- お役立ち記事
- Case Studies of Process Efficiency Through Cooling Time Adjustment
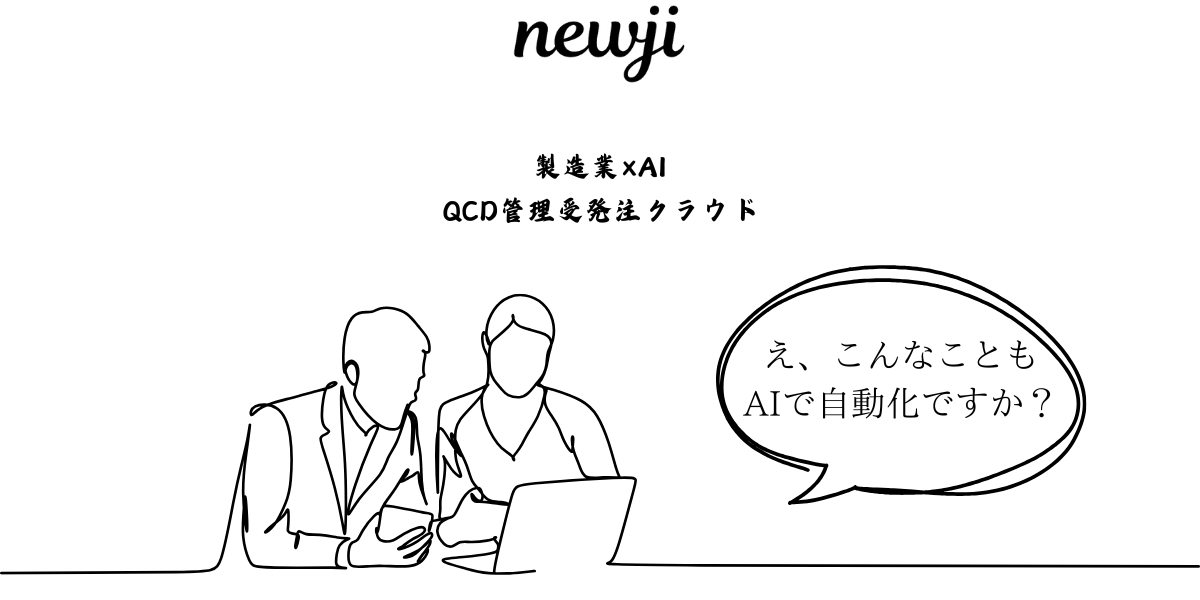
Case Studies of Process Efficiency Through Cooling Time Adjustment
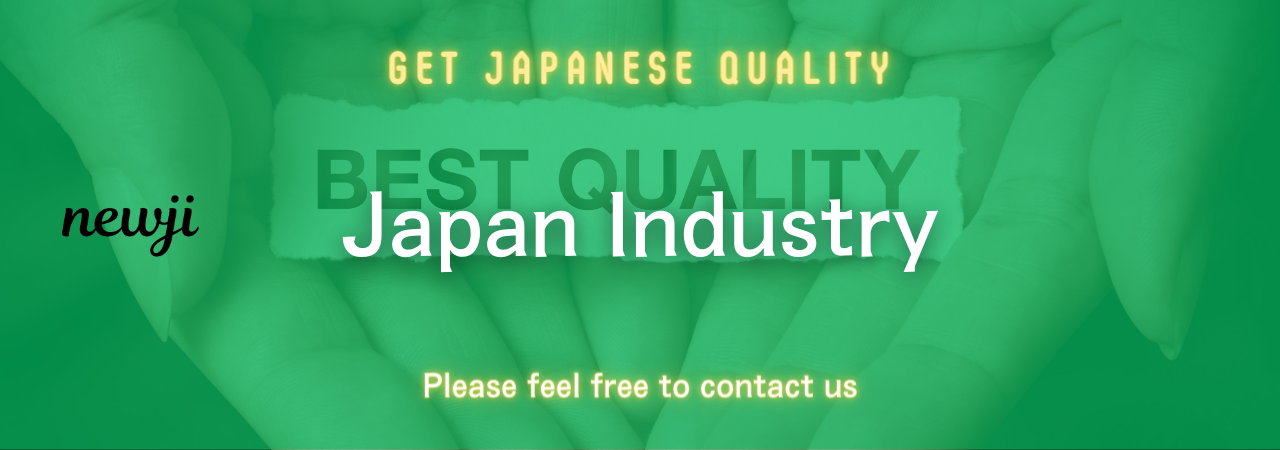
目次
Understanding Process Efficiency
Process efficiency is a critical aspect of operational excellence in any industry.
It refers to the ability of a process to produce the desired output as efficiently and effectively as possible with minimal waste.
In manufacturing, for instance, process efficiency can greatly affect production costs, product quality, and overall profitability.
One important factor that can influence process efficiency is the cooling time of a product or component.
The Importance of Cooling Time
Cooling time is the period required for a product or material to cool down to a specified temperature before moving on to the next stage of production.
