- お役立ち記事
- Boost Operational Efficiency with 5S Activities for Manufacturing Line Managers
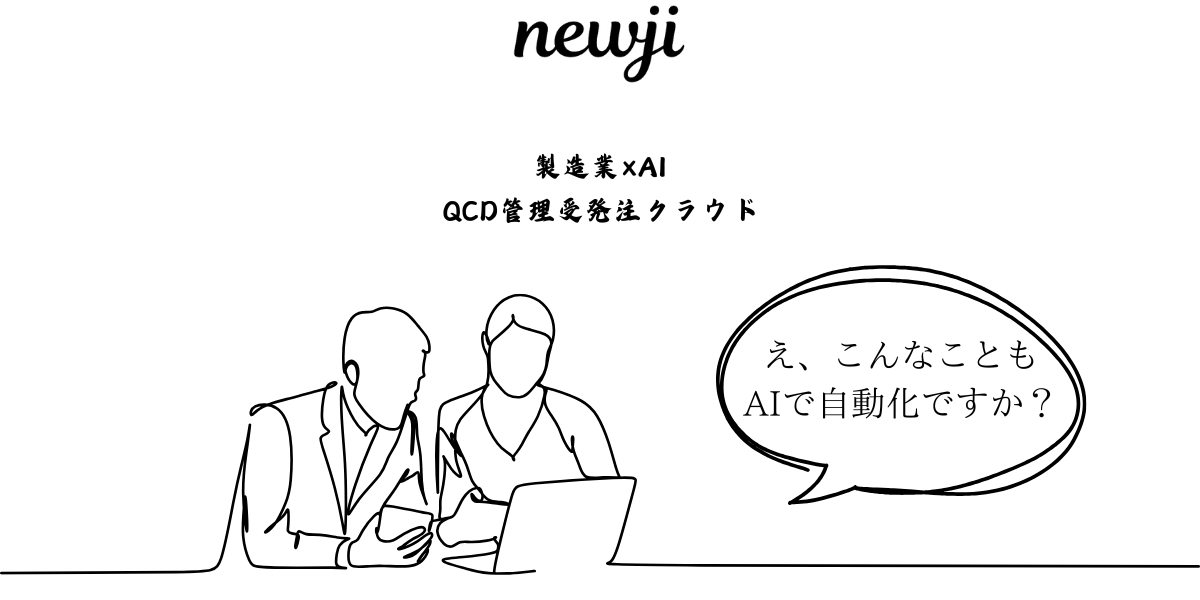
Boost Operational Efficiency with 5S Activities for Manufacturing Line Managers
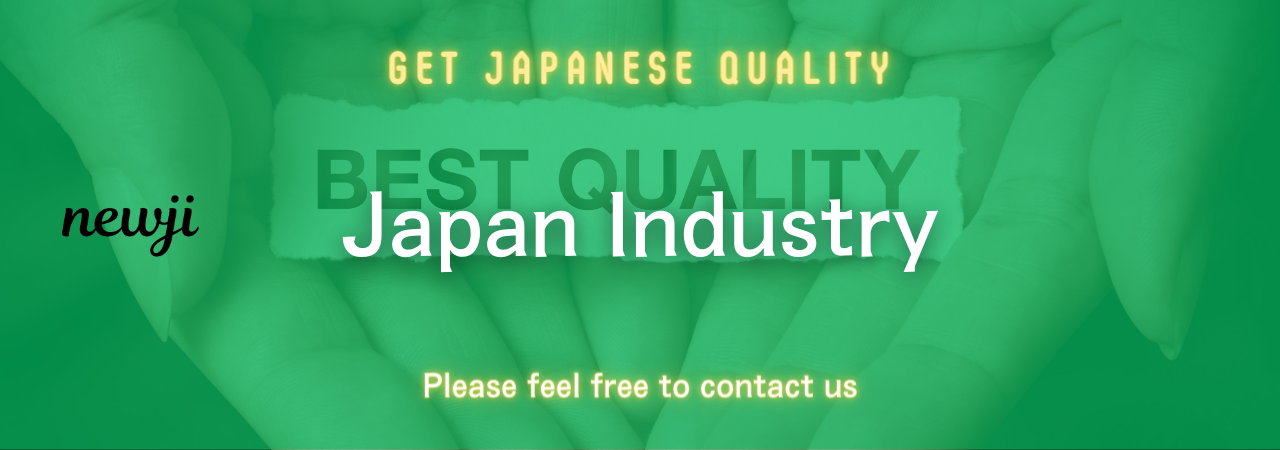
目次
Understanding the 5S System
The 5S system is a simple yet powerful tool that originates from Japan.
It was developed as part of the Toyota Production System, which aims to enhance operational efficiency and eliminate waste.
The 5S system stands for Sort, Set in order, Shine, Standardize, and Sustain.
By implementing these five methods, manufacturing line managers can foster a more organized, productive, and safer work environment.
Sort: Eliminate the Unnecessary
The first step, Sort, involves going through all items in the workplace and removing anything that is not needed for current operations.
This could mean disposing of old tools, obsolete equipment, or unnecessary documents.
The benefit of sorting is that it frees up space and reduces clutter, making it easier for workers to find exactly what they need when they need it.
Additionally, it prevents the accumulation of unnecessary items that could potentially hinder work processes.
Set in Order: Organize Efficiently
Once all unnecessary items have been removed, the next step is to arrange and organize what remains to maximize efficiency.
