- お役立ち記事
- Cable Assembly OEM Manufacturing: Ensuring Efficient Wiring Management
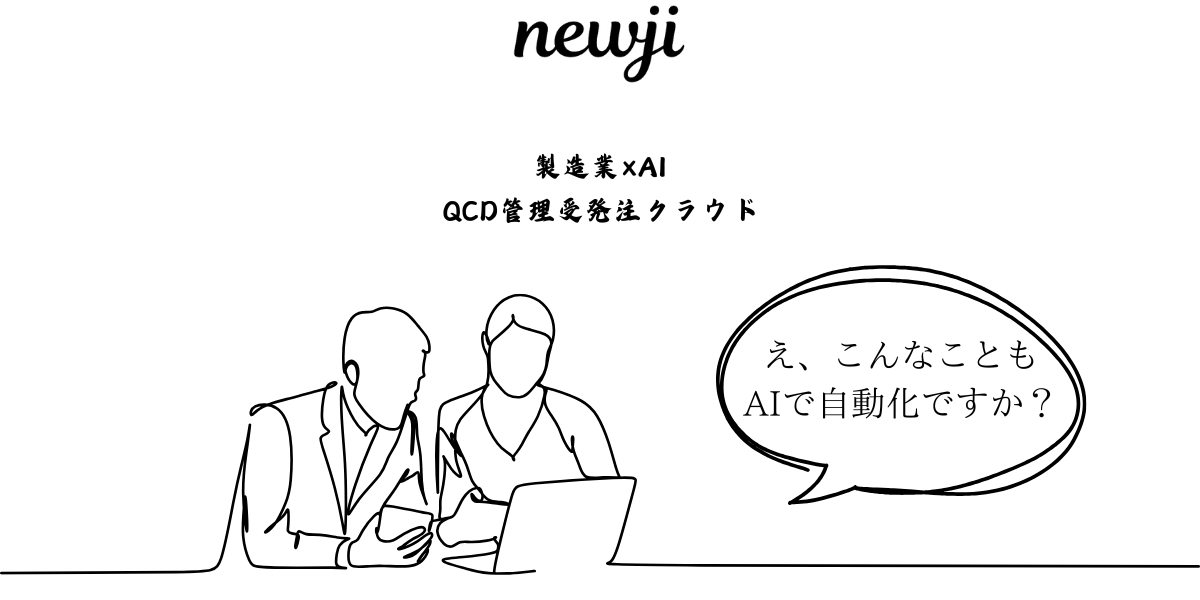
Cable Assembly OEM Manufacturing: Ensuring Efficient Wiring Management
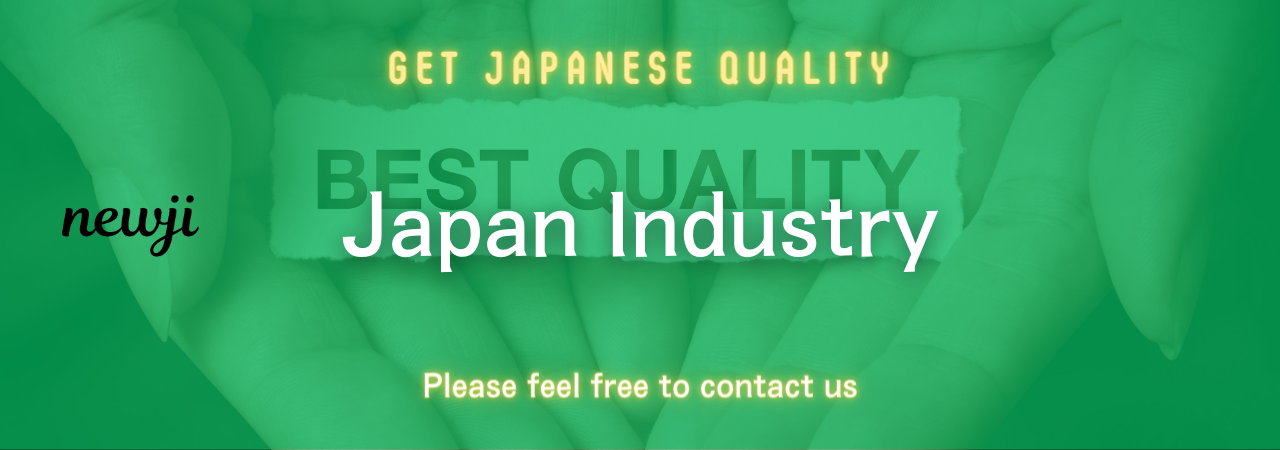
目次
Understanding Cable Assembly OEM Manufacturing
When you think about the wires and cables that power your favorite electronics, it’s easy to overlook the intricate process behind their assembly.
That’s where cable assembly OEM manufacturing comes into play.
Original Equipment Manufacturers (OEMs) specialize in creating precise, reliable cable assemblies tailored to specific needs.
This is essential for many industries, including automotive, aerospace, telecommunications, and healthcare.
The Importance of Efficient Wiring Management
Effective wiring management is crucial for several reasons.
First, it ensures the electrical system’s reliability.
Poorly managed cables can result in malfunctions, leading to costly downtime and repairs.
Moreover, a well-organized wiring system improves safety.
It reduces the risk of electrical shorts, fires, and other hazards.
Finally, efficient cable assembly enhances overall system performance.
It minimizes the chance of signal interference and maximizes the lifespan of the equipment.
Reliability
Reliability is a cornerstone of any electronic device or system.
When cables are properly assembled and managed, they are less likely to break down.
This reliability means fewer disruptions and less maintenance.
OEMs use high-quality materials and advanced techniques to ensure the durability and consistency of their cable assemblies.
