- お役立ち記事
- Case Studies on Implementing Industry 4.0
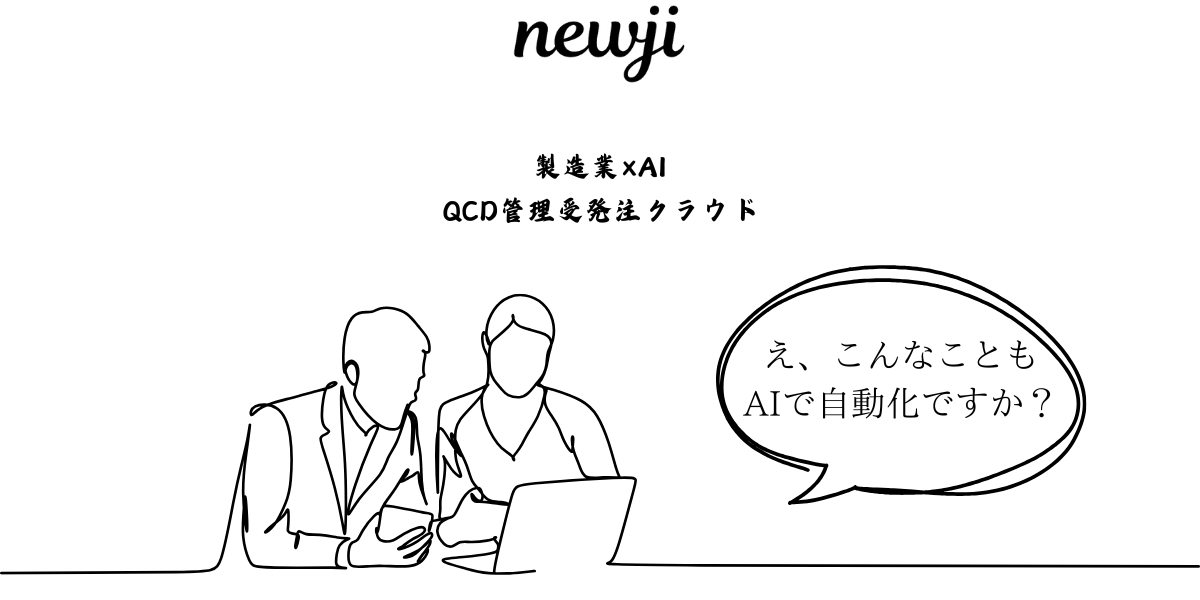
Case Studies on Implementing Industry 4.0
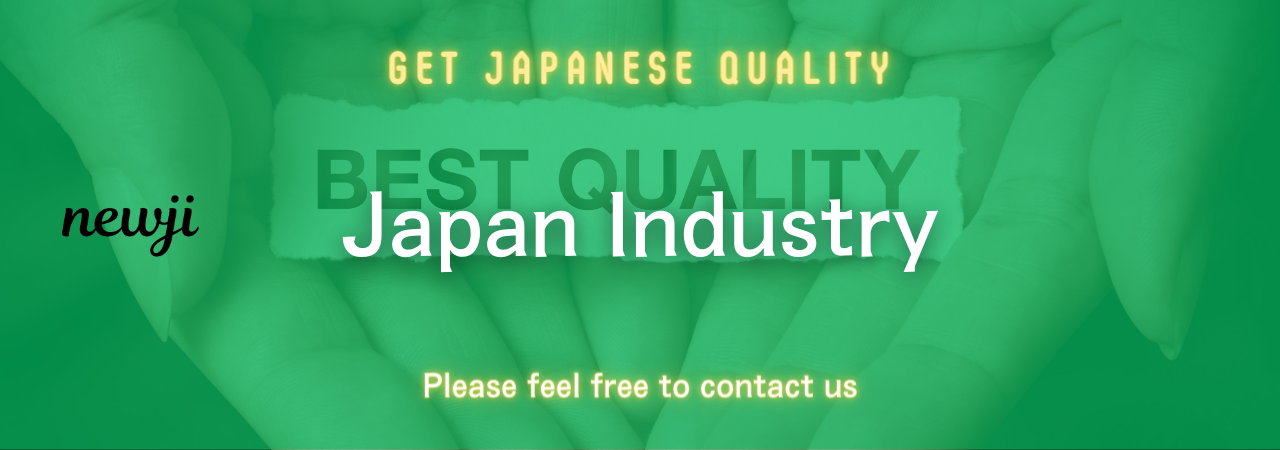
Industry 4.0 represents the fourth industrial revolution, where traditional manufacturing and industrial practices incorporate modern technology, such as the Internet of Things (IoT), cloud computing, and artificial intelligence (AI).
Companies across various sectors are continuously implementing these technologies to enhance their production processes, improve efficiencies, and stay competitive.
The following case studies provide a snapshot of how different industries are leveraging Industry 4.0 innovations.
目次
How the Automotive Industry Embraces Industry 4.0
Case Study: BMW Manufacturing Plant
BMW’s Spartanburg plant in South Carolina is a prime example of how the automotive industry utilizes Industry 4.0 technologies.
The plant incorporates IoT sensors across its assembly lines to monitor and control manufacturing processes in real-time.
These sensors collect vast amounts of data, which are analyzed to detect potential issues before they escalate, ensuring minimal downtime.
Moreover, the plant employs AI algorithms to optimize production schedules.
These algorithms analyze historical data and current conditions to make informed decisions about production rates, supply chain management, and workforce allocation.
As a result, BMW has seen considerable improvements in both operational efficiency and product quality.
