- お役立ち記事
- Case Studies on AI Applications in Manufacturing
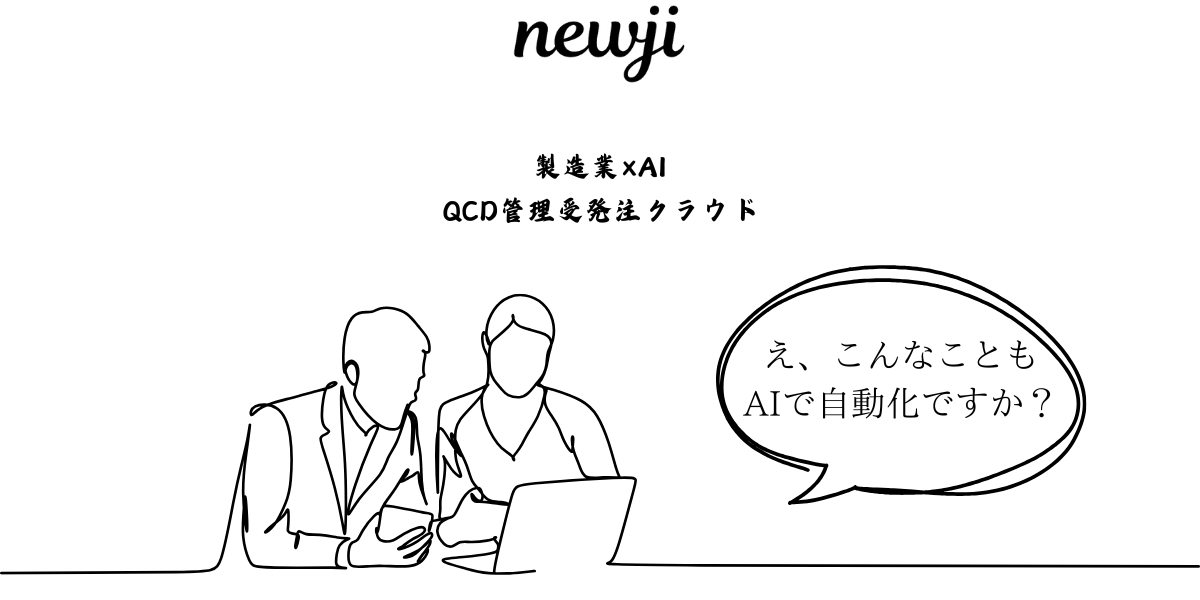
Case Studies on AI Applications in Manufacturing
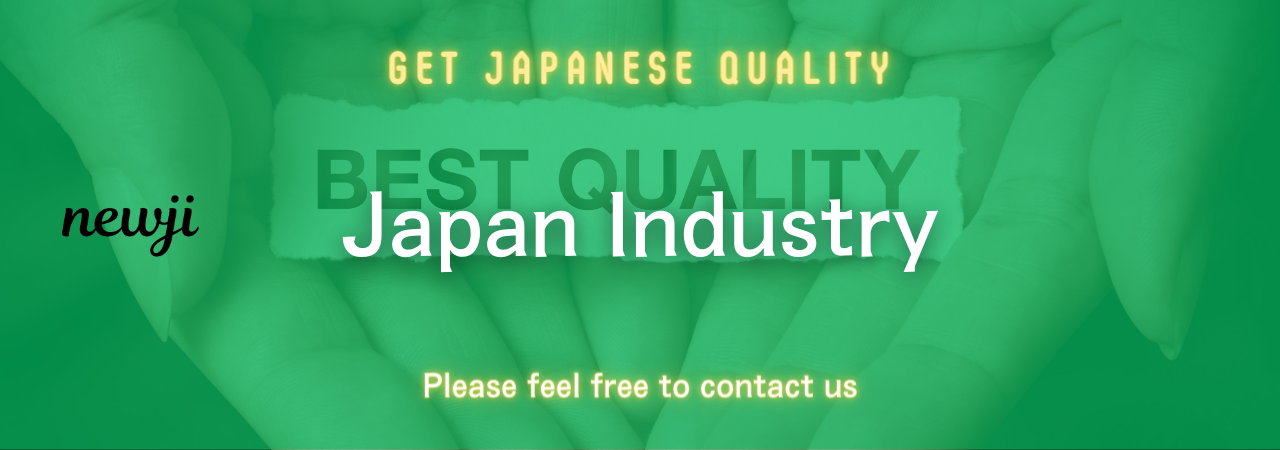
Artificial Intelligence (AI) is transforming the manufacturing industry by revolutionizing the way products are designed, produced, and serviced.
AI applications in manufacturing are enhancing efficiency, improving productivity, and fostering innovation.
In this article, we will explore various case studies that highlight the remarkable applications of AI in manufacturing.
目次
Predictive Maintenance
Predictive maintenance is one of the most impactful applications of AI in manufacturing.
By leveraging machine learning algorithms and data analytics, manufacturers can predict equipment failures before they occur.
This proactive approach reduces downtime and maintenance costs.
Case Study: Rolls-Royce
Rolls-Royce, a leading manufacturer of aircraft engines, has implemented AI-based predictive maintenance to monitor the health of its engines.
The company uses sensors to collect data on engine performance and operating conditions.
AI algorithms analyze this data to predict potential issues and schedule maintenance activities.
