- お役立ち記事
- Case study of multinational procurement risk management promoted by purchasing department
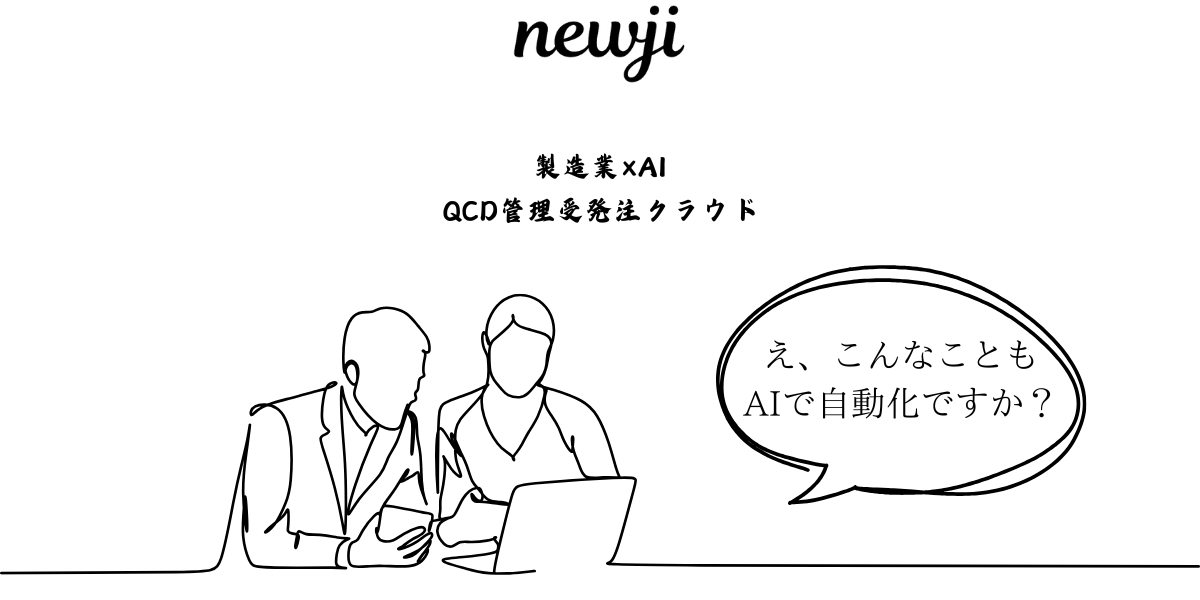
Case study of multinational procurement risk management promoted by purchasing department
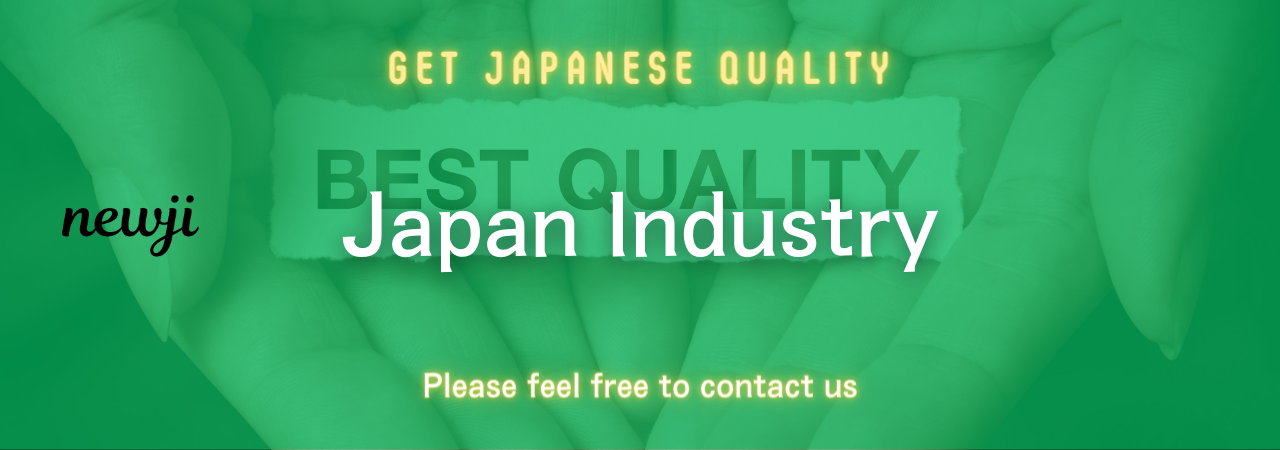
目次
Understanding Multinational Procurement Risk Management
In the global business environment, multinational corporations often encounter a myriad of challenges when sourcing goods and services from different countries.
Procurement risk management plays a crucial role in ensuring that these organizations can operate smoothly and efficiently.
The purchasing department, responsible for acquiring goods and services, is at the forefront of this risk management process.
Understanding the complexities and nuances of multinational procurement risk management can help organizations mitigate risks and capitalize on opportunities.
Key Risks in Multinational Procurement
Multinational procurement involves several risks that need to be carefully managed.
