- お役立ち記事
- Case Studies on Using Mobile Apps in Production Sites
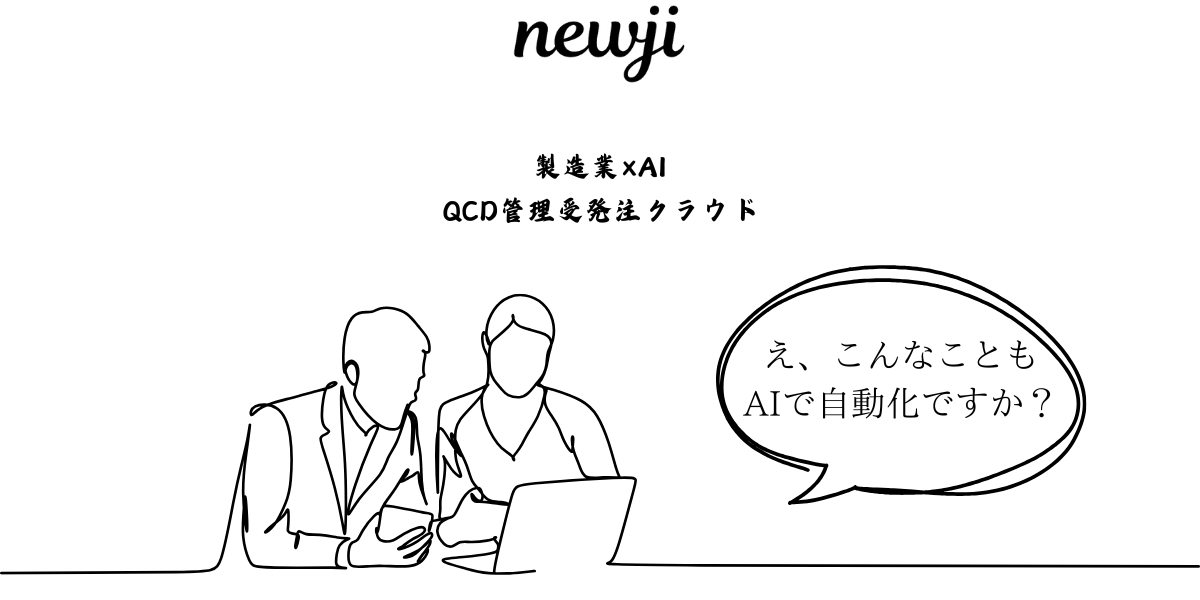
Case Studies on Using Mobile Apps in Production Sites
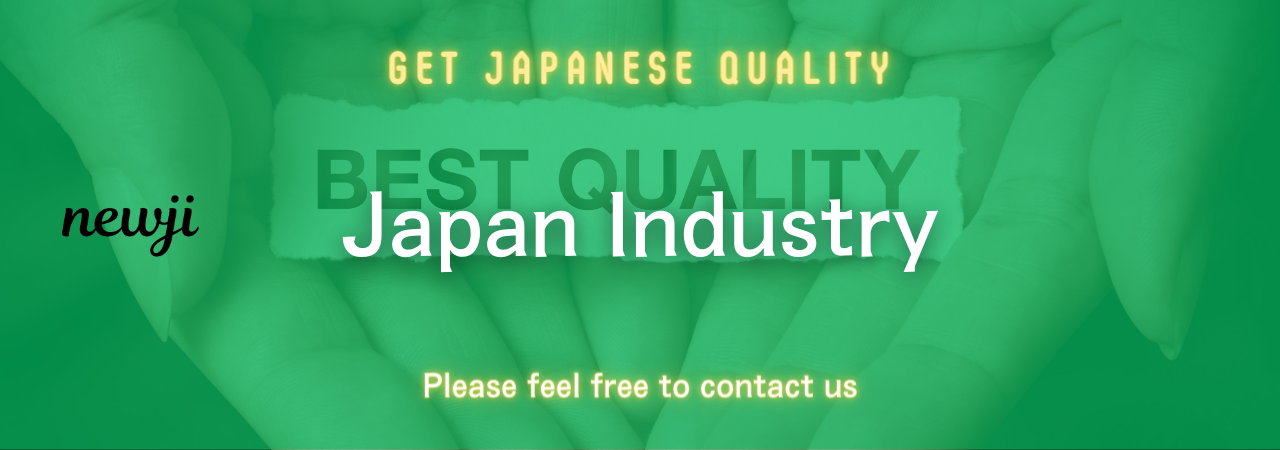
Mobile apps are transforming various industries, and production sites are no exception.
