- お役立ち記事
- By requesting a prototype, we create a product that the client can be confident in! How to achieve both functionality and durability in small-volume production
月間76,176名の
製造業ご担当者様が閲覧しています*
*2025年3月31日現在のGoogle Analyticsのデータより
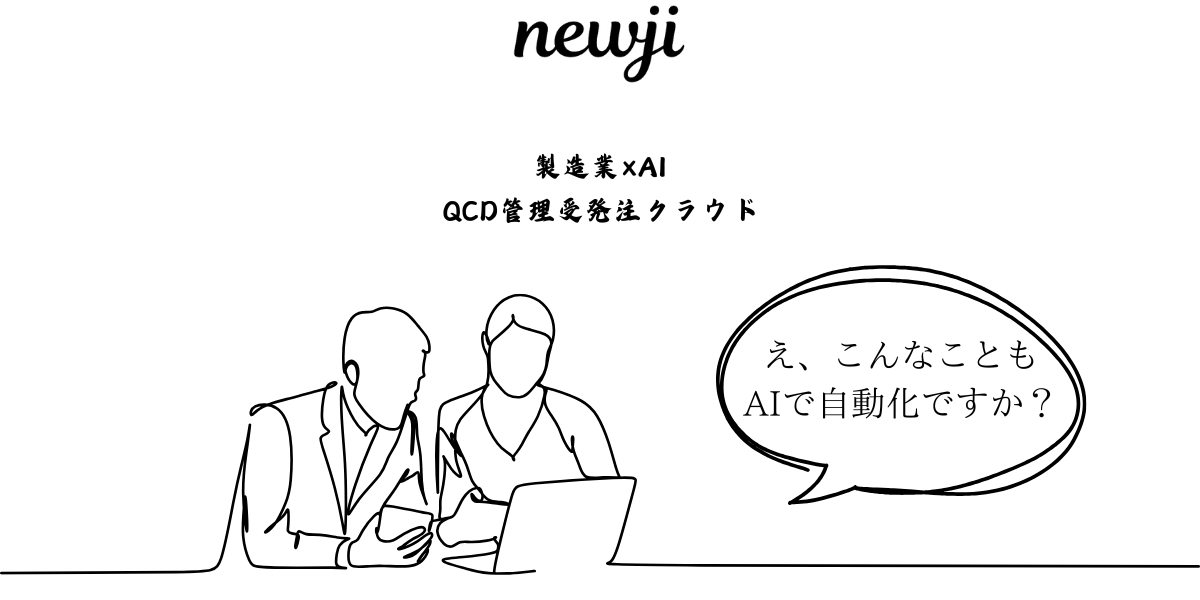
By requesting a prototype, we create a product that the client can be confident in! How to achieve both functionality and durability in small-volume production
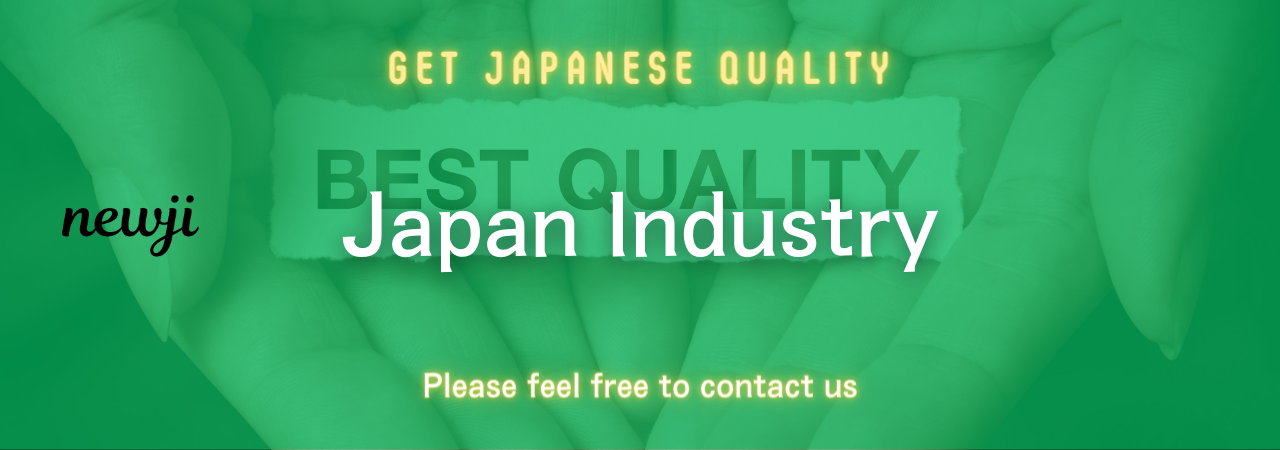
目次
Understanding the Importance of Prototyping
In today’s competitive market, ensuring that a product meets both functionality and durability standards is essential.
Creating a prototype is the first step towards achieving this, especially in small-volume production.
A prototype allows you and your team to visualize the product, test its functionality, and make improvements before mass production begins.
It is a crucial step to ensure that the final product meets customer expectations.
When embarking on the journey of product development, collaborating with clients to create a prototype should be the priority.
