- お役立ち記事
- Calking Technology and Application: Machining Processes for Improving Part Assembly and Joint Strength
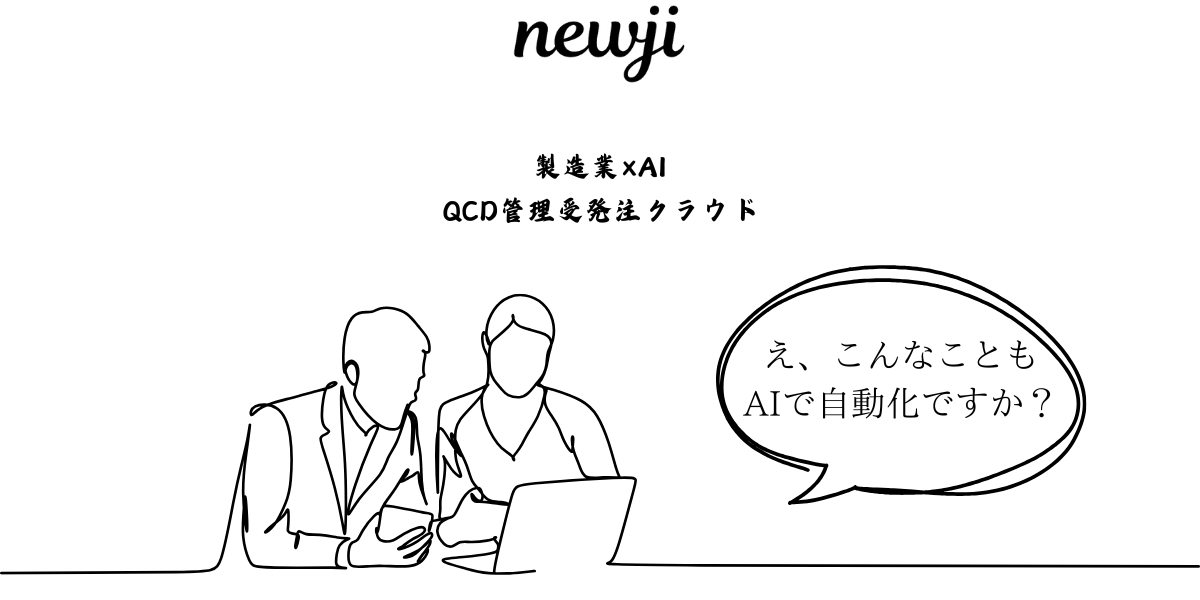
Calking Technology and Application: Machining Processes for Improving Part Assembly and Joint Strength
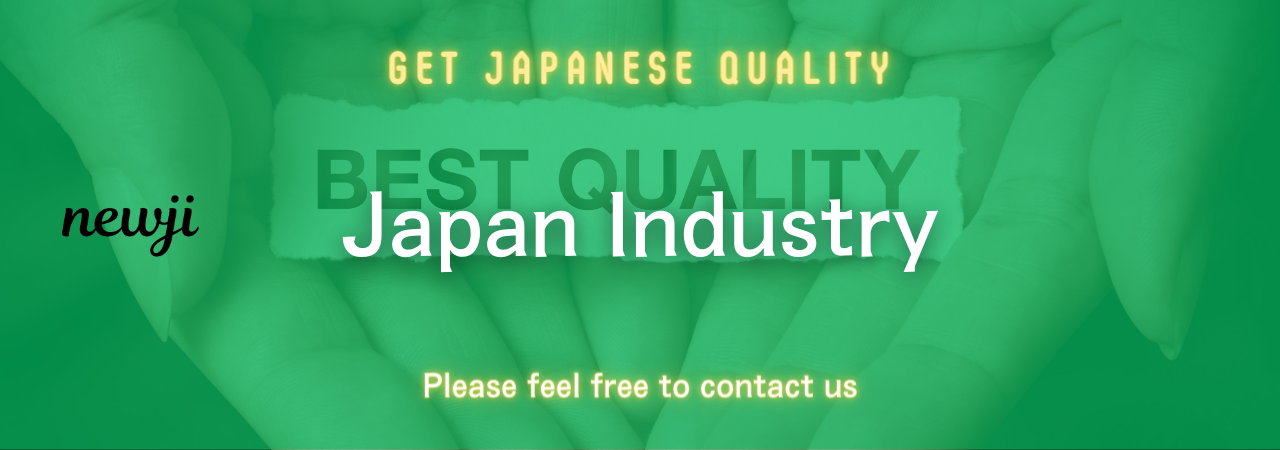
Machining processes play a crucial role in modern manufacturing, improving part assembly and joint strength.
One innovative technique that has gained significant attention is calking technology.
Let’s explore how this process works and how it benefits various industries.
目次
What is Calking Technology?
Calking, also known as caulking, involves the permanent deformation of materials to achieve a tight and secure joint.
This process typically uses mechanical forces to press or deform one part into or around another, creating an interlocking bond without the need for adhesives or fasteners.
It is commonly used in metalworking and automotive industries to enhance the integrity and durability of assembled components.
The Importance of Calking in Manufacturing
Enhanced Joint Strength
One of the primary benefits of calking technology is its ability to significantly improve joint strength.
