- お役立ち記事
- Case Studies of Quality Assurance Initiatives Contributing to Quality Cost Reduction in Manufacturing
この記事は、当社の提供するお役立ち記事の一部です。詳しくは公式サイトをご覧ください。
Case Studies of Quality Assurance Initiatives Contributing to Quality Cost Reduction in Manufacturing
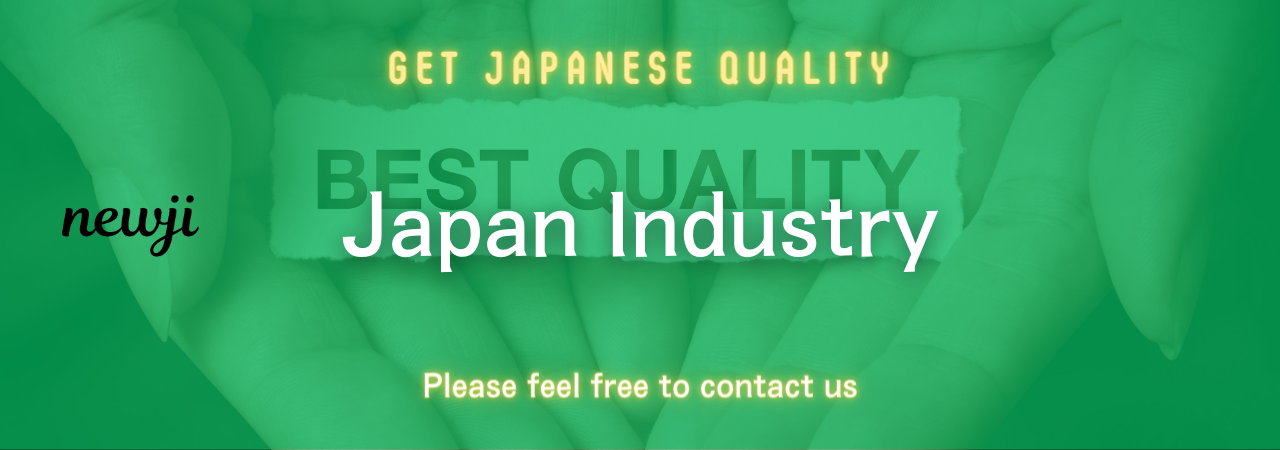
Quality assurance plays a crucial role in various industries, particularly in manufacturing. Effective quality assurance initiatives can lead to substantial cost reductions by minimizing defects, improving product reliability, and streamlining processes. This article delves into case studies of quality assurance initiatives that have substantially cut down quality costs in manufacturing.
目次
Understanding Quality Assurance in Manufacturing
Quality assurance is a systematic process used to determine if a product or service meets specified requirements. In manufacturing, it involves planning and overseeing production processes to ensure quality standards are upheld. Effective quality assurance helps prevent defects, reduces waste, and ensures customer satisfaction.
Importance of Quality Assurance in Cost Reduction
Quality assurance is pivotal in cost reduction as it helps to identify defects early in the production process. By preventing defective products from reaching the market, manufacturers save on rework, returns, and warranty claims. Additionally, maintaining high-quality standards enhances customer trust and brand reputation, which can lead to increased sales and profitability.
Case Study 1: Implementing Total Quality Management (TQM)
One notable example of a successful quality assurance initiative is the implementation of Total Quality Management (TQM) by a leading automotive manufacturer. TQM is an organization-wide approach focused on continuous improvement and customer satisfaction.
Reducing Defects with TQM
The automotive manufacturer adopted TQM principles by fostering a culture of quality throughout the organization. This included training employees at all levels on quality management techniques and establishing cross-functional teams to identify and solve quality-related issues.
As a result, the company significantly reduced the number of defects in their vehicles. Early detection of issues and preventive measures decreased the need for costly repairs and recalls. The implementation of TQM led to a 20% reduction in manufacturing costs over three years.
Case Study 2: Lean Manufacturing and Six Sigma Integration
Another company, a consumer electronics manufacturer, effectively reduced quality costs through the integration of Lean Manufacturing and Six Sigma methodologies. Lean Manufacturing focuses on eliminating waste, while Six Sigma aims to reduce process variation and enhance product quality.
