- お役立ち記事
- BOM basics and construction points, and application to reuse and standardization design
月間76,176名の
製造業ご担当者様が閲覧しています*
*2025年3月31日現在のGoogle Analyticsのデータより
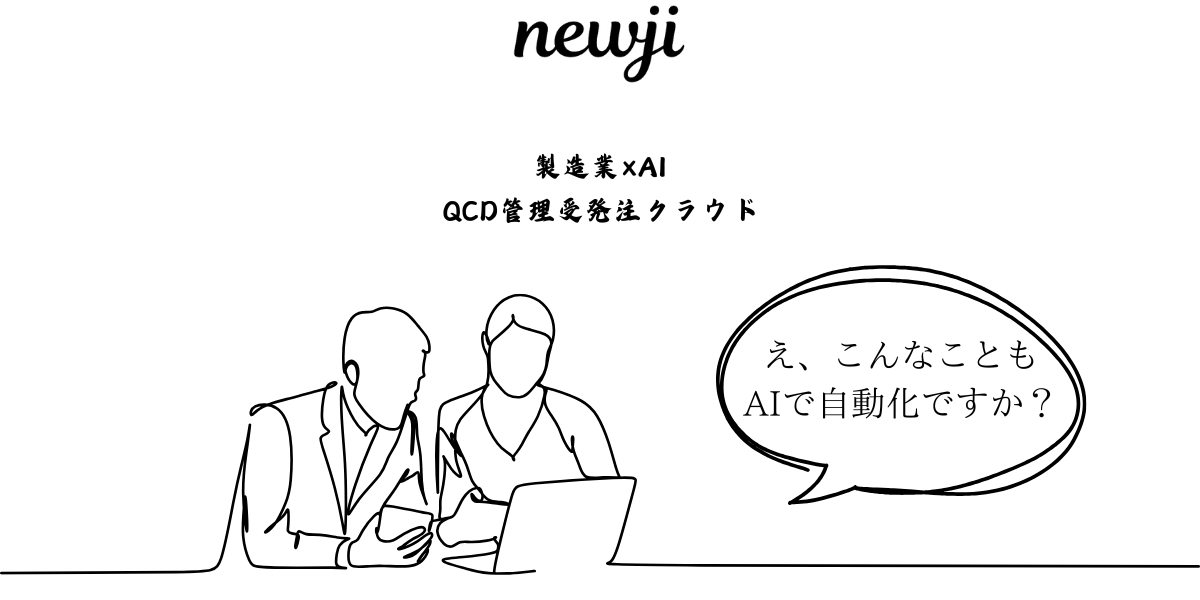
BOM basics and construction points, and application to reuse and standardization design
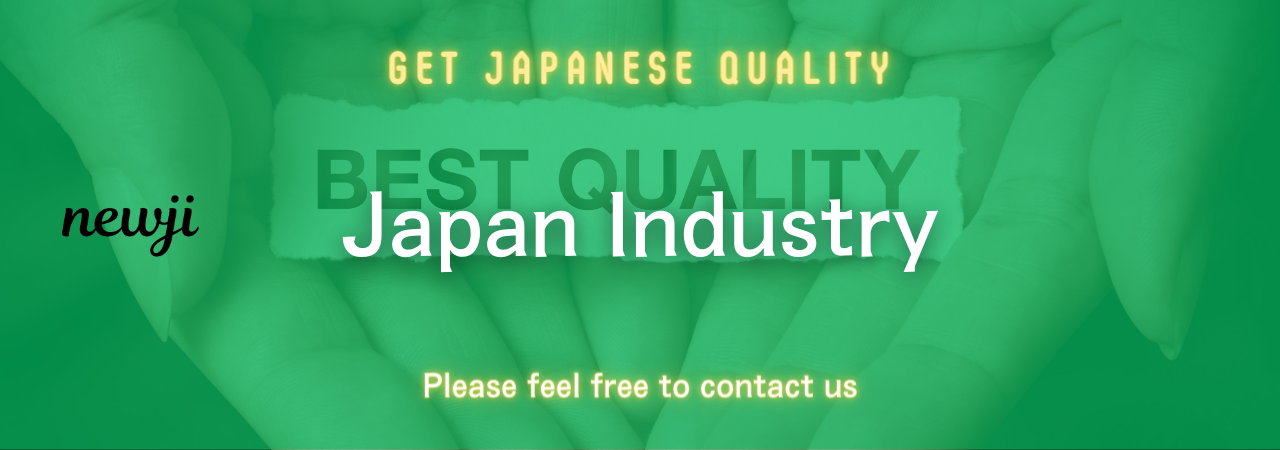
目次
Understanding the Basics of BOM
A Bill of Materials, commonly known as BOM, is an essential component in the manufacturing and production industries.