This approach has enabled Rolls-Royce to minimize unplanned downtime and improve the reliability of its engines.
Quality Control
Maintaining high-quality standards is crucial in manufacturing, and AI plays a significant role in ensuring product quality.
AI-powered vision systems can inspect products in real-time and detect defects with high accuracy.
Case Study: BMW
BMW, a renowned automobile manufacturer, uses AI-driven quality control systems on its production lines.
The company employs AI-powered cameras to inspect various components of its vehicles.
These cameras can detect even the smallest defects, such as scratches or dents, that are often missed by human inspectors.
By implementing AI for quality control, BMW has significantly reduced the number of defective products and enhanced customer satisfaction.
Supply Chain Optimization
AI is revolutionizing supply chain management by optimizing inventory levels, improving demand forecasting, and enhancing logistics.
Case Study: Siemens
Siemens, a global leader in automation and digitalization, has adopted AI to optimize its supply chain operations.
The company uses AI algorithms to analyze historical data and predict future demand for its products.
AI models also optimize inventory levels by determining the right amount of stock to be held at various locations.
As a result, Siemens has been able to reduce excess inventory, cut costs, and improve supply chain efficiency.
Robotic Process Automation (RPA)
Robotic Process Automation (RPA) uses AI to automate repetitive and mundane tasks in manufacturing.
RPA frees up human workers to focus on more strategic and complex activities.
Case Study: Foxconn
Foxconn, a leading electronics manufacturer, has implemented AI-powered RPA in its production facilities.
The company uses robotic arms equipped with AI algorithms to perform tasks such as component assembly, testing, and packaging.
These robots work tirelessly and with high precision, leading to increased productivity and reduced labor costs.
Foxconn’s adoption of RPA has also improved workplace safety by reducing the need for human workers to perform hazardous tasks.
Process Optimization
AI enhances manufacturing processes by optimizing parameters and reducing variability.
AI-driven process optimization leads to higher efficiency, lower production costs, and better product quality.
Case Study: Procter & Gamble
Procter & Gamble (P&G), a global consumer goods company, has implemented AI to optimize its production processes.
P&G uses AI algorithms to analyze data from its manufacturing operations and identify optimal process parameters.
For example, in its detergent manufacturing plants, AI models analyze variables such as temperature, pressure, and ingredient ratios to determine the best conditions for production.
This approach has resulted in improved product consistency, reduced waste, and lower energy consumption.
Product Design and Development
AI is transforming product design and development by enabling rapid prototyping and innovation.
AI-powered tools can generate design concepts, simulate performance, and optimize designs for manufacturability.
Case Study: General Electric (GE)
General Electric (GE), a multinational conglomerate, uses AI to accelerate product design and development.
GE employs AI-driven generative design software to create innovative and efficient designs for its products.
The software generates multiple design options based on specified criteria and constraints.
AI algorithms also simulate the performance of these designs under various conditions, allowing engineers to select the best option.
This approach has significantly reduced the time and cost associated with product development while fostering innovation.
Energy Management
AI applications in energy management help manufacturers reduce energy consumption, lower costs, and minimize their environmental footprint.
Case Study: Tesla
Tesla, a pioneer in electric vehicles and renewable energy, uses AI to optimize energy management in its manufacturing facilities.
The company employs AI algorithms to monitor energy usage and identify opportunities for improvement.
AI models also predict energy demand and optimize the operation of renewable energy sources, such as solar panels and battery storage systems.
Tesla’s AI-driven energy management approach has resulted in significant energy savings and reduced carbon emissions.
Conclusion
AI applications in manufacturing are driving significant improvements in efficiency, productivity, and innovation.
From predictive maintenance and quality control to supply chain optimization and energy management, AI is transforming every aspect of the manufacturing process.
The case studies of Rolls-Royce, BMW, Siemens, Foxconn, Procter & Gamble, General Electric, and Tesla illustrate the diverse and impactful ways AI is being leveraged in the industry.
As AI technology continues to evolve, we can expect even more groundbreaking applications that will further revolutionize manufacturing.
資料ダウンロード
QCD調達購買管理クラウド「newji」は、調達購買部門で必要なQCD管理全てを備えた、現場特化型兼クラウド型の今世紀最高の購買管理システムとなります。
ユーザー登録
調達購買業務の効率化だけでなく、システムを導入することで、コスト削減や製品・資材のステータス可視化のほか、属人化していた購買情報の共有化による内部不正防止や統制にも役立ちます。
NEWJI DX
製造業に特化したデジタルトランスフォーメーション(DX)の実現を目指す請負開発型のコンサルティングサービスです。AI、iPaaS、および先端の技術を駆使して、製造プロセスの効率化、業務効率化、チームワーク強化、コスト削減、品質向上を実現します。このサービスは、製造業の課題を深く理解し、それに対する最適なデジタルソリューションを提供することで、企業が持続的な成長とイノベーションを達成できるようサポートします。
オンライン講座
製造業、主に購買・調達部門にお勤めの方々に向けた情報を配信しております。
新任の方やベテランの方、管理職を対象とした幅広いコンテンツをご用意しております。
お問い合わせ
コストダウンが利益に直結する術だと理解していても、なかなか前に進めることができない状況。そんな時は、newjiのコストダウン自動化機能で大きく利益貢献しよう!
(Β版非公開)