- お役立ち記事
- Case study of product life cycle cost reduction project supported by purchasing department
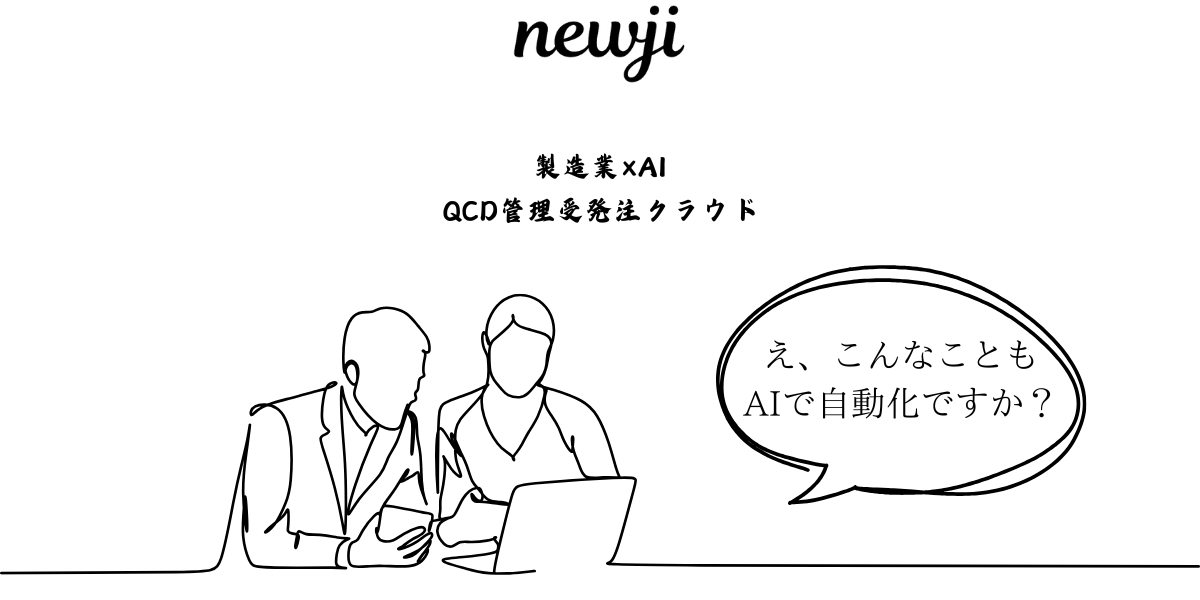
Case study of product life cycle cost reduction project supported by purchasing department
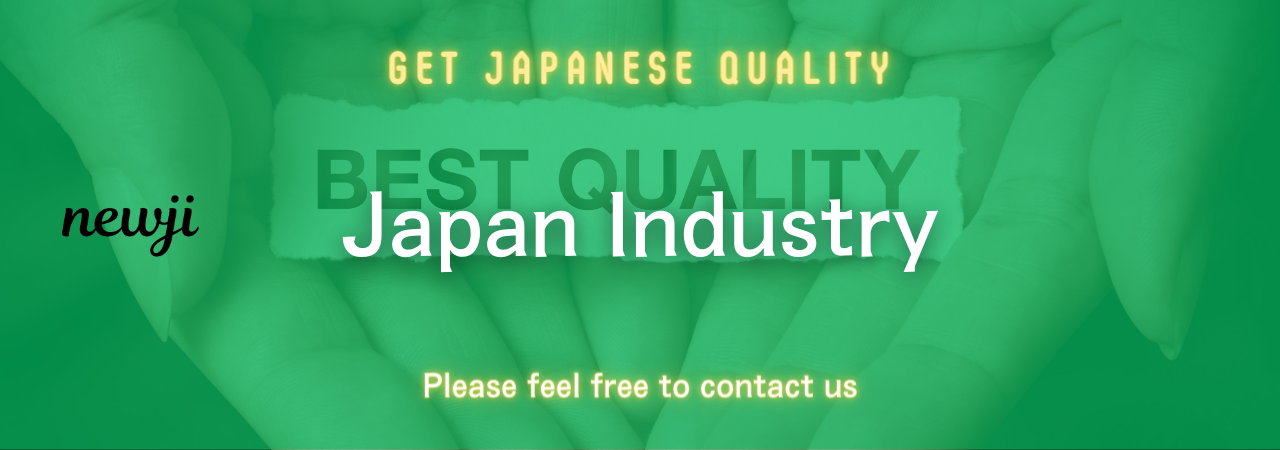
目次
Understanding Product Life Cycle Costs
The concept of product life cycle costs is crucial in understanding how a product develops from inception to withdrawal from the market.
These costs encompass everything from the initial research and development phase, through production and marketing, to eventual decline and disposal.
Each stage involves different expenses, which collectively determine the total cost of a product’s life cycle.
Reducing these costs without compromising on quality or performance is a critical aspect that companies strive to achieve.
By focusing on cost efficiency throughout the product’s life span, businesses can enhance their competitive edge and profitability.
