- お役立ち記事
- Case study of digitalization of procurement process recommended by purchasing department
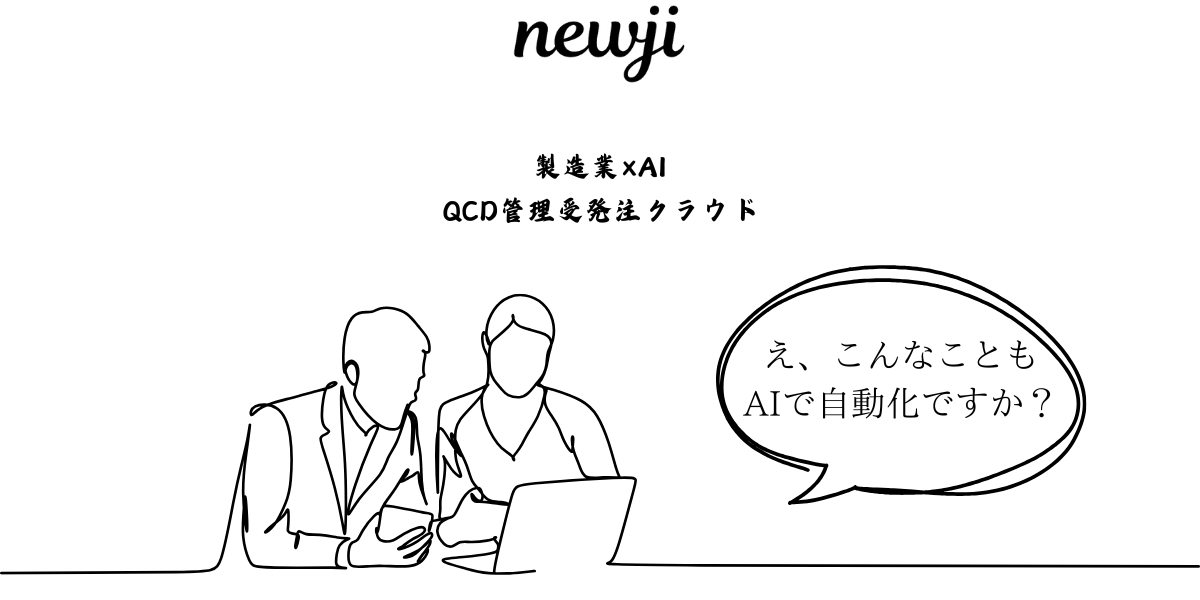
Case study of digitalization of procurement process recommended by purchasing department
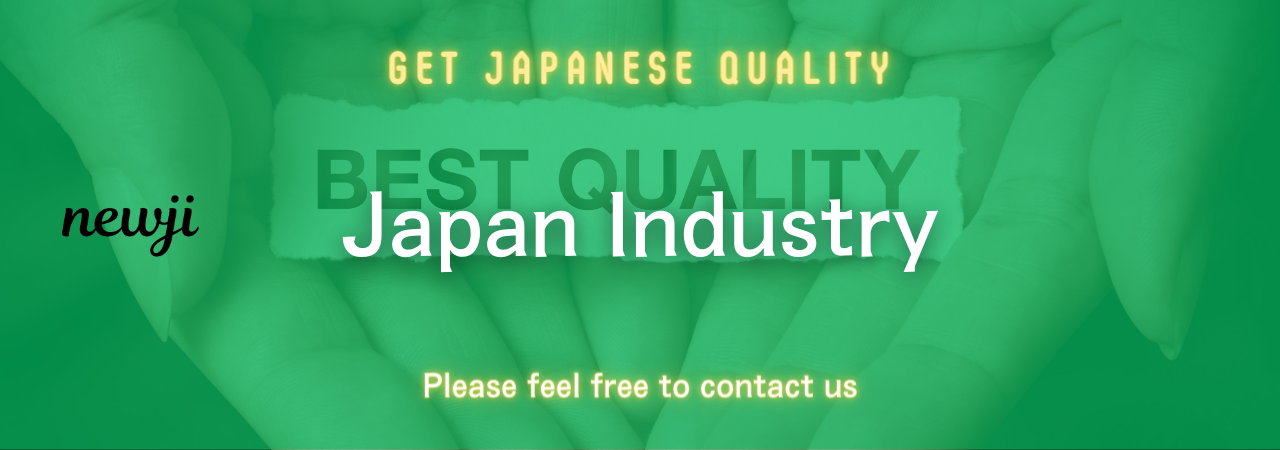
目次
Introduction to Procurement Process Digitalization
In today’s rapidly evolving business landscape, digitalization has become a crucial component of efficiency and competitiveness.
Procurement processes, traditionally seen as paper-driven and time-consuming, are now being transformed through digital tools and technologies.
This change not only streamlines operations but also enhances transparency, reduces costs, and improves supplier relationships.
