- お役立ち記事
- Business Process Reengineering (BPR) in Supply Chains: Success Stories and Practices
Business Process Reengineering (BPR) in Supply Chains: Success Stories and Practices
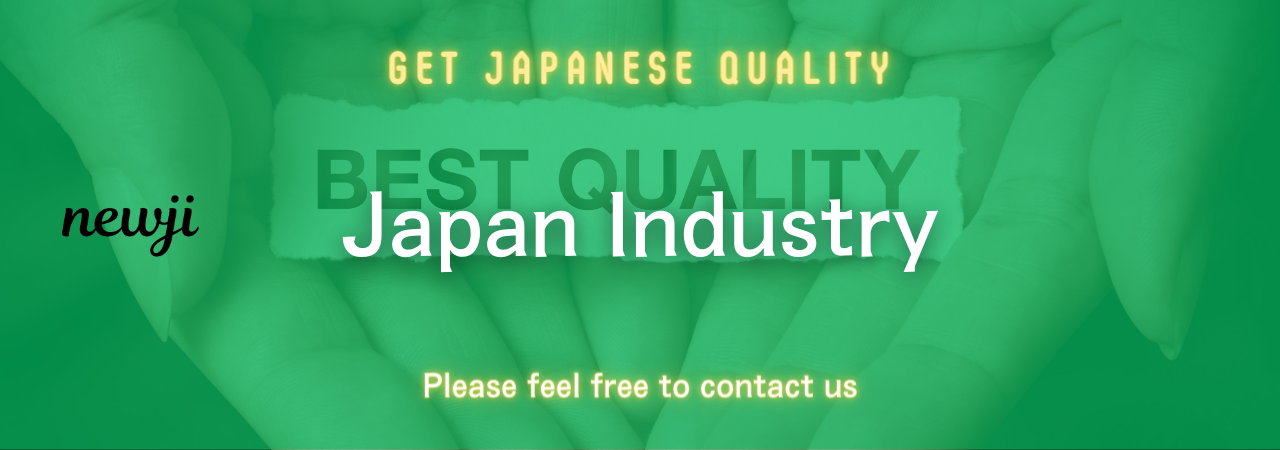
Business process reengineering (BPR) involves analyzing and redesigning core business procedures to achieve substantial improvements.
In supply chains, BPR can lead to significant efficiencies and cost savings.
By exploring success stories and best practices, companies can understand how BPR can transform their supply chain operations.
目次
What is Business Process Reengineering (BPR)?
Business process reengineering refers to the thorough examination and radical redesign of business processes.
Its goal is to achieve remarkable improvements in critical performance measures such as cost, service, quality, and speed.
Rather than making minor adjustments, BPR advocates implementing fundamental changes.
This approach often involves rethinking how work flows through the organization and leveraging technology to streamline processes.
The Importance of BPR in Supply Chains
A supply chain encompasses a network of suppliers, manufacturers, and retailers working together to produce and distribute products.
Given the complexity of supply chains, implementing BPR can address inefficiencies and bottlenecks.
It enhances operational efficiency, reduces costs, and improves customer satisfaction.
With the global market becoming more competitive, companies need BPR to stay ahead.
Reducing Lead Times
One major benefit of BPR in supply chains is the reduction of lead times.
By analyzing each step of the process, businesses can identify redundancies that slow down operations.
For example, implementing advanced inventory management systems can reduce the time needed to restock products.
This ensures products are available when customers need them, thereby increasing sales and customer loyalty.
Enhancing Collaboration
BPR fosters better collaboration among various entities in the supply chain.
Streamlining communication channels and integrating information systems can lead to more efficient decision-making.
For instance, real-time data sharing between suppliers and manufacturers allows for proactive adjustments in production schedules.
This minimizes delays and ensures smoother operations.
Success Stories in BPR for Supply Chains
Many companies have successfully implemented BPR and reaped its benefits.
By examining these success stories, businesses can glean insights into effective practices.
Cisco Systems
Cisco Systems, a global leader in networking technology, undertook BPR to enhance its supply chain efficiency.
Facing rapid market changes, Cisco aimed to streamline its supply chain to respond faster to customer demands.
They reengineered their processes by leveraging digital technologies and integrating supply chain operations.
Cisco implemented a centralized data management system that provided real-time visibility into inventory levels.
This enabled them to make data-driven decisions and reduce stockouts.
The result was a more responsive and agile supply chain that could better serve customers’ needs.
Ford Motor Company
Ford Motor Company, a pioneer in the automotive industry, also adopted BPR to overhaul its supply chain.
