- お役立ち記事
- Case study of successful prototype welding of high heat-resistant stainless steel in Yota Village
月間77,185名の
製造業ご担当者様が閲覧しています*
*2025年2月28日現在のGoogle Analyticsのデータより
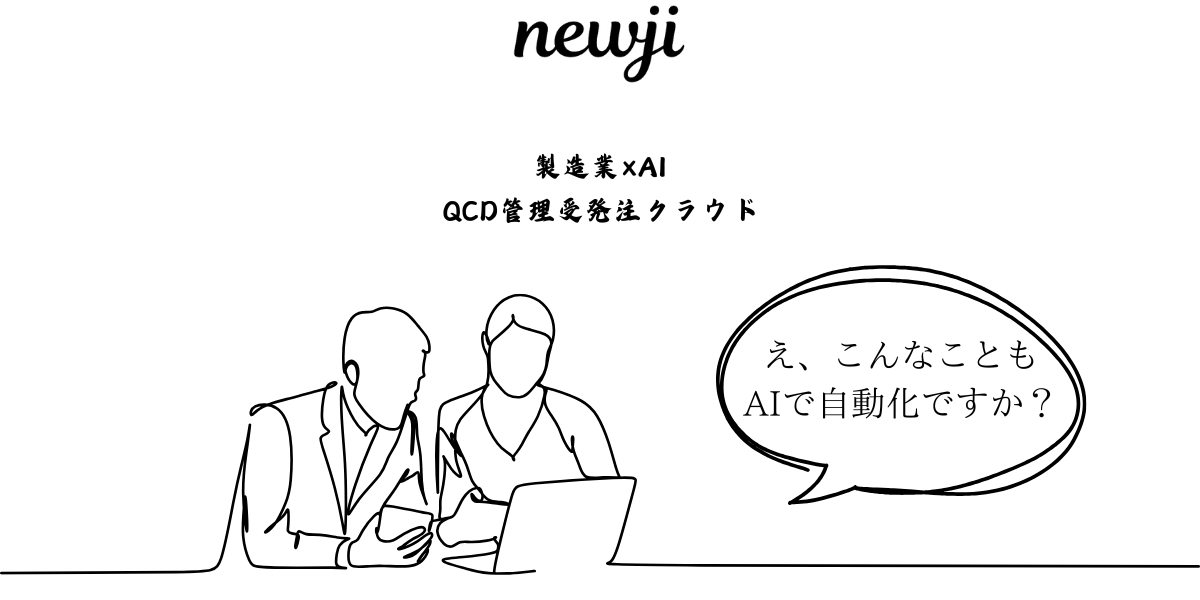
Case study of successful prototype welding of high heat-resistant stainless steel in Yota Village
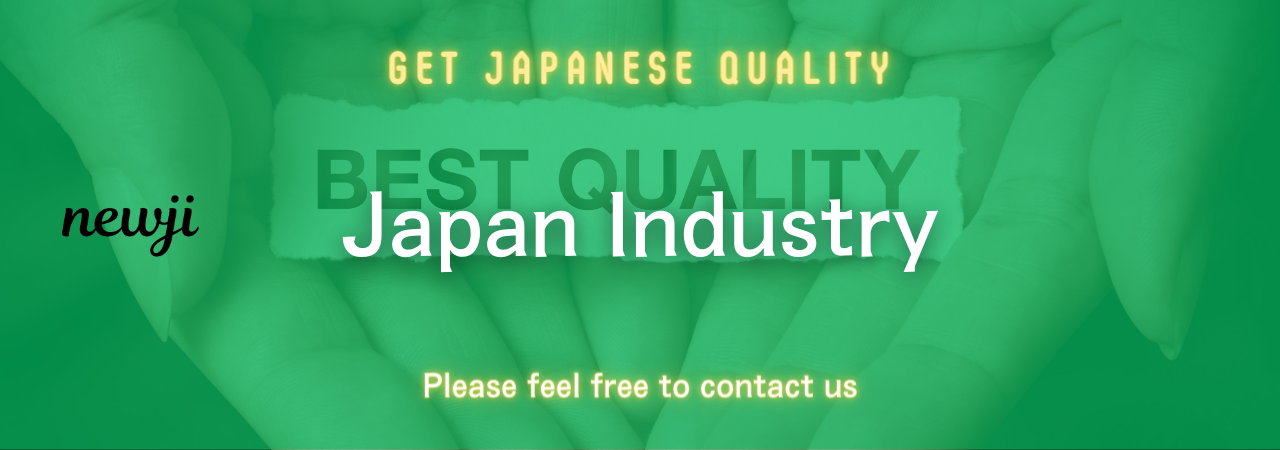
目次
Understanding Stainless Steel Welding
Stainless steel is a popular material in various industries due to its durability, corrosion resistance, and aesthetic appeal.
Welding stainless steel, however, requires special skills and knowledge to maintain its structural integrity.
Different grades of stainless steel have unique properties that need to be considered during the welding process.
In the case study from Yota Village, a prototype was successfully welded using high heat-resistant stainless steel.
This accomplishment highlights the importance of understanding the properties and challenges associated with welding this type of material.
The Challenges of Welding High Heat-Resistant Stainless Steel
High heat-resistant stainless steel is designed to withstand extreme temperatures without losing its strength or corrosion resistance.
