- お役立ち記事
- Case study of purchasing department process review to promote procurement efficiency in the manufacturing industry
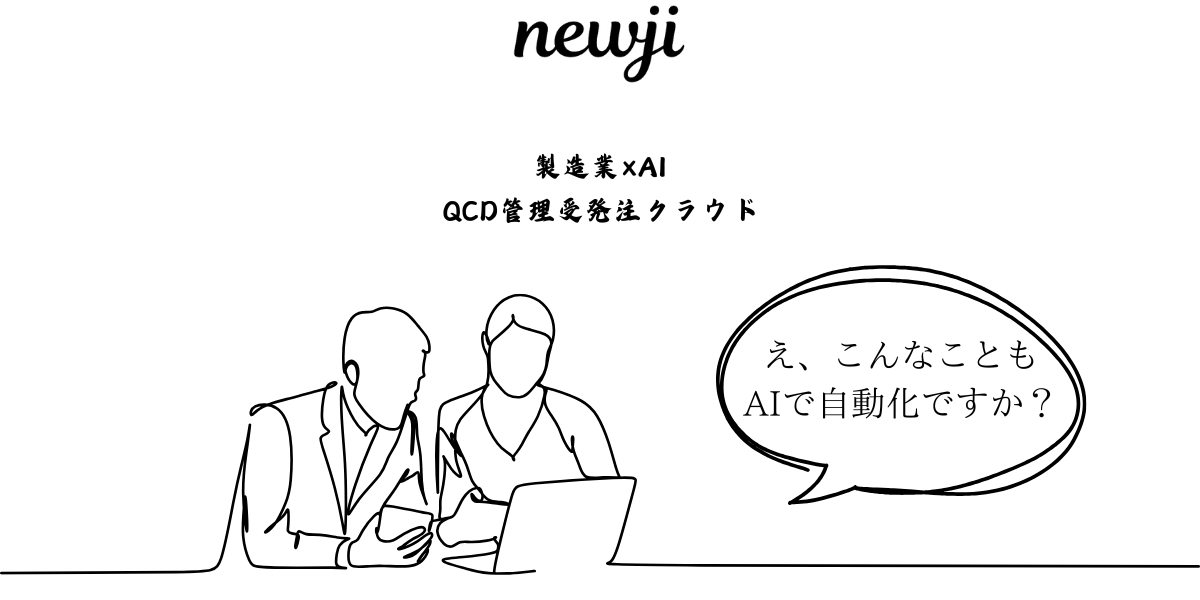
Case study of purchasing department process review to promote procurement efficiency in the manufacturing industry
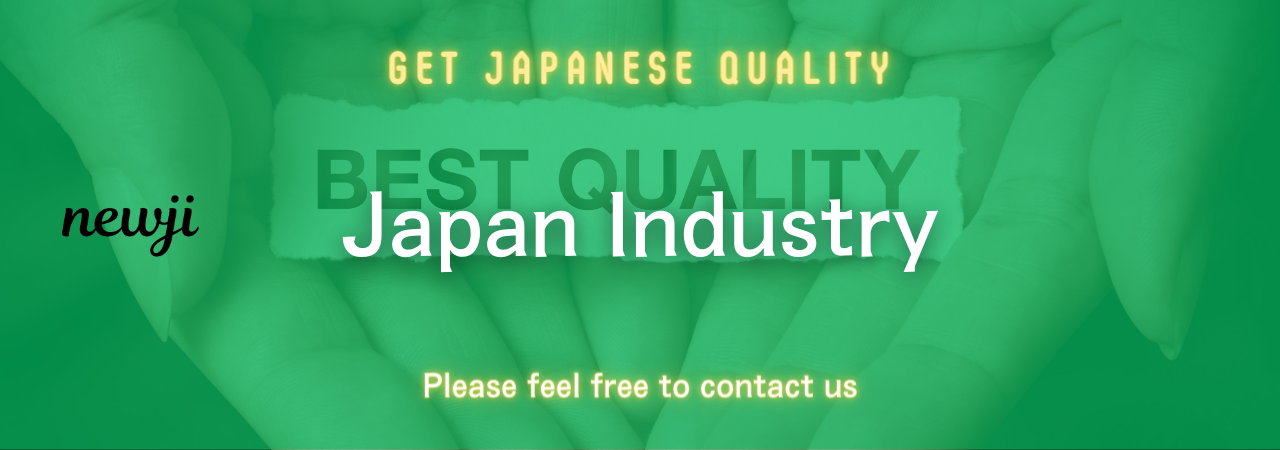
目次
Understanding the Importance of Procurement Efficiency
Efficient procurement processes are essential for the manufacturing industry.
They not only help in reducing costs but also in improving the overall productivity of the organization.
By reviewing and optimizing the purchasing department’s processes, companies can gain a competitive edge in the market.
