- お役立ち記事
- Case study of successful precision stainless steel cutting prototype production in Tainai City
月間76,176名の
製造業ご担当者様が閲覧しています*
*2025年3月31日現在のGoogle Analyticsのデータより
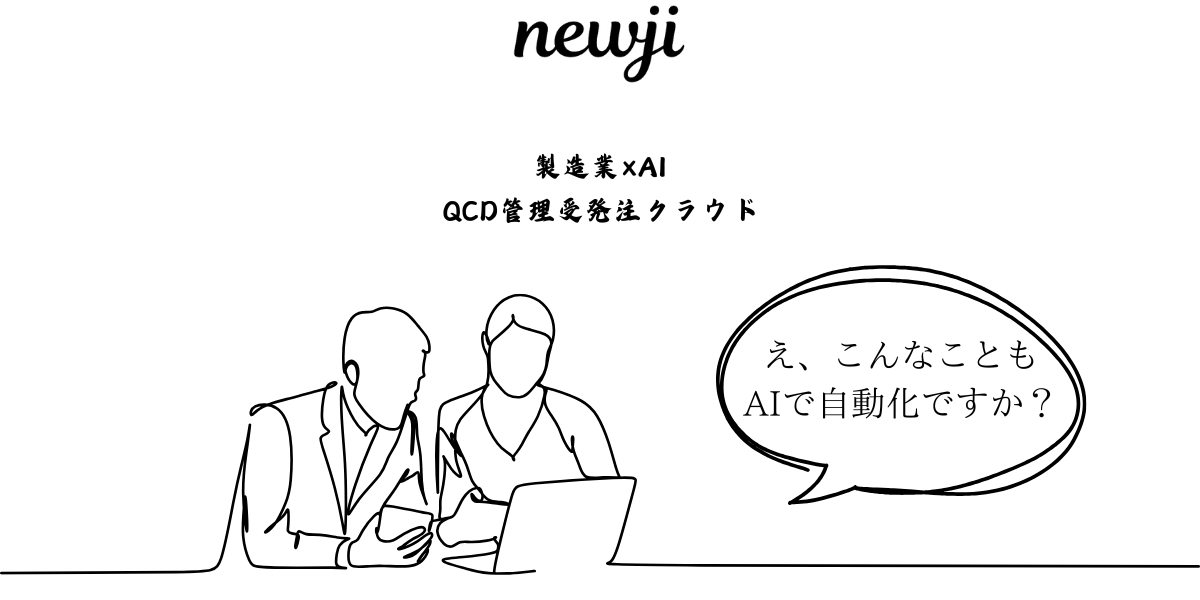
Case study of successful precision stainless steel cutting prototype production in Tainai City
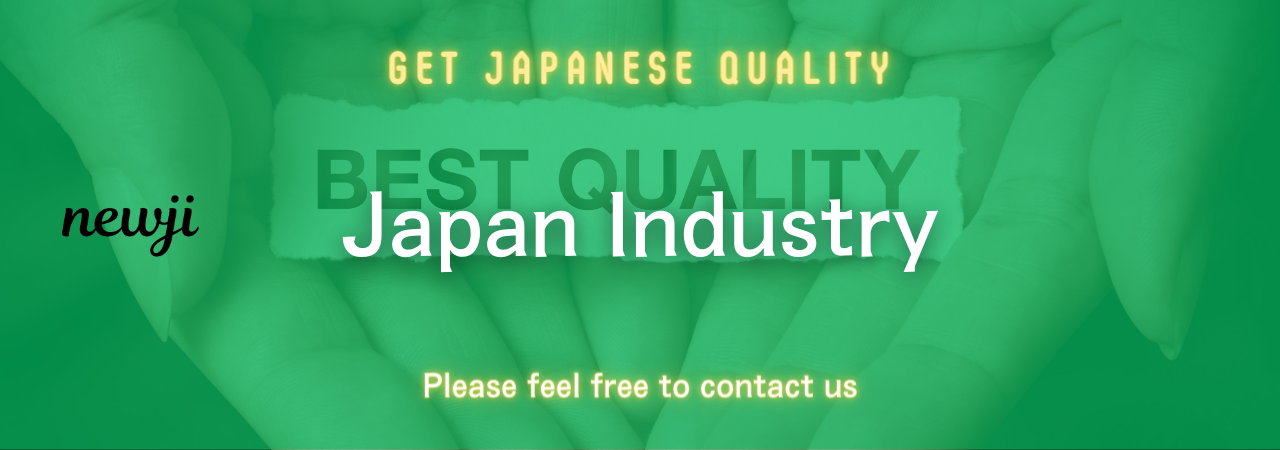
目次
Introduction to Precision Stainless Steel Cutting
Tainai City has become a notable hub for precision manufacturing and innovation, particularly in precision stainless steel cutting.
This city is home to various companies and workshops specializing in producing high-quality prototypes for industries like aerospace, automotive, and electronics.
This article will explore a successful case study of precision stainless steel cutting prototype production in Tainai City, examining the key factors and strategies that led to its success.
The Importance of Precision in Steel Cutting
Precision stainless steel cutting is critical for industries that demand accuracy and consistency.
Stainless steel is prized for its strength, resistance to corrosion, and aesthetic appeal, making it ideal for many applications.
However, working with stainless steel requires specialized tools and techniques to ensure precision.