The Role of the Purchasing Department
The purchasing department plays a vital role in managing and reducing product life cycle costs.
As the central hub for procurement and supplier relationships, this department is pivotal in negotiating better prices and securing quality materials, which directly impact costs.
By taking a strategic approach, the purchasing team can significantly influence the cost efficiency of a product.
Their involvement in cost management extends beyond price negotiation to include reducing waste and ensuring sustainable purchasing practices.
A collaborative approach with other departments, such as research and development, ensures that cost-saving measures are integrated from the earliest stages of the product life cycle.
Effective Supplier Relationship Management
Developing strong relationships with suppliers is an essential strategy for cost reduction.
By fostering open and cooperative relationships, the purchasing department can negotiate better terms, such as bulk discounts or preferential payment terms.
Strong relationships also allow for better communication channels, leading to more timely problem resolution.
Suppliers who feel valued and part of the process might offer insights into cost-saving opportunities or innovations that could further enhance product life cycle cost efficiency.
Case Study Overview
A comprehensive study was conducted on a product life cycle cost reduction project, where the purchasing department executed several strategies to minimize costs.
The project spanned various stages of the product life cycle, from raw material sourcing to production and beyond.
The objective was to identify areas where cost savings could be implemented without sacrificing the quality or integrity of the product.
Through strategic planning and execution, the company aimed to streamline processes and achieve a noteworthy reduction in overall expenses.
Phase 1: Raw Material Optimization
The first phase of the project focused on optimizing raw material costs.
By evaluating existing suppliers and identifying alternative sources, the purchasing department was able to secure better deals and reduce material costs significantly.
Additionally, bulk purchasing strategies were employed, leading to substantial savings.
Innovative agreements with suppliers were formed, allowing for flexible delivery schedules and just-in-time inventory management, further reducing storage and handling costs.
Phase 2: Production Efficiency
In the production phase, the focus was on improving manufacturing efficiency.
The purchasing department collaborated closely with production managers to identify equipment and processes that were due for upgrades or efficiency improvements.
Investments in newer, more efficient machinery were made, reducing waste and cutting down on energy consumption.
Process optimization techniques were also implemented, resulting in shorter production times and less material wastage.
Phase 3: Distribution and Logistics
The third phase concentrated on optimizing distribution and logistics.
A review of the existing distribution network was conducted, leading to the consolidation of shipping routes and leveraging of distribution partnerships.
By switching to more strategic shipping partners, costs related to logistics were reduced while delivery times and reliability improved.
The focus on logistics efficiency additionally lowered carbon footprints, aligning with the company’s sustainability goals.
Challenges Encountered
While the project achieved significant cost reductions, several challenges were encountered along the way.
One major hurdle was resistance to change within the organization, as some stakeholders were concerned about the impact of cost-cutting measures on product quality and performance.
To address these concerns, continuous stakeholder engagement and transparent communication of project goals and achievements were vital.
Another challenge was finding the right balance between cost reduction and maintaining supplier relationships, as aggressive cost-cutting could strain key partnerships.
Results and Benefits
Upon completion of the project, the company realized considerable savings in product life cycle costs.
Not only did this lead to enhanced profitability, but it also created value for customers through affordable pricing without compromising quality.
Moreover, the strategies implemented provided long-term benefits, including streamlined operations and strengthened supplier partnerships.
The project also fostered a culture of continuous improvement within the organization, instilling an ongoing focus on cost efficiency.
Conclusion
In summary, the purchasing department’s pivotal role in reducing product life cycle costs cannot be overstated.
Through strategic supplier management, process optimization, and cost-effective logistics planning, the department can drive significant cost improvements.
The case study highlights the importance of a holistic approach, where every phase of the product life cycle is considered for potential efficiencies.
These initiatives not only enhance financial performance but also establish a foundation for sustainable business practices.
資料ダウンロード
QCD調達購買管理クラウド「newji」は、調達購買部門で必要なQCD管理全てを備えた、現場特化型兼クラウド型の今世紀最高の購買管理システムとなります。
ユーザー登録
調達購買業務の効率化だけでなく、システムを導入することで、コスト削減や製品・資材のステータス可視化のほか、属人化していた購買情報の共有化による内部不正防止や統制にも役立ちます。
NEWJI DX
製造業に特化したデジタルトランスフォーメーション(DX)の実現を目指す請負開発型のコンサルティングサービスです。AI、iPaaS、および先端の技術を駆使して、製造プロセスの効率化、業務効率化、チームワーク強化、コスト削減、品質向上を実現します。このサービスは、製造業の課題を深く理解し、それに対する最適なデジタルソリューションを提供することで、企業が持続的な成長とイノベーションを達成できるようサポートします。
オンライン講座
製造業、主に購買・調達部門にお勤めの方々に向けた情報を配信しております。
新任の方やベテランの方、管理職を対象とした幅広いコンテンツをご用意しております。
お問い合わせ
コストダウンが利益に直結する術だと理解していても、なかなか前に進めることができない状況。そんな時は、newjiのコストダウン自動化機能で大きく利益貢献しよう!
(Β版非公開)