- お役立ち記事
- Calibration Importance and Practices in Manufacturing
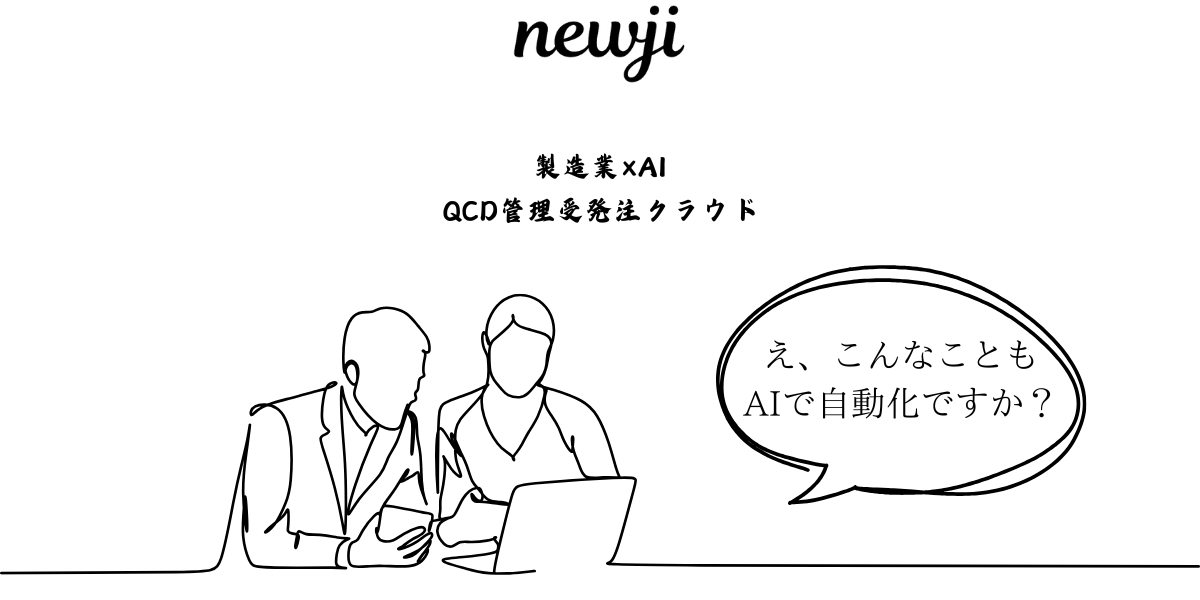
Calibration Importance and Practices in Manufacturing
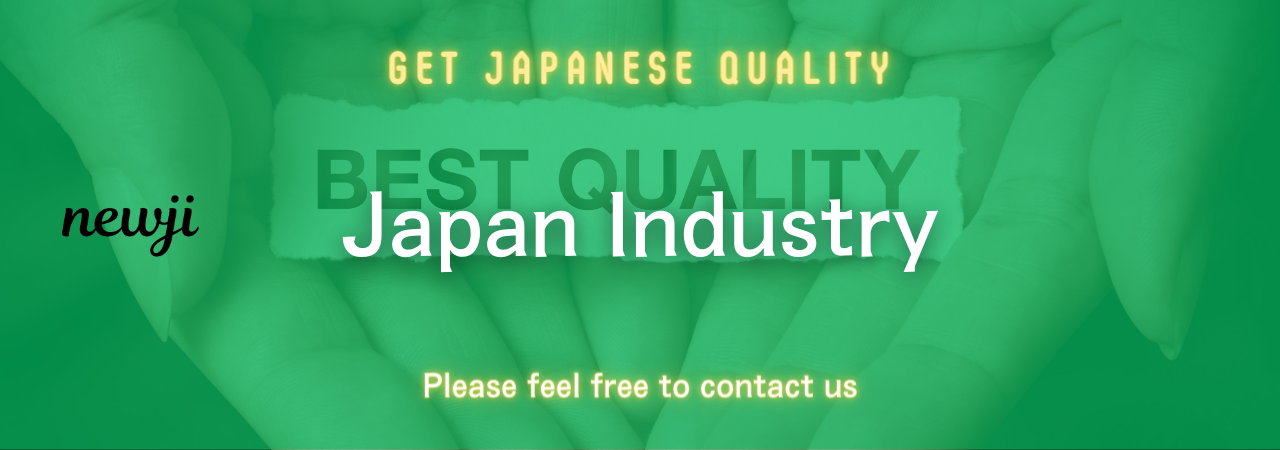
目次
Introduction to Calibration in Manufacturing
Calibration plays a crucial role in manufacturing.
