- お役立ち記事
- Case Studies: Solving〇〇Challenges with Japanese Manufacturing Expertise
月間76,176名の
製造業ご担当者様が閲覧しています*
*2025年3月31日現在のGoogle Analyticsのデータより
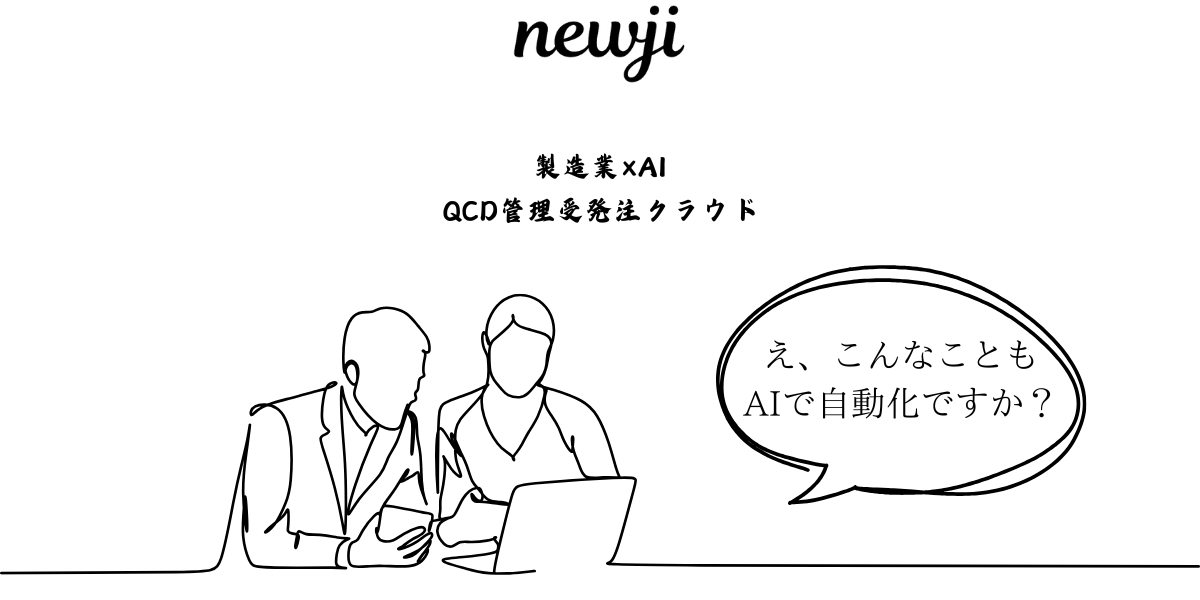
Case Studies: Solving〇〇Challenges with Japanese Manufacturing Expertise
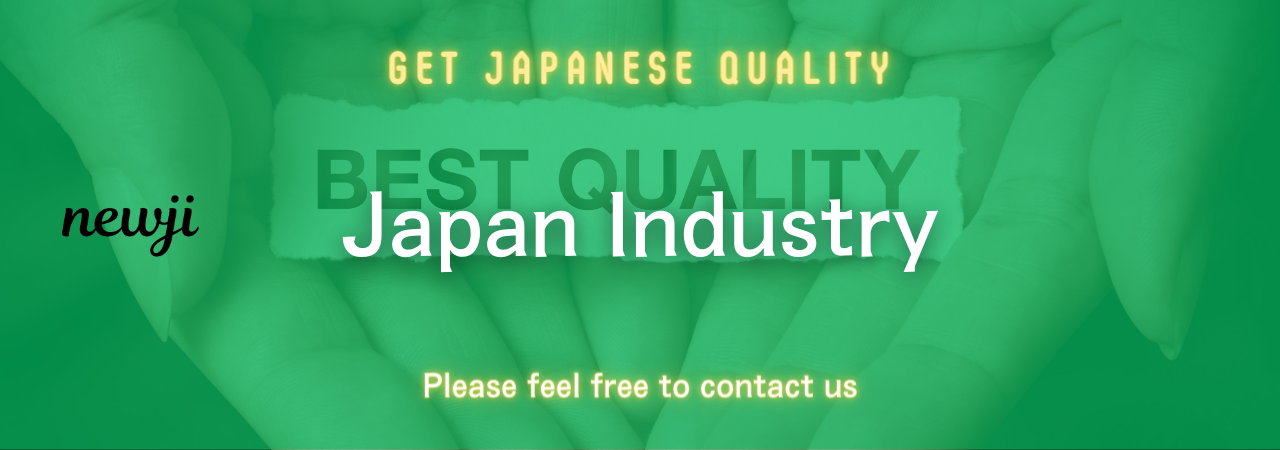
Japanese manufacturing has long held a reputation for excellence, innovation, and precision. Over decades, this reputation has built a strong foundation for Japanese firms, allowing them to tackle a wide range of challenges across various industries. Case studies demonstrate just how dynamic and effective Japanese manufacturing expertise can be in solving complex problems. From automotive advancements to healthcare improvements, let’s explore how Japanese companies apply their unique skills to achieve remarkable results.
Automotive Industry: Enhancing Safety and Efficiency
Japan’s automotive sector is a cornerstone of the country’s manufacturing landscape. Companies like Toyota and Honda have set industry standards for both safety and efficiency. A notable case study involves Toyota’s development of the Toyota Production System (TPS), a methodology aimed at improving manufacturing efficiencies and reducing waste. This approach, often referred to as “lean manufacturing,” has revolutionized automobile production worldwide.
