- お役立ち記事
- Case Studies and Effects of Utilizing the Seven QC Tools in Manufacturing Quality Management
Case Studies and Effects of Utilizing the Seven QC Tools in Manufacturing Quality Management
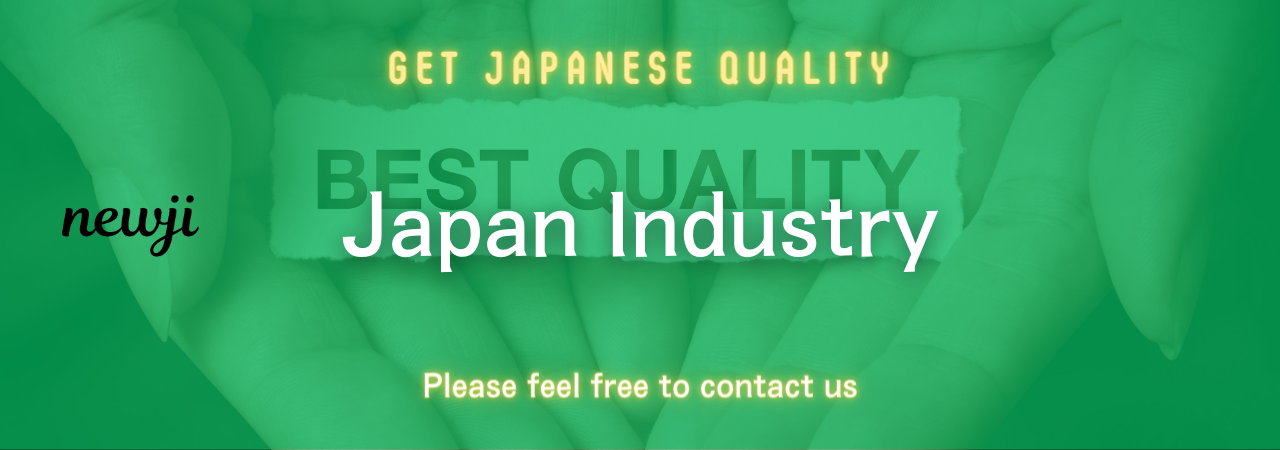
目次
Introduction to the Seven QC Tools
Quality control (QC) is essential in manufacturing to ensure products meet the desired standards.
By using various Quality Control tools, manufacturers can systematically address quality issues and improve processes.
Among these tools, the Seven QC Tools are particularly effective and widely recognized.
These tools are simple yet powerful techniques that help in problem-solving and quality improvement.
The Seven QC Tools Explained
Before diving into case studies, it’s vital to understand what each of the Seven QC Tools entails.
Pareto Chart
A Pareto Chart is a bar chart that prioritizes issues so that the most significant problems get tackled first.
Often referred to as the 80-20 rule, it suggests that 80% of problems can be attributed to 20% of causes.
Cause-and-Effect Diagram
Also known as the Fishbone or Ishikawa Diagram, this tool helps identify the root causes of a problem.
It breaks down the problem into its contributing factors, making it easier to pinpoint what needs to be addressed.
Control Chart
Control Charts are used to study how processes change over time.
They help in identifying trends, enabling manufacturers to maintain process control and ensure quality consistency.
Histogram
A Histogram is a bar graph that shows the frequency distribution of data points.
It helps in understanding the spread and central tendency of a dataset, critical for process improvements.
Check Sheet
A Check Sheet is a structured form for collecting and analyzing data.
It provides a simple way to capture data in real-time, facilitating more accurate and consistent record-keeping.
Scatter Diagram
Scatter Diagrams display the relationship between two variables.
They help in identifying correlations, which can be crucial for solving quality problems.
Flowchart
Flowcharts visualize a process from start to finish, making it easy to understand each step.
They are particularly useful for process documentation and identifying bottlenecks.
Case Studies in Utilizing the Seven QC Tools
Let’s explore real-world examples to understand how these tools have been effectively used in manufacturing quality management.
Case Study 1: Improving Assembly Line Efficiency with Pareto Charts
A leading automobile manufacturer faced frequent defects in its assembly line, leading to higher costs and customer complaints.
By using Pareto Charts, the quality team identified that 70% of the defects were caused by just three issues.