Case Study: Mercedes-Benz and Predictive Maintenance
Mercedes-Benz has also adopted Industry 4.0 principles, particularly in predictive maintenance.
Sensors installed in machinery and equipment continuously monitor various parameters like temperature, vibration, and pressure.
The data gathered helps in predicting potential failures before they occur, thus enabling proactive maintenance.
Using predictive maintenance, Mercedes-Benz has reduced unplanned downtime significantly, saving both time and costs.
Additionally, the approach has enhanced the lifespan of machinery, leading to more sustainable production processes.
The Impact of Industry 4.0 on the Healthcare Sector
Case Study: Siemens Healthineers and Digital Twins
Siemens Healthineers exemplifies the integration of Industry 4.0 in healthcare.
One of their groundbreaking innovations includes the use of digital twins—virtual replicas of physical devices.
Medical machines such as MRI and CT scanners are equipped with IoT sensors that send real-time data to their digital twins.
These digital twins allow engineers to simulate different scenarios and optimize machine settings without interrupting ongoing operations.
Hospitals benefit from this technology by experiencing less downtime and improved machine performance.
Patients receive quicker, more accurate diagnoses, enhancing overall healthcare delivery.
Case Study: Philips and AI-Powered Diagnostics
Philips has been at the forefront of using AI in healthcare diagnostics.
Their AI-powered systems can analyze medical images and provide accurate diagnoses much faster than traditional methods.
For instance, AI algorithms can identify abnormalities in radiology images, such as tumors, with high precision.
The speed and accuracy provided by these AI systems enable doctors to make quicker, more informed decisions.
This approach not only improves patient outcomes but also alleviates the workload on healthcare professionals.
Revolutionizing the Manufacturing Sector with Industry 4.0
Case Study: General Electric’s Brilliant Factories
General Electric (GE) has introduced the concept of “Brilliant Factories” to exemplify the integration of Industry 4.0 technologies in manufacturing.
These factories utilize a combination of IoT, AI, and advanced analytics to create highly efficient and responsive manufacturing environments.
Sensors collect data from various parts of the factory, which is then analyzed to optimize manufacturing processes continually.
For example, GE’s Brilliant Factories can predict equipment failures and schedule maintenance before a breakdown occurs.
This predictive capability can reduce unplanned downtime by up to 20%.
Case Study: Siemens and Smart Automation
Siemens has also been a pioneer in implementing Industry 4.0 technologies through its smart manufacturing solutions.
Their automated systems use AI and IoT to control various aspects of the production process autonomously.
For instance, Siemens’ smart factories can adjust production rates in real-time based on demand signals from the market.
This level of automation and real-time responsiveness ensures that production is always aligned with demand, reducing waste and lowering costs.
Furthermore, the interconnected systems provide valuable insights into every stage of the manufacturing process, enabling continuous improvement.
The Role of Industry 4.0 in Retail
Case Study: Walmart and Supply Chain Optimization
Walmart leverages Industry 4.0 technologies to optimize its expansive supply chain.
IoT sensors track products from the warehouse to the store shelves, providing real-time inventory data.
This data-driven approach ensures that products are always in stock and readily available to customers.
Moreover, Walmart uses AI algorithms to predict customer demand.
These predictions help in inventory planning, ensuring that the right products are available at the right time.
The result is a more efficient supply chain, improved customer satisfaction, and increased sales.
Case Study: Amazon and Warehouse Automation
Amazon’s use of Industry 4.0 technologies extends to its highly automated warehouses.
Robots equipped with IoT sensors and AI-driven navigation systems perform tasks such as sorting, packing, and transporting items.
These robots work alongside human employees to increase productivity and reduce operational costs.
The real-time data collected by these robots is analyzed to optimize warehouse layout and operations continuously.
As a result, Amazon can fulfill orders more quickly, ensuring timely delivery to customers around the globe.
Conclusion
These case studies illustrate the transformative potential of Industry 4.0 across various sectors.
From automotive and healthcare to manufacturing and retail, the integration of IoT, AI, and advanced analytics is revolutionizing traditional processes and enhancing efficiencies.
As more companies embrace these technologies, we can expect to see even greater improvements in operational performance, customer satisfaction, and overall industry innovation.
By leveraging Industry 4.0 principles, businesses not only stay competitive but also pave the way for a more efficient, sustainable, and interconnected future.
資料ダウンロード
QCD調達購買管理クラウド「newji」は、調達購買部門で必要なQCD管理全てを備えた、現場特化型兼クラウド型の今世紀最高の購買管理システムとなります。
ユーザー登録
調達購買業務の効率化だけでなく、システムを導入することで、コスト削減や製品・資材のステータス可視化のほか、属人化していた購買情報の共有化による内部不正防止や統制にも役立ちます。
NEWJI DX
製造業に特化したデジタルトランスフォーメーション(DX)の実現を目指す請負開発型のコンサルティングサービスです。AI、iPaaS、および先端の技術を駆使して、製造プロセスの効率化、業務効率化、チームワーク強化、コスト削減、品質向上を実現します。このサービスは、製造業の課題を深く理解し、それに対する最適なデジタルソリューションを提供することで、企業が持続的な成長とイノベーションを達成できるようサポートします。
オンライン講座
製造業、主に購買・調達部門にお勤めの方々に向けた情報を配信しております。
新任の方やベテランの方、管理職を対象とした幅広いコンテンツをご用意しております。
お問い合わせ
コストダウンが利益に直結する術だと理解していても、なかなか前に進めることができない状況。そんな時は、newjiのコストダウン自動化機能で大きく利益貢献しよう!
(Β版非公開)