In today’s fast-paced economy, it is crucial for manufacturing businesses to adapt and improve their procurement strategies to ensure long-term success.
Why Process Review is Necessary
The procurement process in manufacturing involves a series of activities, from sourcing raw materials to negotiating contracts with suppliers.
Over time, these activities may become fragmented or outdated, leading to inefficiencies and increased costs.
A thorough process review helps to identify these pain points and implement necessary improvements.
This not only streamlines operations but also enhances supplier relationships and ensures timely deliveries.
Steps Involved in Procurement Process Review
1. Evaluate Current Processes
The first step in reviewing the procurement process is to evaluate the existing procedures and practices.
This involves understanding how orders are placed, how suppliers are sourced, and how contracts are managed.
It is important to document each step of the process and gather feedback from employees involved in these activities.
2. Identify Bottlenecks and Inefficiencies
Once the current processes are documented, the next step is to identify any bottlenecks or inefficiencies.
This could be anything from lengthy approval times to communication gaps between departments.
Data analysis and employee interviews can be useful in pinpointing these issues.
The goal is to understand where time and resources are being wasted.
3. Set Clear Objectives
After identifying inefficiencies, it’s important to set clear, actionable objectives for improving the procurement process.
These objectives should align with the overall goals of the manufacturing company, such as reducing costs or improving turnaround times.
Setting measurable targets helps in tracking progress and ensuring accountability.
4. Implement Changes
With clear objectives in place, the next step is to implement the necessary changes to the procurement process.
This may involve introducing new technologies, such as procurement software, to automate repetitive tasks.
It could also mean revising supplier contracts or changing the way inventory is managed.
Whatever the changes, it’s crucial to communicate them effectively to all stakeholders.
5. Monitor and Review
The final step is to monitor the new processes and review their effectiveness regularly.
This involves tracking key performance indicators (KPIs) related to procurement efficiency, such as order accuracy and lead times.
Regular reviews help in identifying areas for further improvement and ensure that the benefits of the process changes are sustained over time.
Case Study: A Manufacturing Success Story
To understand the impact of procurement process review, let’s take a look at a hypothetical case study of a manufacturing company, “ABC Manufacturing.”
ABC Manufacturing was facing high procurement costs and frequent delays in receiving materials.
The company’s leadership decided to undertake a comprehensive review of their purchasing department’s processes.
Current Process Analysis
The analysis revealed that the company relied heavily on manual processes, which led to errors and delays.
There were also inconsistencies in supplier evaluation and a lack of clear communication channels between the procurement team and other departments.
Improvements Implemented
Based on the findings, ABC Manufacturing implemented several key changes.
First, they introduced procurement software to automate order placements and inventory management.
They also revised their supplier evaluation criteria, focusing on reliability and cost-effectiveness.
Additionally, they established regular communication meetings between the procurement team and other departments to ensure alignment and transparency.
Results Achieved
As a result of these changes, ABC Manufacturing saw a significant reduction in procurement costs and an improvement in order accuracy.
Supplier relationships improved, leading to more timely deliveries and better quality materials.
Moreover, the company’s overall efficiency increased, allowing them to meet customer demands more effectively.
Conclusion
A process review of the purchasing department can significantly enhance procurement efficiency in the manufacturing industry.
By identifying inefficiencies and implementing strategic improvements, companies can reduce costs, improve supplier relationships, and enhance overall productivity.
Regular monitoring and continuous improvement are key to sustaining these benefits over time.
Manufacturers looking to stay competitive must prioritize procurement process optimization as a core aspect of their operations.
資料ダウンロード
QCD調達購買管理クラウド「newji」は、調達購買部門で必要なQCD管理全てを備えた、現場特化型兼クラウド型の今世紀最高の購買管理システムとなります。
ユーザー登録
調達購買業務の効率化だけでなく、システムを導入することで、コスト削減や製品・資材のステータス可視化のほか、属人化していた購買情報の共有化による内部不正防止や統制にも役立ちます。
NEWJI DX
製造業に特化したデジタルトランスフォーメーション(DX)の実現を目指す請負開発型のコンサルティングサービスです。AI、iPaaS、および先端の技術を駆使して、製造プロセスの効率化、業務効率化、チームワーク強化、コスト削減、品質向上を実現します。このサービスは、製造業の課題を深く理解し、それに対する最適なデジタルソリューションを提供することで、企業が持続的な成長とイノベーションを達成できるようサポートします。
オンライン講座
製造業、主に購買・調達部門にお勤めの方々に向けた情報を配信しております。
新任の方やベテランの方、管理職を対象とした幅広いコンテンツをご用意しております。
お問い合わせ
コストダウンが利益に直結する術だと理解していても、なかなか前に進めることができない状況。そんな時は、newjiのコストダウン自動化機能で大きく利益貢献しよう!
(Β版非公開)