- お役立ち記事
- BOM/PLM basics and construction project points
月間76,176名の
製造業ご担当者様が閲覧しています*
*2025年3月31日現在のGoogle Analyticsのデータより
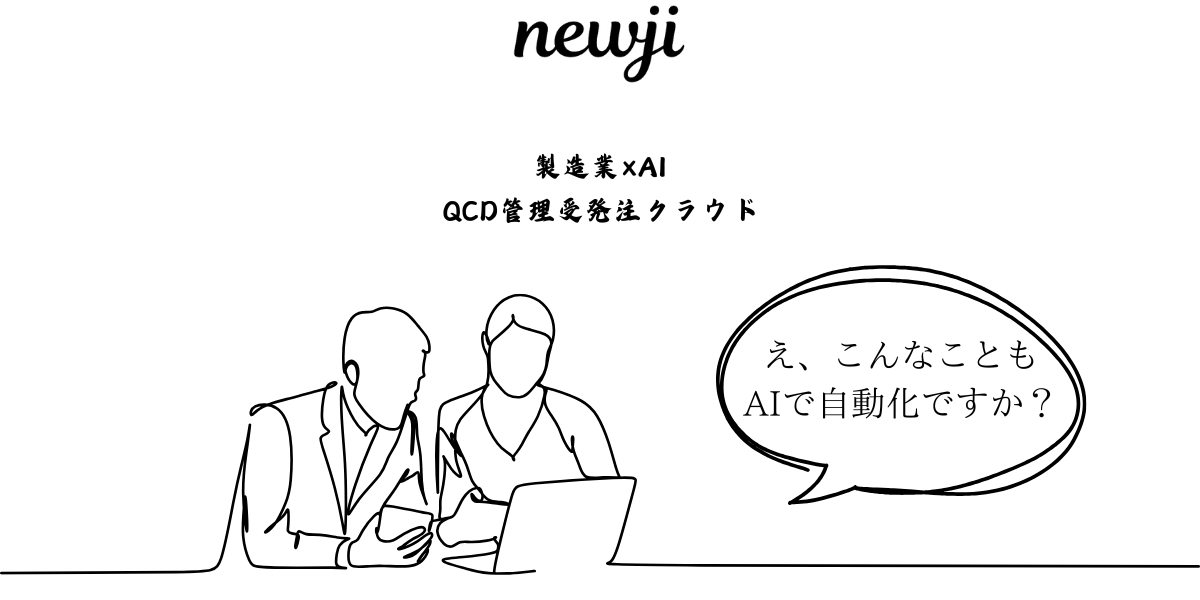
BOM/PLM basics and construction project points
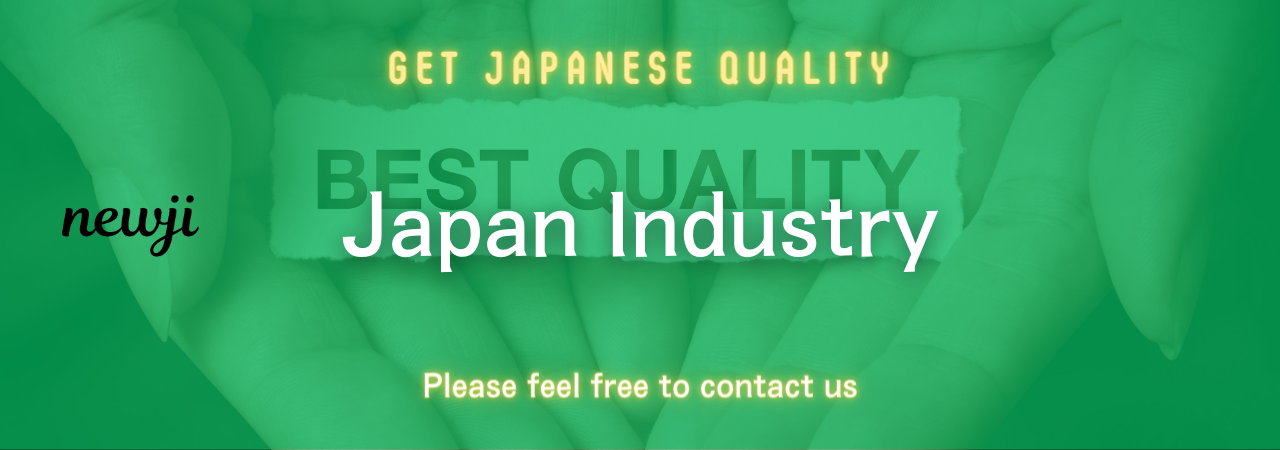
目次
Understanding BOM and PLM: The Basics
When it comes to managing manufacturing and product development processes, there are two key terms you might often hear: BOM and PLM.
These terms stand for Bill of Materials and Product Lifecycle Management, respectively.
Understanding these concepts is crucial for efficient product management and successful project execution.
Let’s delve into the basics of what BOM and PLM entail and how you can implement them effectively in construction projects.
What is a Bill of Materials (BOM)?
A Bill of Materials, or BOM, is a comprehensive list of raw materials, parts, and components needed to construct, manufacture, or repair a product or service.
In simple terms, it’s like a recipe in cooking.
