- お役立ち記事
- CAN protocol basics, control and applications/latest technology
月間77,185名の
製造業ご担当者様が閲覧しています*
*2025年2月28日現在のGoogle Analyticsのデータより
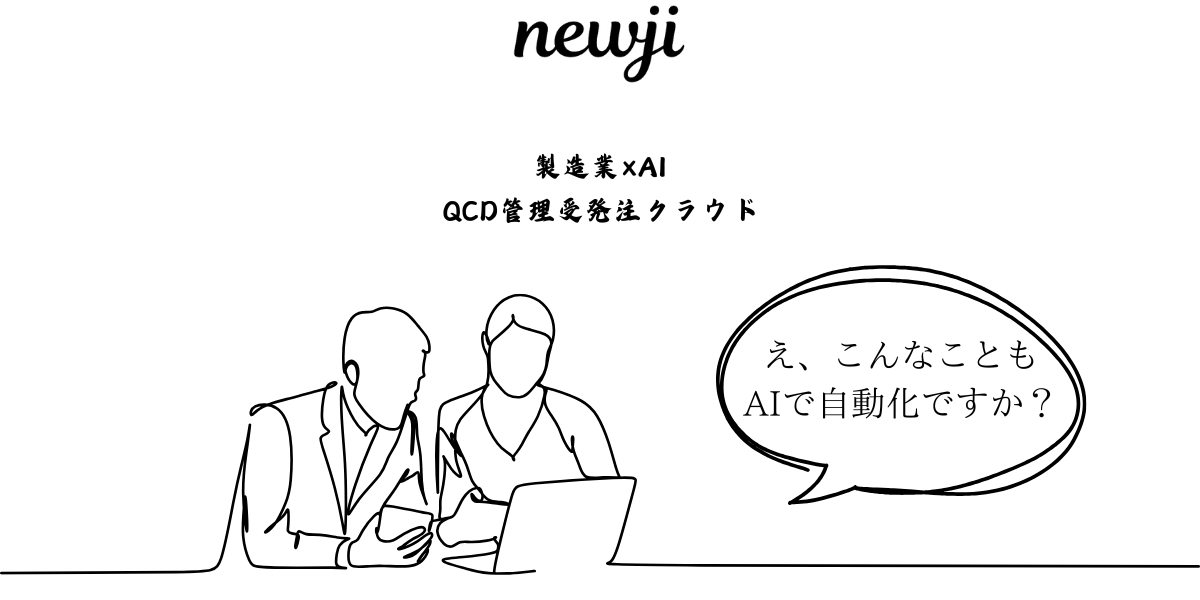
CAN protocol basics, control and applications/latest technology
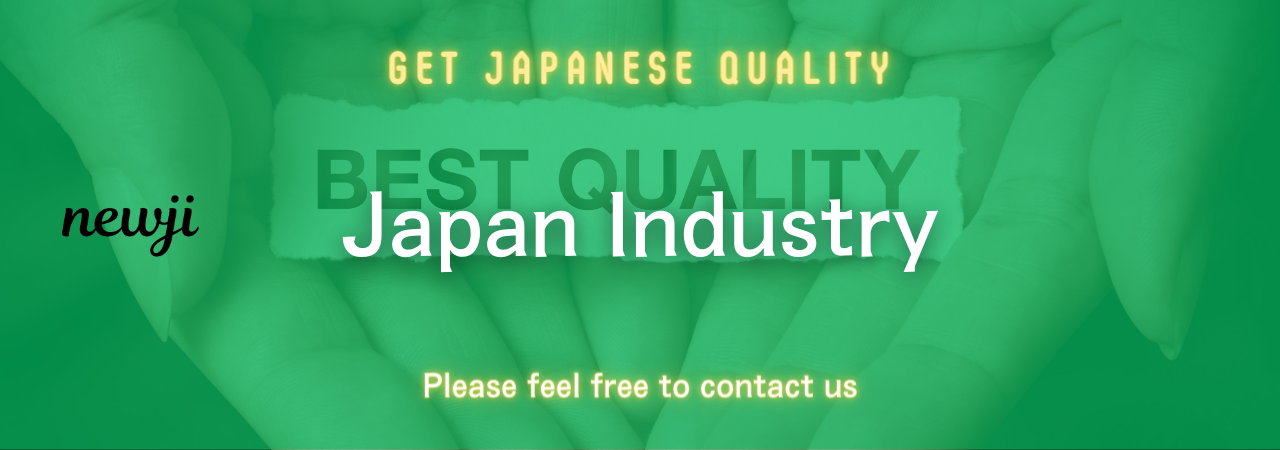
目次
Understanding the Basics of CAN Protocol
The Controller Area Network (CAN) protocol is a communication system that enables robust and seamless data exchange between devices within a network, whether it’s in vehicles, machinery, or modern computing systems.
Initially developed for automotive purposes, its reliability and efficiency have made it popular across various industries.
To understand the basics of CAN protocol, let’s dive into its core components and functions.
What is CAN Protocol?
The CAN protocol is a robust serial communication protocol used primarily in vehicles to connect various electronic control units (ECUs).
Introduced in the 1980s by Bosch, it ensures that different devices in complex systems can communicate effectively without a central computer.
It’s like a language that microcontrollers and devices use to exchange information efficiently.
How Does CAN Protocol Work?
The CAN protocol operates on a multi-master basis, meaning each node (or device) can send and receive messages anytime.
This dynamic approach ensures that data flow remains uninterrupted, even if one node fails.
