- お役立ち記事
- Case Studies of Successful Remote Ramp-Up of New Product Mass Production
Case Studies of Successful Remote Ramp-Up of New Product Mass Production
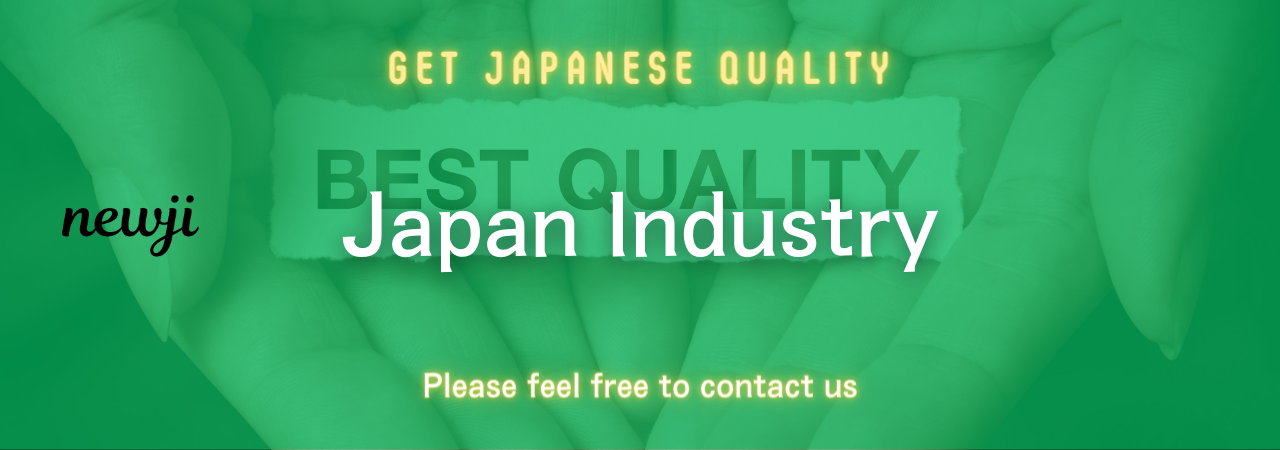
As the world of manufacturing evolves, companies are increasingly embracing remote strategies to enhance their operations. One significant aspect of this evolution is the ramp-up of new product mass production remotely. Transitioning to remote ramp-up can be challenging, but several companies have successfully navigated this path, providing invaluable insights and demonstrating its potential. In this article, we will delve into some case studies that highlight the benefits and strategies for successfully managing new product mass production remotely.
目次
Case Study 1: TechPioneers Inc.
Background
TechPioneers Inc., a leading technology firm, specializes in consumer electronics. The company decided to launch a new line of smartwatches with cutting-edge health monitoring features. Given the global nature of their operations, TechPioneers faced logistical challenges but aimed to ramp up production remotely.
Challenges Faced
1. Integration of new suppliers: The company had to onboard and integrate multiple new suppliers located in different parts of the world.
2. Quality control: Ensuring consistent quality of components without physical inspections posed a significant hurdle.
3. Coordination: Managing cross-functional teams spread across various locations required meticulous planning.
Strategies Employed
1. Leveraging Technology: TechPioneers utilized sophisticated project management software and communication tools to ensure seamless coordination among team members and suppliers.
2. Virtual Training Programs: The company developed extensive virtual training programs for new suppliers to align them with the production standards.
3. Remote Quality Monitoring: Implementing IoT-enabled devices allowed real-time monitoring of production quality from a distance.
Results
TechPioneers successfully ramped up the production of their new smartwatch line without major delays. Remote quality monitoring tools significantly reduced defect rates by 20%, and virtual training programs ensured suppliers met the required standards from the onset. This case shows how leveraging advanced technologies can address the common hurdles in remote production ramp-up.
Case Study 2: GreenAuto Motors
Background
GreenAuto Motors, renowned for its electric vehicles (EVs), decided to introduce a new model with improved battery technology. The company faced the additional complexity of managing the production scale-up during a global pandemic, necessitating remote strategies.
Challenges Faced
1. Supplier Coordination: Like many automotive companies, GreenAuto relies on a diverse supply chain, which became difficult to manage remotely.
2. Maintaining Timelines: Launching a new model required strict adherence to timelines, which could be jeopardized by remote operations.
3. Employee Training: New battery technology required specialized training for every team involved in production.
Strategies Employed
1. Digital Supply Chain Platforms: To streamline supplier coordination, GreenAuto implemented digital supply chain platforms that provided real-time updates and analytics.
