- お役立ち記事
- Casting Techniques and Applications: Casting Techniques for Forming Metal Parts and Improving Product Strength
Casting Techniques and Applications: Casting Techniques for Forming Metal Parts and Improving Product Strength
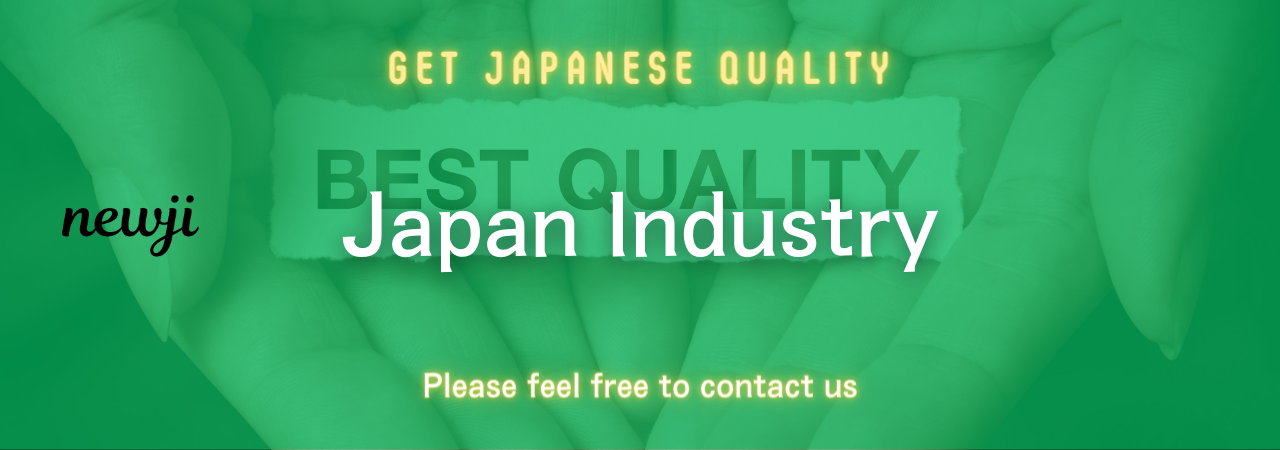
目次
Understanding Casting Techniques
Casting is an intricate process that involves pouring molten metal into a mold to create various parts and components.
This method has been used for centuries, dating back to ancient civilizations.
Today, casting has become more advanced, with numerous techniques available to suit different applications and materials.
Sand Casting
Sand casting is one of the oldest and most widely used casting techniques.
This method employs sand as the mold material, which is mixed with clay and water to form a solid and reusable mold.
Sand casting is particularly advantageous for producing large metal parts or components with complex geometries.
The process starts with creating a pattern of the desired part, typically made from wood, metal, or plastic.
This pattern is then placed in a mold box and surrounded by sand.
Once the sand is packed tightly around the pattern, the pattern is removed, leaving a cavity in the shape of the part.
Molten metal is then poured into this cavity, forming the final product as the metal cools and solidifies.
Die Casting
Die casting is another popular casting technique, particularly in the automotive and consumer electronics industries.
This method uses a metal die, or mold, typically made from steel, to create parts with high precision and a smooth surface finish.
Die casting is highly efficient and cost-effective, especially for producing large volumes of small to medium-sized parts.
The process begins with melting metal, such as aluminum or zinc, and then injecting it into the die under high pressure.
This high-pressure injection ensures that the molten metal fills the entire mold cavity, creating intricate details and precise dimensions.
Once the metal cools and solidifies, the die is opened, and the finished part is ejected.
Die casting is ideal for mass-producing parts with consistent quality and tight tolerances.
Investment Casting
Investment casting, also known as lost-wax casting, is a technique commonly used for creating intricate and detailed metal parts.
This method involves creating a wax model of the desired part, which is then coated with a ceramic shell.
Once the ceramic shell hardens, the wax is melted and drained away, leaving a hollow mold.
Molten metal is then poured into this ceramic mold, taking the shape of the intricate details encoded within.
After the metal has cooled and solidified, the ceramic shell is broken away, revealing the final part.
Investment casting is perfect for making high-precision components, such as turbine blades, medical devices, and jewelry.
