- お役立ち記事
- Blade Design and Aerodynamic Analysis for Aircraft Engines
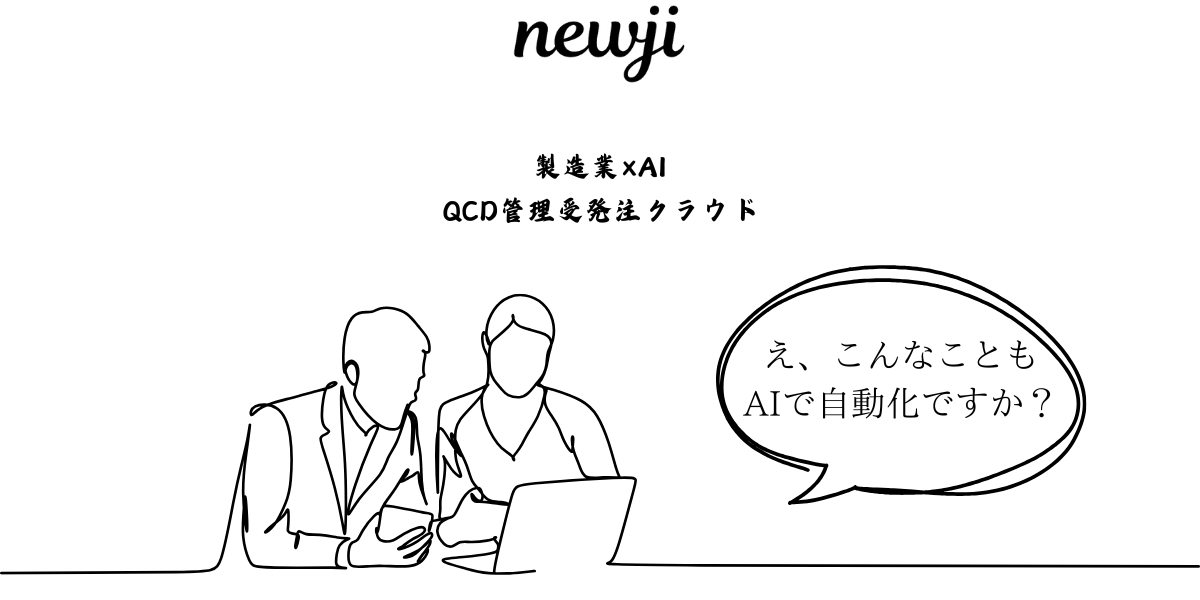
Blade Design and Aerodynamic Analysis for Aircraft Engines
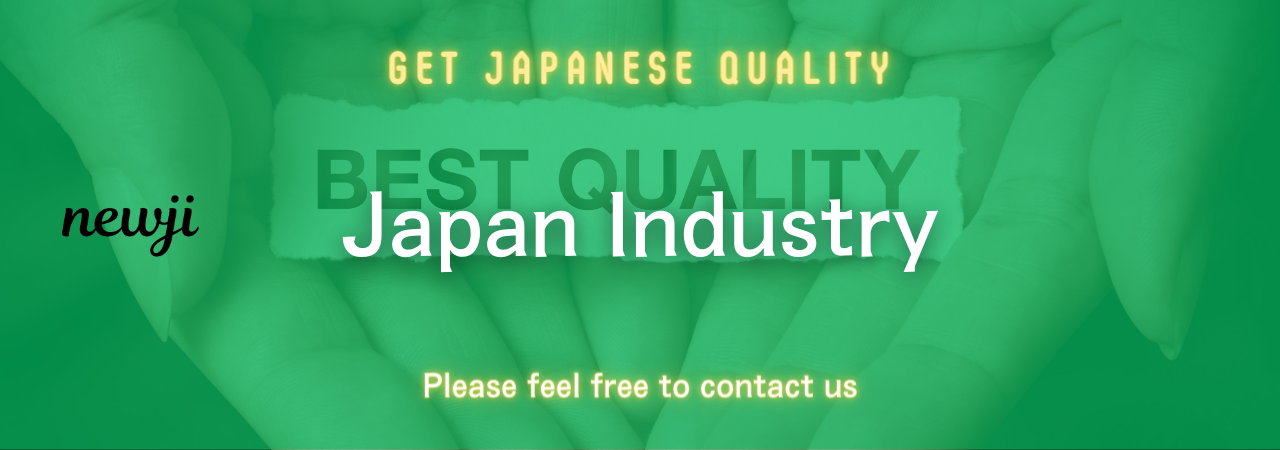
Understanding how aircraft engines work involves a deep dive into their blade design and aerodynamic principles.
Aircraft engine efficiency and performance are significantly influenced by blade design, making it a crucial aspect in aeronautical engineering.
This article will explore the essentials of blade design and the importance of aerodynamics in aircraft engines.
目次
Importance of Blade Design in Aircraft Engines
The blade is one of the essential components of an aircraft engine.
Its design affects the engine’s ability to produce thrust and its overall efficiency.
Here’s why blade design is vital:
Thrust Production
Thrust is the force that propels an aircraft forward.
Blades must be designed to optimize the amount of air they move, increasing the thrust produced by the engine.
Well-designed blades can efficiently convert the energy from the engine into forward motion.
