- お役立ち記事
- Best Practices in Product Quality Management for Manufacturing
Best Practices in Product Quality Management for Manufacturing
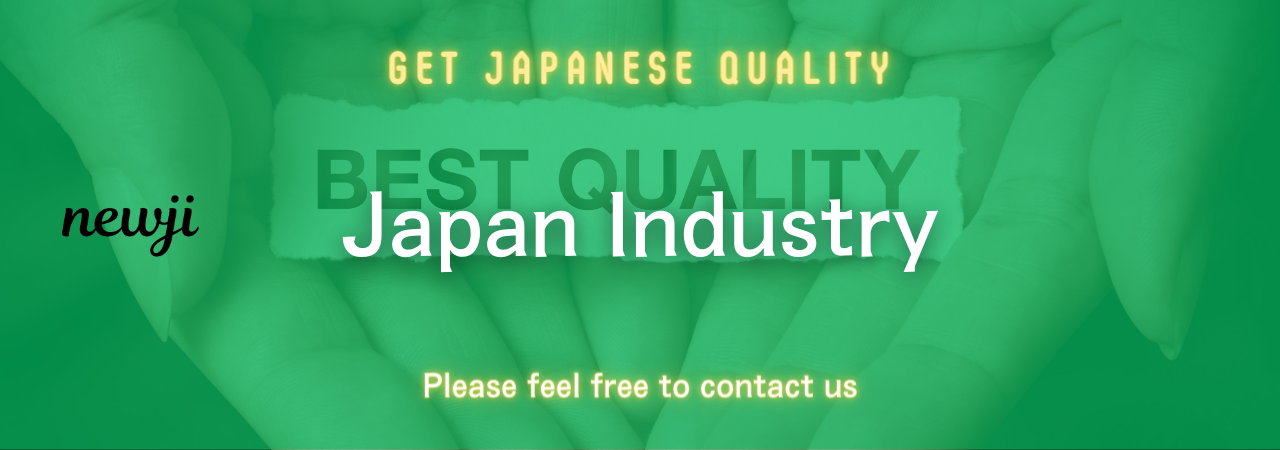
Managing product quality is a pivotal component of success for any manufacturing company.
Effective product quality management ensures that products meet or exceed customer expectations, fostering trust and loyalty while reducing the likelihood of costly recalls or returns.
In this article, we will explore best practices in product quality management for manufacturing companies.
目次
Understanding Product Quality Management
Product quality management encompasses all activities and processes aimed at ensuring that manufactured products meet specified standards.
These standards can be regulatory, industry-specific, or company-specific, and they typically cover aspects such as durability, performance, safety, and aesthetics.
Establishing Quality Control Systems
One of the first steps in effective product quality management is to establish robust quality control systems.
These systems are designed to monitor and evaluate the quality of products at various stages of the manufacturing process.
They involve regular inspections, testing, and measurement of products to ensure they align with predefined standards.
Implementing Total Quality Management (TQM)
Total Quality Management (TQM) is a holistic approach that focuses on continuous improvement in all areas of the organization.
TQM emphasizes customer satisfaction, employee involvement, and process improvement.
By adopting TQM principles, companies can create a culture of quality where every employee takes responsibility for product quality.
Setting Clear Quality Standards
Setting clear quality standards is crucial for manufacturing companies aiming to uphold product quality.
These standards should be well-defined and documented, making them easily accessible to all employees involved in the production process.
Specifying Product Requirements
Product requirements form the basis of quality standards.
They should outline the technical specifications, performance criteria, and regulatory requirements that the product must meet.
By having clear product requirements, companies can align their manufacturing processes to consistently produce high-quality products.
Regularly Reviewing and Updating Standards
Quality standards should not be static.
They need to be reviewed and updated regularly to adapt to changing market demands, technological advancements, and regulatory changes.
Continuous review ensures that the standards remain relevant and effective in maintaining product quality.
Incorporating Advanced Quality Tools and Techniques
Modern manufacturing companies have access to a wide range of advanced quality tools and techniques that can help monitor and improve product quality.
Incorporating these tools into the manufacturing process can significantly enhance product quality management.
Utilizing Statistical Process Control (SPC)
Statistical Process Control (SPC) is a method used to monitor and control production processes through statistical analysis.
SPC helps identify variations in the manufacturing process that may affect product quality.
By analyzing this data, companies can take preventive actions to correct any deviations and maintain consistent product quality.