For example, Toyota faced significant challenges in balancing cost-efficiency with high-quality production. By implementing TPS, they introduced just-in-time manufacturing and jidoka, or automation with a human touch. These principles ensure that every part is available precisely when needed, reducing inventory costs and enhancing production flow. Remarkably, this system has propelled Toyota to be one of the most reliable and cost-effective automakers in the world.
Electronics Industry: Innovating the Future
Another pillar of Japanese manufacturing success is its electronics industry. Companies like Sony, Panasonic, and Sharp have consistently delivered breakthroughs that reshape how we live. A significant case study is Sony’s PlayStation series. Initially, Sony faced the formidable challenge of entering a market dominated by established players like Nintendo and Sega.
However, by leveraging their manufacturing prowess and innovative designs, Sony introduced the first PlayStation, which featured superior graphics and a sophisticated CD-ROM format. This technological advancement not only captivated gamers but set new standards in the gaming industry. Today, the PlayStation brand is synonymous with cutting-edge technology and immersive gaming experiences.
Healthcare: Precision and Reliability
In the medical field, Japanese manufacturers also shine brightly. Case studies in healthcare demonstrate the prowess of companies like Terumo and Olympus in delivering medical equipment that prioritizes precision and reliability. Terumo, for instance, played a critical role in improving blood management systems with their innovative syringe technology.
Their challenge lay in reducing contamination and improving the accuracy of blood sample collection. By focusing on state-of-the-art materials and rigorous manufacturing processes, Terumo developed syringes that significantly minimized contamination risks, enhancing patient safety. This innovation underscores the vital role Japanese expertise plays in healthcare advancements.
Aerospace: Soaring High with Technology
Japan’s foray into the aerospace industry further exemplifies manufacturing excellence. Mitsubishi Heavy Industries (MHI) provides a compelling case study with their development of the Mitsubishi Regional Jet (MRJ). The challenge here was to create an aircraft that was both highly fuel-efficient and comfortable for passengers, in a market traditionally dominated by American and European manufacturers.
Through meticulous design and advanced manufacturing techniques, MHI achieved these objectives. The MRJ boasts a revolutionary engine design and aerodynamics that decrease fuel consumption and reduce noise, making it an attractive option for airlines worldwide. This project highlights how Japanese manufacturing acumen extends into highly specialized and competitive fields like aerospace.
Robotics: Pioneering Tomorrow’s Technology
Japan is also synonymous with advancements in robotics, a field where precision and innovation are paramount. Companies like FANUC and SoftBank Robotics are at the forefront of developing robots for various applications, from industrial automation to customer service.
A notable case study involves FANUC’s industrial robots, which are instrumental in manufacturing environments around the globe. These robots address challenges like increasing production efficiency and ensuring high precision in tasks like welding, assembly, and material handling. By integrating advanced sensors and AI technologies, FANUC creates robots that not only improve productivity but also ensure consistent, high-quality output. This is particularly vital in sectors that demand unwavering precision, such as electronics and automotive manufacturing.
Sustainability: Leading the Green Movement
Japanese manufacturers are also making significant strides in sustainability, addressing global environmental challenges with innovative solutions. Toyota’s introduction of hybrid technology through the Prius model is a landmark case study. Faced with growing concerns over fossil fuel emissions and environmental sustainability, Toyota pioneered the mass market hybrid vehicle.
The Prius combined traditional internal combustion engines with electric propulsion, drastically reducing emissions and fuel consumption. This breakthrough not only cemented Toyota’s leadership in the green vehicle movement but also inspired other automakers to follow suit, fostering a more sustainable global automotive industry.
Conclusion: The Legacy of Japanese Manufacturing
The case studies outlined illustrate that Japanese manufacturing expertise is not confined to one industry but spans multiple sectors, each facing unique challenges. From automotive and electronics to healthcare, aerospace, and robotics, Japanese firms continuously exemplify excellence through innovation, precision, and a commitment to quality.
This extensive expertise positions Japan as a global leader in solving intricate manufacturing challenges. By focusing on efficiency, sustainability, and cutting-edge technology, Japanese manufacturers not only drive their industries forward but also contribute significantly to global advancements. Through relentless innovation and rigorous standards, Japan’s manufacturing legacy continues to shape the future, setting benchmarks for quality and reliability worldwide.
資料ダウンロード
QCD管理受発注クラウド「newji」は、受発注部門で必要なQCD管理全てを備えた、現場特化型兼クラウド型の今世紀最高の受発注管理システムとなります。
ユーザー登録
受発注業務の効率化だけでなく、システムを導入することで、コスト削減や製品・資材のステータス可視化のほか、属人化していた受発注情報の共有化による内部不正防止や統制にも役立ちます。
NEWJI DX
製造業に特化したデジタルトランスフォーメーション(DX)の実現を目指す請負開発型のコンサルティングサービスです。AI、iPaaS、および先端の技術を駆使して、製造プロセスの効率化、業務効率化、チームワーク強化、コスト削減、品質向上を実現します。このサービスは、製造業の課題を深く理解し、それに対する最適なデジタルソリューションを提供することで、企業が持続的な成長とイノベーションを達成できるようサポートします。
製造業ニュース解説
製造業、主に購買・調達部門にお勤めの方々に向けた情報を配信しております。
新任の方やベテランの方、管理職を対象とした幅広いコンテンツをご用意しております。
お問い合わせ
コストダウンが利益に直結する術だと理解していても、なかなか前に進めることができない状況。そんな時は、newjiのコストダウン自動化機能で大きく利益貢献しよう!
(β版非公開)