- お役立ち記事
- Best practices for establishing a quality assurance system necessary for electronic component manufacturing
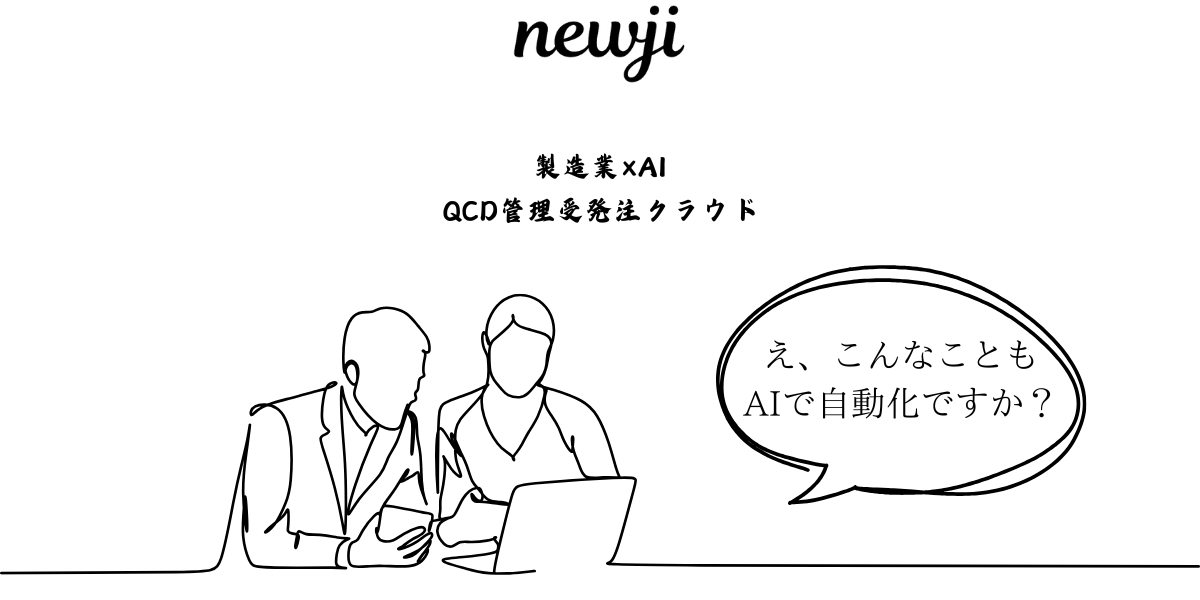
Best practices for establishing a quality assurance system necessary for electronic component manufacturing
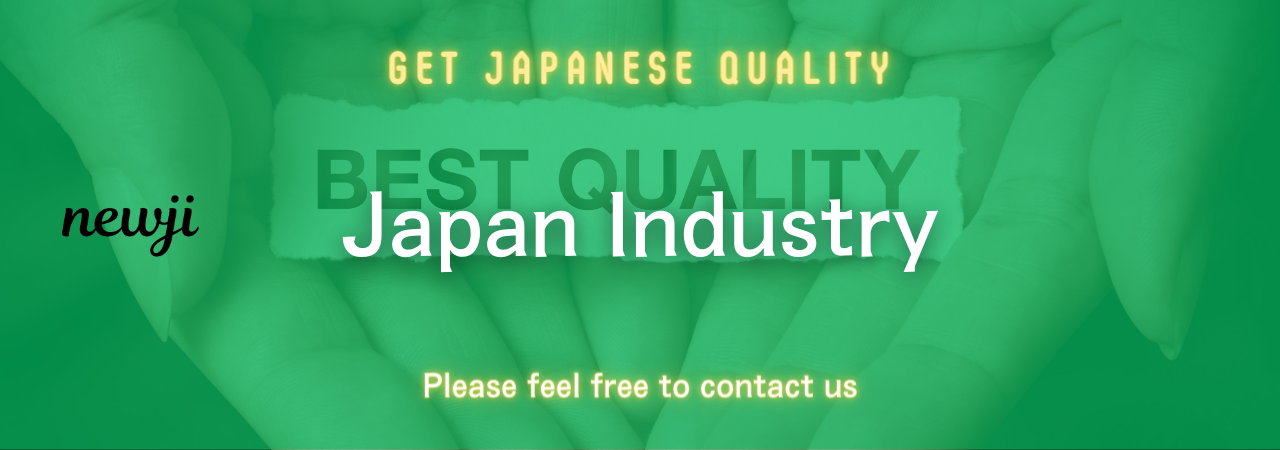
目次
Understanding the Importance of Quality Assurance in Electronic Component Manufacturing
In the world of electronic component manufacturing, maintaining high quality is not just a goal; it’s a necessity.
The demand for reliable, high-performance electronics has never been higher, and a thorough quality assurance system is essential for meeting these expectations.
Quality assurance ensures that products meet strict specifications and industry standards, preventing costly defects and ensuring customer satisfaction.
Key Elements of Quality Assurance Systems
Establishing a robust quality assurance system involves several key elements that work together to maintain high standards.
Let’s explore these essential components.
1. Setting Clear Standards and Specifications
To ensure consistency and quality, manufacturers must first establish clear standards and specifications for their products.
