- お役立ち記事
- Business models and platforms for DX in the manufacturing industry
月間76,176名の
製造業ご担当者様が閲覧しています*
*2025年3月31日現在のGoogle Analyticsのデータより
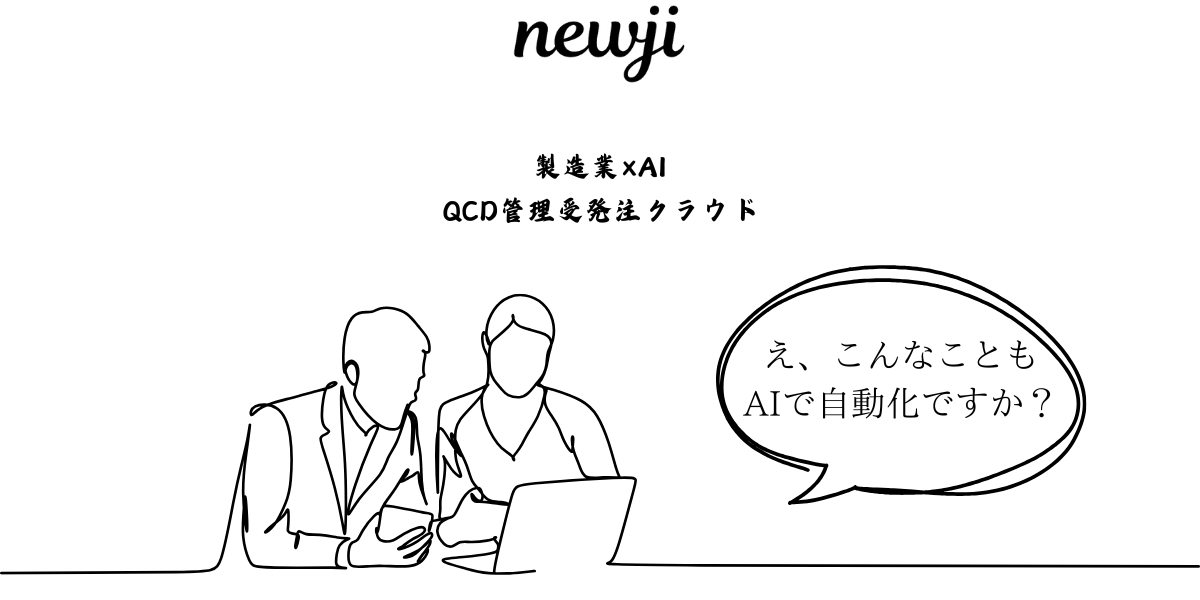
Business models and platforms for DX in the manufacturing industry
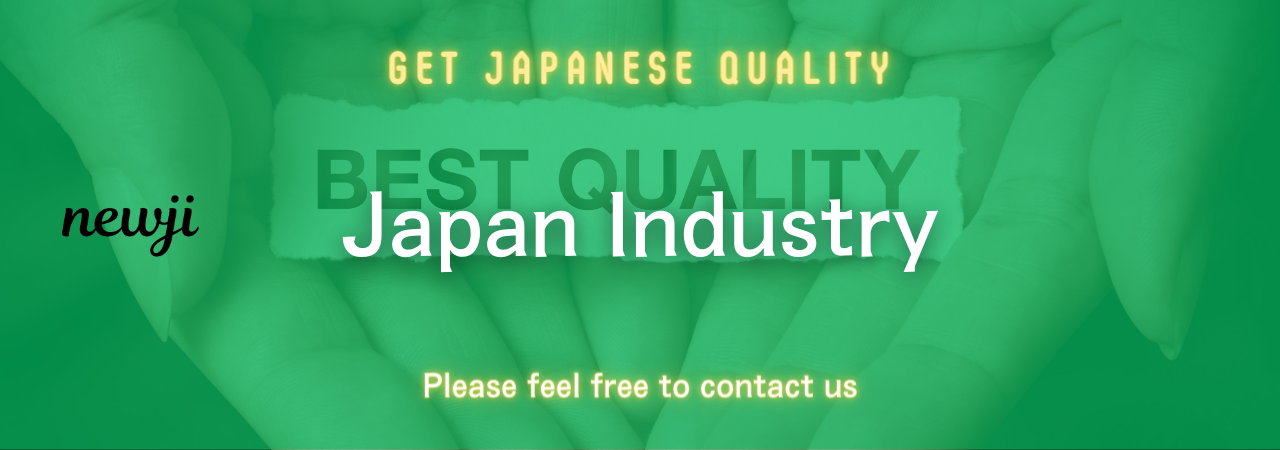
目次
Understanding Digital Transformation in Manufacturing
Digital transformation, often referred to as DX, is reshaping industries across the globe, and manufacturing is no exception.
It involves integrating digital technology into all areas of a business, fundamentally changing how it operates and delivers value to customers.
For the manufacturing sector, this transformation is crucial for staying competitive, improving efficiencies, and fostering innovation.
Manufacturers are now leveraging advanced technologies such as the Internet of Things (IoT), artificial intelligence (AI), and big data analytics to streamline their operations.
DX in manufacturing aims to optimize production processes, enhance product quality, or even create entirely new business models.
The goal is to become more agile, customer-centric, and efficient.
Key Business Models for Digital Transformation
There are several business models that manufacturers can adopt to successfully implement digital transformation.
Each of these models offers unique benefits and can be tailored to meet specific organizational needs.
1. Product-as-a-Service (PaaS)
One innovative model that many manufacturers are adopting is Product-as-a-Service (PaaS).
This model shifts the traditional sales approach from selling products to providing a service that includes the product.
