- お役立ち記事
- Case Studies on Improving Manufacturing Lines
月間76,176名の
製造業ご担当者様が閲覧しています*
*2025年3月31日現在のGoogle Analyticsのデータより
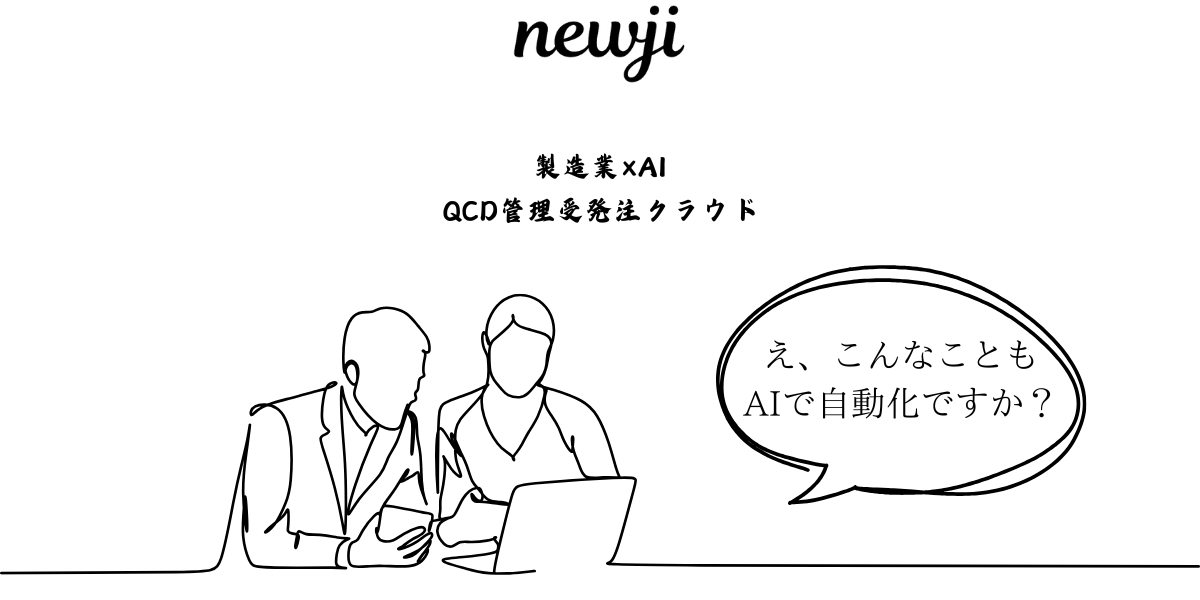
Case Studies on Improving Manufacturing Lines
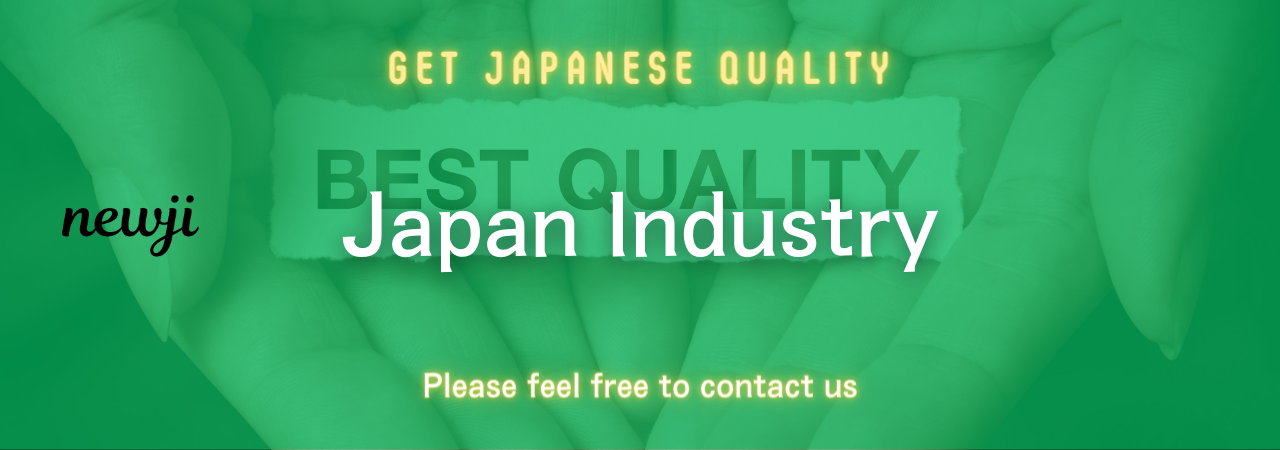
Manufacturing lines are the backbone of any production facility.
To improve efficiency, reduce costs, and enhance product quality, manufacturers are constantly looking for ways to optimize their processes.
In this article, we will explore several case studies on improving manufacturing lines. These real-world examples demonstrate how different companies have tackled common challenges and achieved significant improvements.
目次
Case Study 1: Implementing Lean Manufacturing Principles
One of the most popular methodologies for improving manufacturing lines is Lean Manufacturing.
A well-known electronics manufacturer implemented Lean principles to reduce waste and improve production efficiency.
The company began by identifying areas with excessive waste, such as overproduction, waiting times, and unnecessary transportation.
