- お役立ち記事
- CAE for Strength Analysis: Practical Techniques for Designers
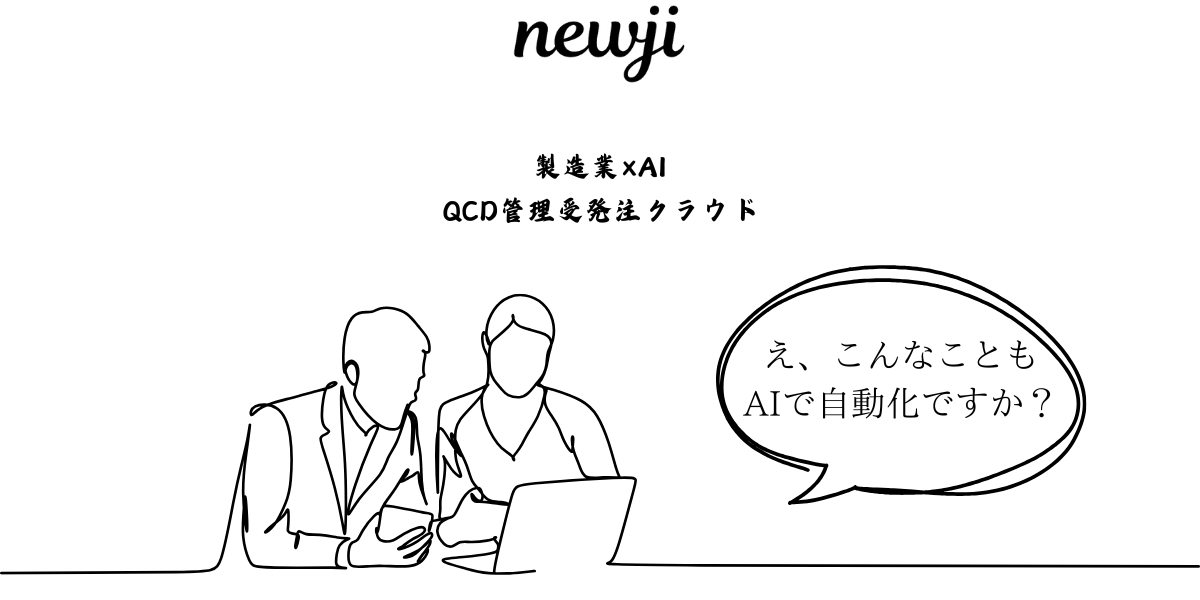
CAE for Strength Analysis: Practical Techniques for Designers
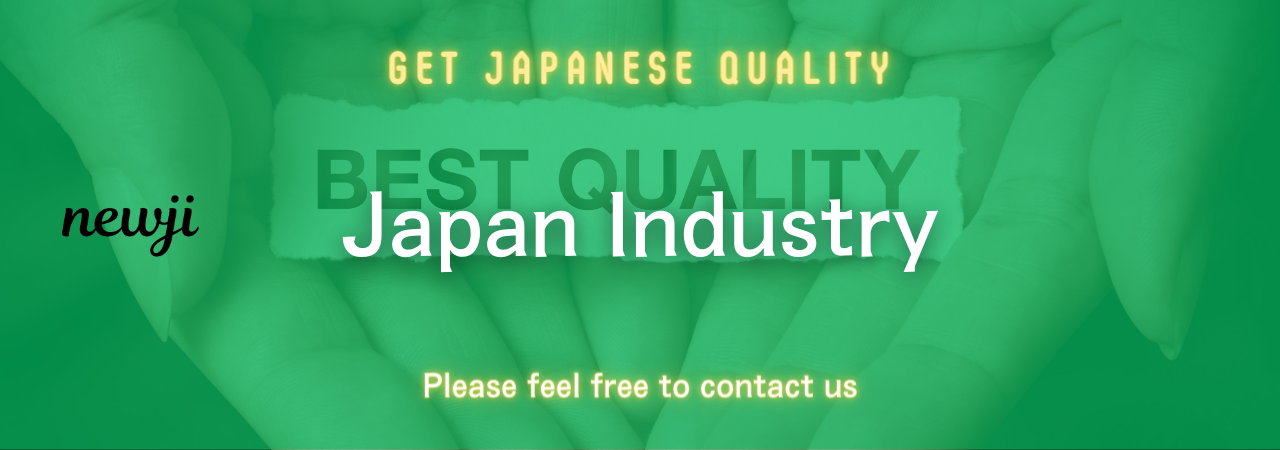
目次
Introduction to CAE for Strength Analysis
Computer-Aided Engineering (CAE) has revolutionized how designers and engineers approach problem-solving in various industries.
When it comes to strength analysis, CAE provides invaluable tools that help design professionals simulate and test the durability and resilience of their products under different conditions.
