- お役立ち記事
- Building backup suppliers for crisis management Preparations that purchasing departments should make
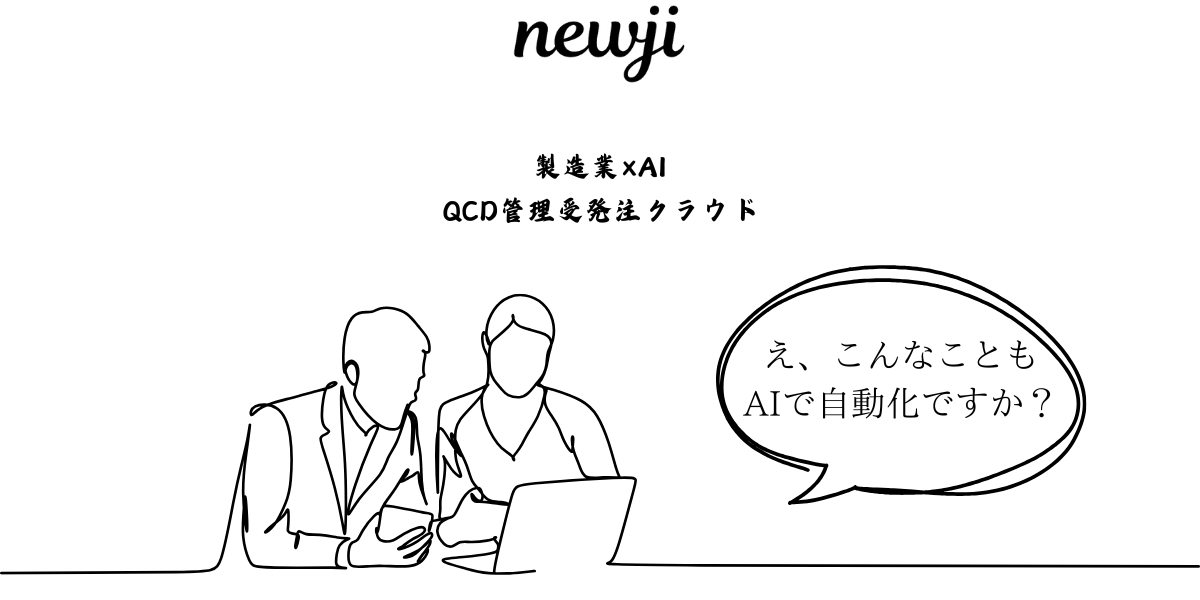
Building backup suppliers for crisis management Preparations that purchasing departments should make
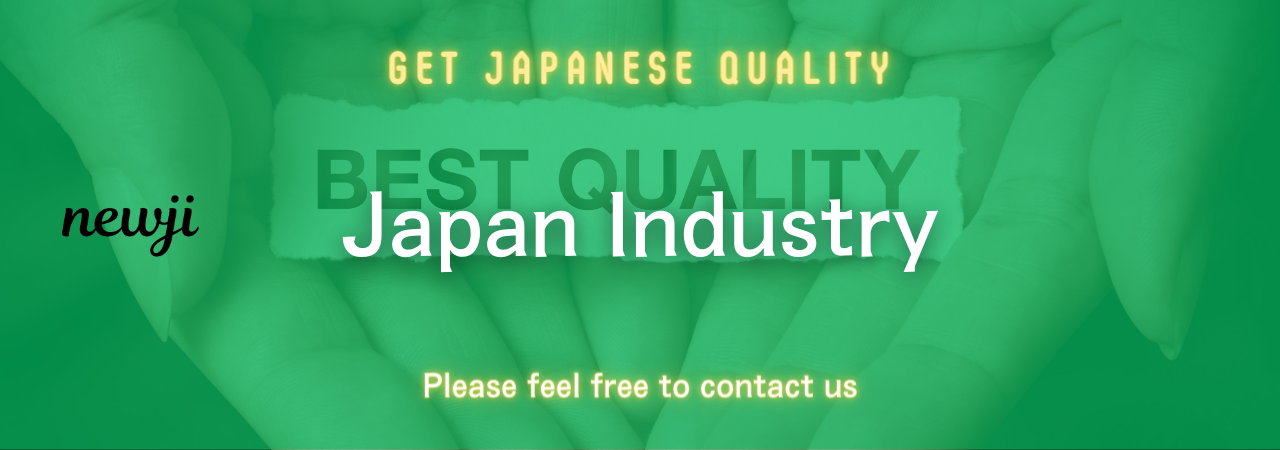
目次
Understanding the Importance of Backup Suppliers
In today’s unpredictable business environment, having a resilient supply chain is crucial for any organization.
One key aspect of building a robust supply chain is establishing relationships with backup suppliers.
Backup suppliers serve as an insurance policy, helping businesses maintain operations when primary suppliers face disruptions.
Whether due to natural disasters, political instability, or economic downturns, disruptions can occur without warning.
Being prepared with alternative suppliers ensures that your business can continue to function smoothly, even in the face of unexpected challenges.
For purchasing departments, this means actively seeking and maintaining relationships with multiple suppliers.
Identifying Potential Backup Suppliers
The first step in building backup suppliers is identifying potential candidates.
Purchasing departments need to research and evaluate suppliers who can meet the company’s quality, cost, and delivery requirements.
Start by looking at your current network of suppliers and assess whether they have the capacity to serve as a backup.
