- お役立ち記事
- Building cooperative relationships to shorten lead times Coordinating purchasing and production
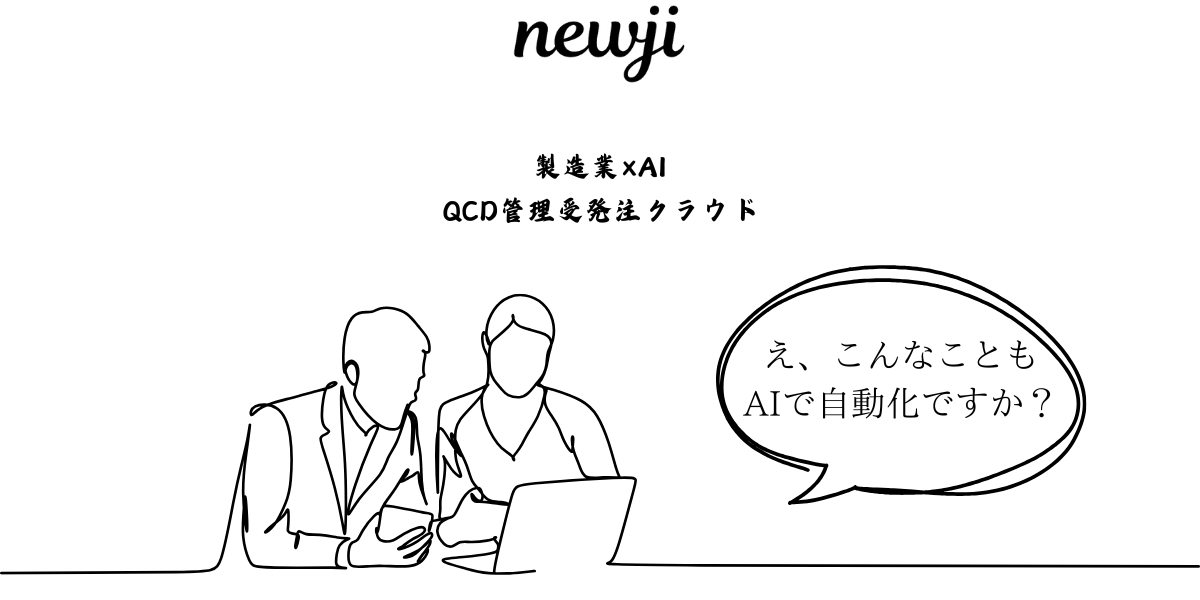
Building cooperative relationships to shorten lead times Coordinating purchasing and production
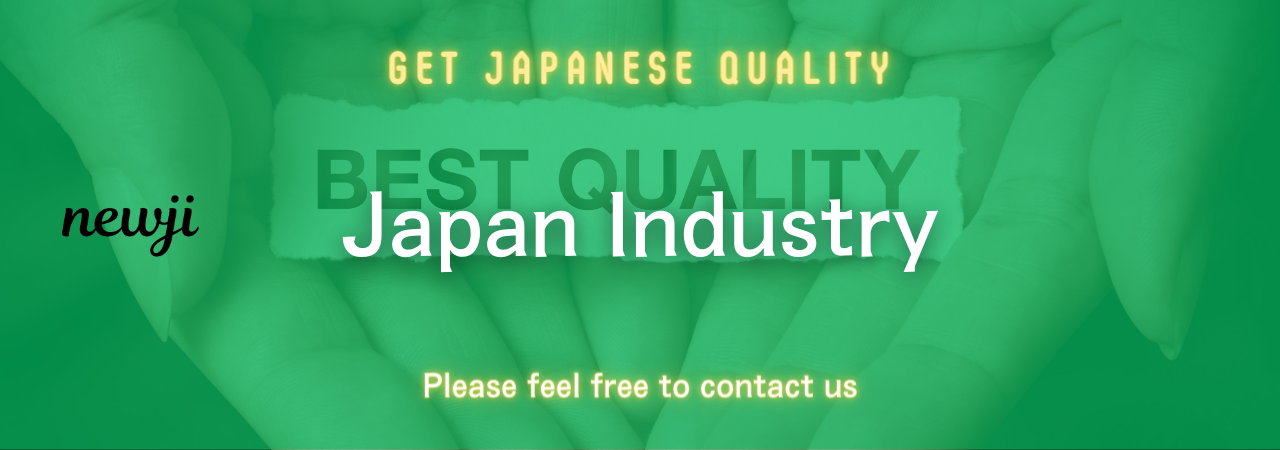
目次
Understanding the Importance of Lead Times
In the dynamic world of manufacturing and production, lead time is a crucial factor that impacts efficiency and customer satisfaction.
Lead time refers to the total time it takes from receiving a customer order to delivering the finished product.
Shortening this time is essential for businesses aiming to stay competitive in the market.
By reducing lead times, companies can respond more swiftly to demand changes, minimize inventory costs, and improve service levels.
To achieve this, building cooperative relationships between purchasing and production is vital.