This makes it an ideal choice for industries such as aerospace, automotive, and chemical processing.
However, the very properties that make this type of stainless steel appealing also pose significant challenges during the welding process.
One of the major challenges is maintaining the material’s heat resistance during welding.
Excessive heat can lead to oxidation, which compromises the corrosion resistance of the stainless steel.
The welding process must be carefully controlled to prevent melting or warping, which can alter the material’s structural properties.
Another challenge is dealing with the thermal expansion of the material.
High heat-resistant stainless steel can expand and contract significantly during welding, leading to distortion or cracking if not properly managed.
Welders must use precise techniques to ensure that the joints remain strong and the overall structure is maintained.
Planning the Prototype Welding Project
Before beginning the welding process in Yota Village, a detailed plan was developed to address the specific challenges of high heat-resistant stainless steel.
The plan included selecting the appropriate welding method, preparing the materials, and implementing quality control measures throughout the project.
The choice of welding method is critical to achieving a successful weld.
Techniques such as tungsten inert gas (TIG) welding and laser welding are often preferred for high heat-resistant stainless steel due to their precision and control.
These methods allow welders to focus the heat precisely, minimizing the risk of oxidation and distortion.
Material preparation is another key aspect of the planning process.
The surfaces that will be welded must be thoroughly cleaned and prepped to remove any contaminants that could affect the quality of the weld.
In some cases, special coatings or treatments may be applied to enhance the material’s heat resistance during welding.
Finally, quality control measures were established to monitor the welding process and ensure that the prototype met the necessary standards.
This included regular inspections, testing of weld joints, and thorough documentation of the entire process.
Executing the Weld in Yota Village
With a comprehensive plan in place, the team in Yota Village began the welding process.
Experienced welders, well-versed in the challenges of high heat-resistant stainless steel, were selected to carry out the work.
Their skills and knowledge were crucial in executing a successful prototype weld.
The use of TIG welding was instrumental in ensuring precision and control.
The welders carefully monitored the heat input to avoid compromising the stainless steel’s properties.
Special procedures were implemented to manage the thermal expansion of the material, allowing the welds to remain stable despite temperature fluctuations.
The result was a flawlessly welded prototype that maintained its structural integrity and heat-resistant properties.
This was achieved through meticulous planning, skilled execution, and constant attention to detail.
The Impact of the Successful Prototype
The successful welding of high heat-resistant stainless steel in Yota Village has significant implications for various industries.
It demonstrates the potential for creating robust, durable structures capable of withstanding high temperatures and corrosion, a critical requirement in many modern applications.
This achievement also provides valuable insights into best practices for welding high heat-resistant stainless steel.
The case study offers a framework for other welding projects, emphasizing the importance of planning, precise technique, and quality assurance.
Industries that rely on stainless steel structures can draw from this example to enhance their processes, ultimately leading to more reliable and efficient products.
The insights gained from this project may also inspire further research and innovation in the field of stainless steel welding.
Lessons Learned from Yota Village
One of the key lessons from the successful prototype welding in Yota Village is the importance of collaboration and expertise.
Bringing together skilled welders, engineers, and planners was crucial in overcoming the challenges posed by high heat-resistant stainless steel.
Each team member contributed invaluable knowledge and experience, resulting in a cohesive and effective execution.
Another important takeaway is the need for ongoing quality control and testing throughout the welding process.
Ensuring that each step meets high standards of quality helps to prevent defects and ensure the final product’s reliability.
Finally, the case study reaffirms the necessity of understanding the material’s properties and adapting techniques accordingly.
Welding high heat-resistant stainless steel requires a comprehensive approach that considers the unique challenges and leverages advanced methods to achieve the desired results.
In conclusion, the successful welding of high heat-resistant stainless steel in Yota Village stands as a testament to innovation and precision.
The insights gained from this experience will undoubtedly influence future projects, promoting excellence in the field of stainless steel welding.
資料ダウンロード
QCD管理受発注クラウド「newji」は、受発注部門で必要なQCD管理全てを備えた、現場特化型兼クラウド型の今世紀最高の受発注管理システムとなります。
ユーザー登録
受発注業務の効率化だけでなく、システムを導入することで、コスト削減や製品・資材のステータス可視化のほか、属人化していた受発注情報の共有化による内部不正防止や統制にも役立ちます。
NEWJI DX
製造業に特化したデジタルトランスフォーメーション(DX)の実現を目指す請負開発型のコンサルティングサービスです。AI、iPaaS、および先端の技術を駆使して、製造プロセスの効率化、業務効率化、チームワーク強化、コスト削減、品質向上を実現します。このサービスは、製造業の課題を深く理解し、それに対する最適なデジタルソリューションを提供することで、企業が持続的な成長とイノベーションを達成できるようサポートします。
製造業ニュース解説
製造業、主に購買・調達部門にお勤めの方々に向けた情報を配信しております。
新任の方やベテランの方、管理職を対象とした幅広いコンテンツをご用意しております。
お問い合わせ
コストダウンが利益に直結する術だと理解していても、なかなか前に進めることができない状況。そんな時は、newjiのコストダウン自動化機能で大きく利益貢献しよう!
(β版非公開)