You can also explore new suppliers in different geographical regions.
This diversification is crucial as it reduces the risk of disruptions affecting all your suppliers simultaneously.
Industry trade shows and online supplier directories can serve as excellent resources to discover potential backup suppliers.
Evaluating Supplier Capabilities
Once you’ve identified potential backup suppliers, the next step is to evaluate their capabilities.
This involves assessing their production capacity, delivery capabilities, financial stability, and commitment to quality.
Conduct thorough investigations and, if possible, visit their facilities to verify their operations.
It’s also important to look at their track record.
Have they successfully dealt with crises in the past?
Talking to their existing clients can provide insights into their reliability and performance under pressure.
By choosing suppliers with a proven history of resilience, you increase the chances of seamless transitions during crises.
Negotiating Terms and Agreements
Having identified and evaluated potential backup suppliers, it’s crucial to proceed with negotiating terms and agreements.
Formulating clear contracts that outline roles, responsibilities, and expectations is vital.
Make sure to clearly define pricing arrangements, delivery timelines, and quality specifications.
An effective strategy is to negotiate flexible contractual terms that allow for scaling up or down based on your needs.
This adaptability can prove essential during crises when demand tends to fluctuate.
Also, consider including clauses that address crisis scenarios, ensuring suppliers prioritize your orders if a disruption occurs.
Building Strong Supplier Relationships
Beyond contracts, building strong relationships with backup suppliers is key.
Maintain regular communication to stay updated on their operations and any changes that might affect you.
Establishing trust ensures that they are more likely to prioritize your needs during times of crisis.
Invest in long-term partnerships by offering fair terms and treating them as integral parts of your supply chain.
This relational approach can lead to better collaboration, innovation, and problem-solving when unexpected challenges arise.
Monitoring and Reviewing Supplier Performance
Having a backup plan doesn’t end with supply contracts.
Continuous monitoring and review of supplier performance are crucial to ensuring preparedness.
Regularly assess their capabilities and analyze key performance indicators, such as delivery accuracy, quality control, and response times.
Establish a feedback loop for performance reviews with backup suppliers.
This allows for addressing areas of improvement and encourages suppliers to consistently meet your standards.
Staying vigilant with performance evaluations helps maintain readiness for unpredictable disruptions.
Implementing a Supplier Risk Management Plan
Building backup suppliers is an integral part of a wider supplier risk management plan.
Purchasing departments should also create risk assessment frameworks that identify and mitigate potential issues across the supply chain.
Scenarios might include political unrest, climate events, or market volatility affecting specific regions.
Implement strategies such as stockpiling key materials if viable, or developing multiple shipping routes to mitigate transport disruptions.
By having a comprehensive risk management plan, your teams can act swiftly and effectively when crises arise.
Investing in Technology for Better Coordination
Investing in technology is another significant aspect of crisis management preparedness.
Leveraging supply chain management software can enhance visibility and coordination across the supply chain.
With real-time data, purchasing departments can promptly address potential disruptions and coordinate with backup suppliers effectively.
Automation and data analytics tools aid in anticipating demand, tracking shipments, and managing inventory levels efficiently.
Utilizing such technological solutions eases the burden on procurement teams during crises, enhancing decision-making capabilities.
Training and Preparing Your Team
Beyond supplier relationships, it’s crucial that purchasing department personnel are well-prepared.
Regular training sessions focusing on crisis management and supply chain resilience ensure your team is ready to act swiftly.
Workshops and simulations of crisis scenarios can help teams practice and refine their response strategies.
Encourage open communication and collaboration among team members.
This fosters a culture of proactive readiness, ensuring that everyone knows their responsibilities during emergencies and works diligently to maintain steady operations.
Conclusion: Securing Business Continuity
Building backup suppliers is more than a tactical approach—it’s central to securing business continuity.
By preparing ahead, purchasing departments can protect their organizations against disruptions, ensuring smooth and efficient operations even amidst crises.
Through thoughtful planning, evaluation, and ongoing management, a robust supplier network is achievable.
By prioritizing this aspect of crisis management, companies position themselves to thrive in dynamic and uncertain landscapes.
資料ダウンロード
QCD調達購買管理クラウド「newji」は、調達購買部門で必要なQCD管理全てを備えた、現場特化型兼クラウド型の今世紀最高の購買管理システムとなります。
ユーザー登録
調達購買業務の効率化だけでなく、システムを導入することで、コスト削減や製品・資材のステータス可視化のほか、属人化していた購買情報の共有化による内部不正防止や統制にも役立ちます。
NEWJI DX
製造業に特化したデジタルトランスフォーメーション(DX)の実現を目指す請負開発型のコンサルティングサービスです。AI、iPaaS、および先端の技術を駆使して、製造プロセスの効率化、業務効率化、チームワーク強化、コスト削減、品質向上を実現します。このサービスは、製造業の課題を深く理解し、それに対する最適なデジタルソリューションを提供することで、企業が持続的な成長とイノベーションを達成できるようサポートします。
オンライン講座
製造業、主に購買・調達部門にお勤めの方々に向けた情報を配信しております。
新任の方やベテランの方、管理職を対象とした幅広いコンテンツをご用意しております。
お問い合わせ
コストダウンが利益に直結する術だと理解していても、なかなか前に進めることができない状況。そんな時は、newjiのコストダウン自動化機能で大きく利益貢献しよう!
(Β版非公開)