This helps to address issues and weaknesses early on, saving both time and resources in the process.
Balancing Functionality and Durability in Prototyping
When designing a product, balancing functionality and durability can be challenging.
Functionality refers to how well the product performs its intended tasks, while durability involves how long the product will last under expected usage.
The key is to meet client requirements by ensuring the prototype provides superior functionality without compromising on durability.
This is particularly important for small-volume production where each unit needs to meet rigorous standards due to lower production volumes.
Begin by understanding the intended use of the product and the environment in which it will be used.
This will affect the choice of materials and design solutions incorporated in the prototype.
Choose materials that are not only suitable for the functionality but also contribute to the longevity of the product.
Throughout the design process, keep in mind that finding a balance is essential to producing a successful prototype.
Choosing the Right Materials
The choice of materials is one of the most important aspects when creating a prototype.
Materials can significantly affect both the functionality and durability of the product.
By choosing materials that are both robust and efficient, you ensure that the prototype can withstand wear and tear while performing optimally.
For example, using lightweight alloys or specialty plastics can enhance both the lifespan and usability of the product.
Climate and environmental conditions should also be considered when selecting materials.
For example, if the product will be exposed to moisture or extreme temperatures, choosing corrosion-resistant and temperature-resistant materials is a wise decision.
Design Strategies for Enhanced Durability
Design plays a crucial role in ensuring that the prototype withstands usage over time.
Focusing on strategic design improvements can significantly enhance durability.
Consider incorporating design features like reinforced joints, additional support structures, or flexible design elements that can absorb shocks and stresses.
Using computer simulations and tests to validate the durability aspects of the design can be beneficial.
In some cases, modular design may be a suitable approach that allows for easy repair and component replacement, extending the product’s lifespan.
Engaging Clients in the Prototyping Process
Involving clients in the prototyping process is a strategy that ensures the final product aligns with their expectations.
Regularly engaging with clients and soliciting their feedback helps refine the prototype and build confidence in the product.
Transparency in communication builds trust, and showing clients the stages and progress helps them understand how their needs are being met.
Set clear expectations and demonstrate how you are addressing their requirements in terms of functionality and durability.
Presenting multiple iterations can allow clients to provide input on desirable features, aesthetic preferences, and any practical concerns they might have.
Testing and Iteration
Testing is a vital stage in prototyping.
It involves examining the product under real-world conditions to assess functionality and durability.
Conduct a series of tests to evaluate how the prototype functions and to identify any potential weaknesses.
Use this as an opportunity to gather data, make necessary adjustments, and refine the design further.
Iteration is crucial after testing—modifying and improving the prototype can lead to a better product.
It is not uncommon to go through several iterations before achieving a prototype that satisfies all criteria.
Leveraging Technology for Effective Prototyping
Modern technology offers numerous tools and resources that facilitate the prototyping process.
With advancements in 3D printing and computer-aided design (CAD), creating accurate models of the prototype has become more efficient.
These technologies allow for rapid prototyping, enabling you to create, test, and iterate designs much faster than traditional methods.
They provide a cost-effective way to make accurate alterations, ultimately leading to a durable and functional product.
Additionally, technology helps visualize complex designs and catch potential issues early on.
Emphasizing Quality Control
When creating a product, especially in small-volume production, a strong focus on quality control is essential.
It ensures each unit meets the high standards clients expect.
Implement rigorous quality checks throughout the prototyping phase, using standardized procedures to assess both function and durability.
Quality control should be a continuous process, from the initial design to the final product, helping to mitigate potential failures and recalls.
Conclusion
Prototyping is an integral part of product development, particularly in achieving both functionality and durability during small-volume production.
By carefully selecting materials, employing strategic design enhancements, and engaging clients throughout the process, you can create a product that meets expectations.
Utilize modern technology and focus on quality control to streamline efforts and deliver a superior product.
These steps not only increase client confidence but also ensure a successful outcome in competitive markets.
資料ダウンロード
QCD管理受発注クラウド「newji」は、受発注部門で必要なQCD管理全てを備えた、現場特化型兼クラウド型の今世紀最高の受発注管理システムとなります。
ユーザー登録
受発注業務の効率化だけでなく、システムを導入することで、コスト削減や製品・資材のステータス可視化のほか、属人化していた受発注情報の共有化による内部不正防止や統制にも役立ちます。
NEWJI DX
製造業に特化したデジタルトランスフォーメーション(DX)の実現を目指す請負開発型のコンサルティングサービスです。AI、iPaaS、および先端の技術を駆使して、製造プロセスの効率化、業務効率化、チームワーク強化、コスト削減、品質向上を実現します。このサービスは、製造業の課題を深く理解し、それに対する最適なデジタルソリューションを提供することで、企業が持続的な成長とイノベーションを達成できるようサポートします。
製造業ニュース解説
製造業、主に購買・調達部門にお勤めの方々に向けた情報を配信しております。
新任の方やベテランの方、管理職を対象とした幅広いコンテンツをご用意しております。
お問い合わせ
コストダウンが利益に直結する術だと理解していても、なかなか前に進めることができない状況。そんな時は、newjiのコストダウン自動化機能で大きく利益貢献しよう!
(β版非公開)