These risks can be broadly categorized into a few main areas:
1. Supply Chain Disruptions
Supply chain disruptions can arise from various factors such as natural disasters, political instability, and transportation issues.
These disruptions can lead to delays in delivery, increased costs, and ultimately affect the company’s ability to meet customer demand.
Effective risk management requires identifying potential disruption points and developing contingency plans to address them.
2. Currency Fluctuations
Dealing with suppliers in multiple countries means dealing with different currencies.
Currency fluctuations can significantly impact the cost of goods and services, thereby affecting the overall procurement budget.
Purchasing departments must monitor exchange rates and use hedging strategies to mitigate the impact of adverse currency movements.
3. Regulatory and Compliance Risks
Different countries have different regulations and compliance requirements, which can pose challenges for procurement professionals.
Failing to adhere to these regulations can result in fines, legal issues, and damage to a company’s reputation.
It is essential to stay informed about local laws and work closely with legal experts to ensure compliance.
4. Supplier Risks
Supplier-related risks include the possibility of a supplier failing to deliver goods or providing subpar quality.
Evaluating supplier reliability, financial stability, and performance history are critical components of managing supplier risk.
Developing strong relationships with suppliers and conducting regular evaluations can reduce the likelihood of supplier-related issues.
The Role of the Purchasing Department
The purchasing department plays a vital role in managing multinational procurement risks.
By implementing effective strategies, the department can ensure the continuity of supply, control costs, and maintain quality standards.
1. Strategic Sourcing
Strategic sourcing involves evaluating and selecting suppliers based on a comprehensive assessment of their capabilities, cost structures, and risk factors.
The purchasing department can utilize data analytics and market intelligence to make informed decisions about supplier selection.
This approach helps to build a resilient supplier network that can withstand various challenges.
2. Leveraging Technology
Technological advancements have revolutionized procurement processes.
Purchasing departments can use procurement software to automate and streamline their operations, facilitating better risk management.
Technologies such as blockchain can enhance transparency and traceability, reducing the chances of fraud and other unethical practices.
3. Establishing Risk Mitigation Strategies
To effectively manage risks in multinational procurement, the purchasing department needs to establish comprehensive risk mitigation strategies.
These strategies should include contingency plans, supplier diversification, and insurance coverage for unforeseen events.
Regular training and development for procurement professionals can also enhance their ability to identify and respond to emerging risks.
Case Study: An Example of Successful Procurement Risk Management
To illustrate the importance of procurement risk management, let’s consider a case study of a multinational corporation in the automotive industry.
Background
Company XYZ, a leading automotive manufacturer, sources components from suppliers in over 20 countries.
The company faced several procurement challenges, including fluctuating raw material prices, geopolitical tensions, and environmental regulations.
Approach
To address these challenges, Company XYZ’s purchasing department implemented a robust risk management framework.
They utilized data analytics tools to forecast price trends and negotiated long-term contracts with key suppliers to lock in prices.
In dealing with geopolitical risks, the company diversified its supplier base, ensuring that they were not overly reliant on suppliers from politically volatile regions.
Additionally, they collaborated with legal experts to stay updated on environmental regulations in each sourcing country.
Outcome
As a result of these strategic risk management practices, Company XYZ was able to maintain a steady supply of components, minimize cost fluctuations, and comply with global regulations.
The purchasing department’s proactive approach to risk management played a crucial role in the company’s continued success in the competitive automotive industry.
Conclusion: The Necessity of Proactive Risk Management
In today’s interconnected world, multinational procurement risk management is an essential aspect for any global business.
The purchasing department’s role is critical in ensuring that an organization can navigate complexities and uncertainties to maintain a competitive edge.
By understanding and addressing key procurement risks, leveraging technology, and establishing strategic partnerships, companies can safeguard their operations against potential disruptions.
Ultimately, proactive procurement risk management enables organizations to seize opportunities and thrive in the global market.
資料ダウンロード
QCD調達購買管理クラウド「newji」は、調達購買部門で必要なQCD管理全てを備えた、現場特化型兼クラウド型の今世紀最高の購買管理システムとなります。
ユーザー登録
調達購買業務の効率化だけでなく、システムを導入することで、コスト削減や製品・資材のステータス可視化のほか、属人化していた購買情報の共有化による内部不正防止や統制にも役立ちます。
NEWJI DX
製造業に特化したデジタルトランスフォーメーション(DX)の実現を目指す請負開発型のコンサルティングサービスです。AI、iPaaS、および先端の技術を駆使して、製造プロセスの効率化、業務効率化、チームワーク強化、コスト削減、品質向上を実現します。このサービスは、製造業の課題を深く理解し、それに対する最適なデジタルソリューションを提供することで、企業が持続的な成長とイノベーションを達成できるようサポートします。
オンライン講座
製造業、主に購買・調達部門にお勤めの方々に向けた情報を配信しております。
新任の方やベテランの方、管理職を対象とした幅広いコンテンツをご用意しております。
お問い合わせ
コストダウンが利益に直結する術だと理解していても、なかなか前に進めることができない状況。そんな時は、newjiのコストダウン自動化機能で大きく利益貢献しよう!
(Β版非公開)