- お役立ち記事
- Building Distributed Manufacturing Networks and the Advantages of Local Production
月間76,176名の
製造業ご担当者様が閲覧しています*
*2025年3月31日現在のGoogle Analyticsのデータより
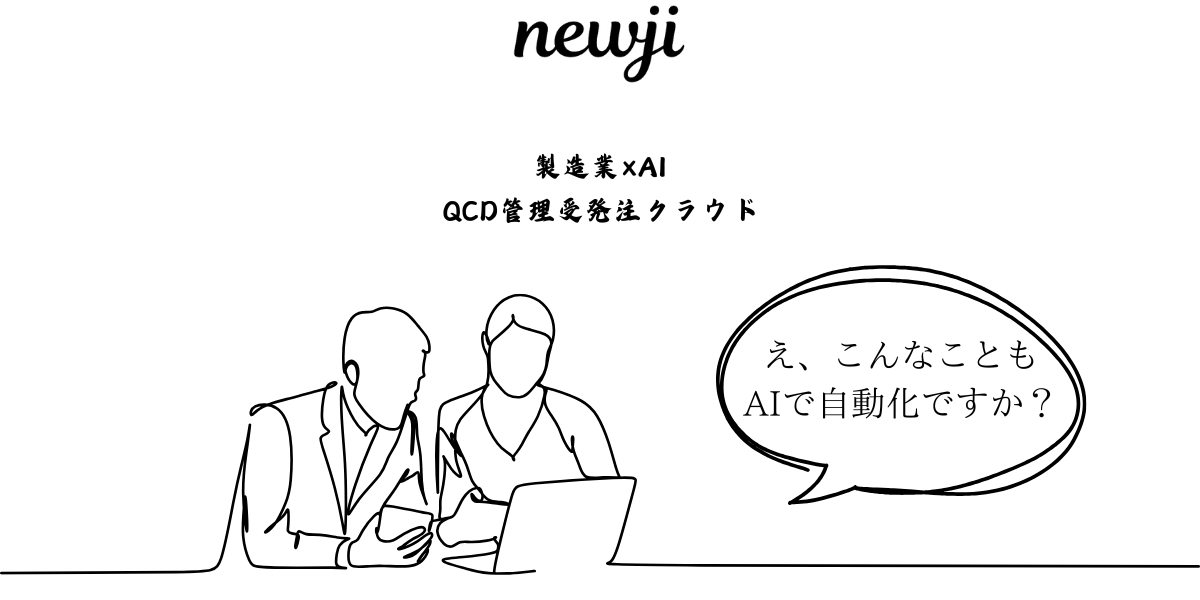
Building Distributed Manufacturing Networks and the Advantages of Local Production
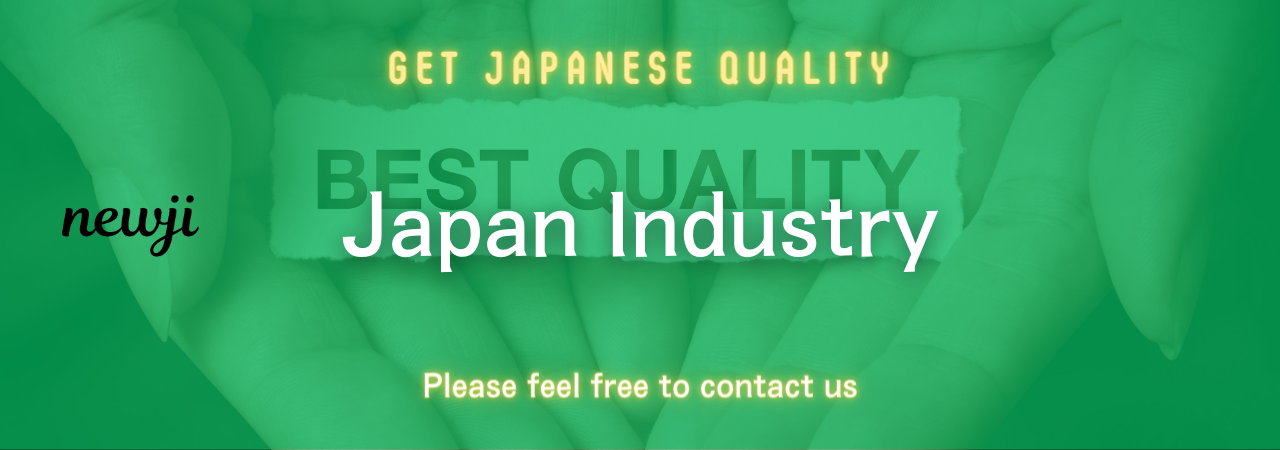
Distributed manufacturing represents a fundamental shift from centralized production models to decentralized, localized production units connected through advanced technology and digital communication networks.
This approach, often leveraging Industry 4.0 technologies such as IoT, big data analytics, and additive manufacturing (3D printing), offers numerous benefits for industries and consumers alike.
目次
Understanding Distributed Manufacturing
Distributed manufacturing, also known as distributed production, involves the use of a network of geographically dispersed facilities to manufacture products.
Each facility operates semi-independently but remains interconnected through a digital communication network.
This innovative method stands in stark contrast to traditional centralized manufacturing, where production happens in a single, often large, facility.
The essence of distributed manufacturing lies in its ability to produce goods closer to the point of consumption.
This practice reduces the need for long-distance transportation, leading to faster delivery times and lower logistics costs.
Additionally, it enhances the sustainability of manufacturing operations by cutting down on carbon emissions associated with shipping goods over long distances.
Key Advantages of Local Production
The advantages of local production within a distributed manufacturing framework are multifaceted.