Streamlining Processes with Lean Manufacturing
The manufacturer identified areas in their production line where waste was prevalent. By applying Lean principles, they streamlined their assembly process, reduced inventory levels, and improved production flow. This initiative led to a 15% reduction in production costs.
Enhancing Product Quality with Six Sigma
To complement Lean Manufacturing, the company adopted Six Sigma techniques to reduce defects and improve product quality. They used data-driven approaches to identify root causes of defects and implemented corrective actions. This resulted in a 25% reduction in defect rates and a notable improvement in customer satisfaction.
Case Study 3: Implementing Statistical Process Control (SPC)
A major pharmaceutical company successfully reduced quality costs by implementing Statistical Process Control (SPC). SPC involves using statistical methods to monitor and control production processes.
Improving Process Consistency with SPC
The pharmaceutical company integrated SPC tools to monitor their production process. This allowed them to detect deviations from quality standards in real-time and make necessary adjustments promptly.
By improving process control and reducing variability, the company achieved consistent product quality. This initiative led to a 30% reduction in quality-related costs, including lessened downtime and fewer product recalls.
Case Study 4: Adopting Automated Quality Inspection Systems
An aerospace manufacturer reduced quality costs by adopting automated quality inspection systems. These systems use advanced technologies such as machine vision and artificial intelligence to inspect products for defects.
Enhancing Inspection Accuracy with Automation
The aerospace manufacturer implemented automated inspection systems at various stages of their production line. These systems quickly and accurately identified defects that human inspectors might miss, ensuring only high-quality products reached customers.
As a result, the company saw a dramatic reduction in defects and an increase in inspection efficiency. The adoption of automated quality inspection systems led to a 35% reduction in quality assurance costs over two years.
Case Study 5: Continuous Improvement Programs
A leading household appliance manufacturer achieved significant cost savings through continuous improvement programs. These programs involve ongoing efforts to enhance products, services, and processes.
Fostering a Culture of Continuous Improvement
The manufacturer encouraged employees to participate in continuous improvement initiatives by suggesting ideas for quality enhancement. They established a reward system to recognize and implement feasible suggestions.
This culture of continuous improvement resulted in numerous small changes that collectively had a significant impact. The manufacturer reduced defect rates by 40%, leading to substantial cost savings in quality assurance.
Conclusion
Quality assurance initiatives play a vital role in reducing quality costs in manufacturing. The above case studies demonstrate the effectiveness of various approaches such as Total Quality Management, Lean Manufacturing, Six Sigma, Statistical Process Control, automated inspection systems, and continuous improvement programs. By implementing these initiatives, manufacturers can significantly enhance product quality, reduce defects, and achieve substantial cost savings.
These examples underscore the importance of adopting robust quality assurance practices in manufacturing environments. Ultimately, a commitment to quality not only fosters customer satisfaction but also leads to a more profitable and efficient operation.
資料ダウンロード
QCD調達購買管理クラウド「newji」は、調達購買部門で必要なQCD管理全てを備えた、現場特化型兼クラウド型の今世紀最高の購買管理システムとなります。
ユーザー登録
調達購買業務の効率化だけでなく、システムを導入することで、コスト削減や製品・資材のステータス可視化のほか、属人化していた購買情報の共有化による内部不正防止や統制にも役立ちます。
NEWJI DX
製造業に特化したデジタルトランスフォーメーション(DX)の実現を目指す請負開発型のコンサルティングサービスです。AI、iPaaS、および先端の技術を駆使して、製造プロセスの効率化、業務効率化、チームワーク強化、コスト削減、品質向上を実現します。このサービスは、製造業の課題を深く理解し、それに対する最適なデジタルソリューションを提供することで、企業が持続的な成長とイノベーションを達成できるようサポートします。
オンライン講座
製造業、主に購買・調達部門にお勤めの方々に向けた情報を配信しております。
新任の方やベテランの方、管理職を対象とした幅広いコンテンツをご用意しております。
お問い合わせ
コストダウンが利益に直結する術だと理解していても、なかなか前に進めることができない状況。そんな時は、newjiのコストダウン自動化機能で大きく利益貢献しよう!
(Β版非公開)