- お役立ち記事
- Case Studies on the Utilization of Digital Twins in Manufacturing During the Industry 4.0 Era
Case Studies on the Utilization of Digital Twins in Manufacturing During the Industry 4.0 Era
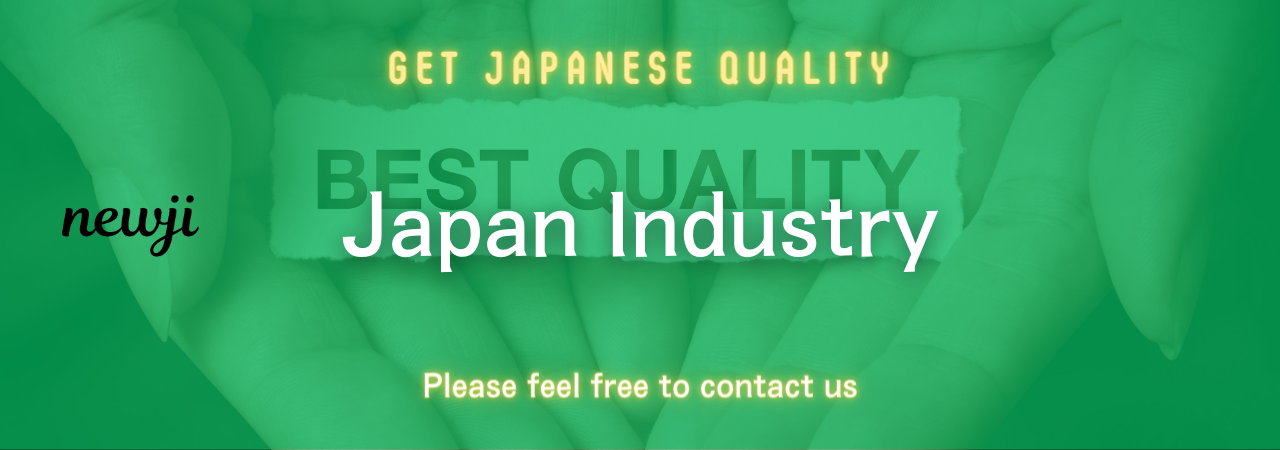
目次
Understanding Digital Twins
Digital twins have emerged as one of the most exciting innovations in the manufacturing industry.
But what exactly are digital twins?
In simple terms, a digital twin is a virtual replica of a physical object or system.
This digital replica can be used to analyze and optimize processes, making it a valuable tool in the era of Industry 4.0.
Industry 4.0, often referred to as the fourth industrial revolution, involves the automation and digitalization of manufacturing.
This revolution leverages technologies such as the Internet of Things (IoT), big data analytics, and artificial intelligence.
Among these, digital twins play a crucial role in enhancing productivity and efficiency.
How Digital Twins Work
A digital twin operates by gathering data from sensors installed on the physical object or system.
These sensors collect real-time data, which is then fed into the digital twin.
The digital twin uses this data to simulate the performance and behavior of the physical counterpart.
This allows manufacturers to monitor systems in real time, predict issues, and optimize processes.
Moreover, digital twins enable manufacturers to test different scenarios and determine the best solutions without disrupting the actual production line.
This can lead to significant cost savings and better overall performance.
Case Study 1: Reducing Downtime in Automotive Manufacturing
One of the most compelling applications of digital twins is in automotive manufacturing.
A global automotive manufacturer faced frequent downtime issues that resulted in significant production losses.
By implementing digital twin technology, they were able to monitor the condition and performance of their machinery in real time.
The digital twin created a detailed virtual model of the manufacturing equipment.
The data from the sensors was continuously analyzed to detect any irregularities.
Whenever a potential issue was identified, the system alerted the maintenance team, allowing them to address the problem before it caused a breakdown.
As a result, the company saw a dramatic reduction in downtime and improved overall productivity.
Predictive Maintenance
Predictive maintenance is one of the standout benefits of using digital twins.
By analyzing data patterns, digital twins can predict when a piece of equipment is likely to fail.
In the automotive case study, predictive maintenance helped the company avoid costly repairs and unexpected breakdowns.
