- お役立ち記事
- Boosting Japanese Manufacturing Excellence: The Power of “スキル開発” (Skill Development)
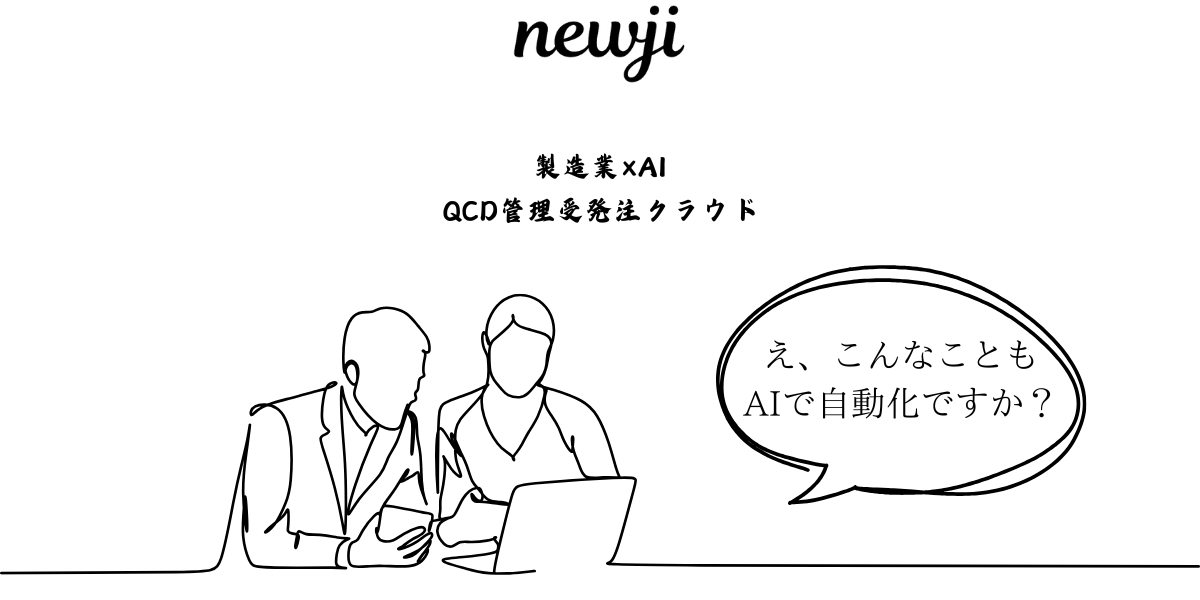
Boosting Japanese Manufacturing Excellence: The Power of “スキル開発” (Skill Development)
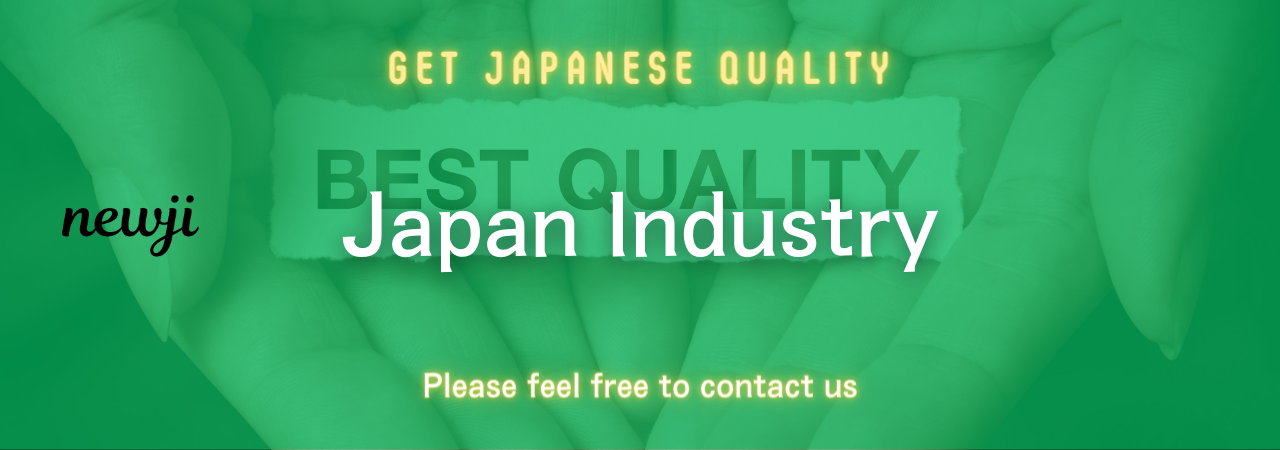
目次
Introduction to Skill Development in Japanese Manufacturing
Japanese manufacturing has long been synonymous with quality, efficiency, and innovation. A significant factor contributing to this reputation is the emphasis on “スキル開発” (skill development). Skill development in the Japanese manufacturing sector focuses on continuous improvement, employee training, and the cultivation of a highly skilled workforce. This article explores the power of skill development in boosting Japanese manufacturing excellence, particularly from the perspective of international procurement and purchasing professionals.