Applying Six Sigma Methodology
Six Sigma is a data-driven methodology that focuses on improving quality by identifying and eliminating defects in processes.
It employs various tools and techniques, such as DMAIC (Define, Measure, Analyze, Improve, Control), to systematically reduce variability and improve product quality.
Implementing Six Sigma can lead to significant quality improvements and cost savings.
Ensuring Supplier Quality Management
Suppliers play a critical role in the overall quality of manufactured products.
Therefore, it is essential to implement effective supplier quality management to ensure that the raw materials and components used in manufacturing meet the required quality standards.
Selecting Reliable Suppliers
The first step in supplier quality management is selecting reliable suppliers who have a proven track record of delivering high-quality materials.
This can be done through a thorough evaluation process that includes assessing the supplier’s quality management systems, production capabilities, and past performance.
Conducting Regular Supplier Audits
Regular supplier audits are essential to verify that suppliers continue to meet quality standards.
Audits involve on-site inspections, reviews of the supplier’s quality control processes, and testing of materials.
By conducting regular audits, companies can ensure that their suppliers consistently provide high-quality materials.
Training and Development for Quality Improvement
Investing in training and development for employees is crucial for maintaining and improving product quality.
Quality management training equips employees with the necessary skills and knowledge to uphold quality standards and continuously improve processes.
Providing Quality Management Training
Quality management training should be provided to employees at all levels of the organization.
This training can include topics such as quality control techniques, problem-solving methods, and standards compliance.
Well-informed employees are better equipped to identify and address quality issues effectively.
Encouraging Continuous Learning
Fostering a culture of continuous learning and improvement is essential for long-term success in product quality management.
Encouraging employees to stay updated with industry trends, new technologies, and best practices can lead to ongoing enhancements in product quality.
Leveraging Technology for Quality Management
Advancements in technology have revolutionized quality management in manufacturing.
By leveraging technology, companies can streamline quality control processes, increase efficiency, and improve accuracy.
Implementing Quality Management Software (QMS)
Quality Management Software (QMS) is a powerful tool that helps companies manage and monitor quality processes digitally.
QMS can automate workflows, track quality data, and generate reports, providing real-time insights into product quality.
Implementing QMS can lead to more efficient quality management and faster decision-making.
Using IoT and AI for Quality Control
The Internet of Things (IoT) and Artificial Intelligence (AI) are transforming quality control in manufacturing.
IoT devices can monitor production processes in real-time, detecting any anomalies that may affect quality.
AI algorithms can analyze large datasets to identify patterns and predict potential quality issues before they occur.
By integrating IoT and AI, companies can enhance their proactive approach to quality management.
Conclusion
Effective product quality management is essential for manufacturing companies to ensure customer satisfaction, reduce costs, and maintain a competitive edge.
By establishing robust quality control systems, setting clear quality standards, incorporating advanced quality tools, ensuring supplier quality, investing in training, and leveraging technology, companies can achieve and maintain high product quality.
Implementing these best practices can lead to continuous improvement, enhanced product reliability, and long-term success in the manufacturing industry.
資料ダウンロード
QCD調達購買管理クラウド「newji」は、調達購買部門で必要なQCD管理全てを備えた、現場特化型兼クラウド型の今世紀最高の購買管理システムとなります。
ユーザー登録
調達購買業務の効率化だけでなく、システムを導入することで、コスト削減や製品・資材のステータス可視化のほか、属人化していた購買情報の共有化による内部不正防止や統制にも役立ちます。
NEWJI DX
製造業に特化したデジタルトランスフォーメーション(DX)の実現を目指す請負開発型のコンサルティングサービスです。AI、iPaaS、および先端の技術を駆使して、製造プロセスの効率化、業務効率化、チームワーク強化、コスト削減、品質向上を実現します。このサービスは、製造業の課題を深く理解し、それに対する最適なデジタルソリューションを提供することで、企業が持続的な成長とイノベーションを達成できるようサポートします。
オンライン講座
製造業、主に購買・調達部門にお勤めの方々に向けた情報を配信しております。
新任の方やベテランの方、管理職を対象とした幅広いコンテンツをご用意しております。
お問い合わせ
コストダウンが利益に直結する術だと理解していても、なかなか前に進めることができない状況。そんな時は、newjiのコストダウン自動化機能で大きく利益貢献しよう!
(Β版非公開)