In this article, we will explore a case study of digitalizing the procurement process, as recommended by the purchasing department, highlighting the benefits and steps involved.
The Need for Digitalization in Procurement
As companies grow, so does the complexity of their procurement needs.
Managing vendor relationships, purchasing orders, and inventory levels with outdated methods can lead to inefficiencies and increased errors.
Digitalizing the procurement process addresses these challenges by automating and optimizing tasks.
This transformation is not just a trend but a necessity for maintaining a competitive edge in the market.
Digital tools allow companies to manage their procurement activities more effectively, saving time and resources in the long run.
Benefits of Digitalizing Procurement
There are several benefits to embracing digitalization in procurement:
1. **Increased Efficiency**: Automation reduces the manual effort required for repetitive tasks, speeding up the entire procurement cycle.
2. **Enhanced Accuracy**: Digital systems lessen the risk of human error by ensuring data consistency and reliability.
3. **Cost Savings**: By optimizing processes and improving supplier negotiations, companies can significantly reduce costs.
4. **Improved Transparency**: Digital platforms offer better visibility into procurement activities, facilitating compliance and decision-making.
5. **Agility and Scalability**: Businesses can quickly adapt to changes in supply chain dynamics and scale operations as needed, thanks to digital tools.
Case Study: Digitalization Initiative by a Leading Company
Let us take a closer look at a case study of a leading manufacturing company that successfully implemented a digital procurement strategy with the support of its purchasing department.
Background
The company, faced with an expanding operation and a growing number of suppliers, identified its procurement process as a bottleneck.
Frequent delays, manual errors, and increased procurement costs were hindering productivity.
The purchasing department advocated for the digitalization of procurement to address these issues and enhance the overall efficiency and transparency of the operation.
Initiative Implementation
The company embarked on its digitalization journey by following a structured plan:
1. **Assessment and Goal Setting**: They began by assessing their current procurement processes to identify areas needing improvement and establishing clear digitalization goals.
2. **Technology Selection**: The team researched and selected a cloud-based procurement platform that suited their needs, offering features such as automated purchase orders, vendor management, and real-time analytics.
3. **Training and Change Management**: Staff members were trained to use the new system, with change management strategies implemented to ease the transition and encourage adoption.
4. **Integration with Existing Systems**: The new procurement platform was integrated with existing ERP and financial systems to ensure seamless data sharing and process continuity.
5. **Pilot Program and Feedback**: A pilot program was launched to test the new system in a controlled environment, gathering feedback and making necessary adjustments before full-scale implementation.
Results and Impact
The digitalization of the procurement process led to significant positive outcomes for the company:
1. **Time Savings**: Procurement cycle times were reduced by 30%, allowing teams to focus on strategic activities rather than manual processes.
2. **Cost Reduction**: The company reported a 20% reduction in procurement costs due to improved supplier negotiations and optimized ordering.
3. **Improved Supplier Relationships**: Enhanced communication and collaboration tools helped strengthen ties with key suppliers, fostering better terms and reliable deliveries.
4. **Increased Transparency and Control**: The new system provided comprehensive visibility into procurement activities, enabling better compliance and audit readiness.
Conclusion and Recommendations
The case study clearly illustrates that digitalizing procurement processes can drive significant improvements in efficiency, cost management, and supplier relationships.
Companies considering a similar initiative should invest in the right technology, prioritize training and change management, and focus on integrating systems to maximize benefits.
The purchasing department plays a critical role in spearheading such digital transformations, ensuring that businesses stay competitive and prepared for future challenges.
資料ダウンロード
QCD調達購買管理クラウド「newji」は、調達購買部門で必要なQCD管理全てを備えた、現場特化型兼クラウド型の今世紀最高の購買管理システムとなります。
ユーザー登録
調達購買業務の効率化だけでなく、システムを導入することで、コスト削減や製品・資材のステータス可視化のほか、属人化していた購買情報の共有化による内部不正防止や統制にも役立ちます。
NEWJI DX
製造業に特化したデジタルトランスフォーメーション(DX)の実現を目指す請負開発型のコンサルティングサービスです。AI、iPaaS、および先端の技術を駆使して、製造プロセスの効率化、業務効率化、チームワーク強化、コスト削減、品質向上を実現します。このサービスは、製造業の課題を深く理解し、それに対する最適なデジタルソリューションを提供することで、企業が持続的な成長とイノベーションを達成できるようサポートします。
オンライン講座
製造業、主に購買・調達部門にお勤めの方々に向けた情報を配信しております。
新任の方やベテランの方、管理職を対象とした幅広いコンテンツをご用意しております。
お問い合わせ
コストダウンが利益に直結する術だと理解していても、なかなか前に進めることができない状況。そんな時は、newjiのコストダウン自動化機能で大きく利益貢献しよう!
(Β版非公開)