The Importance of Skill Development in Manufacturing
Skill development is crucial in maintaining and enhancing the competitiveness of manufacturing companies. It involves training employees to acquire new skills, improve existing ones, and adapt to technological advancements. In the context of Japanese manufacturing, skill development is deeply ingrained in the corporate culture and plays a pivotal role in sustaining operational excellence.
Advantages of Skill Development
1. **Enhanced Productivity**: Skilled workers can perform tasks more efficiently, reducing production time and costs.
2. **Improved Quality**: Proper training ensures that products meet high-quality standards, which is essential for maintaining customer trust.
3. **Innovation and Adaptability**: A well-trained workforce can adapt to new technologies and processes, fostering innovation.
4. **Employee Satisfaction and Retention**: Investing in employees’ growth leads to higher job satisfaction and lower turnover rates.
Disadvantages of Skill Development
1. **High Initial Investment**: Training programs require significant financial and time resources.
2. **Time-Consuming**: Developing skills takes time, which may delay immediate production needs.
3. **Risk of Attrition**: Trained employees may leave for better opportunities, leading to a loss of investment.
4. **Implementation Challenges**: Ensuring the effectiveness of training programs can be difficult, especially in large organizations.
Skill Development Strategies in Japanese Manufacturing
Japanese companies employ various strategies to ensure effective skill development. These strategies are tailored to meet the unique demands of the manufacturing sector and to align with the company’s long-term goals.
On-the-Job Training
On-the-job training is a cornerstone of skill development in Japanese manufacturing. Employees learn by performing their duties under the supervision of more experienced workers. This hands-on approach ensures that skills are directly applicable to the production process.
Continuous Improvement (Kaizen)
Kaizen, or continuous improvement, is a philosophy that encourages all employees to contribute to the improvement of processes and products. This approach fosters a culture of ongoing skill development and operational excellence.
Formal Education and Certification
Many Japanese manufacturers invest in formal education and certification programs. These programs provide employees with advanced knowledge and specialized skills necessary for complex manufacturing tasks.
Cross-Training and Job Rotation
Cross-training and job rotation involve moving employees between different roles and departments. This practice broadens their skill sets, enhances their understanding of the entire manufacturing process, and increases workforce flexibility.
Implementing Skill Development in International Procurement
For professionals in international procurement and purchasing, understanding and leveraging skill development in Japanese suppliers can lead to significant benefits. Effective implementation requires a strategic approach tailored to the specific needs of the procurement process.
Assessing Supplier Capabilities
Before engaging with Japanese suppliers, it is essential to assess their skill development programs. Evaluating their training strategies and employee capabilities ensures that they can meet your quality and delivery requirements.
Collaborative Training Programs
Collaborating with suppliers on training programs can enhance mutual understanding and improve communication. Joint training initiatives can align procurement practices with the supplier’s operational processes, leading to more efficient collaborations.
Performance Monitoring and Feedback
Regularly monitoring supplier performance and providing constructive feedback can drive continuous improvement. This practice ensures that suppliers maintain high standards and continue to develop their skills in line with your company’s expectations.
Negotiation Techniques with Japanese Suppliers
Negotiating with Japanese suppliers requires a nuanced approach that respects cultural norms and leverages the strengths of skill development. Effective negotiation techniques can lead to more favorable terms and stronger supplier relationships.
Building Trust and Relationships
In Japanese business culture, building trust and long-term relationships is paramount. Investing time in relationship-building activities, such as regular meetings and site visits, can foster mutual respect and understanding.
Understanding Cultural Nuances
Being aware of cultural differences, such as communication styles and decision-making processes, can enhance negotiation outcomes. Demonstrating respect for Japanese customs and practices can facilitate smoother negotiations.
Emphasizing Quality and Long-Term Partnership
Focusing on quality and the potential for long-term partnerships rather than short-term gains aligns with Japanese values. Highlighting the mutual benefits of collaboration can lead to more productive negotiations.
Market Conditions and Their Impact on Skill Development
Understanding market conditions is essential for effective skill development and procurement strategies. Various external factors can influence the demand for skills and the strategies employed by manufacturers.
Technological Advancements
Rapid technological advancements require continuous skill development to keep pace with new manufacturing processes and tools. Companies must invest in training to ensure their workforce remains competent and adaptable.
Globalization and Competition
Global competition drives the need for higher efficiency and innovation. Skill development helps manufacturers stay competitive by improving productivity and fostering innovative solutions.
Economic Trends
Economic fluctuations can impact the availability of resources for training. During economic downturns, companies may prioritize cost-cutting over skill development, while economic booms can provide opportunities for investment in employee training.
Best Practices for Skill Development in Procurement
Implementing best practices in skill development can enhance procurement efficiency and effectiveness. These practices ensure that the procurement team is well-equipped to manage supplier relationships and optimize purchasing strategies.
Continuous Learning and Development
Encouraging continuous learning through workshops, seminars, and online courses keeps the procurement team updated on the latest industry trends and best practices.
