- お役立ち記事
- BOM (Bill of Materials)/PLM basics and key points for DX success
BOM (Bill of Materials)/PLM basics and key points for DX success
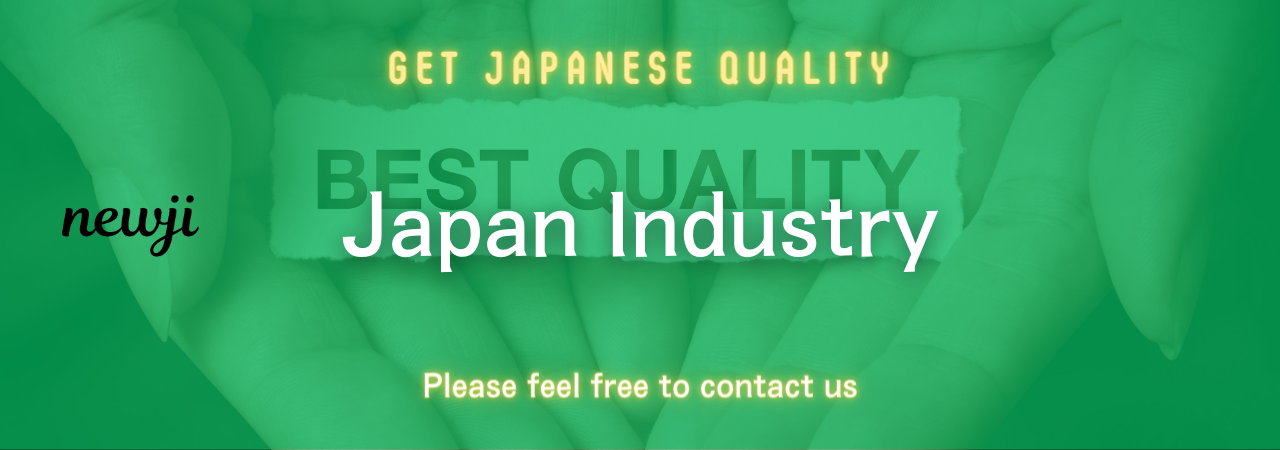
目次
Understanding the Basics of BOM and PLM
When we talk about modern manufacturing and product lifecycle management, two critical concepts often arise: BOM (Bill of Materials) and PLM (Product Lifecycle Management).
These are essential for efficient production processes and successful digital transformation (DX) in any manufacturing organization.
Let’s first define these terms for clearer understanding and explore their roles in the process.
What is BOM?
A Bill of Materials (BOM) is essentially the complete list of raw materials, components, assemblies, and sub-assemblies required to manufacture a product.
Think of it as a recipe for product creation that details each ingredient necessary in the exact amount and order for a successful build.
There are two main types of BOMs: Engineering BOMs (EBOM) and Manufacturing BOMs (MBOM).
Engineering BOMs are created by engineers during the design phase.
They represent the product as designed, outlining all components from the engineering perspective.
Manufacturing BOMs, on the other hand, are used during the product manufacturing phase.
They cater to how the product will be assembled, focusing on all production requirements.
What is PLM?
Product Lifecycle Management (PLM) is a systematic approach to managing the series of stages a product goes through, from initial concept through to its eventual disposal.
PLM involves integrating people, processes, and technology to manage product data throughout its lifecycle.
PLM acts as a unified platform, ensuring all parties have access to up-to-date product information.
This helps in reducing errors, improving collaboration, and speeding up time to market.
The Intersection of BOM and PLM
The relationship between BOM and PLM is crucial, as they complement each other to ensure efficient product management.
BOMs are managed within the PLM system, allowing for easy updates and consistency across departments.
With an effective PLM system, any changes made in the BOM are automatically updated for all stakeholders.
This ensures that everyone involved is working with the most recent data, minimizing errors and streamlining manufacturing processes.
Key Points for DX Success
Digital transformation involves employing digital technologies to fundamentally change business operations and provide new value to customers.
Successfully integrating BOM and PLM is key to achieving DX success in manufacturing.
Here are some vital points:
1. Centralized Data Management
By leveraging a PLM system, organizations can manage all product-related data in a centralized location.
This enables easier access, better security, and ensures everyone is working with accurate and up-to-date information.
Centralization enhances collaboration across departments, as well as with external partners or suppliers.
2. Improved Collaboration
PLM systems support cross-departmental collaboration, breaking down silos and enabling teams to work more effectively together.
By having access to real-time data, teams can make informed decisions swiftly, speeding up the product development process.
BOMs play a critical role in this collaboration, as they provide detailed specifications necessary for different departments, such as production and procurement.
3. Enhanced Change Management
Change is inevitable in product development.
Whether it’s due to new regulations, customer feedback, or technological advancements, products often require adjustments.
PLM systems streamline change management by providing a controlled environment where changes are documented, evaluated, and approved efficiently.
Automatic updates to the BOM within the PLM system ensure consistent implementation of changes across the board.
4. Cost and Time Savings
Streamlined processes and accurate data management lead to significant cost reductions and time savings.
PLM systems automate many tasks, reducing manual errors and labor costs.
By optimizing the BOM management within a PLM framework, businesses can avoid unnecessary expenses related to product redesigns or defective production batches.
Navigating Challenges in BOM and PLM Integration
While the benefits of integrating BOM and PLM are significant, there are challenges that organizations may face:
Data Quality and Integrity
For effective integration, ensuring data quality and integrity is crucial.
Organizations must regularly audit their data for accuracy and completeness.
Training and Adoption
Implementing new systems requires change management and training initiatives to ensure users are comfortable and competent with the new tools.
Investing in comprehensive training programs can facilitate smoother transitions and higher adoption rates.
Conclusion
In conclusion, understanding and effectively integrating BOM and PLM are foundational to achieving digital transformation success in manufacturing.
By centralizing data, fostering collaboration, and enhancing change management, businesses can realize significant cost savings and improved efficiency.
While challenges exist, strategic planning and investment in technology and training can overcome these hurdles.
Ultimately, the synergy of BOM and PLM propels organizations towards innovation and competitive advantage in an increasingly digital landscape.
資料ダウンロード
QCD調達購買管理クラウド「newji」は、調達購買部門で必要なQCD管理全てを備えた、現場特化型兼クラウド型の今世紀最高の購買管理システムとなります。
ユーザー登録
調達購買業務の効率化だけでなく、システムを導入することで、コスト削減や製品・資材のステータス可視化のほか、属人化していた購買情報の共有化による内部不正防止や統制にも役立ちます。
NEWJI DX
製造業に特化したデジタルトランスフォーメーション(DX)の実現を目指す請負開発型のコンサルティングサービスです。AI、iPaaS、および先端の技術を駆使して、製造プロセスの効率化、業務効率化、チームワーク強化、コスト削減、品質向上を実現します。このサービスは、製造業の課題を深く理解し、それに対する最適なデジタルソリューションを提供することで、企業が持続的な成長とイノベーションを達成できるようサポートします。
オンライン講座
製造業、主に購買・調達部門にお勤めの方々に向けた情報を配信しております。
新任の方やベテランの方、管理職を対象とした幅広いコンテンツをご用意しております。
お問い合わせ
コストダウンが利益に直結する術だと理解していても、なかなか前に進めることができない状況。そんな時は、newjiのコストダウン自動化機能で大きく利益貢献しよう!
(Β版非公開)