This proactive approach not only reduced downtime but also extended the lifespan of the equipment.
Case Study 2: Optimizing Production in Chemical Manufacturing
Another interesting case is in the chemical manufacturing industry.
A leading chemical company needed to optimize their production process to meet increasing demand while maintaining quality.
They opted for digital twin technology to achieve this goal.
The digital twin provided a comprehensive virtual model of the entire production line, from raw material intake to finished product output.
By simulating different production scenarios, the company could identify bottlenecks and inefficiencies.
They were able to adjust parameters such as temperature, pressure, and flow rates to achieve optimal production conditions.
This led to a significant increase in throughput and product quality.
Enhanced Decision Making
One of the key advantages of digital twins is their ability to enhance decision-making.
In the chemical manufacturing case, the digital twin offered insights that were previously unavailable.
Managers could make data-driven decisions based on real-time simulations and scenario analyses.
This resulted in better resource allocation and more efficient production cycles.
Case Study 3: Improving Supply Chain Management in Electronics Manufacturing
Electronics manufacturing is another field where digital twins have proved incredibly valuable.
A major electronics manufacturer faced challenges in managing their complex supply chain.
They needed to ensure that components from various suppliers arrived on time and met quality standards.
The digital twin of their supply chain allowed them to track every component in real time.
They could monitor the location, condition, and expected delivery times of all supplies.
By analyzing this data, they could identify potential delays and quality issues before they impacted production.
This resulted in a more reliable supply chain and reduced lead times.
Risk Mitigation
Digital twins also play a vital role in risk mitigation.
For the electronics manufacturer, the digital twin provided a detailed overview of the entire supply chain.
This enabled them to identify vulnerabilities and develop contingency plans.
If a supplier faced an unforeseen issue, the company could quickly adjust their plans to minimize disruption.
This proactive approach significantly reduced risks and ensured smoother operations.
The Future of Digital Twins in Manufacturing
The potential of digital twins in manufacturing is immense.
As technology continues to advance, so will the capabilities of digital twins.
Future applications may include even more sophisticated simulations and predictive analytics.
Furthermore, the integration of artificial intelligence and machine learning with digital twins will open new possibilities.
AI-driven digital twins could offer even more accurate predictions and automated optimizations.
This could lead to unprecedented levels of efficiency and innovation in manufacturing.
In conclusion, digital twins are transforming the manufacturing landscape in the Industry 4.0 era.
By providing real-time insights, predictive maintenance, enhanced decision-making, and risk mitigation, digital twins are enabling manufacturers to achieve new heights of productivity and efficiency.
As more companies adopt this technology, the future of manufacturing looks brighter than ever.
By exploring the case studies presented here, it is evident that digital twins are not merely a trend but a strategic tool for modern manufacturing.
They offer tangible benefits that drive business success and set the stage for continuous improvement and innovation.
資料ダウンロード
QCD調達購買管理クラウド「newji」は、調達購買部門で必要なQCD管理全てを備えた、現場特化型兼クラウド型の今世紀最高の購買管理システムとなります。
ユーザー登録
調達購買業務の効率化だけでなく、システムを導入することで、コスト削減や製品・資材のステータス可視化のほか、属人化していた購買情報の共有化による内部不正防止や統制にも役立ちます。
NEWJI DX
製造業に特化したデジタルトランスフォーメーション(DX)の実現を目指す請負開発型のコンサルティングサービスです。AI、iPaaS、および先端の技術を駆使して、製造プロセスの効率化、業務効率化、チームワーク強化、コスト削減、品質向上を実現します。このサービスは、製造業の課題を深く理解し、それに対する最適なデジタルソリューションを提供することで、企業が持続的な成長とイノベーションを達成できるようサポートします。
オンライン講座
製造業、主に購買・調達部門にお勤めの方々に向けた情報を配信しております。
新任の方やベテランの方、管理職を対象とした幅広いコンテンツをご用意しております。
お問い合わせ
コストダウンが利益に直結する術だと理解していても、なかなか前に進めることができない状況。そんな時は、newjiのコストダウン自動化機能で大きく利益貢献しよう!
(Β版非公開)