This could mean leasing machinery rather than selling it outright, with additional services such as maintenance and updates included.
By adopting PaaS, manufacturers can establish ongoing relationships with their customers, ensuring consistent revenue streams.
This model also allows for better maintenance and monitoring of products, improving customer satisfaction and product longevity.
2. Smart Manufacturing
Smart manufacturing is another promising model for digital transformation.
It leverages technologies like IoT and AI to create a highly automated and data-driven production environment.
Smart factories can optimize production processes in real-time, reducing waste and improving efficiency.
With predictive maintenance, manufacturers can reduce downtime by anticipating equipment failures before they happen.
By analyzing data from connected devices, manufacturers can improve product quality and reduce costs.
3. Supply Chain Integration
Integrating digital technology into the supply chain is crucial for a seamless manufacturing process.
This model involves creating a digital network that connects all parts of the supply chain, from suppliers to customers.
Through the use of blockchain, manufacturers can ensure transparency and traceability in their supply chains.
Real-time data sharing allows for better inventory management, reducing excess stock and potential delays.
The Role of Platforms in Digital Transformation
Platforms play an essential role in facilitating digital transformation in the manufacturing industry.
They provide the infrastructure needed to implement the aforementioned business models effectively.
1. IoT Platforms
IoT platforms serve as the backbone of smart manufacturing.
They enable devices and systems to communicate with each other, creating an interconnected network of data-driven insights.
These platforms allow manufacturers to monitor and control machinery remotely, optimizing operations and reducing costs.
By harnessing the power of IoT platforms, manufacturers can achieve real-time visibility into their operations.
This data can be used to make informed decisions, enhance predictive maintenance, and improve overall production efficiency.
2. Cloud Computing Platforms
Cloud computing platforms provide the flexibility and scalability necessary for digital transformation.
They allow manufacturers to store and process large volumes of data without the need for expensive on-premises infrastructure.
This not only reduces costs but also allows for faster deployment of new digital solutions.
These platforms facilitate collaboration across different departments and locations.
By centralizing data and applications, they ensure that all stakeholders have access to the latest information, fostering innovation and improving decision-making.
3. Data Analytics Platforms
Data analytics platforms are crucial for making sense of the vast amounts of data generated in a digitally transformed manufacturing environment.
These platforms allow manufacturers to derive actionable insights from data, leading to better decision-making and strategic planning.
Through advanced analytics, manufacturers can analyze trends, predict market demands, and optimize their supply chains.
This data-driven approach helps in identifying areas for improvement and driving continuous innovation.
Challenges in Implementing Digital Transformation
While digital transformation presents a wealth of opportunities, it also comes with its own set of challenges.
Understanding these challenges is key to successfully implementing a digital transformation strategy.
1. Legacy Systems
Many manufacturers still rely on outdated systems and processes that are not compatible with modern digital technologies.
Integrating new technologies with these legacy systems can be complex and costly.
To overcome this challenge, manufacturers need to gradually phase out old systems and replace them with modern, agile solutions.
This requires careful planning and a clear understanding of the business needs.
2. Skills Gap
Digital transformation requires a workforce that is proficient in new technologies.
However, there is often a skills gap, with existing employees lacking the necessary expertise.
To address this challenge, manufacturers should invest in training and development programs to upskill their workforce.
This not only helps in implementing digital transformation but also increases employee engagement and retention.
3. Cybersecurity Concerns
With increased connectivity comes the risk of cyber-attacks.
Protecting sensitive data and ensuring the security of digital systems is a major concern for manufacturers.
Implementing robust cybersecurity measures, such as encryption and regular audits, is essential to safeguard data and maintain customer trust.
Manufacturers should also focus on building a strong security culture within the organization.
The Future of Digital Transformation in Manufacturing
The future of digital transformation in manufacturing is promising, with continuous advancements in technology driving innovation.
Manufacturers who embrace digital transformation will be well-positioned to thrive in an increasingly competitive market.
Key trends such as the adoption of artificial intelligence, machine learning, and advanced robotics will further enhance manufacturing processes.
These technologies will enable manufacturers to produce high-quality products faster and at a lower cost.
As the industry continues to evolve, digital transformation will become a critical component of any successful manufacturing strategy.
Manufacturers who leverage innovative business models and digital platforms will lead the way in creating value, improving efficiency, and delighting customers.
資料ダウンロード
QCD管理受発注クラウド「newji」は、受発注部門で必要なQCD管理全てを備えた、現場特化型兼クラウド型の今世紀最高の受発注管理システムとなります。
ユーザー登録
受発注業務の効率化だけでなく、システムを導入することで、コスト削減や製品・資材のステータス可視化のほか、属人化していた受発注情報の共有化による内部不正防止や統制にも役立ちます。
NEWJI DX
製造業に特化したデジタルトランスフォーメーション(DX)の実現を目指す請負開発型のコンサルティングサービスです。AI、iPaaS、および先端の技術を駆使して、製造プロセスの効率化、業務効率化、チームワーク強化、コスト削減、品質向上を実現します。このサービスは、製造業の課題を深く理解し、それに対する最適なデジタルソリューションを提供することで、企業が持続的な成長とイノベーションを達成できるようサポートします。
製造業ニュース解説
製造業、主に購買・調達部門にお勤めの方々に向けた情報を配信しております。
新任の方やベテランの方、管理職を対象とした幅広いコンテンツをご用意しております。
お問い合わせ
コストダウンが利益に直結する術だと理解していても、なかなか前に進めることができない状況。そんな時は、newjiのコストダウン自動化機能で大きく利益貢献しよう!
(β版非公開)