービスです。AI、iPaaS、および先端の技術を駆使して、製造プロセスの効率化、業務効率化、チームワーク強化、コスト削減、品質向上を実現します。このサービスは、製造業の課題を深く理解し、それに対する最適なデジタルソリューションを提供することで、企業が持続的な成長とイノベーションを達成できるようサポートします。
製造業ニュース解説
製造業、主に購買・調達部門にお勤めの方々に向けた情報を配信しております。
新任の方やベテランの方、管理職を対象とした幅広いコンテンツをご用意しております。
お問い合わせ
コストダウンが利益に直結する術だと理解していても、なかなか前に進めることができない状況。そんな時は、newjiのコストダウン自動化機能で大きく利益貢献しよう!
(β版非公開)