- お役立ち記事
- Bottleneck Analysis and Improvement Methods in Production Machinery
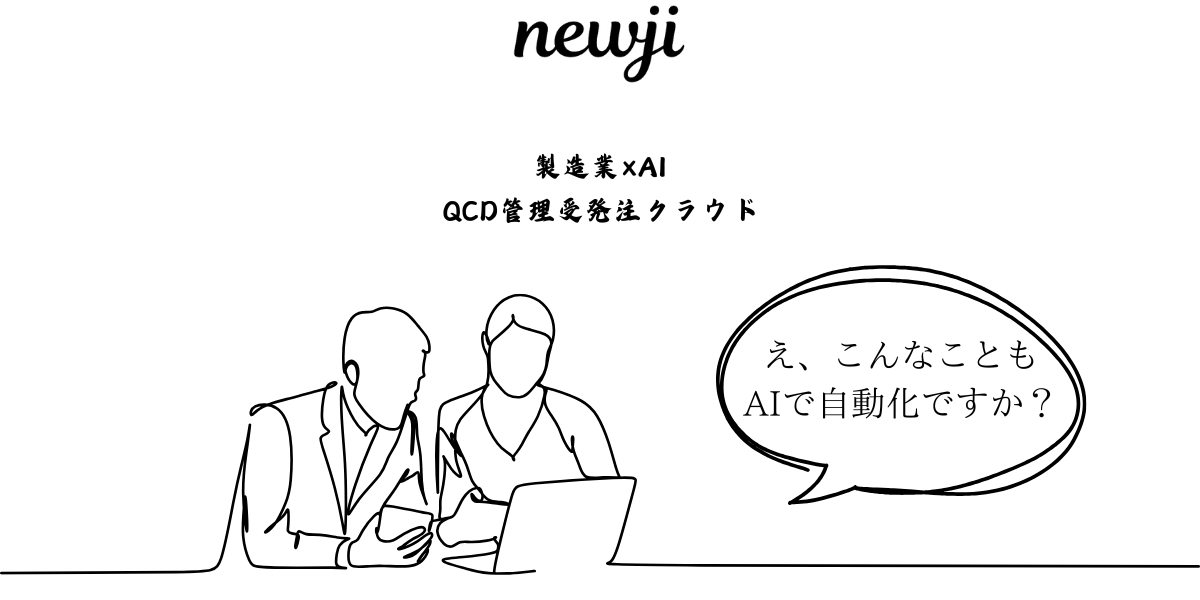
Bottleneck Analysis and Improvement Methods in Production Machinery
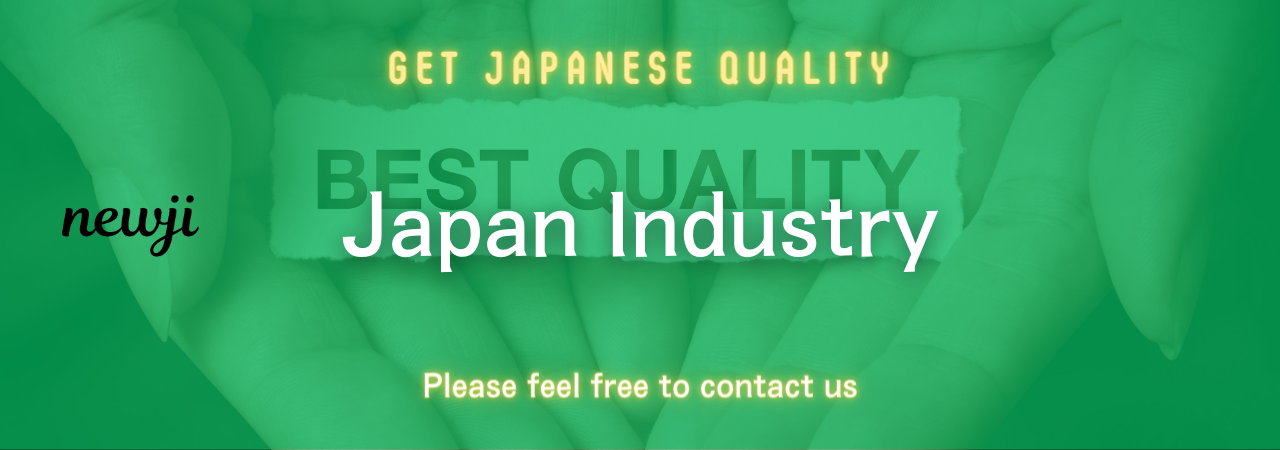
目次
Understanding Bottleneck Analysis in Production Machinery
Bottleneck analysis is a critical aspect of optimizing production machinery and ensuring that every component operates efficiently.
In simple terms, a bottleneck is a point in production where the flow slows down, potentially halting operations.
Identifying and addressing bottlenecks is essential for improving productivity and maintaining a smooth operational flow.
In any production process, time is of the essence.
The faster and more efficiently tasks are completed, the more products can be manufactured in a given timeframe.