Everything should have a designated place.
Tools and equipment should be clearly labeled and stored where they are easily accessible.
This reduces time spent searching for things and ensures that when a tool is needed, it is quickly within reach.
A workplace with a proper “set in order” plan allows for smoother workflow and prevents downtime caused by misplaced items.
Shine: Keep Everything Clean
Shine is all about keeping the workplace clean and tidy.
Regular cleaning is essential, not only for maintaining equipment but also for identifying potential issues such as leaks or wear and tear before they become problems.
A clean environment promotes pride and ownership among employees, leading to higher morale and better performance.
It also reduces the risk of accidents and the deterioration of equipment, contributing to a safer and smoother-running manufacturing line.
Standardize: Create Uniform Processes
Standardizing involves developing uniform procedures and best practices for everyone to follow.
This step ensures that each task is performed in the most efficient way possible, every time.
Standardization can include creating schedules for cleaning and maintenance or establishing guidelines for organizing tools.
By doing this, variability in processes is minimized, leading to consistent quality and output.
Training should be provided to ensure everyone understands and adheres to these standards.
Sustain: Maintain and Improve
The final step, Sustain, is about developing habits that promote long-term commitment to the 5S processes.
It involves regular audits and inspections to ensure that the standards are being maintained.
Creating a culture that values continuous improvement is essential.
Employees should be encouraged to suggest improvements and be rewarded for identifying process enhancements.
Sustaining the 5S system requires management commitment and clear communication to ensure its success.
Benefits of Implementing 5S in Manufacturing
By embracing the 5S methodology, manufacturing line managers stand to gain multiple benefits.
Firstly, it significantly enhances the organization within the workplace.
An organized environment boosts productivity as it minimizes the time spent on non-value-adding activities.
Safety is another critical aspect greatly improved by 5S.
A clean and well-organized workplace is less prone to accidents, which protects workers and reduces downtime due to injuries.
Moreover, regular maintenance and cleaning help in identifying potential hazards before they escalate.
5S also leads to cost savings.
By eliminating unnecessary items and inefficiencies, resources are better utilized, and unnecessary expenditures are curtailed.
Lastly, implementing 5S enhances employee engagement and morale.
Employees who work in a clean, organized, and safe environment are generally more satisfied and motivated.
This leads to higher retention rates and a more dedicated workforce.
Getting Started with 5S Implementation
To successfully implement 5S, manufacturing line managers should start by gaining buy-in from top management and the employees who will be involved in the process.
Communicating the benefits clearly and demonstrating how 5S can positively impact the company and individual roles is key.
A designated project team should be assembled to lead the initiative, ideally involving individuals from various levels across the company.
This team will be responsible for coordinating efforts, providing training, and monitoring progress.
Conducting a pilot program in a small area of the facility can serve as a practical way to test the 5S processes and make necessary adjustments before a company-wide roll-out.
This allows managers to address potential challenges and set a precedent for how the system should operate.
Training is a vital component of successful 5S implementation.
All employees should understand the principles of 5S and their roles in maintaining it.
Continuous feedback and refresher training sessions will help maintain momentum and prevent complacency over time.
Overcoming Challenges in 5S Activities
Some challenges may arise during the 5S implementation process, but they can be addressed with the right approach.
One common challenge is resistance to change.
Some employees might be reluctant or skeptical about new processes.
Open communication and involving them in decision-making can minimize resistance.
Another challenge is sustaining the changes over the long term.
Regular audits and reviews ensure that processes are followed and help maintain focus on continuous improvement.
Incentives and recognitions for those who excel in the implementation can encourage others to align with the 5S principles.
Lastly, lack of time can also be an obstacle as employees might feel they are too busy to engage with 5S activities.
Line managers need to prioritize these activities and make them a part of everyday operations, rather than viewing them as additional tasks.
Employing the 5S system can transform manufacturing operations, making them more efficient, safe, and productive.
Line managers who fully embrace and commit to these activities will find themselves leading a more streamlined and effective manufacturing line, ultimately resulting in improved performance and increased satisfaction for all stakeholders.
資料ダウンロード
QCD調達購買管理クラウド「newji」は、調達購買部門で必要なQCD管理全てを備えた、現場特化型兼クラウド型の今世紀最高の購買管理システムとなります。
ユーザー登録
調達購買業務の効率化だけでなく、システムを導入することで、コスト削減や製品・資材のステータス可視化のほか、属人化していた購買情報の共有化による内部不正防止や統制にも役立ちます。
NEWJI DX
製造業に特化したデジタルトランスフォーメーション(DX)の実現を目指す請負開発型のコンサルティングサービスです。AI、iPaaS、および先端の技術を駆使して、製造プロセスの効率化、業務効率化、チームワーク強化、コスト削減、品質向上を実現します。このサービスは、製造業の課題を深く理解し、それに対する最適なデジタルソリューションを提供することで、企業が持続的な成長とイノベーションを達成できるようサポートします。
オンライン講座
製造業、主に購買・調達部門にお勤めの方々に向けた情報を配信しております。
新任の方やベテランの方、管理職を対象とした幅広いコンテンツをご用意しております。
お問い合わせ
コストダウンが利益に直結する術だと理解していても、なかなか前に進めることができない状況。そんな時は、newjiのコストダウン自動化機能で大きく利益貢献しよう!
(Β版非公開)