By creating a strong mechanical bond, calking ensures that parts remain securely connected, even under high stress or load conditions.
This is particularly important in applications where safety and reliability are critical, such as in automotive, aerospace, and heavy machinery industries.
Improved Assembly Processes
Calking technology simplifies the assembly process by eliminating the need for additional fasteners, adhesives, or welding.
This not only reduces production costs but also minimizes the risk of errors or defects during assembly.
Additionally, calking allows for faster and more efficient production, as components can be quickly and accurately joined together using automated machinery.
Increased Durability and Longevity
Calking creates a tight, secure bond that resists vibration, thermal expansion, and other environmental factors that can weaken joints over time.
As a result, calked assemblies tend to have a longer lifespan and require less maintenance compared to those using traditional fastening methods.
This is especially beneficial in industries where equipment reliability is crucial for continuous operation and safety.
Types of Calking Processes
Several different types of calking processes can be employed depending on the materials, applications, and desired outcomes.
Roller Calking
Roller calking involves using rollers to apply pressure and deform the material, creating an interlocking bond.
This method is commonly used for joining cylindrical components, such as pipes or tubing.
Roller calking is highly efficient and can be easily integrated into automated production lines.
Radial Calking
Radial calking utilizes radial forces to deform the material, typically through the use of a calking tool or machine.
This process is ideal for applications that require high precision and uniform pressure distribution, such as in the assembly of automotive parts or aerospace components.
Orbital Calking
Orbital calking involves the use of an orbital tool that applies pressure in a circular motion, gradually deforming the material to create a secure joint.
This method is particularly effective for applications that require a smooth, consistent finish, such as in the production of electronic devices or medical equipment.
Applications of Calking Technology
Calking technology is used across a wide range of industries and applications, thanks to its versatility and effectiveness.
Automotive Industry
In the automotive industry, calking is used to assemble various components, including engine parts, exhaust systems, and body panels.
Calking ensures that these connections are strong, durable, and capable of withstanding the high stresses and vibrations experienced during vehicle operation.
Aerospace Industry
The aerospace industry relies on calking technology to join critical components, such as fuselage sections, wing assemblies, and hydraulic systems.
The precision and strength provided by calking are essential for maintaining the safety and integrity of aircraft under extreme conditions.
Heavy Machinery
In heavy machinery manufacturing, calking is used to assemble large, complex components, such as hydraulic cylinders, gearboxes, and structural frames.
Calking provides the necessary strength and durability to ensure these machines can operate reliably in demanding environments.
Electronics and Medical Devices
Calking is also used in the production of electronic devices and medical equipment, where precision and reliability are paramount.
Examples include battery assemblies, connector housings, and surgical instruments, all of which benefit from the secure, long-lasting bonds created by calking.
Advantages of Calking Technology
Calking technology offers several advantages over traditional fastening methods, making it an attractive option for many manufacturers.
Cost-Effective Production
By eliminating the need for additional fasteners, adhesives, or welding, calking reduces material costs and simplifies the assembly process.
This leads to lower production costs and increased efficiency, which can ultimately result in more competitive pricing for finished products.
Improved Reliability and Performance
The strong, secure bonds created by calking ensure that assembled components remain intact and functional, even under challenging conditions.
This reliability translates to improved performance and reduced maintenance needs, which are valuable benefits for both manufacturers and end-users.
Environmental Benefits
Calking technology is an environmentally friendly option, as it reduces the need for chemical adhesives and minimizes the generation of waste.
Additionally, the longer lifespan and reduced maintenance requirements of calked assemblies contribute to a more sustainable product lifecycle.
Conclusion
Calking technology is a powerful and versatile machining process that offers numerous benefits for improving part assembly and joint strength.
Its ability to create strong, durable bonds without the need for additional fasteners or adhesives makes it an attractive option for a wide range of industries.
By understanding the various types of calking processes and their applications, manufacturers can harness this innovative technology to enhance their production capabilities and deliver high-quality, reliable products to their customers.
資料ダウンロード
QCD調達購買管理クラウド「newji」は、調達購買部門で必要なQCD管理全てを備えた、現場特化型兼クラウド型の今世紀最高の購買管理システムとなります。
ユーザー登録
調達購買業務の効率化だけでなく、システムを導入することで、コスト削減や製品・資材のステータス可視化のほか、属人化していた購買情報の共有化による内部不正防止や統制にも役立ちます。
NEWJI DX
製造業に特化したデジタルトランスフォーメーション(DX)の実現を目指す請負開発型のコンサルティングサービスです。AI、iPaaS、および先端の技術を駆使して、製造プロセスの効率化、業務効率化、チームワーク強化、コスト削減、品質向上を実現します。このサービスは、製造業の課題を深く理解し、それに対する最適なデジタルソリューションを提供することで、企業が持続的な成長とイノベーションを達成できるようサポートします。
オンライン講座
製造業、主に購買・調達部門にお勤めの方々に向けた情報を配信しております。
新任の方やベテランの方、管理職を対象とした幅広いコンテンツをご用意しております。
お問い合わせ
コストダウンが利益に直結する術だと理解していても、なかなか前に進めることができない状況。そんな時は、newjiのコストダウン自動化機能で大きく利益貢献しよう!
(Β版非公開)