They offer seamless integration of multiple processes, leading to increased efficiency and productivity.
In this article, we will delve into real-life case studies showcasing the application of mobile apps in production sites.
Let’s explore how these sites have benefitted from mobile technology.
目次
The Shift Towards Mobile Technology
Production sites traditionally rely on manual processes and desktop-based systems.
With the advent of mobile technology, there’s a noticeable shift toward mobile-based solutions.
This transition is accelerating the pace of work and enhancing real-time communication.
Real-Time Data Access
One significant advantage of mobile apps in production is real-time data access.
Employees can access updates instantly, promoting quick decision-making.
In a case study of a major automobile manufacturer, implementing a mobile app allowed managers to monitor production lines in real-time.
This innovation drastically reduced downtime and improved overall production efficiency.
Case Study: Ford’s Assembly Line
Ford Motor Company, a leader in the automotive industry, adopted a mobile app to streamline its assembly line.
They faced several challenges, including miscommunication and delays.
The mobile app introduced a centralized platform for all assembly tasks.
Enhanced Communication and Coordination
Before the mobile app, communication was cumbersome and prone to errors.
With the new system, everyone from line workers to managers could communicate seamlessly.
Tasks were assigned and monitored through the app, ensuring that everyone was on the same page.
This resulted in a 30% reduction in errors and a 20% increase in production speed.
Inventory Management
Managing inventory was another area where the app proved beneficial.
Real-time tracking of parts and materials ensured that the assembly line never experienced shortages.
The inventory management feature reduced excess storage costs and improved resource utilization.
Case Study: Delta Electronics’ Production Line
Delta Electronics, a global provider of power and thermal management solutions, integrated mobile apps into their production processes.
They aimed to enhance quality control and increase efficiency.
Quality Control
Maintaining high-quality standards is crucial for Delta Electronics.
The mobile app included features for workers to report issues and escalate them if necessary.
This real-time feedback loop helped in promptly addressing quality concerns.
Analysis showed a 25% improvement in product quality after implementing the mobile app.
Employee Training and Safety
Training new employees was traditionally a time-consuming process.
With the mobile app, training modules could be accessed on the go.
Additionally, safety alerts and protocols were integrated into the app.
This resulted in a more educated workforce and a 15% reduction in workplace accidents.
Case Study: PepsiCo’s Plant Operations
PepsiCo incorporated a mobile app to oversee its plant operations, focusing on efficiency and waste reduction.
The mobile app provided numerous benefits, from tracking production metrics to reducing downtime.
Production Dashboard
The mobile app offered a comprehensive production dashboard.
Managers could monitor output, machine performance, and worker productivity in real-time.
This visibility enabled swift action on any discrepancies.
PepsiCo reported a 12% rise in production efficiency post-implementation.
Waste Reduction
Another critical feature was waste management.
The app tracked production waste and provided insights on reducing it.
Over six months, PepsiCo managed to cut down waste by 18%, contributing to cost savings and environmental conservation.
Conclusion
Mobile apps are revolutionizing production sites by providing real-time data, improving communication, and enhancing efficiency.
The case studies of Ford, Delta Electronics, and PepsiCo demonstrate tangible benefits, such as reduced errors, better quality control, and waste reduction.
As technology continues to evolve, adopting mobile apps in production sites will likely become the norm, driving further innovation and growth.
資料ダウンロード
QCD調達購買管理クラウド「newji」は、調達購買部門で必要なQCD管理全てを備えた、現場特化型兼クラウド型の今世紀最高の購買管理システムとなります。
ユーザー登録
調達購買業務の効率化だけでなく、システムを導入することで、コスト削減や製品・資材のステータス可視化のほか、属人化していた購買情報の共有化による内部不正防止や統制にも役立ちます。
NEWJI DX
製造業に特化したデジタルトランスフォーメーション(DX)の実現を目指す請負開発型のコンサルティングサービスです。AI、iPaaS、および先端の技術を駆使して、製造プロセスの効率化、業務効率化、チームワーク強化、コスト削減、品質向上を実現します。このサービスは、製造業の課題を深く理解し、それに対する最適なデジタルソリューションを提供することで、企業が持続的な成長とイノベーションを達成できるようサポートします。
オンライン講座
製造業、主に購買・調達部門にお勤めの方々に向けた情報を配信しております。
新任の方やベテランの方、管理職を対象とした幅広いコンテンツをご用意しております。
お問い合わせ
コストダウンが利益に直結する術だと理解していても、なかなか前に進めることができない状況。そんな時は、newjiのコストダウン自動化機能で大きく利益貢献しよう!
(Β版非公開)