- お役立ち記事
- Case Studies on Implementing TPM (Total Productive Maintenance)
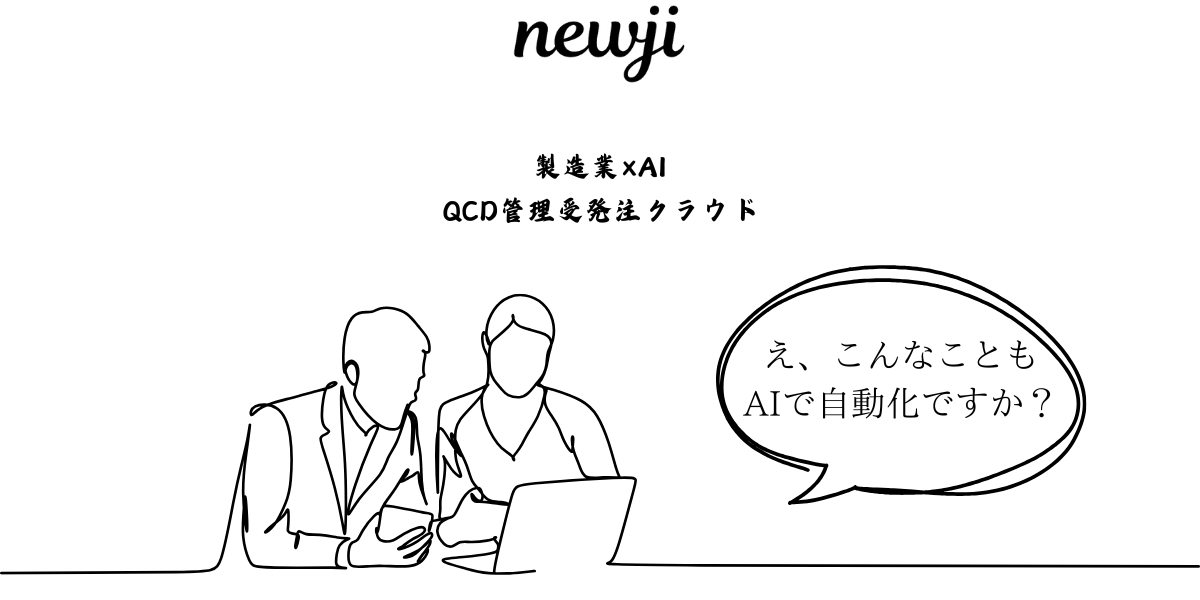
Case Studies on Implementing TPM (Total Productive Maintenance)
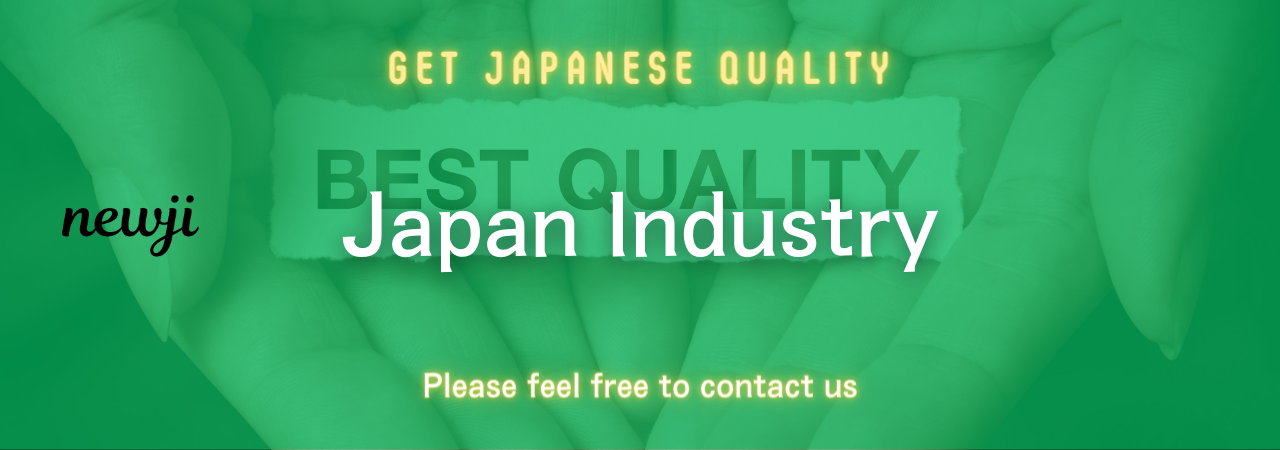
目次
Introduction to Total Productive Maintenance (TPM)
Total Productive Maintenance (TPM) is a systematic approach to maintaining and improving the integrity of production and quality systems through machines, equipment, processes, and employees.
This method integrates maintenance-related activities into the operational functions of a business, aiming to achieve zero defects, zero breakdowns, and zero accidents.
TPM focuses on proactive and preventive techniques to enhance equipment’s operational efficiency, which is achieved by involving all employees—from top management to front-line workers.
Why Implement TPM?
Companies implement TPM for several reasons.
First, it significantly reduces downtime, thereby increasing productivity.
Second, it fosters a workplace culture where employees are motivated to proactively maintain their tools and machinery.
This proactive approach helps companies save on costly repairs and increase the lifespan of equipment.
Lastly, TPM ensures that machines operate at their highest efficiency, which improves the quality of the final product.
Step-by-Step Approach to TPM Implementation
Implementing TPM involves several key steps.
Without proper planning, the initiative may fail to deliver the expected results.
Here’s a structured approach to achieving successful TPM implementation.
Step 1: Initial Evaluation
Before rolling out a TPM program, conduct an initial evaluation.