Ensuring accuracy and precision in measurements can often determine the quality and consistency of products.
Calibration ensures that instruments and devices used in the manufacturing process are giving accurate readings.
With continuous advancements in technology, maintaining the integrity of measurements has never been more critical.
The Importance of Calibration
Consistency in Production
One of the main reasons for calibration is to ensure consistency.
When machines provide consistent measurements, products will have uniform quality.
This consistency is essential for meeting industry standards and customer expectations.
Compliance and Standards
Many industries have stringent regulations that require precise measurements.
Compliance with these regulations is mandatory to avoid legal issues.
Calibration ensures that instruments meet these regulatory standards, safeguarding the company’s reputation.
Cost Efficiency
Accurate instruments reduce waste and rework.
By ensuring that measurements are correct, manufacturers can avoid costly errors.
This efficiency translates to savings in both time and resources, ultimately enhancing profitability.
Calibration Practices
Regular Scheduling
It’s vital to have a regular calibration schedule.
Instruments should be calibrated at scheduled intervals to ensure their accuracy.
The frequency of calibration depends on the usage and the type of instrument.
Environmental Considerations
Environmental factors like temperature and humidity can affect measurements.
Calibrate instruments in conditions similar to their operational environment.
This practice ensures the reliability of the measurements under real-world conditions.
Using Certified Standards
Utilize certified reference standards for calibration.
These standards are traceable to national or international standards.
They provide a benchmark for accuracy, ensuring that the instruments are within the required tolerance levels.
Documentation and Traceability
Maintain detailed records of all calibration activities.
These documents should include the date of calibration, results, and any adjustments made.
Proper documentation ensures traceability and helps in audits and compliance checks.
Challenges in Calibration
Instrument Wear and Tear
Over time, instruments can wear out.
Wear and tear can lead to drifts in measurements.
Regular calibration helps in identifying and rectifying these drifts, ensuring that the instruments remain accurate.
Human Error
Calibration often involves manual processes.
Human error can lead to inaccuracies.
Implementing automated calibration systems can minimize these errors and enhance precision.
Technological Advancements
With technology constantly evolving, keeping up with the latest calibration techniques can be challenging.
Stay updated with the latest advancements to ensure optimal calibration practices.
Future Trends in Calibration
Automated Calibration Systems
The future of calibration lies in automation.
Automated systems reduce human errors and increase efficiency.
They enable real-time monitoring and adjustments, ensuring continuous accuracy.
Internet of Things (IoT)
IoT technology allows for remote monitoring and calibration of instruments.
This connectivity enables manufacturers to keep their equipment optimized, irrespective of their location.
Predictive Maintenance
Predictive maintenance uses data analytics to foresee potential issues with instruments.
By predicting when an instrument will need calibration, manufacturers can avoid unexpected downtime and maintain continuous production.
Conclusion
Calibration is a critical aspect of manufacturing, ensuring consistency, compliance, and cost efficiency.
Implementing rigorous calibration practices and staying updated with technological advancements can significantly enhance manufacturing processes.
By understanding the importance of calibration and adhering to best practices, manufacturers can maintain the highest levels of accuracy and quality in their products.
資料ダウンロード
QCD調達購買管理クラウド「newji」は、調達購買部門で必要なQCD管理全てを備えた、現場特化型兼クラウド型の今世紀最高の購買管理システムとなります。
ユーザー登録
調達購買業務の効率化だけでなく、システムを導入することで、コスト削減や製品・資材のステータス可視化のほか、属人化していた購買情報の共有化による内部不正防止や統制にも役立ちます。
NEWJI DX
製造業に特化したデジタルトランスフォーメーション(DX)の実現を目指す請負開発型のコンサルティングサービスです。AI、iPaaS、および先端の技術を駆使して、製造プロセスの効率化、業務効率化、チームワーク強化、コスト削減、品質向上を実現します。このサービスは、製造業の課題を深く理解し、それに対する最適なデジタルソリューションを提供することで、企業が持続的な成長とイノベーションを達成できるようサポートします。
オンライン講座
製造業、主に購買・調達部門にお勤めの方々に向けた情報を配信しております。
新任の方やベテランの方、管理職を対象とした幅広いコンテンツをご用意しております。
お問い合わせ
コストダウンが利益に直結する術だと理解していても、なかなか前に進めることができない状況。そんな時は、newjiのコストダウン自動化機能で大きく利益貢献しよう!
(Β版非公開)