In various industries such as plastic molding, metal casting, and food processing, cooling time can significantly impact the rate of production and the quality of output.
Adjusting cooling time can lead to notable improvements in process efficiency, which is why it is crucial for businesses to optimize this aspect of their production process.
Effects of Improper Cooling Time
An incorrect cooling time can result in defects such as warping, cracking, or incomplete setting, which ultimately leads to product wastage.
It can also prolong the production cycle, increase energy consumption, and reduce the overall throughput of a manufacturing line.
Conversely, proper adjustment of cooling time can enhance product consistency, increase production speed, and decrease operational costs.
Case Studies: Successful Adjustments in Cooling Time
Let’s explore a few case studies where companies have improved their process efficiency by making thoughtful adjustments to cooling times.
Case Study 1: Plastic Molding Company
A plastic molding company experienced frequent product defects, particularly warping, which led to high scrap rates and customer dissatisfaction.
Through careful analysis and experimentation, the company’s engineering team discovered that reducing the cooling time by 10% resulted in better product integrity.
By implementing this change, the company reduced its reject rate by 20% and increased its production rate, resulting in significant cost savings and enhanced customer satisfaction.
Case Study 2: Metal Casting Manufacturer
A metal casting manufacturer faced high energy costs due to excessive cooling times in its production process.
By conducting an energy audit and studying the cooling times, the company realized that optimizing the cooling time could lead to significant energy savings.
By adjusting the cooling time by 15% without compromising the quality of the metal castings, the manufacturer saved 10% on energy costs and increased the throughput of its production line by 5%.
Case Study 3: Food Processing Plant
A large food processing company producing frozen meals faced issues with inconsistent cooking quality due to varying cooling times in its production process.
This inconsistency often led to uneven textures and flavors, resulting in customer complaints.
After conducting a thorough analysis, the company adjusted its cooling times based on the type and size of the meal portions.
This adjustment led to consistently high-quality products and a 12% increase in production efficiency due to reduced cooling phase variability.
Steps to Optimize Cooling Time
For businesses looking to optimize their cooling times and improve process efficiency, the following steps can be beneficial:
Step 1: Conduct a Comprehensive Analysis
Begin by conducting a detailed analysis of your current production processes.
This includes identifying the average cooling times and pinpointing areas where adjustments can lead to improved efficiencies.
Collect data related to product quality, energy consumption, and production rates.
Step 2: Experiment and Test
It’s crucial to conduct experiments and tests by adjusting the cooling times in controlled environments.
During this phase, closely monitor any changes in product quality, energy usage, production rates, and overall efficiency.
The data obtained from these tests will provide valuable insights for optimizing cooling times.
Step 3: Incorporate Technological Solutions
Consider integrating advanced technologies such as temperature sensors, automated control systems, and simulation software to enhance monitoring and control of cooling times.
These technologies can help ensure precision and consistency in maintaining optimal cooling durations.
Step 4: Train and Educate Your Team
Ensure that your production team is well-trained and informed about the importance of cooling time adjustments.
Provide them with the necessary resources and training to successfully implement and manage these changes.
Step 5: Monitor and Adjust Continuously
Process optimization is an ongoing effort.
Continuously monitor the results of cooling time adjustments and be prepared to make further changes as needed.
Regular reviews and continuous improvement are key components of maintaining high process efficiency.
Conclusion
Cooling time adjustments can have a profound impact on the process efficiency of a business.
As seen in the case studies, companies that successfully optimize cooling times can see significant improvements in product quality, production speed, and cost savings.
By following the outlined steps and committing to a continuous improvement mindset, businesses can ensure they remain competitive and efficient in their respective industries.
資料ダウンロード
QCD調達購買管理クラウド「newji」は、調達購買部門で必要なQCD管理全てを備えた、現場特化型兼クラウド型の今世紀最高の購買管理システムとなります。
ユーザー登録
調達購買業務の効率化だけでなく、システムを導入することで、コスト削減や製品・資材のステータス可視化のほか、属人化していた購買情報の共有化による内部不正防止や統制にも役立ちます。
NEWJI DX
製造業に特化したデジタルトランスフォーメーション(DX)の実現を目指す請負開発型のコンサルティングサービスです。AI、iPaaS、および先端の技術を駆使して、製造プロセスの効率化、業務効率化、チームワーク強化、コスト削減、品質向上を実現します。このサービスは、製造業の課題を深く理解し、それに対する最適なデジタルソリューションを提供することで、企業が持続的な成長とイノベーションを達成できるようサポートします。
オンライン講座
製造業、主に購買・調達部門にお勤めの方々に向けた情報を配信しております。
新任の方やベテランの方、管理職を対象とした幅広いコンテンツをご用意しております。
お問い合わせ
コストダウンが利益に直結する術だと理解していても、なかなか前に進めることができない状況。そんな時は、newjiのコストダウン自動化機能で大きく利益貢献しよう!
(Β版非公開)