By using tools like Value Stream Mapping (VSM), the company gained a clearer view of its processes and pinpointed non-value-added activities.
They then introduced a Kanban system to manage inventory more efficiently, reducing excessive stock and cutting down on storage costs.
Additionally, they restructured the factory layout to minimize movement and transportation of materials. This not only saved time but also reduced the risk of accidents and material damage.
As a result of these Lean Manufacturing initiatives, the company experienced a 20% increase in productivity and a 15% reduction in operating costs over a year.
Case Study 2: Adopting Automation and Robotics
Automation and robotics have revolutionized the manufacturing industry, providing immense benefits in terms of speed, precision, and consistency.
A car manufacturing company decided to implement advanced robotics to automate repetitive tasks on their assembly line.
Before automation, the company faced issues with inconsistent product quality and workers’ fatigue from repetitive tasks.
By deploying robots for tasks such as welding, painting, and assembling, the company saw a significant improvement in the overall quality of their products.
Robotic arms performed tasks with perfect precision, eliminating human errors and ensuring uniformity in production.
Furthermore, automation allowed the company to operate around the clock, which led to a substantial increase in output.
Within six months, the company reported a 30% increase in production volume and a 25% decrease in defects. Additionally, employee satisfaction improved as workers were assigned to more engaging and less physically demanding roles.
Case Study 3: Using Six Sigma to Reduce Defects
Six Sigma is a data-driven approach to improving processes by reducing defects and ensuring quality.
A pharmaceutical company struggling with high defect rates and product recalls decided to implement Six Sigma methodologies to improve their manufacturing line.
The company assembled a team of Six Sigma experts who conducted thorough analyses to identify root causes of defects.
Using tools such as DMAIC (Define, Measure, Analyze, Improve, Control) and statistical process control, they pinpointed specific steps in the production process where errors were most likely to occur.
The team then developed targeted solutions to address these issues, such as tightening process controls, enhancing staff training, and refining equipment maintenance schedules.
Over the course of the project, the defect rate dropped by 50%, and the company enjoyed significant cost savings due to fewer recalls and less waste.
The improved reliability of their products also enhanced their reputation in the market.
Case Study 4: Enhancing Worker Training and Engagement
While technology and processes are critical for optimizing manufacturing lines, the human factor remains equally important.
A consumer goods manufacturer recognized that enhancing worker training and engagement could lead to better performance and fewer errors.
The company launched a comprehensive training program that covered not only technical skills but also emphasized the importance of quality and safety.
Additionally, they implemented a system where employees could provide feedback and suggest improvements to the manufacturing process.
This initiative resulted in a more knowledgeable and motivated workforce, which directly translated to improved operational performance.
The company observed a 15% increase in productivity and a 10% reduction in accident rates.
Employee suggestions also led to several process innovations that further streamlined production.
Case Study 5: Incorporating Predictive Maintenance
Maintenance issues can cause significant downtime and loss of productivity in manufacturing lines.
A food processing company faced frequent equipment breakdowns that disrupted their production schedules.
To address this, they implemented a predictive maintenance program using IoT (Internet of Things) sensors and advanced analytics.
Sensors were installed on critical machinery to monitor parameters such as vibration, temperature, and pressure.
These sensors collected data in real time, which was then analyzed to predict when equipment was likely to fail.
By anticipating breakdowns, the company was able to carry out maintenance proactively, scheduling it during non-peak hours to minimize disruptions.
This predictive maintenance approach resulted in a 40% reduction in unplanned downtime and a 20% decrease in maintenance costs.
Conclusion
These case studies highlight various strategies that manufacturing companies have successfully employed to enhance their production lines.
From Lean Manufacturing and automation to Six Sigma and worker engagement, each approach addresses specific challenges and provides tangible benefits.
By learning from these real-world examples, manufacturers can adopt similar tactics tailored to their unique needs, ultimately driving efficiency, reducing costs, and improving product quality.
As the manufacturing landscape continues to evolve, staying ahead with continuous improvement efforts remains crucial for long-term success.
資料ダウンロード
QCD管理受発注クラウド「newji」は、受発注部門で必要なQCD管理全てを備えた、現場特化型兼クラウド型の今世紀最高の受発注管理システムとなります。
ユーザー登録
受発注業務の効率化だけでなく、システムを導入することで、コスト削減や製品・資材のステータス可視化のほか、属人化していた受発注情報の共有化による内部不正防止や統制にも役立ちます。
NEWJI DX
製造業に特化したデジタルトランスフォーメーション(DX)の実現を目指す請負開発型のコンサルティングサービスです。AI、iPaaS、および先端の技術を駆使して、製造プロセスの効率化、業務効率化、チームワーク強化、コスト削減、品質向上を実現します。このサービスは、製造業の課題を深く理解し、それに対する最適なデジタルソリューションを提供することで、企業が持続的な成長とイノベーションを達成できるようサポートします。
製造業ニュース解説
製造業、主に購買・調達部門にお勤めの方々に向けた情報を配信しております。
新任の方やベテランの方、管理職を対象とした幅広いコンテンツをご用意しております。
お問い合わせ
コストダウンが利益に直結する術だと理解していても、なかなか前に進めることができない状況。そんな時は、newjiのコストダウン自動化機能で大きく利益貢献しよう!
(β版非公開)