Addressing these primary issues resulted in a 40% improvement in assembly line efficiency and a substantial reduction in customer complaints.
Case Study 2: Root Cause Analysis with Fishbone Diagram in Electronics Manufacturing
An electronics manufacturer was troubled by inconsistent quality in its final products.
The team used a Fishbone Diagram to dissect the problem into smaller, manageable sections—material, machinery, manpower, and methods.
This method helped identify that a poorly calibrated soldering machine was the root cause.
After recalibrating the machine, the defect rate dropped by 25%.
Case Study 3: Monitoring Process Stability with Control Charts in Food Processing
A food processing company needed to maintain stable temperature conditions to ensure product quality.
By implementing Control Charts, the operators could monitor the temperature consistently and spot any deviations immediately.
This practice enabled the company to reduce spoilage by 15%, ensuring a higher rate of product consistency.
Case Study 4: Using Histograms to Analyze Production Waste in Textile Manufacturing
A textile manufacturer faced issues with production waste, which was impacting profitability.
Using Histograms, the quality team analyzed the waste data to identify the types of defects contributing to the highest waste.
This analysis helped refine the production process, reducing waste by 20%.
Case Study 5: Streamlining Data Collection with Check Sheets in Pharmaceutical Manufacturing
In pharmaceutical manufacturing, accurate data collection is crucial for compliance and quality assurance.
A Check Sheet was introduced to capture data on the frequency of defects during various stages of production.
This structured data collection method helped in quickly identifying problem areas, leading to a 30% improvement in defect detection and resolution.
Case Study 6: Identifying Relationships with Scatter Diagrams in Metal Fabrication
A metal fabrication company wanted to understand the relationship between machine settings and final product quality.
Using Scatter Diagrams, the company identified that minor changes in machine speed had a significant impact on quality.
Adjusting the machine settings accordingly, they saw a 10% improvement in product quality.
Case Study 7: Process Documentation with Flowcharts in Chemical Manufacturing
A chemical manufacturer needed to document its processes for training and compliance purposes.
Flowcharts were created to visualize each step of the manufacturing process.
This documentation made training new employees quicker and more effective, reducing onboarding time by 15%.
The Impact of the Seven QC Tools on Quality Management
The success stories from various industries showcase the profound impact of the Seven QC Tools on manufacturing quality management.
From improving efficiency and reducing defects to enhancing process documentation, these tools are invaluable assets for any quality management program.
By employing these straightforward yet effective techniques, manufacturers can achieve higher quality, reduce costs, and increase customer satisfaction.
Conclusion: The Future of Quality Control in Manufacturing
The Seven QC Tools continue to be essential resources in manufacturing quality management.
Their simplicity and effectiveness make them accessible and beneficial for any manufacturing operation.
As industries evolve, these tools will remain cornerstones for quality improvement, adapting to new challenges and technologies.
Manufacturers who leverage these tools will undoubtedly find themselves at a competitive advantage, ensuring their products meet and exceed quality standards.
資料ダウンロード
QCD調達購買管理クラウド「newji」は、調達購買部門で必要なQCD管理全てを備えた、現場特化型兼クラウド型の今世紀最高の購買管理システムとなります。
ユーザー登録
調達購買業務の効率化だけでなく、システムを導入することで、コスト削減や製品・資材のステータス可視化のほか、属人化していた購買情報の共有化による内部不正防止や統制にも役立ちます。
NEWJI DX
製造業に特化したデジタルトランスフォーメーション(DX)の実現を目指す請負開発型のコンサルティングサービスです。AI、iPaaS、および先端の技術を駆使して、製造プロセスの効率化、業務効率化、チームワーク強化、コスト削減、品質向上を実現します。このサービスは、製造業の課題を深く理解し、それに対する最適なデジタルソリューションを提供することで、企業が持続的な成長とイノベーションを達成できるようサポートします。
オンライン講座
製造業、主に購買・調達部門にお勤めの方々に向けた情報を配信しております。
新任の方やベテランの方、管理職を対象とした幅広いコンテンツをご用意しております。
お問い合わせ
コストダウンが利益に直結する術だと理解していても、なかなか前に進めることができない状況。そんな時は、newjiのコストダウン自動化機能で大きく利益貢献しよう!
(Β版非公開)