This will help you understand your current maintenance practices and identify areas that require improvement.
Analyze metrics such as downtime, equipment efficiency, and maintenance costs.
Step 2: Training and Awareness
Training is a crucial component of TPM.
Your team needs to be aware of the benefits of TPM and how they can contribute to its success.
Organize workshops and training sessions to educate employees on TPM principles.
Step 3: Form a TPM Committee
Establish a TPM committee consisting of key stakeholders from different departments.
This committee will be responsible for driving TPM initiatives and ensuring their successful execution.
Step 4: Establish Goals and Objectives
Set clear, achievable goals for your TPM program.
These targets could include reducing downtime, improving machine efficiency, or minimizing defects.
Well-defined objectives help in tracking progress and sustaining motivation among team members.
Step 5: Implementation of 5S
The 5S methodology (Sort, Set in order, Shine, Standardize, and Sustain) forms the foundation of TPM.
This approach encourages a clean, organized workspace through regular housekeeping and maintenance activities.
Implementing 5S makes it easier to detect anomalies in equipment, thereby preventing issues before they escalate.
Step 6: Autonomous Maintenance
Autonomous Maintenance empowers machine operators to take responsibility for the upkeep of their equipment.
Operators are trained to perform routine maintenance tasks such as cleaning, inspection, and basic repairs.
This step reduces the reliance on specialized maintenance staff, thereby speeding up the problem-solving process.
Step 7: Planned Maintenance
Develop a scheduled maintenance plan to ensure the regular upkeep of machinery.
This involves maintaining machinery based on usage patterns and predicted failure points.
Planned Maintenance helps in reducing unexpected breakdowns and extends the life of the equipment.
Step 8: Continuous Improvement
TPM is an ongoing process of continuous improvement.
Regularly review performance metrics to identify areas for further enhancement.
Engage employees in brainstorming sessions to come up with innovative solutions to persistent issues.
Case Study 1: Manufacturing Plant A
Manufacturing Plant A faced frequent equipment breakdowns, resulting in lost production time and increased costs.
They decided to implement TPM to reverse this trend.
Initially, they conducted a thorough evaluation to identify problem areas.
Following this, they organized intensive training sessions to ensure that all employees understood the importance of TPM and their roles in its implementation.
A TPM committee was formed to oversee the process, and the 5S methodology was introduced to create a more organized workspace.
Operators were trained to perform autonomous maintenance, which resulted in quicker detection and resolution of issues.
The plant also implemented a planned maintenance schedule to ensure timely servicing of equipment.
Within six months, Manufacturing Plant A saw a 30% reduction in downtime and a significant improvement in overall productivity.
Case Study 2: Food Processing Facility B
Food Processing Facility B struggled with inconsistent product quality and frequent equipment malfunctions.
Their goal was to achieve consistent quality and minimize disruptions.
They started by evaluating their maintenance practices and identifying bottlenecks.
Employee training was prioritized, and a dedicated TPM committee was formed to guide the initiative.
The 5S principles were adopted, resulting in a cleaner, more organized environment.
Autonomous maintenance was introduced, empowering operators to take control of simple maintenance tasks.
This not only improved equipment uptime but also allowed specialized maintenance staff to focus on more complex issues.
By establishing a planned maintenance schedule, they were able to proactively address potential problems.
Within a year, the facility achieved a substantial improvement in product quality and a 25% reduction in maintenance costs.
Challenges and Solutions in Implementing TPM
Despite its benefits, implementing TPM comes with challenges.
One common issue is employee resistance to change.
To overcome this, involve employees in the decision-making process and emphasize the long-term benefits of TPM.
Another challenge is the initial cost of training and system changes.
Although the upfront investment can be substantial, the long-term savings and productivity gains often justify the expense.
Lack of ongoing commitment from management can also hinder the success of TPM.
Sustain the momentum by regularly reviewing progress, celebrating successes, and addressing any emerging issues promptly.
Conclusion
Total Productive Maintenance is a proven strategy for improving efficiency, reducing downtime, and enhancing product quality.
By following a step-by-step approach and learning from successful case studies, companies can implement TPM effectively.
Although challenges may arise, the benefits of a well-executed TPM program far outweigh the difficulties. Whether you operate a manufacturing plant, food processing facility, or any other type of business involving machinery, TPM can help you achieve your operational goals.
Remember that TPM is a continuous journey of improvement, and its success relies on the active participation and commitment of everyone involved.
資料ダウンロード
QCD調達購買管理クラウド「newji」は、調達購買部門で必要なQCD管理全てを備えた、現場特化型兼クラウド型の今世紀最高の購買管理システムとなります。
ユーザー登録
調達購買業務の効率化だけでなく、システムを導入することで、コスト削減や製品・資材のステータス可視化のほか、属人化していた購買情報の共有化による内部不正防止や統制にも役立ちます。
NEWJI DX
製造業に特化したデジタルトランスフォーメーション(DX)の実現を目指す請負開発型のコンサルティングサービスです。AI、iPaaS、および先端の技術を駆使して、製造プロセスの効率化、業務効率化、チームワーク強化、コスト削減、品質向上を実現します。このサービスは、製造業の課題を深く理解し、それに対する最適なデジタルソリューションを提供することで、企業が持続的な成長とイノベーションを達成できるようサポートします。
オンライン講座
製造業、主に購買・調達部門にお勤めの方々に向けた情報を配信しております。
新任の方やベテランの方、管理職を対象とした幅広いコンテンツをご用意しております。
お問い合わせ
コストダウンが利益に直結する術だと理解していても、なかなか前に進めることができない状況。そんな時は、newjiのコストダウン自動化機能で大きく利益貢献しよう!
(Β版非公開)