In the 1990s, Ford faced challenges related to inventory management and production delays.
By undertaking a thorough reengineering process, Ford managed to transform its operations.
Ford implemented techniques like Just-In-Time (JIT) manufacturing and Total Quality Management (TQM).
These efforts led to a reduction in inventory levels and improved production efficiency.
The company also leveraged technology to better connect its supply chain partners, ensuring smoother coordination.
Procter & Gamble (P&G)
Procter & Gamble (P&G), a global consumer goods giant, used BPR to address inefficiencies in its supply chain.
P&G aimed to optimize its product distribution and minimize delays.
The company restructured its supply chain by focusing on centralizing its logistics and inventory management systems.
By adopting advanced data analytics and automation, P&G was able to predict demand more accurately.
This led to optimized inventory levels and reduced stockouts.
The streamlined supply chain operations resulted in cost savings and improved customer satisfaction.
Best Practices for Implementing BPR in Supply Chains
When implementing BPR in supply chains, it’s essential to follow best practices to ensure success.
Clear Objectives and Vision
Define clear objectives and a vision for what you aim to achieve with BPR.
Whether it’s reducing costs, improving delivery times, or enhancing quality, having a clear focus will guide the reengineering process.
Communicate these goals across the organization to ensure everyone is aligned.
Involve Stakeholders
Involve all relevant stakeholders in the BPR process.
This includes suppliers, manufacturers, distributors, and customers.
Collaborative efforts ensure that everyone’s insights and needs are considered, leading to a more comprehensive and effective reengineering effort.
Leverage Technology
Technology plays a crucial role in BPR for supply chains.
Implementing advanced technologies such as automation, data analytics, and artificial intelligence can streamline processes and provide real-time insights.
These tools enable better decision-making and allow for proactive adjustments in the supply chain.
Continuous Improvement
BPR is not a one-time effort; it’s an ongoing process.
Continuously monitor and assess the effectiveness of the reengineered processes.
Gather feedback and make necessary adjustments to ensure sustained improvements.
Adopt a culture of continuous improvement to stay agile and responsive to changing market conditions.
Challenges in BPR for Supply Chains
While BPR offers significant benefits, it’s not without challenges.
Resistance to Change
One of the primary challenges is resistance to change.
Employees and stakeholders may be hesitant to adopt new processes and technologies.
It’s essential to communicate the benefits of BPR and involve them in the reengineering process to gain their buy-in.
Resource Constraints
Implementing BPR can be resource-intensive.
It may require significant investments in technology, training, and process redesign.
Companies need to allocate adequate resources and plan their budgets effectively to ensure successful implementation.
Complexity
Supply chains are inherently complex, and reengineering them can be a daunting task.
Analyzing and redesigning interconnected processes require careful planning and coordination.
Companies may need to engage experienced consultants to navigate the complexities of BPR.
Business process reengineering is a powerful tool for optimizing supply chains.
By studying success stories from companies like Cisco Systems, Ford Motor Company, and Procter & Gamble, businesses can understand the potential benefits of BPR.
Following best practices and addressing challenges can help companies achieve the desired improvements in their supply chain operations.
In a dynamic and competitive market, BPR provides the edge necessary to stay ahead and deliver exceptional value to customers.
資料ダウンロード
QCD調達購買管理クラウド「newji」は、調達購買部門で必要なQCD管理全てを備えた、現場特化型兼クラウド型の今世紀最高の購買管理システムとなります。
ユーザー登録
調達購買業務の効率化だけでなく、システムを導入することで、コスト削減や製品・資材のステータス可視化のほか、属人化していた購買情報の共有化による内部不正防止や統制にも役立ちます。
NEWJI DX
製造業に特化したデジタルトランスフォーメーション(DX)の実現を目指す請負開発型のコンサルティングサービスです。AI、iPaaS、および先端の技術を駆使して、製造プロセスの効率化、業務効率化、チームワーク強化、コスト削減、品質向上を実現します。このサービスは、製造業の課題を深く理解し、それに対する最適なデジタルソリューションを提供することで、企業が持続的な成長とイノベーションを達成できるようサポートします。
オンライン講座
製造業、主に購買・調達部門にお勤めの方々に向けた情報を配信しております。
新任の方やベテランの方、管理職を対象とした幅広いコンテンツをご用意しております。
お問い合わせ
コストダウンが利益に直結する術だと理解していても、なかなか前に進めることができない状況。そんな時は、newjiのコストダウン自動化機能で大きく利益貢献しよう!
(Β版非公開)