- お役立ち記事
- Building and Operating Cyber-Physical Systems in Manufacturing: Case Studies
月間76,176名の
製造業ご担当者様が閲覧しています*
*2025年3月31日現在のGoogle Analyticsのデータより
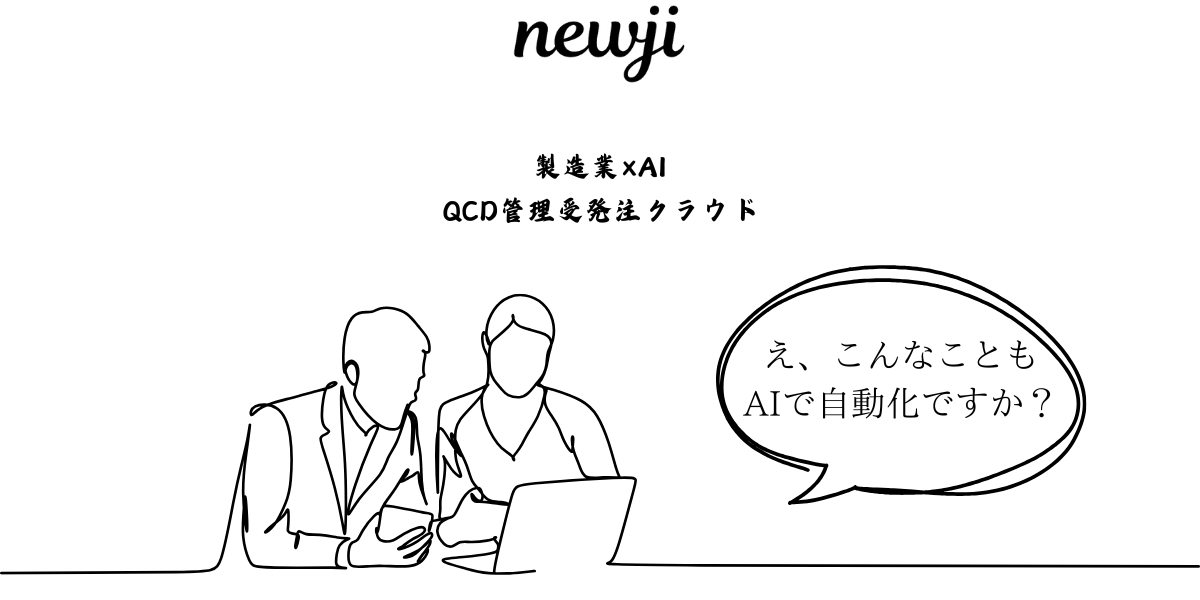
Building and Operating Cyber-Physical Systems in Manufacturing: Case Studies
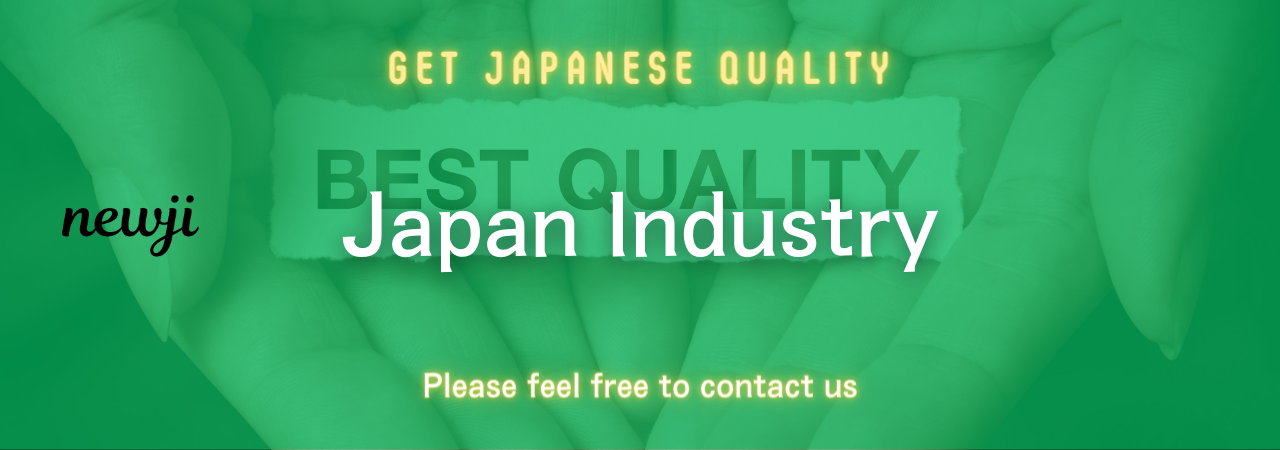
Cyber-Physical Systems (CPS) are revolutionizing the manufacturing sector by merging physical processes with digital data and computational algorithms.
This integration is driving efficiency, precision, and innovation, reshaping how manufacturing operations are conducted.
In this article, we’ll explore the intricacies of building and operating Cyber-Physical Systems in manufacturing through concrete case studies.
目次
Understanding Cyber-Physical Systems in Manufacturing
Cyber-Physical Systems in manufacturing involve embedding sensors, processors, and communication technologies into physical equipment and processes.
This creates a seamless integration between the physical and digital worlds.
By leveraging CPS, manufacturers can achieve real-time monitoring, predictive maintenance, and rapid adaptability to market demands.
Components of Cyber-Physical Systems
There are several key components integral to CPS in manufacturing:
1. **Sensors and Actuators:** These devices collect data from physical processes and perform necessary actions.
2. **Embedded Systems:** Microprocessors and controllers that process sensor data and execute commands to actuators.