These should be based on industry standards, customer requirements, and regulatory guidelines.
By defining what quality means for a specific product, manufacturers set a clear benchmark against which products are evaluated.
2. Comprehensive Training of Personnel
Employee training is critical in maintaining quality.
Every team member should be well-versed in the company’s quality expectations and procedures.
Regular training sessions help employees stay updated on the latest industry practices and technological advancements, enabling them to perform their roles more effectively.
3. Implementing Rigorous Testing Procedures
Testing is a cornerstone of quality assurance in electronic component manufacturing.
Various testing methods, including functional testing, environmental testing, and stress testing, should be employed to catch defects early.
Regular testing ensures that each component can withstand real-world conditions and performance requirements.
4. Utilizing Advanced Technologies and Tools
Incorporating advanced technology into quality assurance processes enhances precision and efficiency.
Automated testing systems, data analysis software, and AI-driven inspection tools can help identify defects faster and with greater accuracy than manual processes.
Investing in these technologies can significantly improve the overall quality of the manufacturing process.
5. Establishing a Feedback Loop
A feedback loop is essential for a dynamic quality assurance system.
Collecting feedback from different stages of the manufacturing process helps identify areas of improvement.
This might include feedback from production teams, customer reviews, or data from quality tests.
Using this information, manufacturers can make informed adjustments to their processes, reducing defects and improving product quality.
6. Continuous Improvement and Adaptation
The electronics industry is rapidly evolving, and quality assurance systems must be adaptable.
Manufacturers should adopt a mindset of continuous improvement, regularly reviewing and updating their processes and standards.
Embracing new technologies and methodologies can keep the quality assurance system aligned with industry advancements and customer expectations.
Benefits of a Strong Quality Assurance System
A well-implemented quality assurance system offers numerous benefits to electronic component manufacturers.
Here are some key advantages that underline its importance.
Enhanced Product Quality and Reliability
With a robust quality assurance system, manufacturers can ensure that their products consistently meet high standards.
This results in more reliable, durable electronic components, reducing the chances of customer dissatisfaction and product returns.
Cost Reduction
Identifying and addressing issues early in the production process prevents costly errors and recalls.
A strong quality assurance system can save a company substantial amounts by minimizing waste and resource misuse.
Increased Customer Satisfaction
Quality assurance builds trust with customers, as they know they are receiving a product that meets stringent quality standards.
Satisfied customers are more likely to become repeat buyers and recommend the brand to others.
Competitive Advantage
In a highly competitive market, consistent quality can be a significant differentiator.
Companies known for their high-quality products are more likely to gain a competitive edge over those that do not prioritize quality assurance.
Challenges in Implementing a Quality Assurance System
While the benefits are clear, implementing a quality assurance system is not without its challenges.
Understanding these challenges can help manufacturers address them proactively.
Resource Allocation
Developing and maintaining a quality assurance system requires significant resources, including time, personnel, and finances.
Companies must carefully balance these demands to ensure their system is both effective and sustainable.
Keeping Up with Industry Changes
The electronics industry is characterized by rapid changes and technological advancements.
Manufacturers must continually update their quality assurance processes to keep pace with these changes, which can be a daunting task.
Resistance to Change
Implementing a new quality assurance system often involves changes in procedures and technology, which might meet resistance from employees.
Communicating the benefits and providing adequate training can help mitigate this challenge.
Final Thoughts
Establishing a quality assurance system is vital for the success and reputation of electronic component manufacturers.
By setting clear standards, training personnel, implementing rigorous testing, and using advanced technologies, companies can ensure their products meet the high expectations of the modern market.
Although challenges exist, the benefits of a strong quality assurance system—enhanced product reliability, reduced costs, increased customer satisfaction, and competitive advantage—make it a worthwhile investment.
In a world where quality is paramount, a well-designed quality assurance system is a manufacturer’s best ally.
資料ダウンロード
QCD調達購買管理クラウド「newji」は、調達購買部門で必要なQCD管理全てを備えた、現場特化型兼クラウド型の今世紀最高の購買管理システムとなります。
ユーザー登録
調達購買業務の効率化だけでなく、システムを導入することで、コスト削減や製品・資材のステータス可視化のほか、属人化していた購買情報の共有化による内部不正防止や統制にも役立ちます。
NEWJI DX
製造業に特化したデジタルトランスフォーメーション(DX)の実現を目指す請負開発型のコンサルティングサービスです。AI、iPaaS、および先端の技術を駆使して、製造プロセスの効率化、業務効率化、チームワーク強化、コスト削減、品質向上を実現します。このサービスは、製造業の課題を深く理解し、それに対する最適なデジタルソリューションを提供することで、企業が持続的な成長とイノベーションを達成できるようサポートします。
オンライン講座
製造業、主に購買・調達部門にお勤めの方々に向けた情報を配信しております。
新任の方やベテランの方、管理職を対象とした幅広いコンテンツをご用意しております。
お問い合わせ
コストダウンが利益に直結する術だと理解していても、なかなか前に進めることができない状況。そんな時は、newjiのコストダウン自動化機能で大きく利益貢献しよう!
(Β版非公開)