A BOM includes detailed information such as part numbers, part names, descriptions, quantities, and unit prices.
There are different types of BOMs, such as:
– **Engineering BOM (EBOM):** This is created during the product development phase and showcases the engineering aspect of a product.
– **Manufacturing BOM (MBOM):** This includes all the parts involved in making a product and is used mainly in the production facility.
– **Service BOM:** Used to understand the parts needed for service requirements, ensuring easy maintenance and repairs.
A well-constructed BOM is crucial for efficient inventory management, cost estimation, and production scheduling.
What is Product Lifecycle Management (PLM)?
Product Lifecycle Management, or PLM, is a strategic approach to managing a product’s lifecycle from inception, through engineering design and manufacturing, to service and disposal.
The PLM process integrates people, processes, business systems, and information to manage the product data throughout its lifecycle.
The stages of PLM include:
1. **Conception:** Initial idea generation and assessment.
2. **Design:** Engineering and detailing the product parts and components.
3. **Manufacture:** Producing the designed product while ensuring quality and efficiency.
4. **Service:** Maintaining and providing after-sales support.
5. **Disposal:** Managing the recycling or disposal of the product once it reaches the end of its life.
PLM tools facilitate collaboration across teams, improve productivity, and enhance product quality by providing a centralized data hub.
Linking BOM and PLM
BOM and PLM are interconnected.
An efficient Product Lifecycle Management system often includes a BOM management component.
They both aim to streamline production processes, reduce errors, and facilitate better communication between departments.
PLM systems manage BOMs by providing a framework for version control, ensuring that all teams involved have access to the most updated information.
This reduces costly mistakes associated with using outdated BOMs and enhances collaboration across different stages of the product lifecycle.
Implementing BOM and PLM in Construction Projects
The construction industry can greatly benefit from the principles of BOM and PLM.
Here’s how these systems can help improve construction projects:
Efficient Resource Management
Both BOM and PLM ensure that all necessary components and materials are accounted for before the project begins.
This prevents resource shortages and allows for optimal material utilization, which is critical in construction, where resource wastage can be costly.
Enhanced Project Planning
Construction projects are complex and require meticulous planning.
Using a BOM can help construction managers estimate costs, schedule deliveries, and manage inventories efficiently.
Coupled with PLM, which allows for tracking the lifecycle of materials and components, managers can anticipate challenges and address them proactively.
Improved Collaboration and Communication
A centralized PLM system ensures that all stakeholders have access to the same set of up-to-date information regarding the project.
This improves communication among architects, engineers, contractors, and suppliers, facilitating smoother project execution.
Quality Assurance
With a well-defined BOM and PLM framework, construction projects can ensure that all components meet quality and regulatory standards.
This is vital for ensuring that the final construction is safe, reliable, and built to last.
Key Points to Consider for Successful BOM/PLM Deployment
To effectively use BOM and PLM in construction projects, several points must be considered:
Customization
Every construction project is unique, and so should be your BOM and PLM systems.
Customize these tools to fit the specific needs and workflows of your project to maximize their effectiveness.
Integration
Ensure that your BOM and PLM systems can seamlessly integrate with other software and tools used in your project.
This integration ensures data consistency and enhances the overall operational efficiency.
Training and Support
Provide adequate training to your team to familiarize them with BOM and PLM systems.
Regularly update training programs to accommodate any system upgrades or changes.
Feedback and Continuous Improvement
Encourage feedback from your team to identify shortcomings and areas of improvement.
Continually refine your BOM and PLM processes based on this feedback to achieve better results in your future projects.
Conclusion
Understanding and implementing BOM and PLM in construction projects can streamline processes, enhance collaboration, and ultimately, lead to successful project outcomes.
By focusing on efficient resource management, thorough project planning, and quality assurance, these tools become indispensable in the realm of modern construction project management.
Keep in mind the necessary customization, seamless integration, and ongoing improvements to unlock the full potential of BOM and PLM systems.
資料ダウンロード
QCD管理受発注クラウド「newji」は、受発注部門で必要なQCD管理全てを備えた、現場特化型兼クラウド型の今世紀最高の受発注管理システムとなります。
ユーザー登録
受発注業務の効率化だけでなく、システムを導入することで、コスト削減や製品・資材のステータス可視化のほか、属人化していた受発注情報の共有化による内部不正防止や統制にも役立ちます。
NEWJI DX
製造業に特化したデジタルトランスフォーメーション(DX)の実現を目指す請負開発型のコンサルティングサービスです。AI、iPaaS、および先端の技術を駆使して、製造プロセスの効率化、業務効率化、チームワーク強化、コスト削減、品質向上を実現します。このサービスは、製造業の課題を深く理解し、それに対する最適なデジタルソリューションを提供することで、企業が持続的な成長とイノベーションを達成できるようサポートします。
製造業ニュース解説
製造業、主に購買・調達部門にお勤めの方々に向けた情報を配信しております。
新任の方やベテランの方、管理職を対象とした幅広いコンテンツをご用意しております。
お問い合わせ
コストダウンが利益に直結する術だと理解していても、なかなか前に進めることができない状況。そんな時は、newjiのコストダウン自動化機能で大きく利益貢献しよう!
(β版非公開)