The Role of Purchasing in Lead Time Reduction
Purchasing is at the forefront of reducing lead times because it deals directly with suppliers – the starting point for most of the production process.
Efficient purchasing processes ensure that raw materials and components arrive on time without delays.
Building strong relationships with suppliers enables buyers to negotiate better terms, secure priority delivery, and manage risks effectively.
Collaborating closely with suppliers can lead to earlier problem identification, thus preventing bottlenecks in the production line.
Furthermore, partnering with reliable suppliers can result in adopting Just-In-Time (JIT) inventory practices, which significantly cut down on storage requirements and reduce waste.
Supplier Segmentation and Selection
Choosing the right suppliers plays a significant role in minimizing lead times.
Segmenting suppliers based on their reliability, delivery speed, and quality can help in forming strategic alliances.
It’s essential to prioritize working with those suppliers who consistently meet deadlines and have a track record of reliability.
Evaluating and renegotiating contracts regularly ensures that any changes in supplier performance are accounted for, leading to better lead time management.
The Importance of Communication
Clear, consistent, and frequent communication between purchasing and suppliers is a cornerstone of reducing lead times.
By sharing forecasts and production schedules, suppliers can better plan their deliveries, avoiding last-minute rushes and errors.
Implementing integrated communication systems can also streamline information flow, ensuring that everyone is on the same page.
Effective communication helps in anticipating potential disruptions, allowing both parties to plan accordingly and keep lead times under control.
The Role of Production in Lead Time Reduction
The production process is where the magic happens, transforming raw materials into finished products.
Coordinating effectively between purchasing and the production department can lead to significant lead time reductions.
Production teams need to be agile and responsive, adapting quickly to changes in demand without compromising quality.
The production schedule should be flexible enough to accommodate any unforeseen delays in the supply chain, ensuring continuous work flow.
Streamlining Production Processes
One way to cut down lead times is by streamlining production processes.
This involves eliminating any unnecessary steps and optimizing workflows for maximum efficiency.
Implementing lean manufacturing principles can help identify and reduce waste, thereby speeding up the entire production cycle.
Regularly reviewing and refining processes ensures the production line is in top shape, contributing to reduced lead times.
Utilizing Technology and Automation
Technological advancements offer tremendous potential in shortening lead times.
Automation plays a crucial role in speeding up production processes by reducing human error and handling repetitive tasks efficiently.
Investing in cutting-edge machinery and technology can enable quicker production while maintaining high quality.
Furthermore, utilizing software solutions for inventory management and production planning provides real-time data that aids in making informed decisions promptly.
Fostering a Collaborative Culture
Building cooperative relationships within a company involves all departments working towards a common goal.
For purchasing and production, collaboration means aligning incentives and breaking down silos that hinder communication.
A cross-functional approach encourages open dialogue and understanding of each department’s challenges and requirements.
Regular meetings and workshops can facilitate greater cohesion and ensure that everyone is committed to reducing lead times.
Performance Metrics and Continuous Improvement
To nurture cooperative relationships, it is essential to establish and track performance metrics.
Key performance indicators (KPIs) relative to lead time should be set and monitored regularly to gauge success and identify areas for improvement.
Implementing a culture of continuous improvement can lead to innovative solutions for reducing lead times.
This means encouraging employees to suggest and test new ideas, fostering an environment where every small gain is valued.
Conclusion
Coordinating purchasing and production is fundamental to shortening lead times within any manufacturing process.
By fostering cooperative relationships with suppliers, streamlining production, and cultivating a collaborative culture, businesses can achieve significant reductions in lead times.
This leads to improved efficiency, cost savings, and greater customer satisfaction, putting companies on a path to long-term success.
資料ダウンロード
QCD調達購買管理クラウド「newji」は、調達購買部門で必要なQCD管理全てを備えた、現場特化型兼クラウド型の今世紀最高の購買管理システムとなります。
ユーザー登録
調達購買業務の効率化だけでなく、システムを導入することで、コスト削減や製品・資材のステータス可視化のほか、属人化していた購買情報の共有化による内部不正防止や統制にも役立ちます。
NEWJI DX
製造業に特化したデジタルトランスフォーメーション(DX)の実現を目指す請負開発型のコンサルティングサービスです。AI、iPaaS、および先端の技術を駆使して、製造プロセスの効率化、業務効率化、チームワーク強化、コスト削減、品質向上を実現します。このサービスは、製造業の課題を深く理解し、それに対する最適なデジタルソリューションを提供することで、企業が持続的な成長とイノベーションを達成できるようサポートします。
オンライン講座
製造業、主に購買・調達部門にお勤めの方々に向けた情報を配信しております。
新任の方やベテランの方、管理職を対象とした幅広いコンテンツをご用意しております。
お問い合わせ
コストダウンが利益に直結する術だと理解していても、なかなか前に進めることができない状況。そんな時は、newjiのコストダウン自動化機能で大きく利益貢献しよう!
(Β版非公開)