- お役立ち記事
- Case Studies of FDM Technology Implementation in SMEs and Success Factors
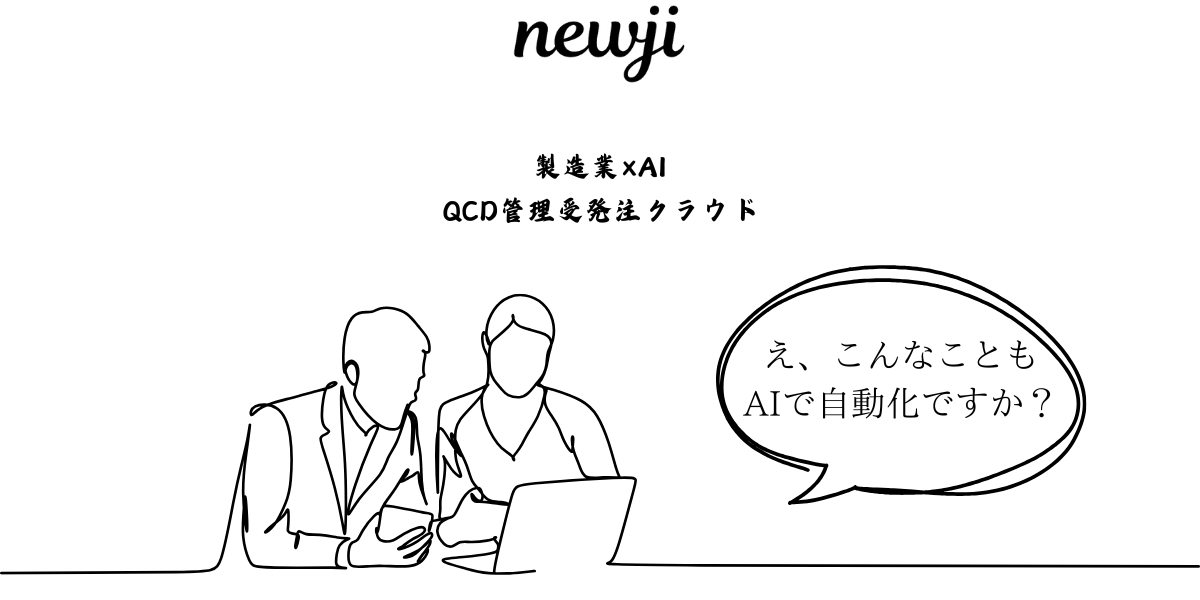
Case Studies of FDM Technology Implementation in SMEs and Success Factors
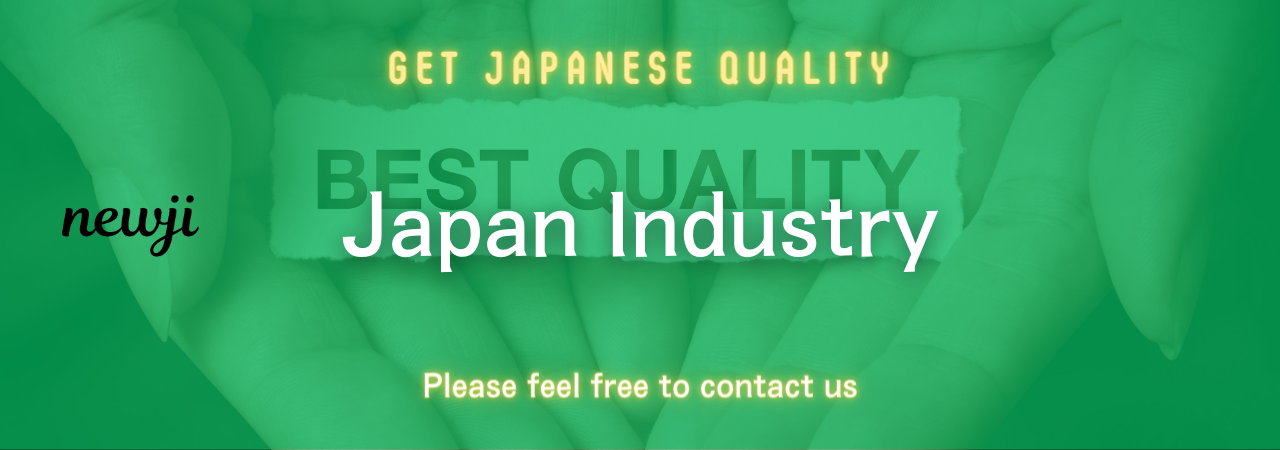
目次
Introduction to FDM Technology in SMEs
Fused Deposition Modeling (FDM) is a 3D printing technology that has gained significant traction across various industries, especially in Small and Medium-sized Enterprises (SMEs).
Its affordability, versatility, and ease of use make it an appealing option for businesses looking to innovate their product development processes.
For SMEs, the integration of FDM technology can lead to reduced production costs, faster prototyping, and greater customization capabilities.
This article explores the successful implementation of FDM technology in SMEs, highlighting key case studies and identifying critical success factors for effective adoption.
