- お役立ち記事
- Burr Prevention Techniques and Methods for Improving Molding Processes
Burr Prevention Techniques and Methods for Improving Molding Processes
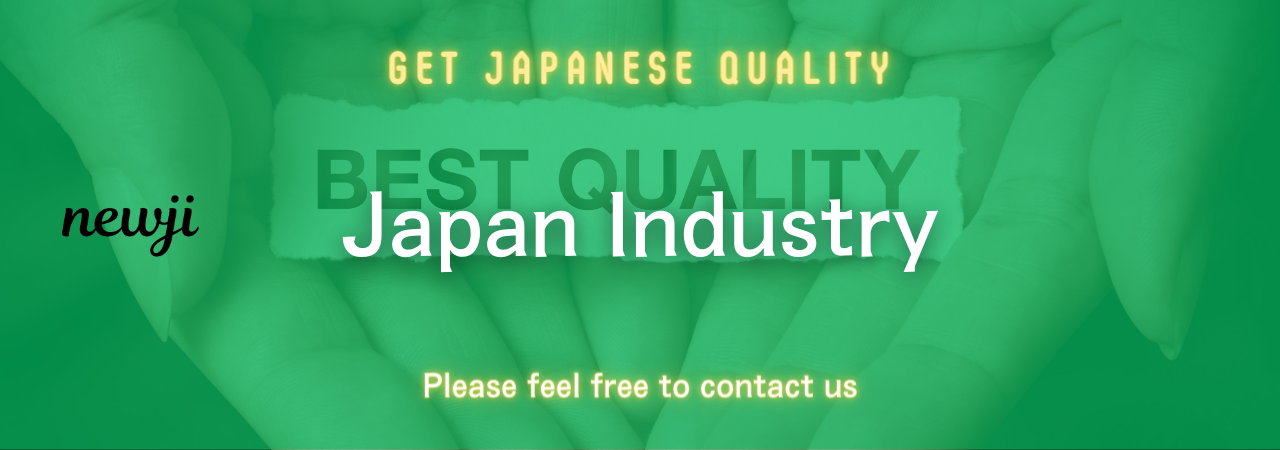
Introduction to Burrs in Molding Processes
In the world of manufacturing, burrs are a common but often overlooked issue.
Burrs are unwanted pieces of material that remain attached to a part after a manufacturing process, such as molding.
They can lead to a multitude of problems, including poor aesthetic quality, reduced functionality, and increased safety risks.
Understanding how to prevent burrs is essential for improving the efficiency and quality of molding processes.
Understanding How Burrs Form
Burrs can form in a variety of ways depending on the material and the manufacturing process involved.
In molding processes, burrs often appear when excess material flows into the small gaps or unwanted areas of the mold, known as flash.
This flash can become a burr if not adequately removed after the part is ejected from the mold.
Understanding the specific conditions under which burrs form is critical for implementing effective preventive measures.
Causes of Burr Formation
Several factors can lead to burr formation in molding processes.
One of the main causes is an improperly designed mold, where the fit between components is not tight enough to prevent material from leaking out.
Additionally, process parameters such as pressure, temperature, and injection speed can also impact burr formation.
Improper maintenance of equipment and worn-out tools are other contributors that can exacerbate the problem.
Common Techniques for Burr Prevention
Preventing burr formation starts with anticipating potential challenges during the molding process.
Several techniques can help in minimizing or eliminating burrs altogether.
Mold Design and Material Selection
Designing molds with tight tolerances is one of the most effective ways to prevent burr formation.
By ensuring there is minimal gap at the parting line, the chance of material leaking out is significantly reduced.
Additionally, choosing suitable materials for the mold can reduce wear and tear, which over time could contribute to burr formation.
Using high-quality, durable materials helps maintain precision in the molds over repeated cycles.
Optimizing Process Parameters
Fine-tuning the molding process parameters plays a crucial role in preventing burrs.
This involves setting the correct temperature and pressure for the specific material being molded.
By controlling these parameters, manufacturers can ensure that material flows properly into the mold without creating flash.
Regularly monitoring and adjusting these settings can adapt the process to varying conditions and new materials.
Regular Equipment Maintenance
Routine maintenance of molds and equipment is essential for burr prevention.
Regular inspections can identify any wear or misalignment in the molds, allowing for timely adjustments.
Keeping molding machines in optimal condition ensures consistent part production and reduces the likelihood of burrs appearing.
Maintaining a clean and efficient operating environment also contributes to minimizing debris that could affect the molding process.
Advanced Methods for Burr Prevention
While basic techniques serve as the foundation for burr prevention, advanced methods offer further enhancements in controlling burr formation.
Using Anti-Burr Technologies
Innovations in technology provide new ways to combat burr formation.
Anti-burr technologies, like advanced sensors and cameras, can detect unwanted material in the molding process in real-time.
These technologies enable manufacturers to make immediate adjustments and ensure the production of burr-free parts.
Implementation of Simulation Software
Simulation software allows for virtual testing of mold designs and process parameters before actual production.
By modeling the molding process, engineers can predict where burrs might form and devise strategies to prevent them.
This preemptive approach saves both time and resources in the long run.
Adopting Lean Manufacturing Practices
Lean manufacturing focuses on waste reduction, and burrs are a form of waste in the molding process.
By adopting lean principles, manufacturers can streamline production, improve mold designs, and enhance the efficiency of their processes.
This approach not only reduces burr formation but also improves overall product quality and reduces costs.
Conclusion
Burr prevention in molding processes is a multifaceted challenge requiring attention to mold design, process parameters, equipment maintenance, and advanced technologies.
By implementing effective burr prevention techniques and continuously optimizing processes, manufacturers can significantly enhance product quality and operational efficiency.
Staying informed about new developments and technologies will further support these efforts, ensuring that burrs remain minimal, if not entirely eliminated.
資料ダウンロード
QCD調達購買管理クラウド「newji」は、調達購買部門で必要なQCD管理全てを備えた、現場特化型兼クラウド型の今世紀最高の購買管理システムとなります。
ユーザー登録
調達購買業務の効率化だけでなく、システムを導入することで、コスト削減や製品・資材のステータス可視化のほか、属人化していた購買情報の共有化による内部不正防止や統制にも役立ちます。
NEWJI DX
製造業に特化したデジタルトランスフォーメーション(DX)の実現を目指す請負開発型のコンサルティングサービスです。AI、iPaaS、および先端の技術を駆使して、製造プロセスの効率化、業務効率化、チームワーク強化、コスト削減、品質向上を実現します。このサービスは、製造業の課題を深く理解し、それに対する最適なデジタルソリューションを提供することで、企業が持続的な成長とイノベーションを達成できるようサポートします。
オンライン講座
製造業、主に購買・調達部門にお勤めの方々に向けた情報を配信しております。
新任の方やベテランの方、管理職を対象とした幅広いコンテンツをご用意しております。
お問い合わせ
コストダウンが利益に直結する術だと理解していても、なかなか前に進めることができない状況。そんな時は、newjiのコストダウン自動化機能で大きく利益貢献しよう!
(Β版非公開)