Leveraging Technology
Utilizing procurement software and tools can streamline processes, improve data analysis, and support decision-making. Training the team to effectively use these technologies enhances overall procurement performance.
Strategic Supplier Partnerships
Developing strategic partnerships with key suppliers ensures alignment of goals and facilitates collaborative skill development initiatives. These partnerships can lead to improved supplier performance and more reliable supply chains.
Data-Driven Decision Making
Implementing data-driven decision-making processes helps the procurement team make informed choices based on accurate and timely information. Training in data analysis and interpretation is essential for this approach.
Challenges and Solutions in Skill Development
Despite its advantages, skill development in procurement and manufacturing comes with challenges. Identifying these challenges and implementing effective solutions is crucial for successful skill development initiatives.
Resistance to Change
Employees and suppliers may resist changes to established processes. Addressing this resistance through clear communication, involvement in decision-making, and demonstrating the benefits of skill development can mitigate this challenge.
Balancing Training with Production Needs
Scheduling training without disrupting production requires careful planning. Implementing flexible training schedules and integrating training into regular workflows can help balance these demands.
Measuring Training Effectiveness
Assessing the impact of training programs can be difficult. Establishing clear metrics and regularly evaluating training outcomes ensures that skill development initiatives deliver the desired results.
Adapting to Technological Changes
Rapid technological changes require continuous updates to training programs. Staying abreast of industry advancements and proactively updating training content can help address this challenge.
Case Studies: Successful Skill Development Initiatives
Examining successful case studies can provide valuable insights into effective skill development practices. These examples highlight the strategies and outcomes of companies that have excelled in this area.
Toyota’s Lean Manufacturing
Toyota’s implementation of lean manufacturing principles emphasizes continuous improvement and employee involvement. Through comprehensive training programs, Toyota has developed a workforce capable of identifying and eliminating waste, enhancing overall efficiency.
Fanuc’s Automation Expertise
Fanuc, a leading automation company, invests heavily in skill development to maintain its position in the global market. Their training programs focus on advanced robotics and software, ensuring that employees remain at the forefront of technological advancements.
Panasonic’s Quality Control
Panasonic’s commitment to quality control is supported by extensive skill development initiatives. Employees receive training in quality management systems and problem-solving techniques, resulting in consistently high product standards.
The Future of Skill Development in Japanese Manufacturing
As the manufacturing landscape evolves, skill development will continue to play a critical role in sustaining Japanese manufacturing excellence. Emerging trends and future directions highlight the ongoing importance of developing a skilled workforce.
Embracing Digital Transformation
Digital transformation projects, such as the integration of artificial intelligence and the Internet of Things, require new skill sets. Japanese manufacturers are increasingly focusing on digital skills training to stay competitive in a digitally driven market.
Sustainability and Green Manufacturing
With a growing emphasis on sustainability, skill development initiatives are incorporating training on green manufacturing practices. This includes energy-efficient processes, waste reduction, and sustainable resource management.
Global Talent Acquisition
To address skill shortages and foster innovation, Japanese manufacturers are expanding their talent acquisition strategies globally. This includes attracting skilled professionals from diverse backgrounds and promoting multicultural training programs.
Conclusion
Skill development, or “スキル開発,” is a cornerstone of Japanese manufacturing excellence. By investing in continuous training, fostering a culture of improvement, and strategically aligning procurement practices, Japanese manufacturers maintain their competitive edge in the global market. For international procurement and purchasing professionals, understanding and leveraging these skill development strategies can enhance supplier relationships, optimize purchasing processes, and drive sustained operational success. As the manufacturing landscape continues to evolve, the commitment to skill development will remain essential in achieving and maintaining manufacturing excellence.
資料ダウンロード
QCD調達購買管理クラウド「newji」は、調達購買部門で必要なQCD管理全てを備えた、現場特化型兼クラウド型の今世紀最高の購買管理システムとなります。
ユーザー登録
調達購買業務の効率化だけでなく、システムを導入することで、コスト削減や製品・資材のステータス可視化のほか、属人化していた購買情報の共有化による内部不正防止や統制にも役立ちます。
NEWJI DX
製造業に特化したデジタルトランスフォーメーション(DX)の実現を目指す請負開発型のコンサルティングサービスです。AI、iPaaS、および先端の技術を駆使して、製造プロセスの効率化、業務効率化、チームワーク強化、コスト削減、品質向上を実現します。このサービスは、製造業の課題を深く理解し、それに対する最適なデジタルソリューションを提供することで、企業が持続的な成長とイノベーションを達成できるようサポートします。
オンライン講座
製造業、主に購買・調達部門にお勤めの方々に向けた情報を配信しております。
新任の方やベテランの方、管理職を対象とした幅広いコンテンツをご用意しております。
お問い合わせ
コストダウンが利益に直結する術だと理解していても、なかなか前に進めることができない状況。そんな時は、newjiのコストダウン自動化機能で大きく利益貢献しよう!
(Β版非公開)