Accurate cutting is crucial because it affects the functionality and longevity of the final product.
Understanding these elements is essential before diving into our case study.
Overview of the Case Study
In our case study, we analyze a local company in Tainai City that successfully produced a precision stainless steel cutting prototype for a sophisticated aerospace component.
The project’s success is attributed to the innovative application of technology, skilled labor, and efficient processes.
The Company Profile
The company at the center of this case study is Tainai Precision Engineering.
Founded in the late 1980s, this firm has established itself as a leader in precision metalwork with a focus on quality and innovation.
Over the years, Tainai Precision Engineering has attracted a team of highly skilled engineers and technicians who are adept at tackling challenging projects.
Project Goals and Objectives
The primary goal of the project was to develop a high-precision stainless steel prototype for an aerospace client.
The objectives included achieving tolerances within a few microns, minimizing material waste, and maintaining the aesthetic finish that the client specified.
Meeting these requirements necessitated a rigorous approach to both the design and manufacturing phases of the project.
Innovative Approaches to Stainless Steel Cutting
Tainai Precision Engineering utilized several cutting-edge technologies and approaches to achieve success with this prototype.
Advanced CNC Machines
A cornerstone of their strategy was the use of advanced Computer Numerical Control (CNC) machines.
These devices provided the precision needed for cutting stainless steel with micron-level accuracy.
CNC machines are known for their ability to replicate intricate designs consistently, which is crucial for aerospace components that require precise specifications.
Laser Cutting Technology
In addition to CNC machines, the company also employed state-of-the-art laser cutting technology.
This technology offered several advantages, including non-contact processing, minimal heat distortion, and the ability to cut complex geometries easily.
Laser cutting provided a precise, clean edge that met the aesthetic and functional requirements of the aerospace prototype.
Skilled Workforce
The expertise of Tainai Precision Engineering’s workforce was another pivotal factor in the project’s success.
The team consisted of technicians and engineers who had extensive experience with precision manufacturing.
Their ability to set up and operate the sophisticated machinery correctly ensured the project met its high standards.
Process Optimization and Quality Assurance
Process optimization and quality assurance played vital roles in ensuring the final product met all the required specifications.
Efficient Production Workflow
A streamlined production workflow allowed for efficient use of time and resources.
Automation and lean manufacturing principles reduced waste and increased productivity, enabling the company to complete the prototype on schedule.
Robust Quality Control Practices
Quality assurance was maintained through rigorous testing and inspection.
Every piece was rigorously assessed, using both manual inspection and automated precision measuring tools, to ensure it met the tight tolerances required by the aerospace industry.
Environmental and Safety Considerations
Environmental sustainability and worker safety are crucial aspects of modern manufacturing, and Tainai Precision Engineering incorporated these into their processes.
Eco-friendly Practices
The company implemented eco-friendly practices, such as recycling metal shavings and using water-based coolants, which are less harmful to the environment than petroleum-based products.
Safety Protocols
Worker safety was assured through strict adherence to safety protocols, including proper training, use of personal protective equipment, and maintaining a clean and organized workspace to prevent accidents.
Outcomes and Client Satisfaction
The results of this project were highly favorable, reflecting the benefits of a meticulous approach to precision manufacturing.
Client Feedback and Approval
The aerospace client was pleased with the final prototype.
Not only did it meet all technical specifications, but it also exceeded expectations in terms of finish and durability, establishing a strong potential for future collaborations.
Enhanced Reputation
The successful completion of this project enhanced Tainai Precision Engineering’s reputation as a leader in precision stainless steel cutting.
The case is now used as a benchmark within the industry, demonstrating how advanced technology and skilled labor can produce superior results.
Conclusion
The case study of successful precision stainless steel cutting prototype production in Tainai City illustrates the importance of combining technology, expertise, and process efficiency.
This model can serve as a guide for other companies striving to achieve excellence in precision manufacturing.
As industries continue to demand higher precision and quality, companies like Tainai Precision Engineering will play an essential role in meeting these challenges through innovation and dedication.
資料ダウンロード
QCD管理受発注クラウド「newji」は、受発注部門で必要なQCD管理全てを備えた、現場特化型兼クラウド型の今世紀最高の受発注管理システムとなります。
ユーザー登録
受発注業務の効率化だけでなく、システムを導入することで、コスト削減や製品・資材のステータス可視化のほか、属人化していた受発注情報の共有化による内部不正防止や統制にも役立ちます。
NEWJI DX
製造業に特化したデジタルトランスフォーメーション(DX)の実現を目指す請負開発型のコンサルティングサービスです。AI、iPaaS、および先端の技術を駆使して、製造プロセスの効率化、業務効率化、チームワーク強化、コスト削減、品質向上を実現します。このサービスは、製造業の課題を深く理解し、それに対する最適なデジタルソリューションを提供することで、企業が持続的な成長とイノベーションを達成できるようサポートします。
製造業ニュース解説
製造業、主に購買・調達部門にお勤めの方々に向けた情報を配信しております。
新任の方やベテランの方、管理職を対象とした幅広いコンテンツをご用意しております。
お問い合わせ
コストダウンが利益に直結する術だと理解していても、なかなか前に進めることができない状況。そんな時は、newjiのコストダウン自動化機能で大きく利益貢献しよう!
(β版非公開)