- お役立ち記事
- Case Studies and Benefits of Applying Quality Function Deployment (QFD) in Manufacturing
月間76,176名の
製造業ご担当者様が閲覧しています*
*2025年3月31日現在のGoogle Analyticsのデータより
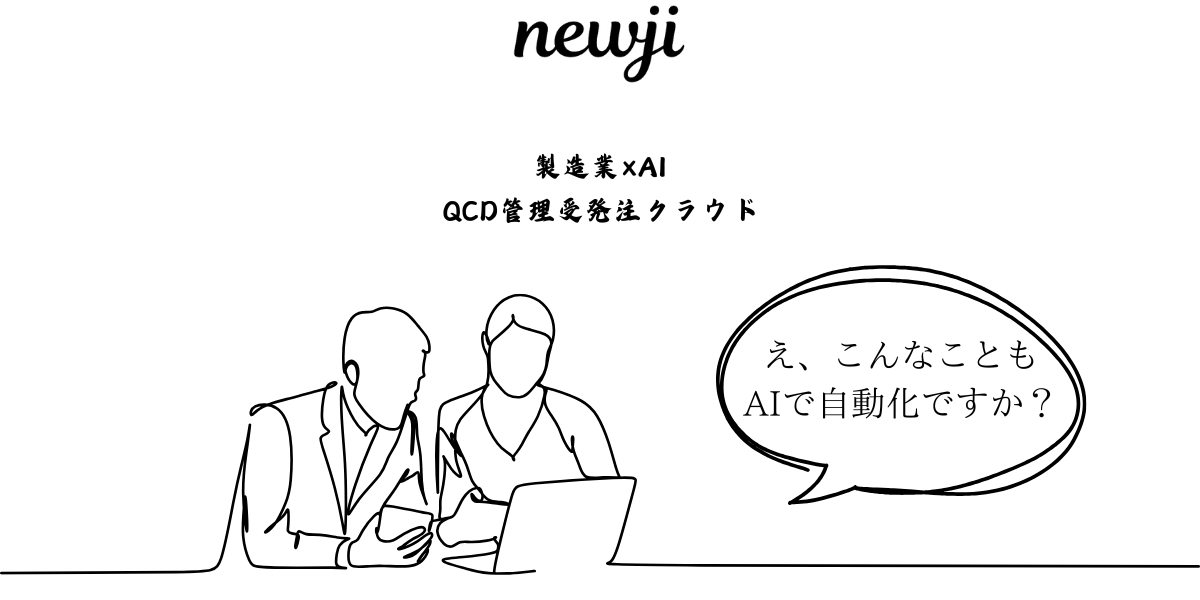
Case Studies and Benefits of Applying Quality Function Deployment (QFD) in Manufacturing
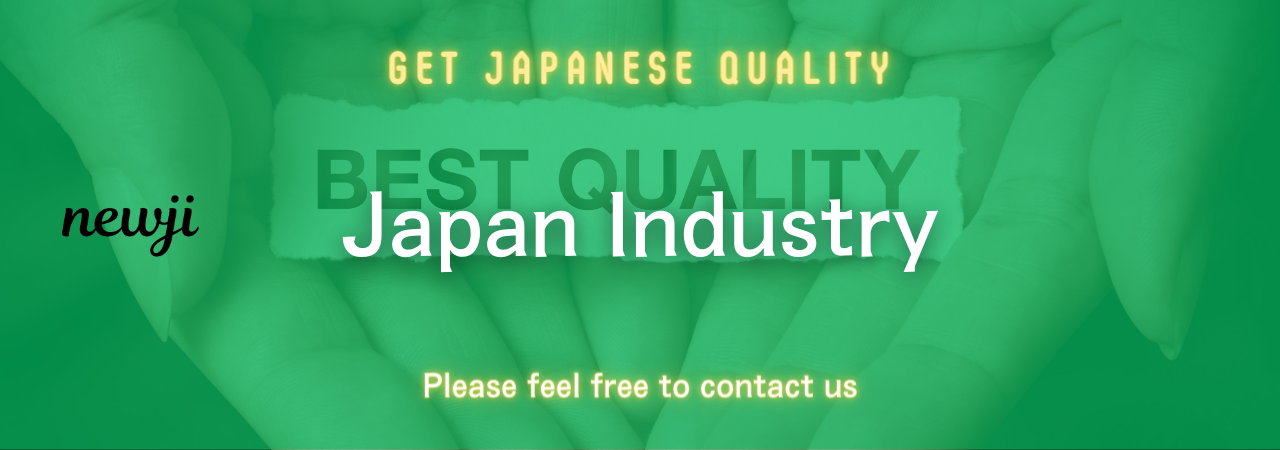
目次
Introduction to Quality Function Deployment (QFD)
Quality Function Deployment (QFD) is a structured methodology used to transform customer requirements into specific company requirements at each stage, from research and product development to engineering and manufacturing.
This approach ensures the final product aligns closely with customer needs and expectations.
For manufacturers, QFD can be a game-changer, improving product quality and customer satisfaction while reducing costs and time to market.
The Foundation of QFD
Understanding Customer Requirements
The first step in QFD involves gathering and understanding customer requirements.