Here are some of the primary benefits:
1. Cost Efficiency
Local production within a distributed network can significantly reduce costs.
By producing goods closer to the end consumer, businesses can save on transportation and warehousing expenses.
Moreover, local production allows for quicker reactions to market demand, thus reducing excess inventory and associated holding costs.
2. Faster Delivery Times
One of the most noticeable benefits for consumers is the reduction in delivery times.
With production facilities closer to the demand centers, the time taken to transport products is drastically reduced.
This is particularly beneficial for fast-moving consumer goods, where timeliness can be a critical factor in consumer satisfaction.
3. Sustainability and Reduced Carbon Footprint
Local production inherently supports environmental sustainability.
By minimizing the distance products must travel, it lowers greenhouse gas emissions from transportation.
Additionally, localized production can more easily incorporate renewable energy sources and sustainable practices, further reducing the environmental impact.
4. Enhanced Customization and Flexibility
Distributed manufacturing networks enable a higher degree of customization for products.
Local production facilities can quickly adapt to specific local market demands and preferences.
This flexibility allows businesses to offer tailored products without the delays and costs associated with modifying centralized production lines.
5. Increased Resilience and Risk Mitigation
A decentralized manufacturing approach enhances the resilience of the supply chain.
By spreading production across multiple locations, businesses can reduce the risk of disruptions caused by localized issues, such as natural disasters, political instability, or industrial strikes.
This diversification enhances the overall stability and reliability of the supply chain.
6. Support for Local Economies
By establishing production facilities locally, businesses contribute to the economic development of the regions in which they operate.
Local production facilities create jobs, support local suppliers, and stimulate regional economic growth, leading to a mutually beneficial relationship between businesses and the communities they serve.
Technologies Enabling Distributed Manufacturing
Several advanced technologies play a crucial role in enabling the distributed manufacturing model.
1. Internet of Things (IoT)
IoT connects various production facilities, equipment, and systems through the internet, enabling real-time monitoring and management.
This connectivity ensures seamless coordination between different manufacturing units and facilitates efficient resource utilization.
2. Big Data and Analytics
The use of big data and analytics allows businesses to gain insights into production processes, supply chain dynamics, and customer preferences.
By leveraging these insights, companies can optimize their operations, forecast demand accurately, and make informed decisions.
3. Additive Manufacturing (3D Printing)
3D printing technology enables rapid prototyping and flexible production.
It allows for on-demand manufacturing of customized products, reducing the need for large-scale centralized production.
This technology is particularly beneficial for producing complex or bespoke items with minimal lead times.
4. Enterprise Resource Planning (ERP) Systems
ERP systems integrate various business processes, such as production, supply chain management, and inventory control.
These systems provide a unified platform for managing operations across a distributed network, ensuring coherence and efficiency.
5. Advanced Robotics and Automation
Automation and advanced robotics play a pivotal role in modern manufacturing.
These technologies enhance precision, speed, and efficiency in production processes, making it feasible to operate multiple localized facilities with consistent quality standards.
Challenges of Implementing Distributed Manufacturing
While distributed manufacturing offers numerous advantages, it also presents certain challenges.
1. Initial Setup Costs
Establishing a network of local production facilities requires a significant initial investment.
Businesses need to invest in infrastructure, technology, and skilled personnel to ensure successful implementation.
2. Coordination and Management
Effective coordination and management of multiple production units can be complex.
Businesses need robust communication and management systems to ensure synchronization and avoid inefficiencies or disruptions.
3. Quality Control
Maintaining consistent quality across different production facilities can be challenging.
It requires stringent quality control mechanisms and standardized procedures to ensure uniformity in product quality.
Future of Distributed Manufacturing
The future of distributed manufacturing looks promising, driven by advancements in technology and increasing demand for agile, sustainable production methods.
As businesses continue to recognize the benefits of localized production, we can expect a significant shift towards this model across various industries.
Moving forward, the integration of artificial intelligence (AI) and machine learning (ML) will further enhance the capabilities of distributed manufacturing networks.
AI and ML can optimize production processes, predict maintenance needs, and improve decision-making through advanced analytics.
In conclusion, distributed manufacturing and local production offer transformative benefits for businesses, consumers, and the environment.
By leveraging advanced technologies and embracing a more decentralized approach, industries can achieve greater efficiency, sustainability, and resilience, paving the way for a more innovative and sustainable future.
資料ダウンロード
QCD管理受発注クラウド「newji」は、受発注部門で必要なQCD管理全てを備えた、現場特化型兼クラウド型の今世紀最高の受発注管理システムとなります。
ユーザー登録
受発注業務の効率化だけでなく、システムを導入することで、コスト削減や製品・資材のステータス可視化のほか、属人化していた受発注情報の共有化による内部不正防止や統制にも役立ちます。
NEWJI DX
製造業に特化したデジタルトランスフォーメーション(DX)の実現を目指す請負開発型のコンサルティングサービスです。AI、iPaaS、および先端の技術を駆使して、製造プロセスの効率化、業務効率化、チームワーク強化、コスト削減、品質向上を実現します。このサービスは、製造業の課題を深く理解し、それに対する最適なデジタルソリューションを提供することで、企業が持続的な成長とイノベーションを達成できるようサポートします。
製造業ニュース解説
製造業、主に購買・調達部門にお勤めの方々に向けた情報を配信しております。
新任の方やベテランの方、管理職を対象とした幅広いコンテンツをご用意しております。
お問い合わせ
コストダウンが利益に直結する術だと理解していても、なかなか前に進めることができない状況。そんな時は、newjiのコストダウン自動化機能で大きく利益貢献しよう!
(β版非公開)