- お役立ち記事
- Best practices for purchasing departments to stabilize material supply chains
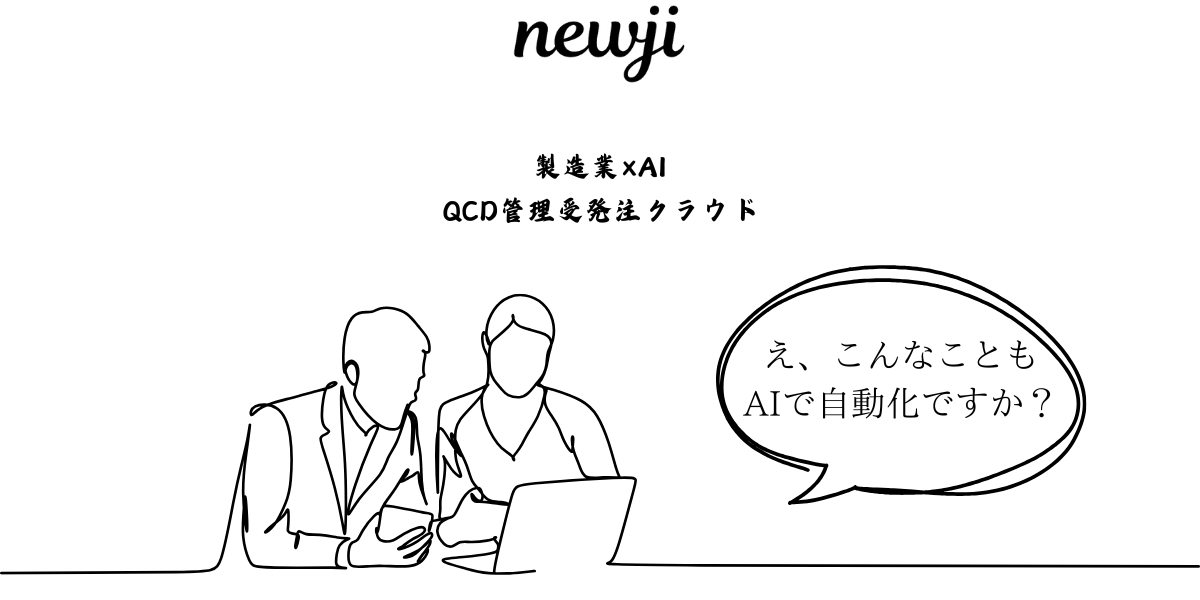
Best practices for purchasing departments to stabilize material supply chains
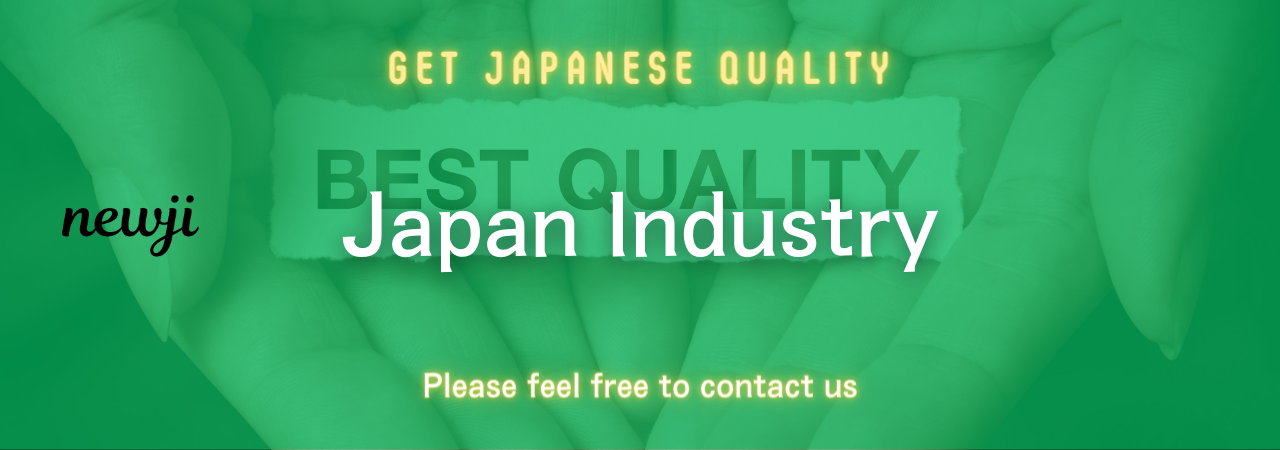
目次
Understanding the Role of Purchasing Departments
Purchasing departments play a critical role in ensuring the smooth operation of businesses by managing the acquisition of goods and services.
They are the backbone of any organization, ensuring that the necessary materials are available to produce goods or provide services.
The efficiency and effectiveness of purchasing departments significantly impact the overall supply chain, which is why stabilizing this sector is paramount for business continuity.
These departments are responsible for negotiating with suppliers, obtaining the best possible prices, and ensuring that products meet specified quality standards.
This requires a mix of strategic decision-making and tactical operations to maintain a steady flow of materials while keeping costs under control.
Purchasing departments must also forecast future material needs and manage inventory levels to prevent shortages or overstocking.