2. Agile Methodologies: Adopting agile project management allowed the company to quickly respond to changes and issues, maintaining the project timeline.
3. Virtual Reality (VR) Training: They used VR to train employees on new assembly techniques and battery handling protocols, ensuring high skill levels without in-person sessions.
Results
Despite the challenges, GreenAuto successfully ramped up production of the new EV model. The use of digital supply chain platforms improved supply chain efficiency by 15%, and VR training reduced the error rates in battery assembly by 25%. This highlights how embracing digital tools can overcome the constraints of remote operations.
Case Study 3: PharmaNext Enterprises
Background
PharmaNext Enterprises, a pharmaceutical company, planned to mass-produce a new antiviral drug. Given the urgent demand and global health situation, they had to ramp up production quickly and remotely.
Challenges Faced
1. Regulatory Compliance: Ensuring the new production sites complied with international regulatory standards remotely was a significant challenge.
2. Supply Chain Disruptions: The pharmaceutical industry’s supply chain was heavily impacted due to the pandemic.
3. Scale-Up Processes: Traditionally, scaling up drug production involves iterative processes that were difficult to replicate remotely.
Strategies Employed
1. Remote Audits: Implementing remote audit technologies and virtual inspections ensured compliance without the need for physical presence.
2. Diversified Supply Chain: The company diversified its supplier base and employed predictive analytics to anticipate and mitigate supply chain disruptions.
3. Modular Manufacturing Units: PharmaNext adopted modular manufacturing units equipped with IoT sensors, allowing remote monitoring and control of production processes.
Results
PharmaNext successfully scaled up production of the antiviral drug, meeting global demand ahead of schedule. Remote audits ensured regulatory compliance, and predictive analytics reduced supply chain disruptions by 30%. This case illustrates how strategic planning and innovative technologies can enable rapid remote production ramp-up in critical industries.
Case Study 4: FashionForward Ltd.
Background
FashionForward Ltd., a major player in the fashion industry, planned to release a new collection of eco-friendly clothing. They decided to manage the entire production process remotely, from design to final manufacturing.
Challenges Faced
1. Design Integration: Coordinating design changes and ensuring they were accurately reflected in production without physical prototypes.
2. Sustainable Sourcing: Sourcing eco-friendly materials while verifying sustainability claims remotely.
3. Timely Delivery: Ensuring the new collection was produced and delivered in a timely manner to capitalize on market trends.
Strategies Employed
1. Digital Design Platforms: Utilizing 3D modeling and digital design platforms allowed real-time collaboration and virtual prototyping.
2. Blockchain Technology: Implementing blockchain technology verified the authenticity and sustainability of materials from suppliers.
3. Smart Logistics: Employing smart logistics solutions ensured efficient tracking and management of shipments.
Results
FashionForward successfully launched their new eco-friendly collection on time. Digital design platforms reduced design cycle time by 40%, and blockchain technology provided transparency in the material sourcing process. This example underscores how digital innovations can support remote production processes in the fashion industry.
Through these case studies, we see that with the right strategies and tools, remote ramp-up of new product mass production is not only feasible but can also lead to improved efficiency and quality. By leveraging technology, companies can overcome the traditional challenges of production ramp-up and adopt more agile and resilient production processes. These success stories serve as a roadmap for others looking to embrace remote production strategies in the future.
資料ダウンロード
QCD調達購買管理クラウド「newji」は、調達購買部門で必要なQCD管理全てを備えた、現場特化型兼クラウド型の今世紀最高の購買管理システムとなります。
ユーザー登録
調達購買業務の効率化だけでなく、システムを導入することで、コスト削減や製品・資材のステータス可視化のほか、属人化していた購買情報の共有化による内部不正防止や統制にも役立ちます。
NEWJI DX
製造業に特化したデジタルトランスフォーメーション(DX)の実現を目指す請負開発型のコンサルティングサービスです。AI、iPaaS、および先端の技術を駆使して、製造プロセスの効率化、業務効率化、チームワーク強化、コスト削減、品質向上を実現します。このサービスは、製造業の課題を深く理解し、それに対する最適なデジタルソリューションを提供することで、企業が持続的な成長とイノベーションを達成できるようサポートします。
オンライン講座
製造業、主に購買・調達部門にお勤めの方々に向けた情報を配信しております。
新任の方やベテランの方、管理職を対象とした幅広いコンテンツをご用意しております。
お問い合わせ
コストダウンが利益に直結する術だと理解していても、なかなか前に進めることができない状況。そんな時は、newjiのコストダウン自動化機能で大きく利益貢献しよう!
(Β版非公開)