It serves as the comprehensive list detailing all the raw materials, components, and instructions necessary to construct, manufacture, or repair a product.
Imagine building a Lego set; the BOM is akin to the manual that tells you which bricks you need and where they go.
This document is vital for ensuring that a product is made precisely to specifications and assists in cost estimation and resource planning.
Each item on a BOM holds a unique part number, description, quantity, and unit of measure.
Having an accurate BOM helps manufacturers predict the materials needed, which ultimately aids in managing inventories effectively.
Key Points in BOM Construction
To construct a BOM successfully, several important factors need to be considered.
First and foremost is accuracy.
Every material required for assembly must be documented to prevent production delays or errors.
Next, clarity is crucial.
Items should be clearly described to avoid any ambiguity.
This includes proper part numbers, descriptions, and appropriate units of measure.
Moreover, hierarchy matters in BOM construction.
BOMs are structured to reflect the product’s composition, meaning components are listed according to the assembly sequence.
For multi-layered products, indentations indicate sub-assemblies, which help with understanding material relationships.
Another point is documentation control.
With multiple versions of products, having controlled documentation ensures the current version is being manufactured.
Manufacturers often implement systems to track changes and record updates.
Finally, integration with other systems is important.
Your BOM should integrate with inventory management systems, production planning, and procurement to ensure a seamless flow of information across departments.
Applying BOM to Reuse
One of the advantages of a well-constructed BOM is the ability to reuse materials and components in different products.
Standardization plays a significant role here, allowing organizations to streamline their production processes by using common parts for various products.
When a company decides to design a new product, they can refer to existing BOMs to identify parts that can be reused.
This not only saves on cost but also reduces the time required for sourcing and production.
By identifying reusable components, companies can also minimize waste, contributing to more sustainable manufacturing practices.
Standardization in BOM
Standardization in a BOM involves using uniform specifications and procedures across products to simplify the production process.
It is achieved by using common components and practices within a product line or even across different product lines.
The process of standardizing parts helps organizations achieve economies of scale, leading to cost reductions.
By standardizing materials or parts, manufacturers can purchase in bulk, which reduces purchase costs and handling time.
Additionally, standardizing facilitates better maintenance and repair processes, as technicians can rely on a familiar set of parts and procedures.
Design for Reuse
Designing with reuse in mind is an integral aspect of modern manufacturing practices.
When companies design parts for reuse, they emphasize flexibility, durability, and compatibility.
The emphasis is placed on designing components that have a longer life cycle, can withstand multiple applications, and maintain efficiency across different products.
This design philosophy can lead to innovative products that are not only efficient but also environmentally friendly.
Such innovations are increasingly becoming a competitive advantage in markets where sustainability is valued by consumers.
Reusable design contributes to a circular economy, where products and materials are used to their fullest extent, then recycled back into the production cycle, reducing the environmental impact.
Conclusion
Understanding the basics of BOM and its application to reuse and standardization is crucial for effective production management.
A precise, clear, and well-integrated BOM aids in every stage of the production process, from planning to execution.
Emphasizing reuse through smart BOM practices leads to cost savings, efficient resource utilization, and a positive impact on the environment.
By focusing on standardization, businesses can simplify their processes, enhance product quality, and remain competitive.
Finally, design strategies that prioritize reuse foster sustainability, aligning business objectives with environmental stewardship.
In today’s competitive landscape, leveraging BOM for strategic advantages is not just beneficial, it’s necessary for the enduring success of manufacturing operations.
資料ダウンロード
QCD管理受発注クラウド「newji」は、受発注部門で必要なQCD管理全てを備えた、現場特化型兼クラウド型の今世紀最高の受発注管理システムとなります。
ユーザー登録
受発注業務の効率化だけでなく、システムを導入することで、コスト削減や製品・資材のステータス可視化のほか、属人化していた受発注情報の共有化による内部不正防止や統制にも役立ちます。
NEWJI DX
製造業に特化したデジタルトランスフォーメーション(DX)の実現を目指す請負開発型のコンサルティングサービスです。AI、iPaaS、および先端の技術を駆使して、製造プロセスの効率化、業務効率化、チームワーク強化、コスト削減、品質向上を実現します。このサービスは、製造業の課題を深く理解し、それに対する最適なデジタルソリューションを提供することで、企業が持続的な成長とイノベーションを達成できるようサポートします。
製造業ニュース解説
製造業、主に購買・調達部門にお勤めの方々に向けた情報を配信しております。
新任の方やベテランの方、管理職を対象とした幅広いコンテンツをご用意しております。
お問い合わせ
コストダウンが利益に直結する術だと理解していても、なかなか前に進めることができない状況。そんな時は、newjiのコストダウン自動化機能で大きく利益貢献しよう!
(β版非公開)