Safety
Safety cannot be compromised in any setting, especially in sectors like healthcare and aerospace.
Incorrectly managed cables can lead to serious accidents.
By adhering to strict standards and regulations, OEM manufacturers ensure that their cable assemblies comply with safety guidelines.
Everything, from insulation to connector choices, is carefully thought out to prevent hazards.
Performance
The efficiency of a cable assembly directly impacts the performance of the overall system.
Properly managed wiring prevents signal loss and electrical noise.
This is especially important in high-performance environments like data centers and research laboratories.
OEMs optimize their cable assemblies to maintain data integrity and quick transmission speeds.
Steps in Cable Assembly OEM Manufacturing
The process of cable assembly OEM manufacturing involves multiple steps that require precision and expertise.
Below, we’ll outline the key stages from concept to production.
Designing the Cable Assembly
The first step in manufacturing a cable assembly is the design phase.
Engineers collaborate with clients to understand their specific requirements.
This includes determining the type of cables, connectors, and any additional components needed.
Software tools and simulations are often used to visualize the final product and make necessary adjustments before moving on to production.
Prototyping
Once the design is finalized, a prototype is created.
This allows for testing and validation to ensure the assembly meets all specifications and functional requirements.
Prototyping is a crucial step as it identifies any potential issues that could arise during mass production.
Feedback from this stage often leads to refinements in the design.
Material Selection
Choosing the right materials is vital for the success of the cable assembly.
Different applications require different types of wiring, insulation, and connectors.
For example, cables used in aerospace need to be lightweight yet highly durable.
In contrast, those used in medical devices may require stringent biocompatibility standards.
OEM manufacturers source high-quality materials that match the application’s specific needs.
Assembly Process
The actual assembly process involves cutting, stripping, crimping, and soldering wires.
Technicians use specialized equipment to ensure precision.
For large-scale orders, automated machines may be employed to speed up the process.
Quality checks are conducted at various stages to ensure each assembly meets the set standards.
Testing and Quality Assurance
No cable assembly leaves the OEM facility without thorough testing.
This can include electrical tests, mechanical tests, and environmental tests to simulate real-world conditions.
High-quality OEMs have stringent quality assurance processes to catch any defects before the product reaches the customer.
Packaging and Delivery
Once testing is complete, cable assemblies are carefully packaged to prevent damage during transit.
OEMs often offer customization options in packaging to meet client needs.
Timely delivery is crucial, as any delays can impact the client’s production schedule.
The Future of Cable Assembly OEM Manufacturing
The industry of cable assembly OEM manufacturing is continuously evolving.
Technological advancements are spearheading innovations that improve efficiency, reliability, and performance.
Automation and Robotics
One of the significant trends is the increased use of automation and robotics.
These technologies streamline the manufacturing process and enhance precision.
Automated systems can handle repetitive tasks with high accuracy, reducing the risk of human errors.
Smart Cables
Another innovation is the development of smart cables.
These cables can monitor their own condition and performance, providing real-time data to the user.
This feature is especially useful in critical applications like healthcare and aerospace, where equipment reliability is paramount.
Environmental Sustainability
OEMs are also focusing on sustainable practices.
From using eco-friendly materials to energy-efficient manufacturing processes, the industry is moving towards reducing its environmental footprint.
Choosing the Right OEM Manufacturer
Selecting the right OEM manufacturer for your cable assembly needs is crucial.
Here are some factors to consider:
Experience and Expertise
Experience matters.
Look for a manufacturer with a proven track record in producing high-quality cable assemblies.
Their expertise will ensure that they can handle any challenges that may arise during the project.
Quality Standards
Ensure the manufacturer adheres to international quality standards.
Certifications like ISO 9001 can provide assurance that the manufacturer maintains rigorous quality control processes.
Customization Capabilities
Every application is unique.
Your OEM manufacturer should be able to offer customized solutions tailored to your specific requirements.
Customer Support
Good communication and support are essential.
Choose a manufacturer who is responsive and willing to collaborate closely with you throughout the project.
In conclusion, cable assembly OEM manufacturing plays a vital role in ensuring efficient wiring management across various industries.
Understanding the importance of reliability, safety, and performance, coupled with the right manufacturing processes, can significantly enhance the overall quality and functionality of electronic systems.
As technology advances, so will the innovations in this field, promising even better and smarter cable assemblies in the future.
資料ダウンロード
QCD調達購買管理クラウド「newji」は、調達購買部門で必要なQCD管理全てを備えた、現場特化型兼クラウド型の今世紀最高の購買管理システムとなります。
ユーザー登録
調達購買業務の効率化だけでなく、システムを導入することで、コスト削減や製品・資材のステータス可視化のほか、属人化していた購買情報の共有化による内部不正防止や統制にも役立ちます。
NEWJI DX
製造業に特化したデジタルトランスフォーメーション(DX)の実現を目指す請負開発型のコンサルティングサービスです。AI、iPaaS、および先端の技術を駆使して、製造プロセスの効率化、業務効率化、チームワーク強化、コスト削減、品質向上を実現します。このサービスは、製造業の課題を深く理解し、それに対する最適なデジタルソリューションを提供することで、企業が持続的な成長とイノベーションを達成できるようサポートします。
オンライン講座
製造業、主に購買・調達部門にお勤めの方々に向けた情報を配信しております。
新任の方やベテランの方、管理職を対象とした幅広いコンテンツをご用意しております。
お問い合わせ
コストダウンが利益に直結する術だと理解していても、なかなか前に進めることができない状況。そんな時は、newjiのコストダウン自動化機能で大きく利益貢献しよう!
(Β版非公開)