This includes identifying what customers need and want from the product.
Customer feedback, surveys, and focus groups are common methods used to gather this information.
House of Quality
The House of Quality is a key tool in QFD.
It’s a visual representation of how customer requirements translate into company requirements.
This matrix helps teams focus on critical product features and align them with customer needs.
Case Study: Automotive Industry
Improving Car Interiors
A well-known car manufacturer used QFD to redesign its car interiors.
Customer feedback revealed a demand for more comfortable and intuitive interiors.
By applying QFD, the manufacturer identified specific areas for improvement, such as seat ergonomics and dashboard layout.
The result was a car interior that received high praise from both customers and critics.
Enhancing Fuel Efficiency
Another case involved improving the fuel efficiency of a new car model.
Using QFD, the manufacturer was able to prioritize features that contributed most to fuel efficiency.
This led to a redesigned engine and aerodynamics, resulting in a significant increase in miles per gallon.
Case Study: Electronics Manufacturing
Developing a New Smartphone
An electronics company used QFD to develop a new smartphone.
Customer needs like battery life, camera quality, and user interface were translated into technical specifications through the House of Quality.
The final product was a commercial success, meeting customer expectations and performing well in the market.
Reducing Product Defects
In another case, a manufacturer aimed to reduce defects in its electronic components.
By applying QFD, the company identified critical areas needing improvement in the production process.
The changes led to a significant reduction in product defects, enhancing overall product quality.
Case Study: Consumer Goods
Optimizing a Kitchen Appliance
A major consumer goods company used QFD to upgrade a popular kitchen appliance.
Customer feedback indicated a need for improved usability and energy efficiency.
By focusing on these areas, the company successfully launched an enhanced product that was well received by customers.
Improving Packaging Design
Another consumer goods company applied QFD to improve the packaging of its products.
This included making it more user-friendly and environmentally sustainable.
The redesigned packaging not only satisfied customer requirements but also contributed to the company’s sustainability goals.
Benefits of Applying QFD in Manufacturing
Enhanced Customer Satisfaction
One of the primary benefits of QFD is enhanced customer satisfaction.
By focusing on what customers really want, manufacturers can create products that meet or exceed expectations.
This often leads to higher customer loyalty and repeat business.
Improved Communication and Collaboration
QFD fosters better communication and collaboration across different departments within a company.
Everyone from marketing to engineering works together with a clear understanding of customer needs and project goals.
This reduces misunderstandings and ensures everyone is on the same page.
Reduced Development Time and Costs
By identifying critical features early in the development process, QFD helps to streamline workflows and eliminate unnecessary steps.
This can lead to significant reductions in both development time and costs, getting products to market faster and more efficiently.
Quality Improvement
QFD places a strong emphasis on quality from the start.
By consistently addressing quality throughout the development process, manufacturers can reduce defects and enhance overall product performance.
Implementing QFD in Your Manufacturing Process
Gathering Customer Requirements
The first step is to gather detailed customer requirements.
Use surveys, interviews, and focus groups to understand what your customers need and want from your product.
Building the House of Quality
Next, translate these requirements into specific product features using the House of Quality.
Involve cross-functional teams to ensure all aspects of the product are considered.
Continuous Feedback and Improvement
QFD is not a one-time process.
Continuously gather feedback and make improvements based on that feedback.
This ensures that your product remains aligned with customer needs.
Conclusion
Quality Function Deployment (QFD) is a powerful tool for manufacturers seeking to improve product quality, enhance customer satisfaction, and reduce costs.
By systematically converting customer needs into actionable specifications, QFD ensures that every stage of product development is aligned with what the customer wants.
Practical examples in the automotive, electronics, and consumer goods industries demonstrate the real-world benefits of QFD.
Implementing QFD in your manufacturing process can lead to significant improvements, making it an indispensable approach in today’s competitive market.
資料ダウンロード
QCD管理受発注クラウド「newji」は、受発注部門で必要なQCD管理全てを備えた、現場特化型兼クラウド型の今世紀最高の受発注管理システムとなります。
ユーザー登録
受発注業務の効率化だけでなく、システムを導入することで、コスト削減や製品・資材のステータス可視化のほか、属人化していた受発注情報の共有化による内部不正防止や統制にも役立ちます。
NEWJI DX
製造業に特化したデジタルトランスフォーメーション(DX)の実現を目指す請負開発型のコンサルティングサービスです。AI、iPaaS、および先端の技術を駆使して、製造プロセスの効率化、業務効率化、チームワーク強化、コスト削減、品質向上を実現します。このサービスは、製造業の課題を深く理解し、それに対する最適なデジタルソリューションを提供することで、企業が持続的な成長とイノベーションを達成できるようサポートします。
製造業ニュース解説
製造業、主に購買・調達部門にお勤めの方々に向けた情報を配信しております。
新任の方やベテランの方、管理職を対象とした幅広いコンテンツをご用意しております。
お問い合わせ
コストダウンが利益に直結する術だと理解していても、なかなか前に進めることができない状況。そんな時は、newjiのコストダウン自動化機能で大きく利益貢献しよう!
(β版非公開)