Bottleneck analysis helps pinpoint where these slowdowns occur and provides insights into how they can be eliminated or minimized.
The Importance of Bottleneck Analysis
Understanding the importance of bottleneck analysis is vital for companies aiming to enhance their output.
Without it, a company may invest in new technology or increase manpower without resolving the core issue affecting production rates.
Spotting bottlenecks allows businesses to direct resources more effectively to areas that will truly enhance productivity.
Bottleneck analysis not only improves efficiency but also reduces costs.
When a production line is optimized, it cuts down unnecessary expenses, such as overtime wages or machine maintenance costs, caused by unanticipated halts in production.
Moreover, it ensures better quality control.
By focusing efforts on critical points in the production process, the likelihood of errors is reduced.
A well-streamlined production line ensures that each product meets the company’s standards before reaching customers.
How to Identify Bottlenecks
Identifying bottlenecks in production machinery requires a keen eye and the right tools.
Here are some methods that can be employed:
1. Observing the Production Process
Visual observation can be one of the simplest yet effective methods to identify bottlenecks.
Walk through the production floor, watching each stage of the process closely.
Look for any points where work tends to pile up or machines appear idle.
These are usually strong indicators of a bottleneck.
2. Analyzing Production Metrics
Numbers don’t lie.
Scrutinize production data to find stages where throughput dips compared to other stages.
Key performance indicators (KPIs) such as cycle time, downtime, and work-in-process levels can offer insights.
Graphs and charts can visually represent these metrics, making it easier to spot inconsistencies.
3. Feedback from Workers
Employees working closely with the machinery often have valuable insights into where problems occur.
Regularly solicit feedback from workers about any delays or issues they notice in the production line.
Their firsthand experience can be instrumental in identifying less obvious bottlenecks.
4. Simulation and Modeling
With modern technology, simulation software can model production processes to identify potential bottlenecks virtually.
These simulations can help visualize production flow and suggest scenarios where slowdowns might occur.
Methods to Improve Bottlenecks
Once bottlenecks are identified, it’s time to work on improvements.
1. Reorganize the Workflow
Streamlining operations can sometimes be as simple as rearranging the workflow.
By tweaking the order of operations or arranging machine layout for better accessibility, efficiency can often be enhanced.
2. Increase Capacity
If a particular machine or stage is constantly overwhelmed, consider increasing its capacity.
This might involve upgrading machinery, adding more equipment, or reallocating human resources to balance workload.
3. Enhance Employee Training
Sometimes bottlenecks are not due to machinery but to human factors.
Providing additional training to employees can help them work more efficiently and utilize machinery to its fullest potential.
4. Implement Preventative Maintenance
Preventative maintenance can ensure that machines continue running smoothly without unexpected breakdowns.
Regular maintenance checks can catch wear and tear before it becomes a bottleneck issue.
5. Use Automation
For repetitive tasks, consider introducing automation to speed up processes.
Automated systems can operate continuously and precisely, reducing delays caused by manual operations.
Continuous Improvement and Monitoring
After implementing solutions to address bottlenecks, continuous monitoring is essential.
Regularly assess production metrics and work processes to ensure that improvements are working as intended.
Be prepared to make adjustments as needed.
Production dynamics can change, and today’s optimization won’t necessarily hold tomorrow.
Keep communication lines open with employees and maintain data records to detect any new bottlenecks early.
Embrace a culture of continuous improvement.
Encourage innovation and experimentation, always looking for new ways to improve production processes.
In conclusion, bottleneck analysis is an ongoing endeavor.
By meticulously evaluating and refining each aspect of production, machinery can operate at peak efficiency.
This not only drives productivity but also enhances product quality and customer satisfaction.
With regular assessment and willingness to adopt new methods, companies can maintain an edge in a competitive market.
資料ダウンロード
QCD調達購買管理クラウド「newji」は、調達購買部門で必要なQCD管理全てを備えた、現場特化型兼クラウド型の今世紀最高の購買管理システムとなります。
ユーザー登録
調達購買業務の効率化だけでなく、システムを導入することで、コスト削減や製品・資材のステータス可視化のほか、属人化していた購買情報の共有化による内部不正防止や統制にも役立ちます。
NEWJI DX
製造業に特化したデジタルトランスフォーメーション(DX)の実現を目指す請負開発型のコンサルティングサービスです。AI、iPaaS、および先端の技術を駆使して、製造プロセスの効率化、業務効率化、チームワーク強化、コスト削減、品質向上を実現します。このサービスは、製造業の課題を深く理解し、それに対する最適なデジタルソリューションを提供することで、企業が持続的な成長とイノベーションを達成できるようサポートします。
オンライン講座
製造業、主に購買・調達部門にお勤めの方々に向けた情報を配信しております。
新任の方やベテランの方、管理職を対象とした幅広いコンテンツをご用意しております。
お問い合わせ
コストダウンが利益に直結する術だと理解していても、なかなか前に進めることができない状況。そんな時は、newjiのコストダウン自動化機能で大きく利益貢献しよう!
(Β版非公開)