Challenges in Material Supply Chains
Material supply chains face many challenges that can lead to instability.
One of the primary issues is the fluctuation in raw material prices, which can significantly affect manufacturing costs and budgets.
Global economic changes, such as trade tariffs and currency variations, further complicate pricing strategies and require constant monitoring.
Another significant challenge is the unpredictability of supplier reliability.
Factors like political unrest, natural disasters, or strikes can disrupt production and distribution, causing delays and financial losses.
Purchasing departments must have contingency plans in place to navigate these challenges and minimize their impact.
The rise in environmental and social responsibility has also increased pressure on purchasing departments to ensure that their supply chains are ethical and sustainable.
Compliance with regulations and maintaining a positive brand image requires significant effort and coordination with suppliers.
Best Practices for Stabilizing Supply Chains
Develop Strong Supplier Relationships
Building solid relationships with suppliers can greatly enhance the stability of material supply chains.
This involves consistent communication, transparency, and mutual trust.
By fostering good relationships, purchasing departments can negotiate better terms, receive priority in delivery schedules, and gain first-hand information about market trends.
Maintaining regular communication also allows for collaborative problem solving.
Suppliers may offer alternative solutions or adjustments in production schedules during challenging times, thereby alleviating potential disruptions.
Diversify the Supplier Base
Relying on a single supplier for critical materials is risky.
Purchasing departments should diversify their supplier base to ensure a steady supply of resources.
By engaging with multiple suppliers, the risk of a supply chain disruption caused by a single source’s failure is significantly reduced.
This diversification can also lead to competitive pricing, as suppliers will vie for your business, ultimately benefiting from cost reductions.
Implement Advanced Inventory Management Techniques
Effective inventory management is crucial for supply chain stability.
Using advanced techniques, such as just-in-time inventory or safety stock, can help in maintaining optimal levels of materials.
Purchasing departments can leverage technology, like inventory management software, to monitor stock levels in real-time, anticipate shortages, and automate reorder processes.
These tools help in reducing waste, minimizing holding costs, and ensuring materials are always available when needed.
Forecast Demand Accurately
Accurate demand forecasting is essential for aligning purchasing strategies with market needs.
Purchasing departments should use data analytics and historical trends to predict future material requirements and adjust purchase orders accordingly.
Regular review of sales forecasts, seasonality, and market dynamics can prevent over-purchasing or under-purchasing, which can destabilize the supply chain.
Assess and Mitigate Risks
Risk assessment is a vital practice for purchasing departments to safeguard against supply chain disruptions.
Identifying potential risks, such as a supplier’s financial instability or geopolitical issues in supplier countries, allows businesses to develop mitigation strategies in advance.
Risk mitigation strategies might include entering into long-term contracts with suppliers, maintaining safety stock, or developing alternative supply routes that can be activated in times of disruption.
The Role of Technology in Supply Chain Stability
Integrating technology into purchasing operations is becoming increasingly indispensable.
Supply chain management software can enhance visibility across the supply chain, offering insights into every stage of the material flow.
This transparency helps in identifying bottlenecks early, allowing purchasing departments to address issues proactively.
Moreover, technologies like blockchain can offer unparalleled traceability and authentication of materials.
By ensuring that all transactions and movements are recorded accurately, businesses can maintain the integrity and reliability of their supply chains.
AI and machine learning can be used to improve demand forecasts and inventory management, thereby enhancing decision-making capabilities and responsiveness to changes.
Conclusion
Purchasing departments have a vital task of stabilizing material supply chains to ensure operational efficiency and cost-effectiveness.
By adopting best practices such as building strong supplier relationships, diversifying suppliers, using advanced inventory management techniques, forecasting demand accurately, and assessing risks, businesses can significantly enhance supply chain stability.
Technology also plays an influential role, providing tools to optimize operations and mitigate potential disruptions.
Through strategic planning and continuous improvement, purchasing departments can create robust supply chains resilient to the challenges of today’s dynamic market environment.
資料ダウンロード
QCD調達購買管理クラウド「newji」は、調達購買部門で必要なQCD管理全てを備えた、現場特化型兼クラウド型の今世紀最高の購買管理システムとなります。
ユーザー登録
調達購買業務の効率化だけでなく、システムを導入することで、コスト削減や製品・資材のステータス可視化のほか、属人化していた購買情報の共有化による内部不正防止や統制にも役立ちます。
NEWJI DX
製造業に特化したデジタルトランスフォーメーション(DX)の実現を目指す請負開発型のコンサルティングサービスです。AI、iPaaS、および先端の技術を駆使して、製造プロセスの効率化、業務効率化、チームワーク強化、コスト削減、品質向上を実現します。このサービスは、製造業の課題を深く理解し、それに対する最適なデジタルソリューションを提供することで、企業が持続的な成長とイノベーションを達成できるようサポートします。
オンライン講座
製造業、主に購買・調達部門にお勤めの方々に向けた情報を配信しております。
新任の方やベテランの方、管理職を対象とした幅広いコンテンツをご用意しております。
お問い合わせ
コストダウンが利益に直結する術だと理解していても、なかなか前に進めることができない状況。そんな時は、newjiのコストダウン自動化機能で大きく利益貢献しよう!
(Β版非公開)