Centrifugal Casting
Centrifugal casting leverages centrifugal force to produce cylindrical parts, such as pipes, tubes, and rings.
In this technique, a rotating mold is used to hold the molten metal while it is being poured.
As the mold spins, the centrifugal force pushes the molten metal towards the outer walls of the mold.
This force helps eliminate impurities and promotes the formation of a dense, uniform structure.
Once the metal cools and solidifies, the resulting part is removed from the mold.
Centrifugal casting is particularly beneficial for creating strong, void-free parts with excellent mechanical properties.
Continuous Casting
Continuous casting is a technique primarily used in the manufacturing of long metal products, such as rods, bars, and sheets.
This method involves continuously pouring molten metal into a water-cooled mold, causing it to solidify almost instantly.
The solidified metal is then continuously extracted from the mold and cut to the desired length.
This process allows for the production of uniform and high-quality metal products without interruptions.
Continuous casting is widely used in the steel and aluminum industries due to its efficiency and ability to produce long, consistent lengths of metal.
Improving Product Strength
Casting techniques play a significant role in determining the strength and durability of metal products.
Various factors influence the final product’s strength, including the choice of metal, the casting method, and post-casting treatments.
Material Selection
Choosing the right metal is crucial for achieving the desired strength and properties in the final product.
Common materials used in casting include iron, steel, aluminum, copper, and their alloys.
Each material has unique characteristics that contribute to the strength and performance of the cast part.
For example, steel is known for its high strength and resilience, making it ideal for structural components and heavy machinery.
Aluminum, on the other hand, offers a good balance of strength and lightweight, making it suitable for automotive and aerospace applications.
Heat Treatments
Heat treatments are essential for enhancing the mechanical properties of cast metal parts.
These treatments involve heating the metal to specific temperatures and then cooling it at controlled rates.
Common heat treatments include annealing, quenching, and tempering.
Annealing is the process of heating the metal and then slowly cooling it to relieve internal stresses and improve ductility.
Quenching involves rapidly cooling the metal after heating it to a high temperature, resulting in increased hardness and strength.
Tempering, on the other hand, is performed after quenching to reduce brittleness and improve toughness.
Surface Finishing
Surface finishing is another critical step in improving the strength and durability of cast metal parts.
This process involves removing surface imperfections and enhancing the surface properties of the cast part.
Common surface finishing techniques include machining, polishing, and coating.
Machining removes excess material and sharp edges, ensuring precise dimensions and a smooth surface.
Polishing further enhances the surface finish by removing fine imperfections or scratches.
Coating, such as painting or plating, adds a protective layer to the metal, preventing corrosion and wear.
Conclusion
Casting techniques are fundamental in the manufacturing industry, enabling the creation of diverse metal parts and components with varying shapes and properties.
From sand casting to investment casting, each method offers unique advantages and applications.
By understanding these techniques and the factors that influence product strength, manufacturers can produce high-quality, durable metal parts for various industries.
資料ダウンロード
QCD調達購買管理クラウド「newji」は、調達購買部門で必要なQCD管理全てを備えた、現場特化型兼クラウド型の今世紀最高の購買管理システムとなります。
ユーザー登録
調達購買業務の効率化だけでなく、システムを導入することで、コスト削減や製品・資材のステータス可視化のほか、属人化していた購買情報の共有化による内部不正防止や統制にも役立ちます。
NEWJI DX
製造業に特化したデジタルトランスフォーメーション(DX)の実現を目指す請負開発型のコンサルティングサービスです。AI、iPaaS、および先端の技術を駆使して、製造プロセスの効率化、業務効率化、チームワーク強化、コスト削減、品質向上を実現します。このサービスは、製造業の課題を深く理解し、それに対する最適なデジタルソリューションを提供することで、企業が持続的な成長とイノベーションを達成できるようサポートします。
オンライン講座
製造業、主に購買・調達部門にお勤めの方々に向けた情報を配信しております。
新任の方やベテランの方、管理職を対象とした幅広いコンテンツをご用意しております。
お問い合わせ
コストダウンが利益に直結する術だと理解していても、なかなか前に進めることができない状況。そんな時は、newjiのコストダウン自動化機能で大きく利益貢献しよう!
(Β版非公開)