The system uses a priority-based bus schedule, where messages with higher priority are sent first.
Each message is sent with an identifier, which dictates its priority and ensures that the appropriate devices receive it.
This identifier serves as a core component in the arbitration process, which minimizes data collisions and ensures seamless data transmission.
Key Features of CAN Protocol
The CAN protocol boasts several unique features that make it a preferred choice for communication systems around the globe.
- Real-Time Communication: The protocol supports real-time data exchange, making it ideal for applications requiring timely and synchronized responses.
- Error Detection Mechanisms: CAN is designed with a robust error-checking system that can detect and locate errors automatically, protecting the integrity of transmitted data.
- Bandwidth Efficiency: The protocol is known for its efficient use of bandwidth, enabling high-speed communication even with a large number of connected nodes.
- Fault Tolerance: With its ability to isolate faulty nodes, CAN ensures that a single point of failure does not affect the entire network.
These attributes are why CAN protocol has been widely adopted outside automotive industries, including medical equipment, industrial machinery, and consumer electronics.
Control Mechanisms in CAN Protocol
Bus Arbitration
Bus arbitration is a fundamental control mechanism in CAN protocol.
When multiple devices attempt to send messages simultaneously, the protocol uses bit-wise arbitration based on priority.
Using this method allows higher-priority messages to proceed first, while lower-priority messages are paused momentarily.
This system ensures timely data transmission and reduces the chance of collisions.
Error Management
Error management is critical for maintaining data integrity in a CAN network.
The protocol includes several layers of error detection, such as:
– Bit Monitoring: Devices listen to their own messages to ensure proper transmission.
– Cyclic Redundancy Check (CRC): A special verification field that checks message validity.
– Acknowledge Slot: Receivers send an acknowledgment back to the transmitter once a message is received correctly.
These mechanisms combined provide an efficient way to handle errors without disrupting the entire network.
Message Framing
In the CAN protocol, each message follows a specific frame structure.
The message frame includes:
– Start of Frame (SOF)
– Arbitration field
– Control field
– Data field(s)
– CRC field
– ACK field
– End of Frame (EOF)
This standardized structure ensures consistency and ease in decoding messages, making it easier for devices to communicate effectively across the network.
Applications of CAN Protocol in Latest Technology
Automotive Industry
The automotive industry remains the primary domain where CAN protocol operates extensively.
It’s used in engine management, antilock braking systems, and even in-car entertainment systems to ensure stable communication among various components.
By providing a common communication platform, CAN protocol has significantly contributed to the advancement of modern vehicle technology.
Industrial Automation
Aside from automotive applications, many industrial automation systems rely on CAN for efficient machinery operations.
This protocol aids in coordinating machinery remotely, reducing manpower, and improving safety in factories and warehouses.
It is instrumental in operating complex machinery, robotic arms, and conveyor systems.
Medical Equipment
The medical field also benefits vastly from the CAN protocol.
In infusion pumps, patient monitoring systems, and imaging devices, CAN allows different parts of medical equipment to work together seamlessly, ensuring timely and accurate medical procedures.
The protocol’s reliability and error-checking features make it ideal for sensitive medical equipment where precision is critical.
Consumer Electronics
Even everyday consumer electronics like smart home devices and some appliances use the CAN protocol.
In smart home systems, CAN helps different devices communicate and work in harmony, providing a connected and seamless user experience.
The Future of CAN Protocol
The continuous evolution of technology presents both opportunities and challenges for the CAN protocol.
Advancements in CAN FD (Flexible Data-rate) are pushing the boundaries of data speed and message length, making CAN suitable for future applications requiring more data throughput.
CAN’s role will likely expand beyond traditional industries to integrate more profoundly within the broader landscape of IoT applications.
Its ability to offer reliable, real-time communication makes it well-suited for modern technology demands.
With increasing demand for efficient, error-resistant communication systems, the application of CAN protocol is bound to grow, solidifying its status as a vital component of the technology ecosystem.
In conclusion, understanding the CAN protocol basics, control mechanisms, and applications is essential for appreciating its value in current and future technology trends.
This versatile communication protocol promises to remain a key player in enabling sophisticated, interconnected systems worldwide.
資料ダウンロード
QCD管理受発注クラウド「newji」は、受発注部門で必要なQCD管理全てを備えた、現場特化型兼クラウド型の今世紀最高の受発注管理システムとなります。
ユーザー登録
受発注業務の効率化だけでなく、システムを導入することで、コスト削減や製品・資材のステータス可視化のほか、属人化していた受発注情報の共有化による内部不正防止や統制にも役立ちます。
NEWJI DX
製造業に特化したデジタルトランスフォーメーション(DX)の実現を目指す請負開発型のコンサルティングサービスです。AI、iPaaS、および先端の技術を駆使して、製造プロセスの効率化、業務効率化、チームワーク強化、コスト削減、品質向上を実現します。このサービスは、製造業の課題を深く理解し、それに対する最適なデジタルソリューションを提供することで、企業が持続的な成長とイノベーションを達成できるようサポートします。
製造業ニュース解説
製造業、主に購買・調達部門にお勤めの方々に向けた情報を配信しております。
新任の方やベテランの方、管理職を対象とした幅広いコンテンツをご用意しております。
お問い合わせ
コストダウンが利益に直結する術だと理解していても、なかなか前に進めることができない状況。そんな時は、newjiのコストダウン自動化機能で大きく利益貢献しよう!
(β版非公開)