3. **Network Connectivity:** Reliable communication networks ensure real-time data transfer and coordination.
4. **Data Analytics:** Advanced algorithms analyze data to generate actionable insights.
5. **Human-Machine Interfaces (HMIs):** Tools that allow human operators to interact with the system and make decisions.
Case Study: Predictive Maintenance
One of the prominent applications of CPS in manufacturing is predictive maintenance.
By continuously monitoring equipment through embedded sensors, manufacturers can predict and prevent failures before they occur.
Implementation
A major automotive company implemented predictive maintenance by integrating CPS into their assembly lines.
Sensors were installed on critical machinery such as robotic arms and conveyor belts.
These sensors continuously monitored parameters like vibration, temperature, and operational speed.
The data collected was transmitted in real-time to an analytics platform.
Benefits
By analyzing the collected data, the company was able to identify patterns indicative of potential failures.
Maintenance could then be scheduled proactively, avoiding unexpected breakdowns and production halts.
This resulted in a significant reduction in downtime, lower maintenance costs, and increased overall equipment efficiency.
Case Study: Quality Control
Ensuring product quality is crucial in manufacturing.
CPS can enhance quality control processes by providing real-time feedback and automating inspection tasks.
Implementation
A leading electronics manufacturer integrated vision systems and robotics, powered by CPS, into their production line.
High-resolution cameras captured images of products at various stages of assembly.
These images were analyzed using artificial intelligence algorithms to detect defects.
Robotic arms, guided by the system, automatically removed defective products from the line.
Benefits
This integration allowed for real-time quality inspection, ensuring that only flawless products moved forward in the production process.
The company saw a drastic improvement in product quality, a reduction in human error, and faster identification and resolution of defects.
Customer satisfaction increased due to the consistent delivery of high-quality products.
Case Study: Supply Chain Optimization
Cyber-Physical Systems can significantly enhance supply chain management by providing real-time tracking and data-driven decision-making.
Implementation
A global consumer goods manufacturer integrated CPS into their supply chain.
GPS and RFID sensors were installed on shipments, allowing for real-time tracking of goods from production to delivery.
Additionally, inventory levels at distribution centers were continuously monitored and optimized using advanced data analytics.
Benefits
The manufacturer gained unprecedented visibility into their supply chain, enabling them to quickly identify and resolve bottlenecks.
Inventory levels were optimized, reducing the risk of overstocking or stockouts.
These improvements resulted in lower logistics costs, faster delivery times, and a more responsive supply chain.
Challenges in Implementing Cyber-Physical Systems
While the benefits of CPS in manufacturing are significant, there are challenges to be addressed:
Data Security
The integration of CPS involves the transmission and processing of vast amounts of data.
Ensuring the security and integrity of this data is crucial to prevent unauthorized access and cyber threats.
Interoperability
Different machines and systems from various manufacturers may need to work together seamlessly.
Achieving interoperability without significant modifications can be challenging.
Cost
The initial investment required for implementing CPS can be substantial.
This includes costs for sensors, embedded systems, network infrastructure, and skilled personnel.
Skill Gap
Building and operating CPS require specialized skills in areas such as data analytics, cybersecurity, and system integration.
Finding and training personnel with the necessary expertise can be challenging.
Future of Cyber-Physical Systems in Manufacturing
The future of CPS in manufacturing is promising, with advancements in technologies like the Internet of Things (IoT), artificial intelligence (AI), and 5G.
Internet of Things (IoT)
IoT enables seamless connectivity between devices, allowing for more efficient data collection and communication.
This will further enhance the capabilities of Cyber-Physical Systems in manufacturing.
Artificial Intelligence (AI)
AI algorithms can analyze massive amounts of data generated by CPS to provide deeper insights and more accurate predictions.
This will drive further automation and optimization in manufacturing processes.
5G Connectivity
The deployment of 5G networks will provide faster and more reliable communication, supporting real-time data transfer and coordination in CPS applications.
CPS is a transformative force in the manufacturing industry, offering numerous benefits in terms of efficiency, quality, and innovation.
However, successfully implementing CPS requires addressing challenges related to data security, interoperability, costs, and skill gaps.
With ongoing technological advancements, the future of Cyber-Physical Systems in manufacturing looks incredibly promising, paving the way for smarter and more resilient manufacturing operations.
資料ダウンロード
QCD管理受発注クラウド「newji」は、受発注部門で必要なQCD管理全てを備えた、現場特化型兼クラウド型の今世紀最高の受発注管理システムとなります。
ユーザー登録
受発注業務の効率化だけでなく、システムを導入することで、コスト削減や製品・資材のステータス可視化のほか、属人化していた受発注情報の共有化による内部不正防止や統制にも役立ちます。
NEWJI DX
製造業に特化したデジタルトランスフォーメーション(DX)の実現を目指す請負開発型のコンサルティングサービスです。AI、iPaaS、および先端の技術を駆使して、製造プロセスの効率化、業務効率化、チームワーク強化、コスト削減、品質向上を実現します。このサービスは、製造業の課題を深く理解し、それに対する最適なデジタルソリューションを提供することで、企業が持続的な成長とイノベーションを達成できるようサポートします。
製造業ニュース解説
製造業、主に購買・調達部門にお勤めの方々に向けた情報を配信しております。
新任の方やベテランの方、管理職を対象とした幅広いコンテンツをご用意しております。
お問い合わせ
コストダウンが利益に直結する術だと理解していても、なかなか前に進めることができない状況。そんな時は、newjiのコストダウン自動化機能で大きく利益貢献しよう!
(β版非公開)