By leveraging CAE, designers can predict product behavior before physical prototypes are created, saving time, resources, and ensuring more optimized performance.
The Role of CAE in Strength Analysis
Strength analysis is crucial in evaluating whether a product can withstand the loads and stresses expected during its lifecycle.
CAE software offers detailed insights into the structural integrity of designs, using simulations to predict performance under various conditions.
By integrating strength analysis into the design process, engineers can identify potential weak points and optimize products for durability.
Benefits of Using CAE in Strength Analysis
One of the major advantages of using CAE for strength analysis is the ability to conduct virtual testing.
This reduces the need for costly and time-consuming physical prototypes.
Furthermore, CAE tools allow for the analysis of complex geometries and materials that might be difficult to test with traditional methods.
Designers can adjust and refine their designs quickly, leading to faster innovation cycles.
How CAE Tools Work
CAE software utilizes finite element analysis (FEA) to simulate real-world physical forces.
Through FEA, a product’s digital model is divided into smaller, manageable parts known as elements.
The software then applies forces, constraints, and loads to the model, calculating the response of each element.
This analysis gives designers a comprehensive view of stress distribution, displacement, and potential failure points within the product.
Application of CAE in Various Industries
Different industries benefit from CAE for strength analysis in unique ways.
Automotive Industry
In the automotive sector, CAE ensures vehicle components are lightweight yet strong enough to meet safety standards.
Strength analysis helps in designing crashworthy structures and optimizing material usage, leading to better fuel efficiency and compliance with safety regulations.
Aerospace Industry
The aerospace industry heavily relies on CAE to ensure the structural integrity of aircraft.
Given the high stakes and extreme conditions, strength analysis is critical for testing materials, components, and overall aircraft designs to ensure safety and performance.
Consumer Electronics
For consumer electronics, CAE helps design robust products that can withstand drops, impacts, and environmental stresses.
A well-conducted strength analysis ensures longevity and reliability which are essential selling points for these types of products.
Practical Techniques for Effective CAE Strength Analysis
While CAE is a powerful tool, its effectiveness heavily depends on correct application techniques.
Creating Accurate Models
The first step is creating a precise digital model of the product.
This involves ensuring dimensions, materials, and constraints are accurate and reflective of real-world conditions.
The model should include all foreseeable factors that can affect the product, providing a realistic basis for the simulation.
Selecting the Right Material Models
CAE tools have a vast library of material properties, and selecting the correct material model is vital.
Understanding the material characteristics and how they respond under stress will provide more reliable simulation results.
Special attention should be paid to new materials or composite materials that might require customized material models.
Refining the Mesh
Meshing is the process of breaking down the model into smaller elements.
A finer mesh will usually yield more accurate results but may increase computational time.
Striking a balance between mesh density and simulation time is crucial.
Focus on areas with high stress or complex geometry for finer mesh application.
Validating and Verifying Results
Simulation results must be validated and verified against experimental data or known benchmarks to ensure accuracy.
Validation ensures that the model accurately represents the physical scenario, while verification checks the correctness of the solution.
Iterative adjustments and comparisons with physical tests help refine the model and improve simulation fidelity.
Conclusion
CAE for strength analysis is an indispensable tool in the modern design landscape.
It empowers engineers and designers to create better products by providing detailed insights into their strength and performance early in the design process.
By understanding the practical techniques for effective CAE application, designers can harness its full potential to produce safe, reliable, and efficient products.
As industries continue to innovate, the role of CAE in strength analysis will only become more critical in developing the next generation of products.
資料ダウンロード
QCD調達購買管理クラウド「newji」は、調達購買部門で必要なQCD管理全てを備えた、現場特化型兼クラウド型の今世紀最高の購買管理システムとなります。
ユーザー登録
調達購買業務の効率化だけでなく、システムを導入することで、コスト削減や製品・資材のステータス可視化のほか、属人化していた購買情報の共有化による内部不正防止や統制にも役立ちます。
NEWJI DX
製造業に特化したデジタルトランスフォーメーション(DX)の実現を目指す請負開発型のコンサルティングサービスです。AI、iPaaS、および先端の技術を駆使して、製造プロセスの効率化、業務効率化、チームワーク強化、コスト削減、品質向上を実現します。このサービスは、製造業の課題を深く理解し、それに対する最適なデジタルソリューションを提供することで、企業が持続的な成長とイノベーションを達成できるようサポートします。
オンライン講座
製造業、主に購買・調達部門にお勤めの方々に向けた情報を配信しております。
新任の方やベテランの方、管理職を対象とした幅広いコンテンツをご用意しております。
お問い合わせ
コストダウンが利益に直結する術だと理解していても、なかなか前に進めることができない状況。そんな時は、newjiのコストダウン自動化機能で大きく利益貢献しよう!
(Β版非公開)