Fuel Efficiency
The efficiency of fuel consumption is a critical factor in aviation.
Blades with poor design increase drag, leading to more fuel usage to maintain speed and altitude.
Conversely, optimized blade design can save significant amounts of fuel, reducing costs and environmental impact.
Durability and Maintenance
Aircraft engines must withstand enormous stress and extreme conditions.
Blade design must account for these challenges to ensure durability and minimize wear and tear.
Improving blade design can extend the time between maintenance intervals, reducing costs and downtime.
Aerodynamic Principles in Blade Design
Aerodynamics studies how air moves around objects.
Understanding aerodynamic principles is essential for designing efficient blades.
The main aerodynamic principles include lift, drag, and airflow patterns.
Lift and Drag
Lift is the force that opposes the weight of the aircraft and allows it to stay in the air.
Drag is the resistance force that opposes the aircraft’s motion.
Blades must be designed to maximize lift and minimize drag to enhance the engine’s performance.
Achieving the right balance between lift and drag is a complex engineering challenge.
Airflow Patterns
Airflow patterns around the blades affect how air is compressed and expelled from the engine.
Laminar airflow, where air moves in smooth layers, is ideal as it reduces drag and increases efficiency.
Turbulent airflow, in contrast, creates more drag and can lead to inefficiencies.
Designing blades to promote laminar airflow is crucial.
Computational Fluid Dynamics (CFD) in Blade Design
Modern advancements in technology, like Computational Fluid Dynamics (CFD), have revolutionized blade design.
CFD simulations allow engineers to model and analyze airflow around blades before physical testing.
These simulations can predict how changes in design affect performance.
Modeling and Simulation
CFD uses numerical methods and algorithms to solve and analyze problems involving fluid flows.
By creating a virtual model of the blade, engineers can simulate how air interacts with the blade surface.
These simulations can reveal potential issues and allow for adjustments without expensive physical prototypes.
Benefits of CFD
CFD provides several benefits in blade design.
It reduces the time and cost associated with physical testing and prototyping.
Engineers can explore multiple design variations quickly and efficiently.
CFD also enhances the accuracy of predictions, leading to more optimized blade designs.
Material Considerations in Blade Design
The materials used in blade construction also play a pivotal role in performance and efficiency.
Modern blades are often made from advanced composites and alloys designed to withstand high temperatures and stresses.
Composite Materials
Composite materials combine different substances to create materials with superior properties.
In blades, composites can offer lightweight strength, reducing the overall weight of the engine and improving fuel efficiency.
They can also increase resistance to heat and stress, enhancing durability.
Alloys
Advanced alloys are used in blade design to provide strength and heat resistance.
Nickel-based superalloys, for example, can withstand the high temperatures found in jet engines.
These materials ensure that the blades maintain their integrity and performance even under extreme conditions.
Future Trends in Blade Design
The evolution of blade design continues as technology advances.
Future trends focus on enhancing efficiency, reducing environmental impact, and improving sustainability.
3D Printing
3D printing, or additive manufacturing, is emerging as a game-changer in blade design.
This technology allows for the creation of complex geometries that traditional manufacturing methods cannot achieve.
Blades created with 3D printing can have optimized shapes for better aerodynamics and performance.
Sustainable Materials
With growing environmental concerns, there is a push toward using sustainable materials in blade manufacturing.
Research is ongoing into biodegradable composites and recyclable materials to minimize the environmental footprint of aircraft engines.
Artificial Intelligence (AI) and Machine Learning
AI and machine learning are being integrated into blade design processes.
These technologies can analyze large datasets to identify patterns and optimize design parameters.
AI can also assist in predictive maintenance, ensuring that blades are serviced before failures occur, improving safety and reliability.
In conclusion, blade design and aerodynamic principles are at the heart of aircraft engine efficiency and performance.
Advancements in computational tools, materials, and manufacturing techniques continue to push the boundaries of what is possible.
Understanding these elements is essential for anyone involved in the field of aeronautical engineering, as they shape the future of aviation.
資料ダウンロード
QCD調達購買管理クラウド「newji」は、調達購買部門で必要なQCD管理全てを備えた、現場特化型兼クラウド型の今世紀最高の購買管理システムとなります。
ユーザー登録
調達購買業務の効率化だけでなく、システムを導入することで、コスト削減や製品・資材のステータス可視化のほか、属人化していた購買情報の共有化による内部不正防止や統制にも役立ちます。
NEWJI DX
製造業に特化したデジタルトランスフォーメーション(DX)の実現を目指す請負開発型のコンサルティングサービスです。AI、iPaaS、および先端の技術を駆使して、製造プロセスの効率化、業務効率化、チームワーク強化、コスト削減、品質向上を実現します。このサービスは、製造業の課題を深く理解し、それに対する最適なデジタルソリューションを提供することで、企業が持続的な成長とイノベーションを達成できるようサポートします。
オンライン講座
製造業、主に購買・調達部門にお勤めの方々に向けた情報を配信しております。
新任の方やベテランの方、管理職を対象とした幅広いコンテンツをご用意しております。
お問い合わせ
コストダウンが利益に直結する術だと理解していても、なかなか前に進めることができない状況。そんな時は、newjiのコストダウン自動化機能で大きく利益貢献しよう!
(Β版非公開)