Understanding FDM Technology
FDM technology operates by using a thermoplastic filament, which is heated to a semi-liquid state and then extruded layer by layer to form a three-dimensional object.
This additive manufacturing process allows for the creation of complex geometric shapes that would be difficult or impossible to achieve through traditional manufacturing methods.
The primary materials used in FDM include ABS, PLA, and other thermoplastics, which are selected based on the desired properties of the finished product.
Benefits of FDM for SMEs
One of the key advantages of FDM technology is cost reduction.
By using fewer materials and reducing the need for complex tooling, SMEs can significantly cut down on overhead expenses.
Additionally, FDM technology allows for rapid prototyping, enabling businesses to quickly test and iterate on new designs before committing to full-scale production.
This agility can lead to improved innovation and a competitive edge in the market.
Case Study 1: A Small Furniture Manufacturer
A small furniture manufacturer implemented FDM technology to enhance its product development process.
Before adopting FDM, this company faced challenges in creating prototypes, as traditional methods were time-consuming and expensive.
By integrating FDM, the manufacturer was able to produce affordable prototypes in-house, allowing for quicker design iterations and more innovative furniture designs.
This transition not only reduced costs but also improved customer satisfaction by offering tailored solutions faster.
Case Study 2: A Local Tech Startup
A local technology startup utilized FDM technology to create custom components for its electronic devices.
Faced with high initial manufacturing costs, the company decided to employ FDM for prototyping and low-volume production runs.
This approach enabled the startup to refine its products rapidly and reduce time-to-market significantly.
As a result, the company was able to allocate resources more efficiently and focus on core business development activities.
Case Study 3: A Custom Jewelry Designer
In the world of custom jewelry, design precision and customization are paramount.
A custom jewelry designer integrated FDM technology into its creative process to produce intricate and personalized pieces.
By leveraging FDM, the designer could create detailed prototypes and bring bespoke designs to life, satisfying customer demands for uniqueness at a lower cost.
The switch to FDM not only streamlined the production process but also broadened the range of creative possibilities available to the designer.
Success Factors for Implementing FDM in SMEs
Understanding the Specific Needs
Before implementing FDM technology, it’s crucial for SMEs to assess their specific needs and the potential impact on their operations.
Understanding the particular challenges and goals of the business will help determine the most appropriate use case for FDM and guide the selection of suitable materials and equipment.
Investing in Training and Support
Training employees on how to effectively use FDM technology is a vital component of successful adoption.
SMEs should invest in training programs and provide ongoing support to ensure that the staff is well-versed in the operation, maintenance, and troubleshooting of FDM equipment.
This knowledge will maximize the technology’s potential benefits and minimize downtime.
Developing a Strategic Plan
A strategic plan for FDM implementation is essential for aligning technology use with the broader objectives of the business.
This plan should outline clear goals, budget considerations, timelines, and performance metrics.
By establishing a roadmap, SMEs can measure progress, make informed decisions, and adapt as needed to optimize the use of FDM technology.
Fostering a Culture of Innovation
Embracing a culture of innovation is key to maximizing the benefits of FDM technology.
Encouraging creativity, experimentation, and continuous improvement among employees will drive the successful integration of FDM into the company’s operations.
Such a culture enables SMEs to fully explore new opportunities and remain competitive in a rapidly evolving marketplace.
Conclusion
FDM technology offers compelling advantages for SMEs looking to innovate and enhance their operational efficiencies.
Through successful case studies, we can see how SMEs across different industries have leveraged FDM to improve agility, reduce costs, and increase customization.
By understanding key success factors such as assessing specific needs, investing in training, developing a strategic plan, and fostering an innovative culture, SMEs can unlock the transformative potential of FDM technology.
As the technology continues to advance, its role in reshaping SME manufacturing landscapes will only grow, paving the way for more innovation and improved business outcomes.
資料ダウンロード
QCD調達購買管理クラウド「newji」は、調達購買部門で必要なQCD管理全てを備えた、現場特化型兼クラウド型の今世紀最高の購買管理システムとなります。
ユーザー登録
調達購買業務の効率化だけでなく、システムを導入することで、コスト削減や製品・資材のステータス可視化のほか、属人化していた購買情報の共有化による内部不正防止や統制にも役立ちます。
NEWJI DX
製造業に特化したデジタルトランスフォーメーション(DX)の実現を目指す請負開発型のコンサルティングサービスです。AI、iPaaS、および先端の技術を駆使して、製造プロセスの効率化、業務効率化、チームワーク強化、コスト削減、品質向上を実現します。このサービスは、製造業の課題を深く理解し、それに対する最適なデジタルソリューションを提供することで、企業が持続的な成長とイノベーションを達成できるようサポートします。
オンライン講座
製造業、主に購買・調達部門にお勤めの方々に向けた情報を配信しております。
新任の方やベテランの方、管理職を対象とした幅広いコンテンツをご用意しております。
お問い合わせ
コストダウンが利益に直結する術だと理解していても、なかなか前に進めることができない状況。そんな時は、newjiのコストダウン自動化機能で大きく利益貢献しよう!
(Β版非公開)